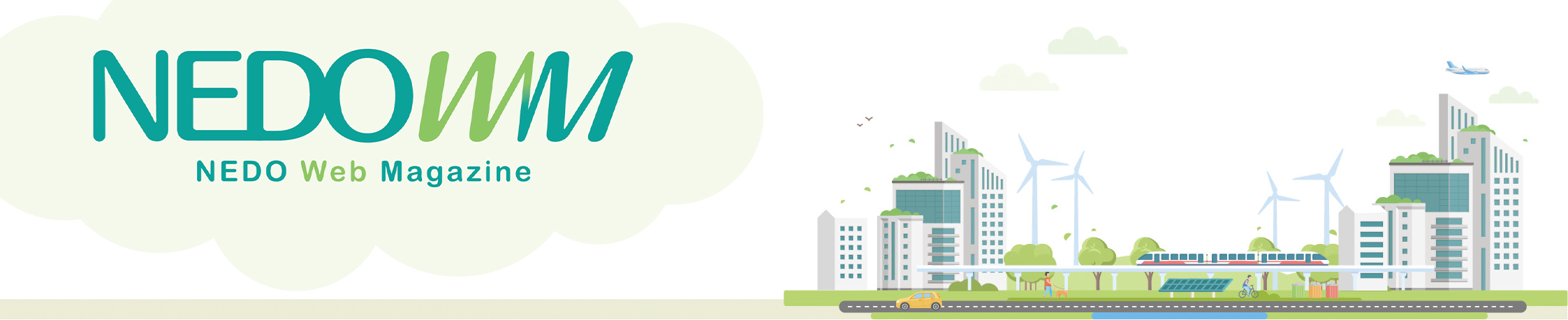
CONTENTS
INTRODUCTION
軽量で高強度な植物由来の新素材BEGINNING
環境に貢献する事業を探す中、CNFの新聞記事に注目BREAKTHROUGH
親水性のセルロースと疎水性の樹脂を仲良くさせるFOR THE FUTURE
販売数、世界で700万足以上FACE
紙のように使われる存在にしたいINTRODUCTION 概要
軽量で高強度な植物由来の新素材
木材由来の紙の原料であるパルプをナノレベルまで解きほぐし、「セルロースナノファイバー(CNF:Cellulose Nano Fiber)」とし、それを樹脂中に均一分散させると、軽量で高弾性のCNF強化樹脂複合材を作り出すことができます。この樹脂複合材を使うことで、部品や製品の軽量化が期待できます。また、持続可能性という観点から見ると、再生可能な植物資源を利用するため、地球環境への負荷低減にもつながります。CNF複合樹脂の実用化にはさまざまな取り組みが行われていますが、パルプのナノファイバー化と樹脂複合化の両方を一度に行う製造方法が、NEDOプロジェクト「グリーン・サステイナブルケミカルプロセス基盤技術開発/セルロースナノファイバー強化による自動車用高機能化グリーン部材の研究開発」(2010〜2012年度)にて産学官連携で研究されたことで実現の目処を得られ、それに続くNEDOプロジェクトにて確立されました。この製造方法は研究拠点の置かれた京都大学にちなんで「京都プロセス」と呼ばれています。参画メンバーの星光PMC株式会社は、京都大学の矢野浩之教授のリーダーシップや他メンバーとの連携もありこの「京都プロセス」の開発に取り組み、その成果を基に独自に改良を重ね、2018年、CNF複合材料「STARCEL®」の商用生産を開始しました。同年、「STARCEL®」は、スポーツ用品メーカー 株式会社アシックスのランニングシューズ「GEL-KAYANO®25」等のミッドソール素材に採用され、2020年2月までに世界で700万足を数える販売実績を上げています。
BIGINNING 開発への道
環境に貢献する事業を探す中、CNFの新聞記事に注目
木材由来の素材CNFは、鋼鉄の5倍の強度かつ5分の1の軽さといった特長を持っています。このCNFを配合した樹脂が「STARCEL®」です。
この複合樹脂を開発した星光PMCは、もともと製紙工程に添加する薬品や印刷インキに使う樹脂の製造を、長らく事業の柱としてきました。しかし、社会がデジタル化していく中で、2000年代中盤以降、紙や印刷需要の頭打ちや減少にさらされていきます。同社にとって新規事業の開拓が大きな事業課題となっていました。
星光PMC取締役で技術本部長の岩田悟さんは当時の事情を、「単純に新規事業を模索するのではなく、持続可能性を考えて、新事業は環境保全に貢献できる内容であることも、重要な経営ビジョンの一つでした」と説明します。
「そこで製紙産業に関わってきたこともあり、木質材料を利用する新事業を開拓することを考えつきました。そんなとき、当時研究開発本部長だった現社長の滝沢智が、京都大学の矢野浩之教授が植物繊維による新素材を開発したと新聞で知り、急いで会いに行きました。2006年のことです。それがCNFに関わることになる始まりでした」(岩田さん)
京都大学生存圏研究所教授の矢野浩之さんは、同大学農学部林産工学科出身で、楽器に使われる木材の性質の研究をしていました。その後、日本材料学会の講演会で、当時セルロースミクロフィブリルなどと呼ばれていたCNFから出来ているパルプ繊維の強度が、炭素繊維相当の強度になるという研究者からの話を聞き、CNFの可能性に着目して、研究に乗り出します。
矢野さんは、星光PMCの滝沢さんと面会した頃、経済産業省近畿経済産業局の委託事業で、京都市産業技術研究所のほか複数の企業とコンソーシアムを形成するなどして、後のCNFにつながる材料の研究開発に着手していました。
当時を思い起こして矢野さんは、「星光PMCがどういう事業をしているか滝沢さんは私に丁寧に説明してくれました。製紙に関わる化学会社なので、CNFの研究と相性がいいかなと考えました」と話します。
そして、この材料に興味を持っていた化学技術戦略推進機構(JCII)(現:化学研究評価機構)が声がけした勉強会の場で、大日本インキ株式会社(現:DIC株式会社)からの打診があり、星光PMCの勉強会メンバー入りが決まりました。DICは星光PMCの親会社に当たります。
この勉強会は、翌2007年9月から矢野さんらが取り組んだNEDOプロジェクト「イノベーション推進事業/大学発事業創出実用化研究開発事業」(2007〜2009年度)での実施体制をつくるという目標もありました。実用化担当事業者として製紙会社や高分子材料メーカー、さらに最終製品を製造するメーカーまで約20社が集まり、原材料から製品までの上流から下流までの流れを強く意識した勉強会となりました。星光PMCは大日本インキの一員として、このプロジェクトに参画しました。
BREAKTHROUGH プロジェクトの突破口
親水性のセルロースと疎水性の樹脂を仲良くさせる
NEDOプロジェクト「イノベーション推進助成事業/大学発事業創出実用化研究開発事業」と、それに続く「グリーン・サステイナブルケミカルプロセス基盤技術開発/セルロースナノファイバー強化による自動車用高機能化グリーン部材の研究開発」(2010〜2012年度)が実施された5年半は、木材由来のパルプからCNFをつくり(図1、写真2)、それをポリエチレンやポリプロピレンなどの樹脂に補強材として高効率に混ぜ入れる「京都プロセス」がまさに築かれていった期間に当たります。その道のりには、数々の課題への挑戦とその克服がありました。
図1 木材の主構成要素。鉄筋コンクリートに例えると、CNFは鉄骨、ヘミセルロースは鉄筋、リグニンはコンクリートに相当(資料提供:京都大学)
写真1 (左上)木材、(右上)チップ化した木材、(左下)加熱・加圧して溶解させて得たパルプ、(右下)疎水化した変性パルプ
強くて軽いナノファイバーであるCNF(「なるほど基礎知識」も参照)を樹脂に混ぜ込むにあたっては、「親水性のものを疎水性のものにどう混ぜ合わせるか」が、まずもって大きな課題でした。
CNFは、セルロース分子を主な成分としていて水とよくなじみます。つまりCNFは「親水性」です。これに対して、相手のプラスチック樹脂は、石油を原料としていて水とはなじみません。つまりプラスチック樹脂は「疎水性」です。親水性のCNFを、疎水性のプラスチック樹脂のなかに、均一に分散するように混ぜ入れなければ、樹脂を補強することはできません。「水と油」を混ぜるようなこの難題に挑んだのが、CNF事業推進部副部長の佐藤明弘さんでした。佐藤さんは言います。「当初プロジェクトでは、セルロースと樹脂に新規の添加剤を加えることなども検討されていましたが、私どもはセルロースを化学変性させることに注力しました」
化学変性とはここでは、親水性であるセルロースの一部をほかのものに置換して、疎水性を持たせることを指します。佐藤さんは、「パルプ繊維に親水性の部位と疎水性の部位の両方をもたせる疎水化剤の候補を加えてみました。樹脂と似た構造があれば、樹脂とのなじみもよくなるだろうとの予測でしたが、実際は、試してだめ、また試してだめという、試行錯誤の繰り返しでした」と話します。
そうしたなか、佐藤さんら星光PMCの研究員たちは、ある薬品に可能性を見出し、矢野さんらプロジェクトメンバーに伝えました。矢野さんはその時のことを現在もよく覚えていて、「『イノベーション推進助成事業/大学発事業創出実用化研究開発事業』プロジェクトが終わりの頃、佐藤さんから月1回の会議の場で、セルロース表面の疎水化剤として『ASA』が使えるのではないかと報告を受けたのです」と振り返ります。
「ASA(Alkenyl Succinic Anhydride)」は、アルケニルコハク酸無水物という有機化合物で、製紙では紙に耐水性を付与しインキのにじみを防ぐサイズ剤として使われています。矢野さんは、「さまざま薬品が候補として試されていたなかで、耐水性を高めるそんな薬品もあるんだなぐらいの感じでそのときは聞いていました」と言います。
佐藤さんらは、CNFと樹脂の混ぜ合わせ工程担当の他社研究員からも結果を聞いたり、プロジェクトの中心人物だった京都大学特任教授の中坪文明さんにアドバイスを求めたりして「どう化学変性させるか」を追求しました。
佐藤さんは、「CNF複合樹脂の強度を出すには、分子同士の結合が行われる親水性の部分を保っておくべきです。でも、CNFを樹脂に均一に分散させるためには、その親水性の部分を疎水化させなければなりません。親水性と疎水性のベストバランスを求めていきました」と説明します。
こうしてプロジェクトメンバーたちは、樹脂にCNFを均一分散させるため、「ASA」でセルロースを疎水化するという方法を打ち立てました。
ナノ化の単独工程を一気にカット
しかし、CNF複合樹脂を商用化するにはまだ大きな壁が立ちはだかっていました。製造コストの壁でした。当時、考えられていた手順は、「パルプを水で解きほぐしてナノファイバーにし、『ASA』で疎水化してから乾燥させ、それを樹脂に混ぜ込んでいく」というものでした。
これでは工程が多すぎて、いくらCNFが強くて軽い材料だといっても、コストがかさんで実用化に見合いません。矢野さんは、「ナノファイバー1kgが1万円では商売にならないのは明らかでした。そこで、コストをどこまで下げられるか思案し、ちょっと妥協してみることを考えたのです」と言います。
このころプロジェクトでは、原料のパルプをナノファイバーにするのに「ビーズミル」という攪拌粉砕機を使っていました。矢野さんは言います。「ビーズミル処理でなくとも、ある程度のナノ化できる方法で、かつ、そこそこの補強性が出れば、それはそれでよいのではないかと考えたのです」
矢野さんたちは、ナノ化の程度が異なるファイバーを試作し、それぞれどのくらいの補強性が出るのか実験してみました。矢野さんはその結果を、「それはもう驚きました」と話します。「実験結果がメンバーから送られてきたので見てみると、ナノ化の程度に関わらず、どれもほぼビーズミルで処理したときのような補強性が出ていたのです」(矢野さん)
「ビーズミルでナノ化するプロセスを一気にカットできる。パルプを『ASA』で疎水化しておけば、樹脂と混ぜ合わせる混錬機のなかでナノファイバーにまでほぐすことができる。これで実用化に向けて進んでいけるぞということになりました」(矢野さん)
こうして、「京都プロセス」の基礎は確立され、CNF複合樹脂の有力な製造方法となりました。その後、「ASA」以外の変性剤で疎水化を施す方法も編み出されています。また、セルロース単体でなく、パルプに含まれるリグニンやヘミセルロースといった他の原材料も生かしたリグノ・セルロースナノファイバーを樹脂と複合化する技術も、NEDOプロジェクト「非可食性食物由来化学品製造プロセス技術開発」(2013〜2019年度)で確立しています(写真2)。
矢野さんが言うように、「京都プロセス」の最大の特長は、パルプのナノファイバー化と樹脂複合化の両方を同時に実施してしまうことにあります。このプロセスの実現には、実験を担った企業などの多数のプロジェクトメンバーの貢献があったのです。
写真2 (上)星光PMC研究所内にある実験室レベルの二軸混錬押出機、(中)疎水変性パルプと樹脂を混ぜ合せるために噛み合わされる2本の回転軸、(下)麺のように押し出されていくCNF配合樹脂
一つ屋根の下で、「集中研方式」
プロジェクトの進め方も、こうしたブレークスルーを後押ししました。佐藤さんは当時の研究現場の雰囲気を、「常に矢野先生や中坪先生、また他の企業のメンバーの方々と一緒に居たので、問題が起きたらその場でアドバイスをいただいて、すぐ解決することができました」と話します。
複数の組織からなるプロジェクトでは通常、メンバー各々が自分の大学や企業などで研究を進め、その成果を定期的に会議に持ち寄って情報共有することで研究開発が進んでいきます。一方、星光PMCなどが取り組んだ今回のNEDOプロジェクトでは、京都大学宇治キャンパス内の生存圏研究所を拠点に研究員たちが集まり、常駐しながら研究開発を進めていく「集中研方式」が採られました。
矢野さんは、「世の中にまだないCNFという材料を創り出せたのは、やはり、いろいろな専門性を備えたメンバーが、いつも顔を合わせていたからこそだと思います」と言います。「何もないところから始まったこの研究開発が、実用化できるレベルまで仕上がっていくことに、集中研方式が果たした役割はとても大きいと思います」(写真3)
写真3 (左)「集中研方式」の拠点となった京都大学宇治キャンパス内の生存圏研究所生物機能材料分野(矢野研究室)の研究棟(ナノセルロースコア・ナノハウス)、(右)関連NEDOプロジェクトによってさらに整備された研究設備
実証設備建設、そして商品化
「京都プロセス」の開発に取り組んだNEDOプロジェクト「グリーン・サステイナブルケミカルプロセス基盤技術開発/セルロースナノファイバー強化による自動車用高機能化グリーン部材の研究開発」プロジェクトは、2013年3月をもって期間終了となりましたが、星光PMCでは、間髪を入れず、その成果の商品化に向け動きました。
岩田さんは言います。「私どもの研究員もNEDOプロジェクトで重要な役割を果たすことができました。疎水化の話にあったように、キーテクノロジーは化学処理にあり、私どもの成果が実用化にも生かせるという思いもありました」
矢野さんからの情報提供もあり、星光PMCは経済産業省の「イノベーション拠点立地推進事業」に応募し、同年、採択されました。この支援を受け、茨城県内の竜ヶ崎工場に変性セルロースの粉末やCNF複合樹脂を実証的に製造するパイロットプラントを建設し、2014年11月から本格的にサンプルの提供を始めています。
「量産する上での不具合が生じることもありました。社員たちにはいろいろ苦労をさせたと思います」(岩田さん)
一例として、パルプがナノファイバーにまでほぐれきらないといった問題が起きました。こうした問題を同社CNF事業推進部研究員の山田修平さんらが、パルプの段階から設計を見直して解決していきました。山田さんは、「解決できたのも、2012年度までのNEDOプロジェクトで基本の部分はしっかりできていた点が大きかったと思います」と話します。
NEDOプロジェクト参画者のつながりが生かされて、星光PMCに企業からの引き合いもありました。スポーツ用品メーカーのアシックスが、NEDOプロジェクトのメンバーだった京都市産業技術研究所から、星光PMCがCNFの商品化を目指しているという情報を受け、アプローチしてきたのです。
アシックスの狙いは、CNFが持つ軽量性と強度・耐久性をランニングシューズのクッション部分であるミッドソールに取り入れられないかというものでした。激しい機能性向上の競争が繰り広げられているランニングシューズ分野だけに、アシックスからの要求内容はレベルの高いものでしたが、山田さんらが中心となり改良を重ねることになります。
矢野さんは初めてランニングシューズへの採用を知らされたときのことを、「採用発表の何日か前に、星光PMCの岩田さんから『直々にお伝えしたいことがあるんです』と連絡をもらいました」と話します。
「大学のホールで待っていると、岩田さんが見慣れぬ人と現れました。アシックスの方でした。そして岩田さんは開口一番、『先生、ランニングシューズとして商品化できることになったんです』と言ってきたんですよ。あのときは思わず涙がにじんできました。NEDOからの支援をこれだけ受けて、どうしても実用化につなげなければならないと思っていたなか、星光PMCが努力してそれを実現させてくれたからです」(矢野さん)
2018年6月1日、ついに星光PMCは「STARCEL®」(写真4)が、アシックスのランニングシューズ「GEL-KAYANO® 25」に採用されたことを発表しました。「京都プロセス」を活用したCNF関連製品の商品化第1号です(写真5)。
その後、2020年2月に、星光PMC、京都大学、他によるNEDO事業での集中研方式による産学官連携の取り組みと、CNFの社会実装化に至るアシックスとの産産連携の取り組みが評価され、内閣府が主催する「第2回 日本オープンイノベーション大賞」で、選考委員会特別賞を受賞することになります。
写真4 星光PMCのCNF配合樹脂「STARCEL®」(左:CNF強化ポリエチレン、右:CNF強化ポリプロピレン)
写真5 アシックスのGEL-KAYANO®25。ミッドソール(光に照らされた部分)のスポンジ材にSTARCEL®を配合
FOR THE FUTURE 開発のいま、そして未来
販売数、世界で700万足以上
「京都プロセス」は、こうして実用化の段階に入りました。星光PMCの「STARCEL®」はGEL-KAYANO®25やMETARIDE™などアシックスの多数のモデルに採用されており、CNFを使用した同社ランニングシューズは、2020年2月時点で、世界全体で700万足以上が販売されています。
星光PMC CNF事業推進部・部長の河端崇さんは、「天然由来の原料から、製品にまで仕上げていくのには苦労もありました。でも、そうした苦労を社員みんなで共有し、課題を乗り越えられた経験は、私どもには大きな財産になりました。世界展開するアシックスのシューズに『STARCEL®』を使っていただけたことは、これまで最終製品に自社製品が使用されていることがわかりにくかった当社の事業分野と異なり、会社全体の一体感の醸成にも役立っています」と話します。
その後「STARCEL®」は、22の大学・研究機関・企業が参画し、CNFの活用で10%の軽量化を目標に実際の自動車を作る、環境省の「NCV(Nano Cellulose Vehicle)プロジェクト」で、コンセプトカーのさまざまな部品に使用されるなどしています(写真6)。
写真6 環境省の「NCVプロジェクト」で作られたコンセプトカー。京都大学宇治キャンパスに展示
第二歩、第三歩を踏んでいくために
「京都プロセス」を活用したCNF複合材料は、実用化の第一歩を踏み出したところです。一方で、強くて軽い樹脂を必要とするシーンは社会に数限りなく存在します。2012年度まで実施した「グリーン・サステイナブルケミカルプロセス基盤技術開発」では、自動車用の高機能化部材の開発がテーマに掲げられていました。
この第一歩を足がかりに、さらに実用化が進めば、原材料をバイオマス資源から得られる点や、高強度の製品を金属よりも軽量で実現できる点でも、環境負荷の低減につながります。また研究開発をリードしてきた日本発の新素材であるという点で、日本の国際競争力向上にもつながります。そしてなにより、製品・部品の材料の選択肢が広がり、私たちの生活を、より豊かにすることでしょう。
「今後、CNF材料を自動車、建材、家電、日用品と、幅広く採用していただけるよう、性能面や供給面での研究開発をこれからも続けていき、さらに加速していけたらと考えています。そのためには、さらに大量に使われることも想定して、供給責任をとれるような体制を整えていく必要があります。『STARCEL®』を幅広く使っていただけるような商品提案をできるようになればと思っています」(河端さん)
開発者の横顔
紙のように使われる存在にしたい
岩田悟さんは、星光PMCの前身時代から、製紙用薬品の新規開発を手がけてきました。CNFの事業化では統括役を果たしてきました。
「CNF材料が、紙のようにごく普通に使われる存在になる世の中を実現することが、私たちの目指すところです。今回の成果は、NEDOが主導した集中研方式で企業の規模に関わりなく得意分野を持った企業が集まったからこそだと思います。NEDOプロジェクトを通じて社員たちが成長を遂げられました。ほかの企業やアカデミアとのネットワークができたことや、付き合いのなかった企業と話しやすくなったのも、参画した成果だと思います」
星光PMC株式会社
取締役/技術本部 本部長
岩田 悟 さん
しんどいときも、楽しいときも
佐藤明弘さんは、NEDOプロジェクト期間中、実際の研究開発を推し進めた中心人物です。京都大学宇治キャンパス内の研究室「ナノコア」で他組織からの研究者たちとともに、試行錯誤の日々を送りました。NEDO担当者も参加しての、毎月の成果報告会でも、研究の進捗などを発表しました。
「なかなか結果が出ないときも会議に出なければならないのはしんどかったです。でも、結果が出て、それをみなさんとディスカッションできたときは楽しかったですね」
星光PMC株式会社
CNF事業推進部 副部長
佐藤 明弘 さん
こたつを囲んでの話し合い
山田修平さんは、自社プラントでのSTARCEL®製造プロセスでの課題克服に貢献しました。NEDOプロジェクトでは、佐藤さん同様「ナノコア」での共同研究生活を送りました。
「まだそれほどセルロースに詳しくないときに集中研に参加したのですが、他の企業の方々も含めてみなさんに、私のわからないことを親切に教えていただきました。『ナノコア』は山小屋風の木造建築で、室内にはこたつもありました。時にはみんなでこたつに脚を突っ込んで話し合い、よいものを開発していこうと、一つになって研究開発に取り組めたと思います」
星光PMC株式会社
CNF事業推進部
山田 修平 さん
深い“友だち”になれたら
河端崇さんは、同社が培った技術を事業化に結びつけ、STARCEL®事業を発展させる役割を、当時も現在も担っています。
「以前に私が扱っていた化学製品は、同じ工程管理をすれば、同じ品質の製品になりました。一方、CNFは天然由来ということもあるのでしょう、同じ品質を保つのには苦労します。CNFともより深い“友だち”になれたらなと思います」
星光PMC株式会社
CNF事業推進部 部長
河端 崇 さん
21世紀のモノづくりはベジタリアン
京都大学の矢野浩之さんは、一連のNEDOプロジェクトや、それ以前の地域新生コンソーシアム研究開発事業(経済産業省)を含め、CNF複合樹脂の製造プロセスを確立・実用化するための取り組みで、リーダー役でありつづけてきました。貫いてきたのは、木という“材料の作り手”の考えに沿うことです。
「太古から資源循環のなかに組み込まれている植物を材料として使うことは、ごくまっとうなことだと思っています。最近、これから人間は植物由来のもので暮らしていくんだという意味を込めて『21世紀のモノづくりはベジタリアン』と言っています」
京都大学
生存圏研究所生物機能材料分野 教授
矢野 浩之 さん
なるほど基礎知識
CNFの特性を樹脂への混ぜ込み時に引き出す京都プロセス
セルロースは木や紙にも含まれますが、木や紙は手で簡単に折れたり、ちぎれたりします。ところが、セルロースが解きほぐされて、幅100nm以下、長さが幅の100倍以上のCNFになると、鋼鉄の5倍以上という高い強度を発揮するようになります。それはなぜでしょうか。
こうした幅と長さをもつナノファイバーでは、束全体としての表面積が大きくなります。例えば、髪の毛1本と、おなじ太さで束状にしたナノファイバーとでは、表面積は1対1000にもなります。表面積が増えることで、ほかの分子との結合部分となる官能基の数が増え、結合力が高まるのです。
また、ナノファイバーでは、セルロースの分子鎖が繊維に沿った方向にまっすぐ並びます。これで結晶化が起きやすくなり、強度が高まります。
加えて、CNFと樹脂が複合する際、分子が「シシケバブ構造」と呼ばれる高次構造を形成するため、これによっても強度が高まります(写真7)。
CNFと樹脂を混ぜ合わせた材料を作り、こうした特性を発揮させるには、製造段階のどこかで、木材由来のパルプの中で繊維の束になって埋もれているナノファイバーに出てきてもらわなければなりません。
そのためにパルプの繊維をナノファイバーまで解きほぐす「解繊」という作業をします。京都プロセスでは、CNFになる手前のパルプを解繊してCNFにしながら、同時にその出来たてのCNFを樹脂に混ぜ込んでしまう「パルプ直接混錬法」を特徴としています(図2)。
なお、CNFを得るための解繊の方法としては、TEMPOとよばれる有機化合物を触媒に用いた「TEMPO酸化法」という方法もあります。NEDOはともに実用化を進めてきました。
写真7 CNF複合樹脂におけるシシケバブ構造の電子顕微鏡像。画像中の太い幹のような部分がCNF (写真提供:星光PMC)
図2 京都プロセスの概要(資料提供:星光PMC/京都大学)
NEDOの役割
「グリーン・サステイナブルケミカルプロセス基盤技術開発」
(2009〜2015年度)
(NEDO内担当部署:材料・ナノテクノロジー部)
日本の化学品製造産業は、地球温暖化、資源枯渇など様々な課題を抱えています。NEDOでは、諸問題を克服し高機能な化学品の持続的製造を可能とする基盤技術の確立を目指し、多くの事業を展開してきました。
化学品原料転換に関するプロジェクトでは、京都大学を拠点として素材、樹脂メーカーの研究者が常駐する集中研方式により、軽量・高強度な特長を持った植物由来で環境にも優しい素材であるセルロースナノファイバー(CNF)の製造技術を開発しました。本事業の成果を基にして星光PMC株式会社は量産化を実現し、その後、株式会社アシックスのランニングシューズに採用されることになりました。
本事業の貢献により製品化まで達成し、また、本事業における産学官連携の取り組みや異分野企業とのマッチングの取り組みは、NEDOの他事業にも継承されています。
関連プロジェクト
お読みいただきありがとうございました。
ぜひともアンケートにお答えいただき、
お読みいただいた感想をお聞かせください。
いただいた感想は、
今後の連載の参考とさせていただきます。