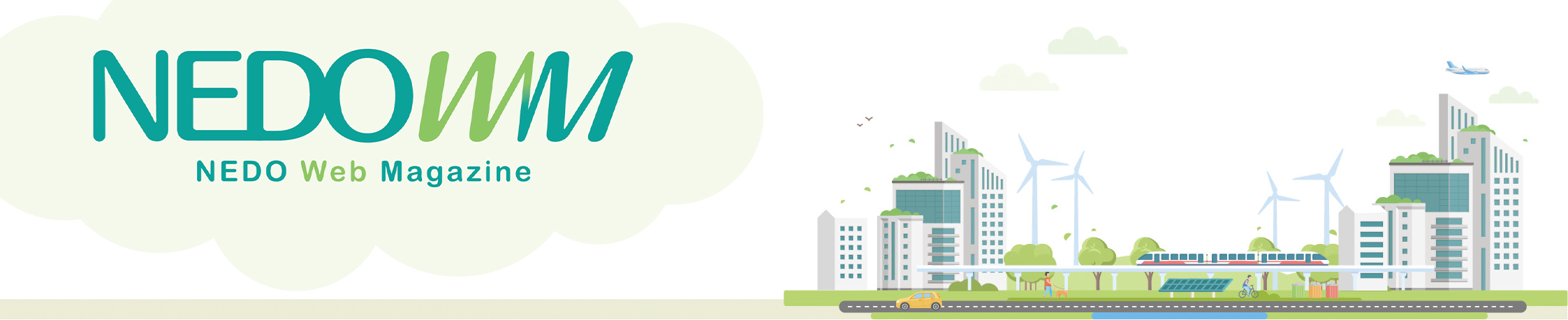
CONTENTS
BEGINNING
世界最高性能の金属3Dプリンターを日本から産み出したいBREAKTHROUGH
市場要望に合わせ「パウダーベッド方式」の造形方法を採用FOR THE FUTURE
複雑かつ高品質な金属造形のニーズに新たな選択肢FACE
「ものづくりをビッグビジネスに」INTRODUCTION 概要
金属粉末から3次元の造形物を作るための装置「電子ビーム金属3Dプリンター」の市場は長らく海外メーカーで占められる状況が続いていました。そこで、高性能な次世代金属3Dプリンターの国産化や日本製品のシェア拡大が産業界の大きな目標となりました。そうした状況の中、日本電子株式会社は、NEDOプロジェクト「次世代型産業用3Dプリンタの造形技術開発・実用化事業」(2017~2018年度)により、大型かつ高精度な金属造形物を作ることのできる電子ビーム金属3Dプリンターを試作し、「JAM-5200EBM」として2021年に実用化、販売を開始しました。造形範囲は最大直径250mm×高さ400mm、造形エリア全面のビーム径誤差は50μm以下で、医療分野における人工関節や宇宙航空分野のタービンブレードなど、複雑かつ高品質な造形が求められるものづくりでの利用拡大が期待されています。
BIGINNING 開発への道
世界最高性能の金属3Dプリンターを日本から産み出したい
電子ビーム金属3Dプリンターは、電子ビームを熱源に用いて金属材料から3次元(3D:3 Dimensions)の造形物を作る装置です(詳細は「なるほど基礎知識」参照)。
金属材料から3次元の造形物を作るという点では、日本は金型鋳造を長年にわたり得意としてきました。一方、そうした技術が発達していない欧米では、2013年2月に、バラク・オバマ米大統領(当時)が、一般教書演説で「3Dプリンターは、あらゆるものづくりに革命をもたらす可能性を秘めている」と述べたように、国家戦略としていち早く3Dプリンターの研究開発に着手していました。
日本でもオバマ演説以降、金属3Dプリンターの技術開発に向けた取り組みが本格化しました。経済産業省が2013年10月より「新ものづくり研究会」を開催し、2014年2月の調査報告書で「(産学官による)金属積層装置や材料、ソフト等の一体の技術開発」の必要性を指摘するなど、金属3Dプリンター開発への機運が高まってきました。
そうした中、電子顕微鏡や半導体フォトマスク製造装置などの事業で、電子ビームの技術を培ってきた日本電子は、新たな事業として電子ビーム金属3Dプリンターの開発に乗り出しました。
長年の電子ビーム技術の知見を金属3Dプリンター開発へ
日本電子株式会社取締役兼専務執行役員の田澤豊彦さんは同社のねらいについて、「理科学・計測機器、産業機器、医用機器という弊社事業の3セグメント中の産業機器セグメントに金属3Dプリンター事業を加えて事業拡大していくことが、大きな社会貢献につながると認識したからです」と説明します。
日本電子が、電子ビーム金属3Dプリンターの開発に着手する直接的なきっかけとなったのは、2013年、電子ビーム積層造形の専門家である東北大学の千葉晶彦教授の研究室へ招かれたことでした。千葉研究室にはスウェーデン製の電子ビーム3Dプリンターが導入されており、日本電子の社員たちは、電子ビームを用いて部品を作る、その装置を「驚き」をもって受け止めました。それと同時に、日本電子が持つ長寿命かつパラメータを自由に変えられる電子ビーム技術で、いろいろな金属の造形ができないかと、相談を受けました。
日本電子株式会社開発・基盤技術センター長の眞部弘宣さんは当時のことを、「初めて金属3Dプリンターに触れて、3次元造形技術に弊社が扱ってきた電子ビームが貢献できることを知り、驚きました。同時に私たちなら、電子ビームがさらに長寿命かつ性能が高くて使いやすい機器を提供できるのではとも考えました」と振り返ります。
こうして日本電子は、2014年、経済産業省のプロジェクト「三次元造形技術を核としたものづくり革命プログラム(次世代型産業用3Dプリンタ等技術開発)」の開始とともに技術研究組合次世代3D積層造形技術総合開発機構(TRAFAM)の一員となり、プロジェクトに参画しました。その後継である2017年度開始のNEDOプロジェクト「次世代型産業用3Dプリンタの造形技術開発・実用化事業」にも引き続き参画して、電子ビーム金属3Dプリンターの実用化に向けた研究開発を進めていくこととなりました。
BREAKTHROUGH プロジェクトの突破口
市場要望に合わせ「パウダーベッド方式」の造形方法を採用
金属3Dプリンターの代表的な造形方法には「パウダーベッド方式」と「デポジション方式」の二つの方式があります。
「パウダーベッド方式」は、原材料である金属粉末を1層敷き詰め、熱源となるレーザーや電子ビームで造形する部分を溶融して積み重ねてゆき(積層造形)、積み重なった塊から不要な粉末を取り除いて、完成品(造形物)を取り出します(詳細は「なるほど基礎知識」参照)(写真1)。
一方「デポジション方式」は、金属粉末を搬送ガスでノズルから噴射すると同時に一般的にはレーザーで溶融して目的の場所に積層していきます。日本電子が研究開発を始める前の2013年に市場調査を実施した結果、電子ビーム方式の市場の9割以上が「パウダーベッド方式」を要望していることが判明しました。これを受けて日本電子は、「パウダーベッド方式」による実用化研究開発を選択しました。
写真1 1層分だけパウダーベッドに敷き詰められた金属粉末材料。直径260mm
厄介なスモークをヘリウムフリーで回避するシールドを開発
電子ビーム3Dプリンターの長年の課題は、電子ビームと金属粉末が起こす「スモーク現象」の克服でした。海外の既製品ではそれを避けるために、積層工程では高価なヘリウムガスを使用しなければなりませんでした。また、造形物1個を作るたびに、電子ビームを放出する素子である「カソード」の交換が必要でした。
「スモーク現象」とは、電子ビームの照射で金属粉末が帯電し、粉末同士が反発して飛散してしまう現象を言います。「スモーク現象」が生じると、うまく積層ができずに造形物が作れないだけでなく、カソードなどの素子にもダメージを与えてしまいます。
その解決策として金属粉末の帯電を抑えるため、金属粉末に予備加熱を行う方法があります。これは金属粉末の温度上昇によって粉末同士が軽く結合する仮焼結状態になることで電気抵抗が低下する現象を利用して、「スモーク現象」の発生を抑える方法です。既存の海外製品では「スモーク現象」を抑えるために、帯電抑制効果のあるヘリウムガスをチャンバー内に導入する方式を採用していました。
しかし、ヘリウムガス方式は海外メーカーの特許技術で、日本電子では採用しにくい状況でした。また、世界的な消費量増加などもあり、ヘリウムガスを使うこと自体が高コストの要因となる可能性もありました。
「そこで、ヘリウムガスを使わずにスモーク現象を回避することを考え、金属粉末の飛散などを物理的に防ぐ仕組みを開発することにしました」と日本電子株式会社3D積層造形プロジェクト技術グループ専任理事の北村真一さんは話します。「こうして『e-Shield』の開発に至りました」(北村さん)
北村さんの言う「e-Shield」とは、造形領域より外側のサラサラした粉末が散乱電子によって帯電するのを防ぎつつ、帯電した金属粉末が飛散して散乱電子が加わり、その帯電領域でさらなる「スモーク現象」が発生するのも防ぐ、ステンレス製遮蔽板のことです。この仕組みを加えることで、ヘリウムガスを使わずとも「スモーク現象」を回避できるようになりました。また、「e-Shield」の導入で予備加熱の温度も低くできました(写真2)。
写真2 チャンバー内に、積層造形スペースを囲うように設置された「e-Shield」
日本電子には、半導体集積回路などの製造工程でシリコン基板上に回路パターンを作るためのフォトマスク製造用電子ビーム装置(マスクライター)の分野で帯電抑制技術の開発経験がありました。それが活かされた形ですが、「安定的にシールドを機能させるという点では、かなり試行錯誤が必要でした」と北村さんは言います。
田澤さんは、「予備加熱により造形物周囲の金属粉末が仮焼結しますが、金属粉末の再利用を考えると仮焼結を最小限に抑えたかったのです。『e-Shield』は、仮焼結を最小限に抑えつつ、スモークを避けるための、我々の最善策でした」と加えます。
「e-Shield」の実装で、ヘリウムガスを使わず「スモーク現象」を回避させ、仮焼結を最小限化し、カソードへのダメージを低減できました。これらにより、装置を安定的に使える高い信頼性や、ヘリウムが不要でカソードの交換周期を長くできることによる低コスト化を実現できました(写真3)。
写真3 仮焼結体で覆われた造形物(左)。仮焼結体を除去していくと、次第に完成品がその姿を現してくる(中央と右)
高出力・高精度な電子ビーム技術を追求し「世界最高」を実現
大きな造形物を高精度で作製するという造形技術面でもブレークスルーがありました。大きな造形物を作るには、高出力の電子ビームが必要となります。低出力の電子ビームでは、積層に時間がかかり、加熱しているそばから必要な熱が失われてしまい、大きな造形物を作るには不向きだからです。
とはいえ、電子ビームを高出力にすればするほど、形状を高精度に作ることが難しくなります。このトレードオフの状況に対し、日本電子株式会社3D積層造形プロジェクト技術グループ長の佐藤崇さんは、「高出力の電子ビームをダイナミックに補正するための技術と、そのためにビームを正確に測定する技術を追求しました」と話します。
電子顕微鏡のトップメーカーとして知られる日本電子ですが、電子顕微鏡で扱う電子ビームの出力はミリワットレベル(mW)であるのに対して、今回の金属3Dプリンターの研究開発での実用化目標出力は6kWにもなり、100万倍レベルの出力になります(写真4)。
この高出力6kWの電子ビームを、いかに高精度に制御していくのか、そこで佐藤さんらが追求したのが、「補正」の技術と、補正のための「測定」の技術です。「これらの実現には苦労がありましたが、プロジェクトでの大きな成果の一つです」と佐藤さんは言います。
写真4 「JAM-5200EBM」の電子銃
電子ビームは、直径250mmのパウダーベッドのさまざまな位置に照射されていきます。このとき電子ビームはビーム偏向に伴う像面湾曲と非点収差の影響を受け、照射する位置によってビームの焦点のボケやビームの形状に歪みが生じます。この状態で積層造形させていくと、造形物も不均一な溶融状態となってしまうため、電子ビームを照射しつつビームの焦点や形状に補正をかけていかなければなりません(写真5)。
写真5 「JAM-5200EBM」の電子銃ビーム照射口
とはいえ、補正をかけるにも、どの程度補正をかければよいのか、その手がかりがなければ、正確な補正ができず、結局は造形物に内部欠陥ができてしまいます。そのため電子ビームの状態をきちんと計測する技術も必要となります(図1)。
図1 電子ビーム自動調整機能の無しの場合(左)と、有りの場合(右)では、ビームの先端形状が異なってくる (イメージ画像) (資料提供:日本電子)
佐藤さんらは、電子顕微鏡や半導体製造用電子ビーム描画装置で培った技術により、金属3Dプリンター向けに計測・補正の技術を高めていきました。「他社が文献で示している数値を見るかぎりは、我々の計測・補正の技術のほうが直接計測する点で優れていると思います」(佐藤さん)
世界最高レベルの製品を実用化
2014年度から2018年度までの足かけ5年間のプロジェクトで日本電子が開発したのが、パウダーベッド方式の電子ビーム金属3Dプリンター「JAM-5200EBM」です(写真6)。電子ビームを放出する素子「カソード」の寿命1,500時間以上、また既存装置で必須だったヘリウムガスが不要といった特長があり、信頼性の向上やコスト削減を実現しました。造形の性能面では、直径250mm×高さ400mmの大型造形物を作製できます(写真7)。
写真6 日本電子が開発した電子ビーム金属3Dプリンター「JAM-5200EBM」
写真7 造形品のサンプル(左)。中央の網球状の造形物には同様の造形物が内包されている(右)。造形物の中に別の造形物を一度の工程で作製できることも、この3Dプリンターならではの特長
日本電子は自社で培ってきた電子ビーム技術などを活用するとともに、自社が持っていなかった新たな技術を他社との連携で構築することで、この電子ビーム金属3Dプリンターを実用化しました。
眞部さんは、「6kWの電子ビーム出力で、造形エリア全面のビーム径誤差が50μm以下の精度というのは世界最高レベルと自負しています。この装置は、金属を溶融するための高出力な電子ビームを用いますが、通常はこのような高出力電子ビームを計測しようとすると、測定系が損傷してしまい正確なビーム計測は困難です。しかし、佐藤は高出力電子ビームでも正確に安定してビーム計測できる他社にはない技術を開発しました。補正という点でも、他社はレンズの構成を考えて工夫を施していますが、佐藤は独自の計算ソフトウェアも駆使しました。それにより世界最高レベルを実現できているのです」と佐藤さんの努力を強調します。
「ほぼ集中研方式」で未踏技術を確立し、ソリューションを構築
このように、日本電子が半導体関連装置や電子顕微鏡で培ってきた技術を活用できた部分はあるものの、当然ながら電子ビーム金属3Dプリンターの開発で新たに必要となった技術もありました。そうした新たな技術を得るために大きな助けとなったのが、プロジェクトに参画した大学や企業などとの連携でした。
眞部さんは、「よくあるプロジェクト連携方式は、参画メンバーが別々に技術開発をして、それを統合させるものです。一方、今回は、『ほぼ集中研方式』といってよいぐらい参画メンバーが大学、企業の垣根を越えてチーム一体で取り組み、成果を上げました」と振り返ります。
「集中研方式」とは、プロジェクト参画メンバーの研究開発者らが、一つの場所に集まって研究開発を行う方式のことです。本プロジェクトでは、電子ビーム方式の金属3Dプリンターの開発を進める日本電子などのTRAFAM会員企業がNEDOのマネジメントのもとでチームを結成し、連携を図りました(図2)。
図2 TRAFAM会員企業で構成された、NEDOプロジェクトの研究開発体制
日本電子にとって、電子ビームで金属粉末を溶かし、緻密な造形物を製作する技術の開発は初挑戦でした。そこで佐藤さんらは、参画メンバーによる月に一度の定例会で、サブプロジェクトリーダーの千葉教授から、金属粉末が溶けて液状化したメルトプール(溶融池)に関する理論の講義を受けたり、千葉研究室にある海外既存製品でのメルトプールの形成を撮影してもらったりして、自分たちの装置での最適な溶かし方を追求していきました。
また、企業との連携では、「金属粉末メーカーから金属粉末の性質などに関する知見を得ることができました。電子ビームで金属粉末をいかに溶かして固め、積層造形の質を高めるかという、日本電子にとっての新たな技術開発に生かすことができました」と佐藤さんは説明します(写真8)。
写真8 「JAM-5200EBM」に使用されている金属粉末
粉末種類(左) 電子ビーム金属3Dプリンターの金属粉末収納部(中) 材料容器に入った金属粉末材料(右)
田澤さんは、「金属粉末を高温に晒しても粒子同士が固まらず、1粒子ずつ分散するような粉末供給技術を、金属粉末メーカーの知見も生かして確立できました。通常はクローズドな知見を積層造形技術のために私どもに提供していただけたのは、やはりNEDOプロジェクトでの連携の大きな成果です」と語ります。
眞部さんも、「金属粉末メーカー、ソフトウェア開発企業、装置メーカー、後加工の技術を持つ企業、さらにユーザーの立場の企業までが、ワンチームとなれたことで、装置単体の提供でなく、ソリューションの提供を目指すことができました」と、NEDOプロジェクトで企業が連携したことの成果を強調します。
FOR THE FUTURE 開発のいま、そして未来
複雑かつ高品質な金属造形のニーズに新たな選択肢
自社で培った技術と、他社から得られた技術が集結し、電子ビーム金属3Dプリンター「JAM-5200EBM」は完成し、2021年3月に販売開始となりました。
眞部さんは、「3月の発売発表直後から多数のお問い合わせをいただいています。金属3Dプリンターの利用を検討しておられる企業とは、造形物作製のデモンストレーションも進めているところです」と話します(2021年10月現在)。
日本電子は装置単体の販売にとどまらず、ソリューションの提供を目指してきたことから、「JAM-5200EBM」は使用時の利便性でも評価を得ています(写真9)。
「装置がどこにあっても、得たい形状のデジタルデータを送信すれば造形は可能です。また、造形状況や装置状況を、スマートフォンなどを介して遠隔監視していただくことも可能です」(眞部さん)
今後、積層造形のデータが蓄積されていけば、それらのデータを人工知能に分析させることで、不具合を未然に防ぐメンテナンス法も確立できると言います。
写真9 造形物の元データとなる3次元計算機支援設計(3DCAD:3 Dimensions Computer-Aided Design)データ(左)と、「JAM-5200EBM」本体のモニタ(右)
写真10 仮焼結した金属粉末を除去中の発電用のタービンブレード(左)と、除去後、磨きだして完成したもの(右)
金属3D造形技術をめぐる競争はこれからも続く
今回、日本電子から金属3Dデジタルプリンター「JAM-5200EBM」が製品化されたことは、日本が強力な技術を携えて金属3D造形技術の競争舞台に立ったことを意味します。日本電子の開発者たちも、今回の実用化、製品化はゴールでなくスタートであるという意識を強く抱いています。
田澤さんは事業推進役の立場から、「ものづくりに3Dプリンティング技術がさらに活用されていく状況を目指します。理解者を増やしながら挑んでいきたい」と抱負を語ります。
佐藤さんは技術開発者として、「金属3Dプリンターの方式としては、私たちの電子ビーム方式のほか、レーザー方式などもあり、競争が激しいことは承知しています。性能面の向上は当然ですが、価格面でも多くの方に魅力的に感じてもらえるよう努力していきたい」と一層の製品競争力の向上を誓います。
北村さんは、「造形をしながら、状況をモニタリングして欠陥を未然に防ぎ、品質を保持していくような装置にレベルアップすることを考えているところです。今後も技術開発で品質をよくしていきたい」と具体的な目標を話します。
眞部さんはより俯瞰的に社会状況を見据え、「日本は3D加工技術の人材がまだ少ない状況です。米国では小学校で、3Dプリンター用樹脂を子どもたちに配布し、教育をしています。今後、日本では開発された装置をいかに使っていくかの発想力が求められます。ぜひ学生や企業の若手の方にも、私たちが開発した装置に触れていただきたい」と人材育成の重要性を強調します。
今後の金属3D造形技術をめぐる国際競争では、装置・ソリューションの普及や人材の育成により利用の輪が広がっていくこと、そして継続的な技術向上が欠かせません。
NEDOも、後継プロジェクトとして「積層造形部品開発の効率化のための基盤技術開発事業」(2019~2023年度)を実施しており、金属積層造形技術の更なる高度化、効率化を目指して研究開発を進めています。
自社の長年の看板製品である電子顕微鏡や半導体マスクライターの得意技術を基盤に、NEDOプロジェクトにより、川上の材料メーカーから川下のユーザーまでの技術や知見を集結して実現した電子ビーム金属3Dプリンター「JAM-5200EBM」が、製品として開花していくばかりでなく、ものづくり分野における日本の将来を開くツールとなることが期待されます。
開発者の横顔
「ものづくりをビッグビジネスに」
3D積層造形事業化プロジェクトを2016年より担当する田澤さんは、大学では化学を専攻していました。1984年に日本電子へ入社してからは、顕微鏡技術と分析技術を組み合わせた表面分析装置の開発や事業展開を担ってきました。
電子ビーム金属3Dプリンター事業について「ものづくりという、弊社の看板事業である顕微鏡の世界とはまた違う、より大きな対象物の世界で貢献していきたい。その観点から、日本発の金属3Dプリンターで成果を上げていきたいと思っています」と話します。
同時に、「さまざまな金属材料で多様な造形物を作っていき、ライブラリーのようなものを構築できれば面白いと思います」と、開発者の顔も見せます。
日本電子株式会社
取締役兼専務執行役員
田澤 豊彦 さん
「一から携われることに魅力がある」
佐藤さんは、日本電子に新卒入社後、半導体事業でマスクライターの開発に携わり、電子銃などの技術開発を担当してきました。そうした経験を生かして、電子ビーム金属3Dプリンターの開発プロジェクトに参加しました。
「メーカーでは、既存技術を改良する仕事は多くあると思いますが、今回のように全く新しい技術や製品、ソリューションを開発する経験はそう多くないでしょうし、一から携われるところに魅力を感じてきました。学生時代、千葉晶彦先生がおられる東北大学で金属材料の勉強をしていました。千葉先生にお会いできたり、再び金属材料に向き合ったりしていることにも感慨深さがあります」
日本電子株式会社
3D積層造形プロジェクト 技術グループ グループ長
佐藤 崇 さん
なるほど基礎知識
パウダーベッド方式の電子ビーム金属積層造形技術
金属材料を3次元形状で使う場面はさまざまあります。中でも、医療分野や航空宇宙分野などでは、チタンなどの加工しづらい金属材料を用い、人工関節や航空機向けの複雑な形状の製品を作りたいというニーズがあり、そうした金属造形物を作るための手段の一つが、今回の「電子ビーム金属3Dプリンター」です。
電子ビームとは、「電子銃」という装置の先端にある、電子放出のための電極「カソード」から高速に放たれる電子の細い流れのことです。電子ビーム金属3Dプリンターでは、この電子ビームを熱源にして、造形物の原料となる金属材料を瞬時に溶かしてから固め、それを積層させていき、目的の形の造形物を得ます(図3)。
図3 電子ビーム金属積層造形の流れ (資料提供:日本電子)
金属3Dプリンターには電子ビーム方式のほかに、レーザー光を用いるレーザー方式があります。レーザー方式では、電子ビーム方式と同様、金属粉末を溶かし固めて造形しますが、金属材料によっては反射が起きるため不向きなものもあります。
それに対し、電子ビーム方式では、電子が金属粉末に衝突し、運動エネルギーが熱に変換されるため、どんな金属材料も高い熱変換効率が得られるという特長があります。
また、電子ビーム金属3Dプリンターにもいくつかの方式があります。日本電子の「JAM-5200EBM」では「パウダーベッド方式」が採用されています。
「パウダーベッド」とは、金属材料の粉末(パウダー)を敷き詰めたベッド(床)の層のことです。そこに電子ビームが照射されると、熱でその粉末が溶けてから固まり、一層分が作られます。これを何度も繰り返すことで積層され、最終的に目的の形の造形物が完成します(写真11、12)。
写真11 パウダーベッド方式による電子ビーム金属積層造形法
(左から)1.造形物の3Dデータを入力。2.金属粉末を1層分敷き詰めてパウダーベッドを用意。3.電子ビームを照射し粉末を溶かしてから固める (写真提供:日本電子)
写真12 パウダーベッド方式による電子ビーム金属積層造形法の続き
(左から)4.基板を1層分下げて、再びパウダーベッドを用意。5.電子ビーム照射・溶融・凝固を繰り返す。6.最終層まで繰り返し、仮焼結された粉末を除去 (写真提供:日本電子)
NEDOの役割
「次世代型産業用3Dプリンタの造形技術開発・実用化事業」
2017~2018年度
NEDO内担当部署:IoT推進部
3Dプリンター市場は、海外製品のシェアが高く、言語・距離などの制約により、ユーザーは迅速かつ十分なサポートが受けられない、コストが高いといった問題があり、国内企業の競争力を確保するために国産の高性能3Dプリンターが望まれていました。
NEDOは本プロジェクトで、次世代のものづくりを持続的にリードするため、少量多品種で高付加価値の製品・部品の製造に適した三次元積層造形技術の開発・実用化を目指しました。
その際、民間企業単独では取り組むことが困難な技術開発に対し、大学、公的研究機関を含めた産学官それぞれのノウハウを持ち寄る場を提供しました。
その結果、本プロジェクトにおいて、電子ビーム金属3Dプリンターや鋳造用砂型3Dプリンターが実用化されたほか、造形装置に相応しい金属粉末材料を生産する技術などが確立されました。
開発された成果は、今後、医療分野における人工関節や宇宙航空分野など、複雑かつ高品質な造形が求められるものづくりでの利用拡大が期待されています。
関連プロジェクト
お読みいただきありがとうございました。
ぜひともアンケートにお答えいただき、
お読みいただいた感想をお聞かせください。
いただいた感想は、
今後の連載の参考とさせていただきます。