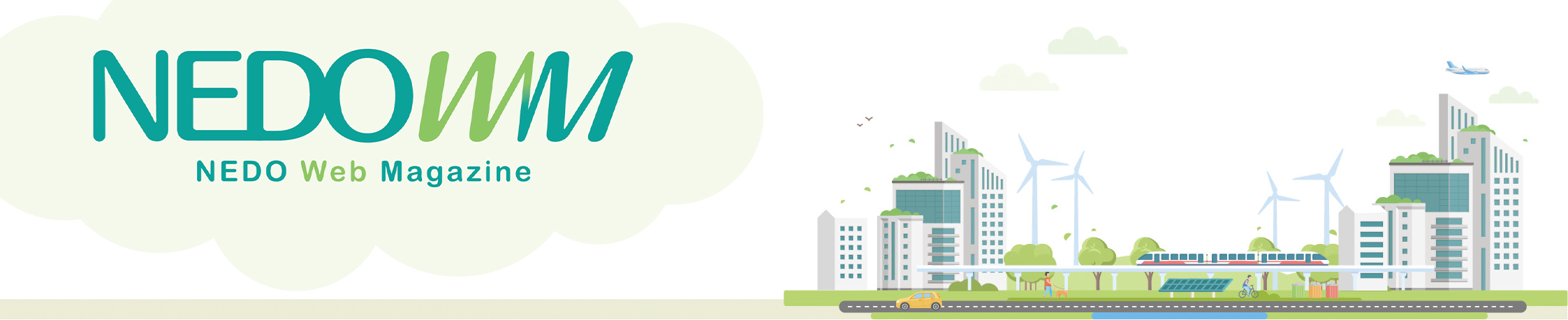
CONTENTS
BEGINNING
ナショナルプロジェクトへの参画は不可欠BREAKTHROUGH
NEDOプロジェクト下で13の要素技術を研究開発FOR THE FUTURE
長期発電実証ができる世界唯一の施設を発展させるFACE
人生の挑戦は山あり谷ありINTRODUCTION 概要
「発電用ガスタービンは高効率化・高出力化の競争で、より高温化していく必要があります。当時、ナショナルプロジェクトとして、必要となるさまざまな技術開発についてNEDOから支援していただきました」と振り返るのは、30年間発電用ガスタービンに携わる三菱重工業株式会社の由里雅則さんです。カーボンニュートラルをはじめとした温暖化対策と増加する電力需要に対応するため、CO2の排出を削減しながら多様な燃料を使用できる高効率な次世代火力発電技術の実用化が求められています。世界で唯一、同一敷地内でガスタービンの研究開発から設計、製造、実証、出荷まで可能な同社の高砂製作所・総合研究所は、研究者とエンジニアが顔をつきあわせて密に協力できる環境が整えられており、「1600℃級J型」に続いて、世界初の1700℃級となる「M501JAC形/M701JAC形ガスタービン」の実機運転を2020年に開始。さらに、次世代火力発電技術として期待が高まる水素燃焼ガスタービンの研究開発にも着手しています。
BIGINNING 開発への道
ナショナルプロジェクトへの参画は不可欠
私たちの生活に欠かせない発電エネルギーを取り巻く状況は時代により変化し、日本ではエネルギー基本計画が定期的に見直されています。2021年10月の第6次エネルギー基本計画では火力発電の今後の在り方として、「安定供給の確保を前提として、火力発電の脱炭素化に向けた環境対応に取り組みつつ、環境対応下での火力の競争力の強化・経済効率性の向上といった課題に取り組んでいく必要がある」とされています。
日本の主要電源である石炭火力発電やLNG(液化天然ガス)火力発電の高効率化を図り、環境負荷の低減と両立しながら有効活用を推進することは、社会的にも重要です。それを実現するための世界最高水準の高効率ガスタービンを開発するには、広範囲にわたる革新的な技術開発によって燃焼器や冷却、耐熱材料、熱遮蔽コーティング、タービン空力、圧縮機空力などの技術を確立することが求められています。
ガスタービンは高温化させることによって熱効率が高まります。日本で初めて「700℃級ガスタービン」の製造に成功した三菱重工業株式会社(以下、三菱重工)は、1962年に神戸造船所タービン専門工場として操業を開始し、1964年に高砂製作所として独立しました。そこを拠点としながら、世界最高性能の大型ガスタービンを次々に開発してきました(写真1)。1978年度から1987年度まで実施された「ムーンライト計画」とそれに続くナショナルプロジェクトへの参画で培われた技術を基に、ガスタービンの高温・効率化を進めてきました。「1150℃級D形ガスタービン」の開発を機に、1984年には天然ガスを燃料で世界最高の熱効率を達成した大型ガスタービンコンバインドサイクル(GTCC)発電システムを日本で初めて開発・製造しています。GTCCとは、ガスタービンで発電し、その排熱を利⽤して発⽣させた蒸気で蒸気タービンを回転させ、さらに発電するシステムです。「コンバインド」(Combined)、つまり複合的に発電するところにポイントがあります。
写真1 広大な敷地を有する三菱重工の高砂製作所(資料提供:三菱重工業株式会社)
三菱重工のGTCC事業の多くは高砂製作所のGTCC事業部で実施されています。GTCC事業部ガスタービン技術部長の由里雅則さんは「発電用ガスタービンの研究開発は過去も現在も高効率化・大出力化の競争であり、より高温化していくことが求められてきました」と言います(写真2)。さらに「ガスタービンの高温化には耐熱材料の開発だけでなく、構成するすべての部品で改良が必要です。それらの開発には長期間を要することから、ナショナルプロジェクトとして研究開発費を継続的に投入して取り組むことが不可欠でした」と状況を説明します。
写真2 ガスタービンについて熱く語る由里雅則さん
由里さんが三菱重工に入社した1990年代前半では、「1350℃級F形ガスタービン」が最新鋭として稼働していた時期でした。その後、国として1700℃級ガスタービンの技術開発を推し進めるべく、2004年度から 経済産業省が実施したナショナルプロジェクト「高効率ガスタービン実用化要素技術開発」(2004~2007年度)が始まりました。当時、ガスタービンの高温化にあたり、既存の研究開発設備の改良や新規導入を自社だけで実現することが難しかったこともあり、三菱重工もナショナルプロジェクトへの参画を決めたといいます。その後、「高効率ガスタービン実用化技術開発」(2008~2011年度:同省実施)、「高効率ガスタービン技術実証事業」(2012~2015年度:同省実施)の中で実用化に向けた研究開発を実施しました。なお、後者の事業は2016年度からはNEDOの「カーボンリサイクル・次世代火力発電等技術開発」のテーマの一つとして、NEDOへ事業継承し、NEDOのマネジメントのもと、商用化に向けた技術開発を実施してきました。
研究開発から設計、製造、実証までを同一敷地内で実施
ガスタービンの開発拠点である高砂地区には、高砂製作所に併設する形で1974年に高砂研究所(現総合研究所)が開設されました。そのため、研究開発から設計、製造、実証までをすべてを同じ敷地内でトータルに行うことができる、世界で唯一の環境が整っています(図1)。
図1 研究開発から実証までを一貫して行える高砂製作所・総合研究所の構成(資料提供:三菱重工業株式会社)
総合研究所で副所長を務める石坂浩一さんは、「研究所と製作所が何かあったら5分でいける距離にあり、意見交換をしやすい環境が研究開発にも影響しています」と話します(写真3)。
写真3 研究者の立場から高砂製作所の事業を支える石坂浩一さん
石坂さんは、「研究所には数百人規模の社員がいますが、組織としては階層がありつつも関係は完全にフラットで、上下関係なく意見交換ができる雰囲気が先輩の代からあり、いろいろな意見が生かされることで、研究開発が上手くいっていると感じます。例えばガスタービンを開発するうえでの技術課題や設計について、エンジニアとも常日頃からかなり密にディスカッションしています。それができる環境は実はあまりないですし、営業やメンテナンスの現場から吸い上げたお客さまのニーズをすぐに聞けるというメリットもあり、大きな強みになっています」と言います。
BREAKTHROUGH プロジェクトの突破口
NEDOプロジェクト下で13の要素技術を研究開発
1700℃級化に向けては、それまで取り組んでいた高温化技術を応用するだけではなく、ほかにも多くの新たな技術導入が必要となります。具体的には、排ガスや騒音などの環境影響に配慮しつつ、ガスタービンの核となる燃焼器やタービン、冷却技術、圧縮機などのさらなる性能向上や信頼性向上につながる技術開発をNEDOのプロジェクトで進めました。
由里さんは、「1500℃級ガスタービンの実用化が始まった頃から社会の環境配慮に対する要求が厳しくなり、燃焼温度を上げながら大気汚染物質の排出を抑制する技術が求められるようになりました。光化学スモッグの原因の一つであるNOx(窒素酸化物)については、弊社は世界で初めて予混合燃焼方式(あらかじめ燃料と空気を混合させて燃焼させる方式)を実用化し、その排出量を大幅に削減させることに成功しました。2010年代に入ってからはCO2が本格的に社会的問題としてフォーカスされはじめ、同時に再生可能エネルギー由来の電力が電力市場に一気に入ってきました」と振り返ります。
また「当時の政府が、温室効果ガス削減手段の一つとして、高効率火力発電技術の開発を位置づけたことから、弊社はガスタービンの開発にさらに力を入れていきました。その際に、時間帯や自然条件によって影響される風力発電や太陽光発電の電力系統変動に素早く対応するために、燃料を入れてすぐ出力を上げられる急速起動のガスタービンが開発できれば、電力系統の安定化ができ、ガスタービンの商品性にとっても大変有利になるといったことを、プロジェクトを通じてNEDOさんからアドバイスいただけたのはとてもありがたいことでした。また、こうした変化に合わせた新しい技術を持つ人材の採用や育成にもつなげることができました」と言います。
NEDOのプロジェクトでは、1700℃級の実用化に必要な超高性能タービンや高性能冷却システム、低熱伝導の遮熱コーティングなど、13の要素技術開発を実施し、すべての目標が達成されました(図2)。
図2 1700℃級の実用化へ向けて開発した13の要素技術(資料提供:三菱重工業株式会社)
例えば、低NOx燃焼器の開発では、NOx排出量や燃焼振動、未燃分の低減や、フラッシュバックといった、それぞれがトレードオフ関係にある技術課題を克服しながら、ビジネスとして成立するようにコストや性能、寿命、フレキシビリティー、メンテナンス性などのユーザー視点からの課題も考えていかなくてはなりません(図3)。低NOx化への打ち手として、燃焼空気量の増加や滞留時間の削減など、複数のアプローチでNOxを少しでも下げる努力を継続的に実施してきました。また、それらの効率的な開発のため、火炎の可視化技術の開発や、燃焼の数値シミュレーション技術の適用なども併せて実施しています。
図3 低NOxで燃焼器の開発で目指したポイント(資料提供:三菱重工業株式会社)
1700°C級ガスタービンの性能を向上しつつ信頼性を確保するには、タービン翼の形状やコーティングをはじめとする高温部品に対する工夫や、燃焼振動を抑制するための音響ダンパ(なるほど基礎知識参照)の導入などのさまざまな打ち手が必要です。また製造技術に関しては、従来から存在する鋳造、溶接技術についても、鋳造シミュレーション技術の開発や先進レーザー溶接技術の開発も実施。さらに、3次元の金属積層造形技術(3Dプリンティング技術)のような先進製造技術も取り入れています。
これらの研究開発は総合研究所において、金属部品を出力できる3Dプリンターの導入や、低熱伝導率遮熱コーティング(TBC:Thermal Barrier Coating)の溶射ロボット施工シミュレーションなどの技術を用いて、改良や検証が行われています(写真4、図4)。
写真4 3Dプリンターによる金属部品の造形(資料提供:三菱重工業株式会社)
図4 複雑な形状のタービン翼に対してTBC(Thermal Barrier Coating)を施工するためにロボットシミュレーション技術を用いている(資料提供:三菱重工業株式会社)
タービン翼の表面を覆う皮膜(TBC)内の気孔を増やす(⾼気孔⽪膜)と熱伝導率が低下し遮熱性が高まりますが、高温環境における高い熱応力などの影響を受けて、TBCや母材の強度低下を招きます。しかし三菱重工では、TBCの多層化やTBCの施工プロセスの改良によって、これを解決したうえで、高砂製作所内の実証発電設備において長期の信頼性検証試験を実施し、実際にその効果を確認しています。
長年にわたるナショナルプロジェクトで必要な技術を開発した三菱重工は、世界最高クラスの温度を実現した「M501JAC形/M701JAC形ガスタービン」を商業化しました(写真5)。2020年1月に試運転を開始し、同年7月には長期実証運転を開始しています。タービン入口温度を1650℃(※)まで高めることで64%の高い熱効率化を実現し、最新の空冷システムを用いた低NOx燃焼器を採用することで起動時間を短縮し、運用性の改善が図られています。また、排熱を利用した蒸気タービン発電とのコンバインドサイクルにより、50Hz 地域向けのGTCC出力は840MWの発電能力を備えています。数字にピンと来ないかもしれませんが、840MWの発電出力は約200万世帯の電力を賄える量に相当します。つまり、横浜市の全世帯(約175万世帯)に電力を供給できる規模です。
※実証発電設備では1700℃級ガスタービンの導入機として1650℃で実証中
写真5 M501JAC形/M701JAC形ガスタービン(資料提供:三菱重工業株式会社)
FOR THE FUTURE 開発のいま、そして未来
長期発電実証ができる世界唯一の施設を発展させる
大型ガスタービンを開発する欧米の競合企業もナショナルプロジェクトを立ち上げており、国家レベルでの競争が激化しています。現在、大型ガスタービンの開発が可能な国はアメリカ・日本・ドイツ・イタリアの4ヵ国があり、中国と韓国も国家を上げたガスタービンの国産化を支援していることから、今後、競合相手となる可能性が高いと見られています。
超高温かつ1万Gを超える遠心力という厳しい条件下で、1年以上の連続運用が求められる発電用ガスタービンは、ロケットエンジンなどと同様に、あらゆる機械製品の中でも最も技術の裾野が広く、燃焼、伝熱、材料、空力、制御など複数の分野において、先進性と完成度の高さが求められます。高い性能はもちろんのこと、信頼性でも世界の最高水準を目指すため、三菱重工では開発した大型ガスタービンを実際に1年間稼働させて、信頼性を確認してから製品として完成させるという、他社にはない取り組みをしています
それを担うのが、高砂製作所内に建設された実証設備複合サイクル発電所です。1997年から2019年まで運転された「T地点」に代わり、T地点横に新設された現在の発電プラント「第二T地点」は、高度な計測機器を備え、長期発電実証ができる世界唯一の施設です。2020年7月より運転を開始したJAC形では、通常の計器による計測と併せて数千点にも及ぶ膨大な数の計測データをオンラインで監視し、性能評価が行われました(写真6)。
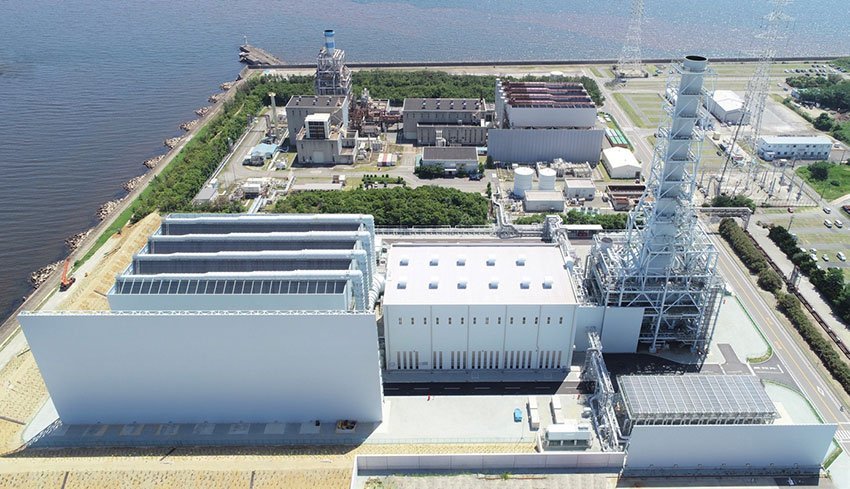
写真6 実際に発電を行っている高砂製作所の第二T地点(資料提供:三菱重工業株式会社)
由里さんは、「発電用の大型ガスタービンは、現地に設置したあと、そこでの試運転でトラブルが発生すれば改修する、というのが以前の導入方法でした。しかしながら、それではトラブルの解決に数か月を要する可能性があり、お客さまに大変迷惑がかかります。弊社は1990年代にG形を開発する際に、そういうアプローチは止めようと決めて、高砂製作所内に発電プラントを建設し、実際に1年間運転させて発電性能と長期信頼性を確認する手順を踏むことで、現地でトラブルが出ないようになりました。1年間も試運転に時間をかけると市場投入が遅れるため、商談では致命的になることもあります。早く出荷したいという営業の立場、良いものを作りたいという現場の立場もそれぞれわかりますが、お客さまにとって安心して回せる機械ということがやはり大事です。T地点の存在のおかげで、市場からの信頼評価は圧倒的に高いですし、きめ細かなアフターサービスやフォローと併せることで、アジアでも評判を高めています」とその理由を説明します。
2004年から参画しているナショナルプロジェクトの目標として、先行する他社に世界市場で追いつくことを掲げていましたが、2011年に1600℃級のJ形が完成したことで技術的に世界のトップとなったことから、その後は世界シェアでのトップ獲得をゴールとして目指していました。その結果、2022年には三菱重工が33%と、26%のシーメンス、25%のGEを越えて1位(全容量帯のOEM別シェア)となり、100MW超の大型ガスタービンのシェアでも1位となりました。「NEDOプロジェクトに参画していたことが大きな支援になり、世界トップになれました。1700℃級の実用化を経て、さらにその先を目指しています」と由里さんは言います。
ネットゼロに向けた発電技術
2020年7月から運転を開始した「JAC形ガスタービン」は、石炭焚き火力と比較してCO2排出を65%削減できることに加え、安定した運転で国内だけでなく、タイや米国、カナダ、ウズベキスタンなど世界中で受注を増やしています。
さらなる高温、高効率化によりCO2排出を削減する研究開発も継続されていますが、三菱重工では並行して、水素などを燃料にゼロ・エミッションを実現する次世代火力発電技術の取り組みも進めています。同社が掲げるネットゼロ・エミッションで泉澤清次社長は、国の取り組みを10年前倒しして2040年にCO2排出量を実質ゼロにすると宣言。具体的には、アンモニア、バイオマスでの混燃ボイラの開発、ガスタービンコンバインドサイクル発電システムに二酸化炭素回収・貯留技術を加えたCO2回収技術などで、排出量を90%削減することを発表しています(図5)。
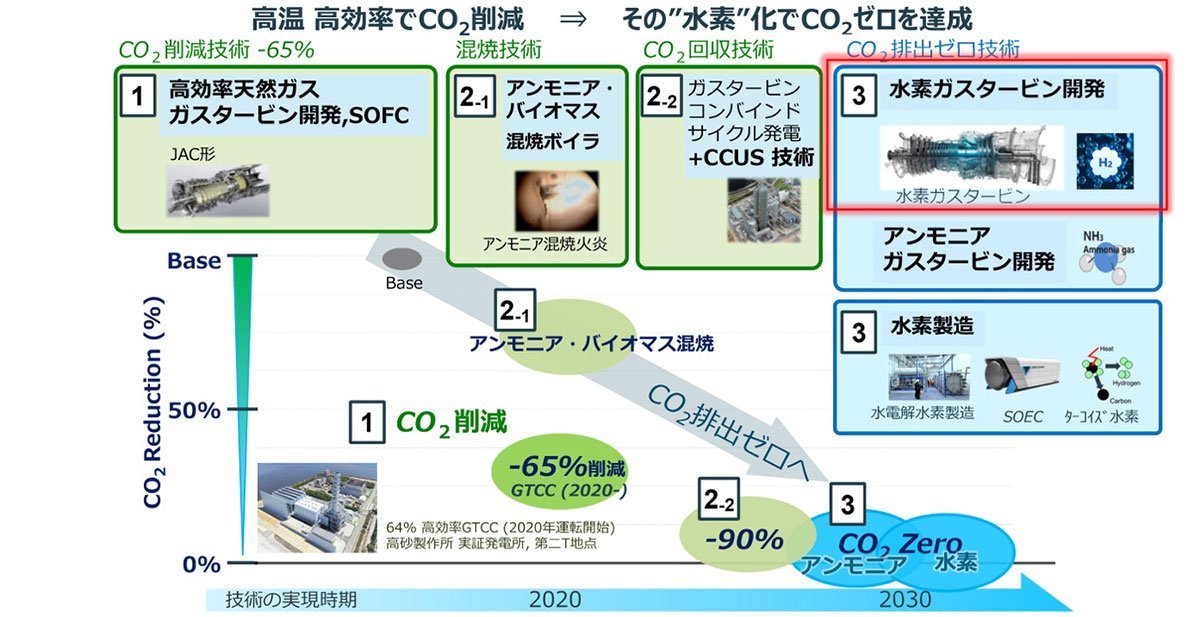
図5 ゼロ・エミッションに向けた三菱重工の発電技術開発ロードマップ(資料提供:三菱重工業株式会社)
「NEDOのほかのプロジェクトでは、化石燃料と水素の混燃・専燃による脱炭素技術にも取り組んでいます」と由里さんは説明します。三菱重工は、NEDOが実施する「水素社会構築技術開発事業」にも参画しており、2015年度から2018年度は水素混焼技術の開発、2020年度から2022年度は水素専焼燃焼器の開発に取り組んでいます。
「水素ガスタービンの開発に関しては、2022年6月に米国ジョージア・パワー社マクドノフ・アトキンソン発電所において、DLN(Dry Low NOx)燃焼器を装備したM501Gガスタービンで水素20%混焼の運転に成功しています。水素焚きM501JAC形ガスタービンは海外で受注しており、2025年に水素30%混焼、2045年までに100%専焼を計画しています」(由里さん)
また三菱重工は、高砂製作所に水素の製造から発電までを一貫して検証できる「高砂水素パーク」を整備中です。
由里さんは、「高砂水素パークは、水素供給が整う2023年以降に実機の検証を始める予定です。水電解水素製造装置によって敷地内で水素が製造できるので、水素に関する研究開発のスピードをかなり上げられると考えています」と説明します。
水素の課題は、非常に燃焼速度が速いために、燃焼器の焼損につながるフラッシュバック(火炎が燃料と空気の混合管の中まで遡上してしまう現象)が発生しやすいことや、燃焼振動が発生しやすいことであり、それらを回避するためのバーナー設計が大変難しいことです。そのためにも同じ敷地内で水素を作り、一貫して研究開発できる意義は大きいと言えます。
「一方で、競争相手が風力、太陽光の変動電力に対応するために、バッテリーとガスタービンを組み合わせた製品も開発してきており、そういう変化も意識しなければこの先は生き残れないだろうと考えます」と由里さんは続けます。
「時代の変化はどんどん早くなります。弊社全体として、再生可能エネルギーも含め、今後主流になりうるあらゆる技術を見据えながら関わっていきます。弊社が高い付加価値を付けられるのは、やはりガスタービン技術ですので、燃料を水素やアンモニアに置き換えていくことを通じて脱炭素を実現していきます。ユニークで圧倒な差がつけられるのはやはり信頼性ですから、自信を持ってこれからも引き続き開発を続けていきます」と由里さんは未来を見据えています。
今後も2050年のカーボンニュートラルを見据え、水素燃焼ガスタービンの研究開発など、新たな技術も取り込みながら、次世代火力発電のさらなる導入促進に向けて、NEDO、そして三菱重工の挑戦は続きます。
開発者の横顔
人生の挑戦は山あり谷あり
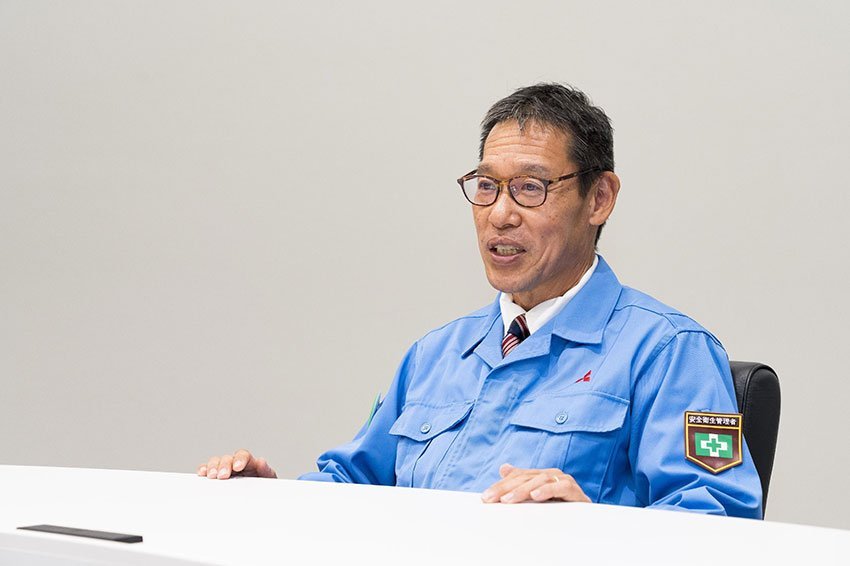
三菱重工業株式会社
GTCC事業部 ガスタービン技術部長
由里雅則さん
「ガスタービンはある意味究極のすり合わせ型の製品ではないか」と由里さんは語ります。
「パーツの数は大小さまざまで何万個もありますし、また圧縮機、燃焼器とタービンといった個々の要素のつなぎもあります。これらをバランス良く組み合わせないと機械としてはうまく動きませんが、そういうすり合わせの重要性を開発メンバーが常に意識しているので、意外に効率良く開発できているのではないかと個人的には思っています」
入社時からガスタービン設計者として開発に携わっている由里さんですが、当初は研究者としてガスタービンに貢献することを希望していたとのことです。
「私はもともと機械が好きで大学では機械工学を専攻していました。入社した時に研究所の配属を希望していましたが残念ながら叶わず、それでも諦めずに設計者としてガスタービン開発をやりたいと言い続けて設計部門の配属になりました。駆け出しの設計者のころはトラブル対応や、現地の試運転への参加、また米国に駐在してジェットエンジンの設計者とともにガスタービンの設計を行うなど、さまざまな経験をできたことが設計者としてのキャリアで良かったと思っています」
「ここ最近はGTCC発電としての最適化のために、プラント技術、営業、サービスなど他部門ともつながり、GT全体を取りまとめるトップとして、ガスタービンの開発に関わり続けています。大変なことがありながらもここまで続けられた一番大きなモチベーションは、社会貢献ができるというのもありますが、やはりエンジニアとして大きなやりがいがあることです。自分たちで考えたアイデアや技術でチャレンジしながら、これだけ大きなものを作る機会は世の中になかなかありません。趣味はロードバイクでのヒルクライムなのですが、これと同じように山あり谷ありというのも、ずっと現場から離れられない魅力なのかもしれません」
研究者と設計者が向き合って議論できる環境を作る
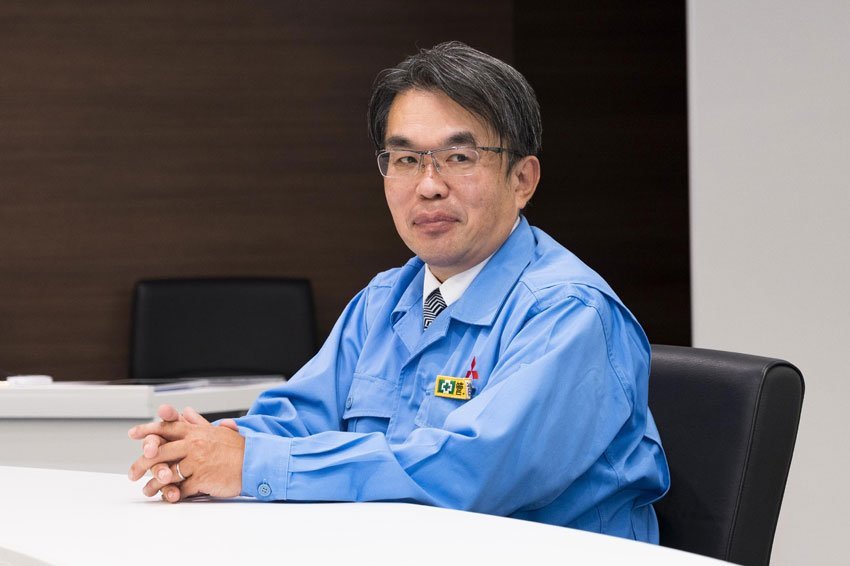
三菱重工業株式会社
総合研究所 副所長 工学博士
石坂浩一さん
大学では流体シミュレーションを専門に学び、博士号を取得してから三菱重工に入社した石坂さんは、高砂製作所と隣接する総合研究所に所属してから2020年までは、主に1700℃級ガスタービンの研究開発の取りまとめを行っていました。
「私の仕事は簡単に言うと、設計と1対1で向き合い、研究と製品の両方を取りまとめられる環境を作ることです。研究所としては少し先を見据えた研究開発を実施していく必要がありますが、常に実用化を念頭に置いた内容とは限りません。もちろんすべての研究は実用化を念頭に置きますが、それぞれの技術の内容やその実用化レベルに目を光らせながら、少しでも成功確率を上げるべく調整していく必要があります。また私自身が研究に加わることもあり、2016年から2018年頃は旋回失速を低減するシミュレーションなどを行っていました。圧縮機の解析やガスタービンの排気、蒸気タービンの翼設計のほか、過去には低NOx燃焼器で使用するスワラーや燃料ノズルの形状を考えたりしていました。燃焼器の逆火対策では文字通りのたうち回るほど苦労して問題を突き止め、そこで使われたシミュレーション技術はガスタービンの開発にも生かされています」
由里さんとは米国勤務中に出会い、今はガスタービン開発で研究と製造というそれぞれの立場から時には熱い意見を交わす関係にあります。
「私はガスタービン以外にもさまざまな製品の研究に関わり、ヘリコプター用のエンジン、極超音速風洞やロケットエンジンなど、当時はあまり知られていない現象を発見し、かなり幅広い分野を経験しています。研究所の仕事はいろんな製品に関われるのが面白いところで、発想を広げるためにも、若い人たちの意見に耳を傾けることを大事にしています」
なるほど基礎知識
新型音響ダンパ──燃焼振動の抑制効果と低NOx性の両立
高温のガスタービンでは、火炎が不安定になることで発生する燃焼器の燃焼振動が問題となります。燃焼振動は短時間で燃焼器の疲労破壊を招いてしまうことがあり、ガスタービンの燃焼技術の中で、音を減衰させ、燃焼時の圧力変動を低減させる「音響ダンパ」は、高温化の要となる燃焼器の重要デバイスです。
音響ダンパとは、多孔板と音響箱によって構成される燃焼筒を取り囲む形で設置された共鳴器です。その開発は古く、航空機用のジェットエンジンの圧力変動を低減するデバイスとして使われていますが、それとほぼ同じ原理のものを産業用ガスタービンの燃焼器に適用しています。ガスタービンの燃焼ガス温度の上昇に伴い、燃焼振動の傾向が強くなってきたため、採用されました。仕組みは、燃焼振動の圧力変動によって生じる流体の変動が、多孔板を出入りすることで流体の運動エネルギーを消散させ、その結果、音圧レベルが低減するというものです(図6)。
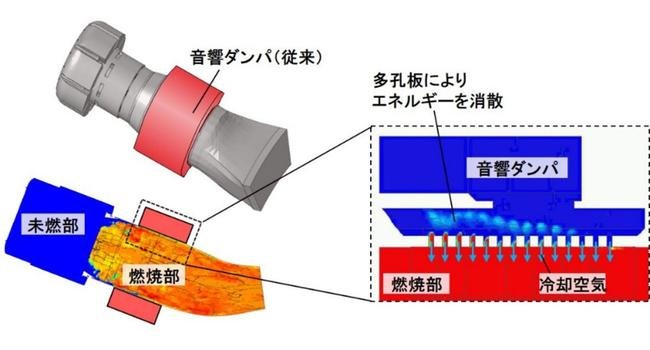
図6 音響ダンパによる燃焼振動レベルの低減原理(資料提供:三菱重工業株式会社)
しかし、従来の音響ダンパには、いくつかの課題がありました。
まず、音響ダンパは燃焼筒に設置することから冷却用に空気が必要になります。ガスタービンは通常、空気が過多な状態で燃焼していますが、音響ダンパの冷却用に空気を消費すると、燃料と空気の混合濃度が濃くなり火炎温度が上昇、その結果、NOxが増大してしまいます。
そこで、音響ダンパの冷却空気を削減することを目的に、音響ダンパの設置場所の再検討を実施しました。解析や音圧分布の計測結果を評価した結果、燃焼器入口に音響ダンパを設置することで、冷却空気が不要になり、NOx排出を増やすことなく燃焼振動を低減する新型音響ダンパを開発できました(図7)。燃焼部と未燃部とでは音圧や流れの条件が異なるため、音響減衰効果が低下すると予想されましたが、多孔板で音響を減衰させる効果を未燃部に合わせて最適化することで、音の減衰を最大化できたのです。
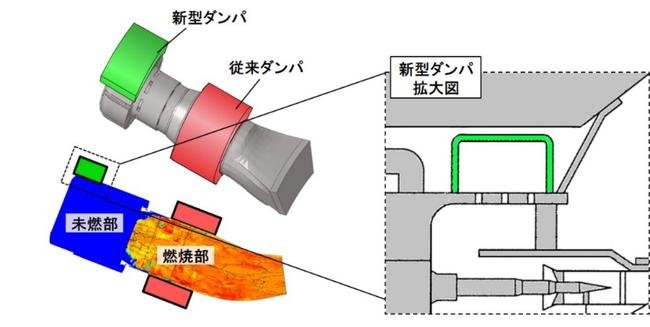
図7 新型音響ダンパの構造(資料提供:三菱重工業株式会社)
試新型音響ダンパを設置した実機運転の結果、燃焼振動を約25%低減でき、NOxも増加しないことが確認されました。
NEDOの役割
「カーボンリサイクル・次世代火力発電等技術開発/②高効率ガスタービン技術実証事業」
2016~2020年度
NEDO内担当部署:環境部
地球温暖化や気候変動は日本のみならず世界共通の課題です。世界がカーボンニュートラル社会へ移行していく中、火力発電においても脱炭素化に向けた研究開発を実施する必要があります。その中でも、ガスタービン製造の市場は日米欧で世界シェアの大半を占めており、他国も政府支援を受けるなど、競争は激化しています。
NEDOは、火力発電の熱効率向上によるCO2排出量削減に向けて、発電効率を高める新型ガスタービンの技術開発に取り組みました。1988年度から始まったNEDO主導の「ニューサンシャイン計画」でも高効率化に取り組むなど、ガスタービン開発には非常に長い歴史があります。開発に長期間を要すること、研究開発の難易度の高さから、NEDOが持つ知識・実績を生かしてプロジェクトを推進しました。
その結果、本プロジェクトにおいて、高効率で信頼性の高い1700℃級ガスタービンの開発に成功しました。世界をリードする発電技術の開発を行うことで、NEDOは引き続きカーボンニュートラル社会に貢献していきます。
当時のNEDO担当者の声(在間信之さん)
2050年のカーボンニュートラルを実現するためには、再生可能エネルギーの導入や、火力発電の脱炭素化に向けたアンモニア・水素などの脱炭素燃料の導入、そしてCO2の回収・利用・貯留(CCUS)といった取り組みが必要です。エネルギー政策の基本的な方向性を示す「第6次エネルギー基本計画」でも、CO2排出を削減する措置の推進に取り組むことが明記されています。現在、NEDOではこれらの目標を達成するために、火力発電に関連した多くの技術開発に取り組んでいます。
太陽光発電をはじめとした再生可能エネルギーは、時間帯や天候の影響を受けやすいという課題があります。電力を安定的に供給するには、火力発電を活用し、電力の需要と供給に柔軟に対応する仕組みが必要です。そこで、「機動性に優れる広負荷帯高効率ガスタービン複合発電の要素研究」では、夕方などの電力需要が増えた際に急速に起動運転できるシステムや、日中、再生可能エネルギーによる発電量が多いときには待機時の消費エネルギーを減らす技術の開発を行っています。
また、「アンモニア混焼火力発電技術研究開発・実証事業」では、燃焼時にCO2を発生しないアンモニアを火力発電の燃料として活用する燃焼技術の開発を行っています。ガスタービンの発電効率を向上させることで、発電コストを下げる効果があります。さらに、CO2の分離・回収技術の開発にも「CO2分離・回収技術の研究開発」として取り組んでいます。
石炭を熱すると熱分解反応が起こりますが、この際生じる石炭ガスを利用する、次世代の高効率石炭火力発電システム「IGFC」(石炭ガス化燃料電池複合発電システム)に今回の1700℃級ガスタービンを組み込むことで、従来の石炭火力発電システムのCO2排出量を65%以上削減することができます。
カーボンニュートラルの実現に向けて開発を進めているこれらの技術は、1700℃級ガスタービンの開発成果がベースになっており、火力発電に関連したCO2排出削減技術の総合的な効率向上につながる、大きな成果だと考えています。
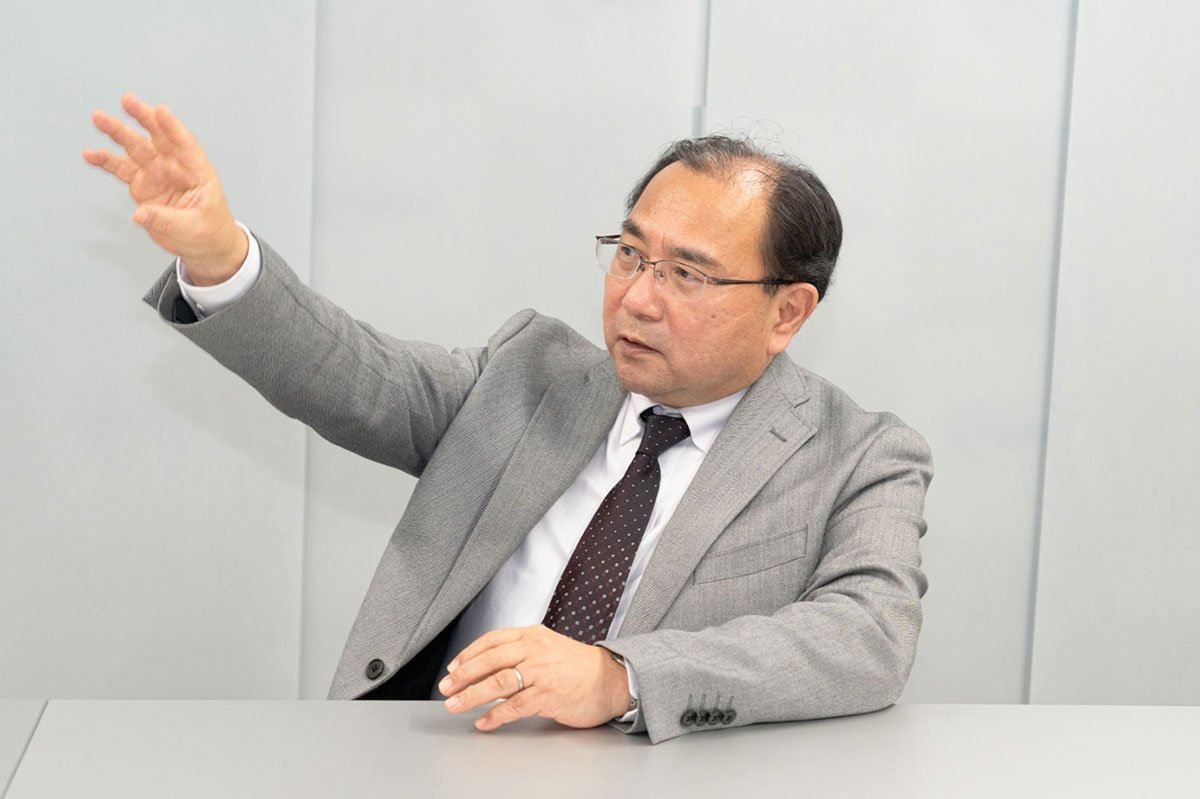
国立研究開発法人新エネルギー・産業技術総合開発機構
環境部
統括調査員
在間信之さん
関連プロジェクト
お読みいただきありがとうございました。
ぜひともアンケートにお答えいただき、
お読みいただいた感想をお聞かせください。
いただいた感想は、
今後の連載の参考とさせていただきます。