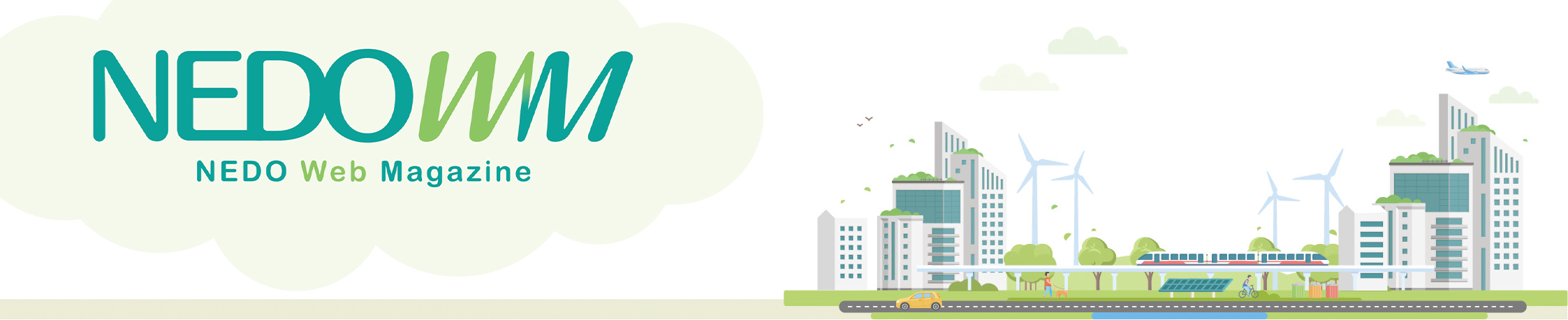
CONTENTS
INTRODUCTION
CNF関連製品を市場に送り出すBEGINNING
地球上に最も多く存在する生物資源BREAKTHROUGH
企業を動かしたCNFの魅力とはFOR THE FUTURE
食べられるCNFの開発FACE
ニーズではなくシーズから生まれた研究成果INTRODUCTION 概要
CNF関連製品を市場に送り出す
強度は鉄の5倍で重さは鉄の5分の1――。植物由来のセルロースナノファイバー(CNF)は、循環型社会実現への“夢の新素材”と期待されています。自動車車体などが鉄からCNF配合強化樹脂に換われば、軽量化による大幅な燃費向上が可能です。CNF自体の環境負荷は低く、燃焼時のCO2排出は実質ゼロ(カーボンニュートラル)、土壌に埋めても微生物によって分解されます。それだけでなく、CNFは紙の需要が減少する製紙業界にとって新たな成長分野に位置付けられています。紙の原料であるパルプから均一なCNFをつくる技術は、東京大学が2006年に確立しました。その周辺技術をNEDOプロジェクトで東京大学らと共に開発、実用化の道を拓いたのは日本製紙株式会社です。その後、同社はCNFに抗菌・消臭機能を付与した機能性シートの開発に世界で初めて成功し、2015年には子会社の日本製紙クレシア株式会社から、大人用紙おむつ「肌ケア アクティ」シリーズをCNF関連製品として世に送り出しました。
BIGINNING 開発への道
地球上に最も多く存在する生物資源
セルロースナノファイバー(CNF)とは、セルロース分子が直鎖状に並んだ極細の繊維のことです。1本のCNFの太さは3~4nm(ナノメートル)。髪の毛の太さは0.05~0.08mm程度ですから、その1万分の1よりも微細な繊維です(写真1)。
写真1 製紙用パルプをナノサイズまで解きほぐした(解繊した)極微細の天然繊維、セルロースナノファイバー(写真提供:日本製紙)
セルロースは植物の主成分の一つで、地球上で最も多量に生産・蓄積される生物資源です。樹木の重量の約4割を占め、地球上で最も多く存在する多糖類でもあります。
「セルロース分子鎖30~40本が直鎖状に連なってセルロースミクロフィブリルを形成し、それらが集合してミクロフィブリルの束となります。その束がさらに集まって『植物繊維』をつくり、植物繊維同士がリグニンと呼ばれる接着成分によって強固に結び付けられ『植物繊維集合体』となり、それらが集まって樹木を構成しています(図1)」
図1 樹木中のセルロースミクロフィブリルは、地球上で最大蓄積量・最大年間成長量のバイオ系ナノ素材(資料提供:東京大学 磯貝教授)
東京大学大学院農学生命科学研究科教授の磯貝明さんは、樹木の階層構造を説明します。
画期的な技術を⽣んだ研究の始まり
セルロース分子の集合体であるセルロースミクロフィブリルは、人工的には得られない優れた特性を多く備えています。樹木からミクロフィブリルの単体もしくは集合体を分離する試みは1980年代から検討され、集合体を分離する技術の一部は実用化されてきましたが、ミクロフィブリル単体の分離は長く実現できずにいました。
その壁を越えたのは2006年のこと。磯貝さんらが、画期的な技術を確立したことによります。その技術の名は「TEMPO酸化法」といいます。「TEMPO」とは触媒に使う有機化合物2,2,6,6-テトラメチルピペリジン 1-オキシル (2,2,6,6-tetramethylpiperidine 1-oxyl)の略称です。
磯貝さんは、自身が大学院生だった1980年代当時、セルロースをはじめとする多糖類の化学構造変換の研究に取り組んでいました。セルロースの化学反応を制御し、高分子合成のように新しい物質を作り出すことを考えていたと言います。
1995年、そうした模索の只中で、磯貝さん(当時は助教授)はふとした偶然からTEMPOと出会います。TEMPOを触媒に使いデンプンの化学構造を変えるという、オランダのある研究チームの論文をたまたま見つけたのがきっかけでした。
「彼らは有機溶剤をまったく使わず、水系の常温常圧下で、TEMPOを触媒量(ごく少量)だけ使ってデンプンの化学構造を変えて水に溶かす成果を出していました。デンプンもセルロースと同じ多糖類です。TEMPOでデンプンの化学構造を変えられるなら、セルロースでも面白い反応が起こるのではないか。そういう期待で、1996年にTEMPOを使ったセルロースの化学構造変換の研究に着手しました」(磯貝さん)
やりつくした先の「世紀の発見」
「セルロースが水に溶けたら面白いだろうと、何年もかけてさまざまな実験を試しましたが、なかなかうまくいかない。TEMPOを触媒に使うと、セルロースの集合体であるパルプが白くなることは分かりましたが、それでは大して面白くない。考えつきそうな実験はやり尽くしたし、もう八方塞がりかなと思っていた時、研究室に入ってきたのが齋藤継之さんでした」(磯貝さん)
この研究の活路が見出されたのは、2006年のことです。大学院博士課程に在籍していた齋藤さんが、短期留学先のフランスで世紀の発見をします。
「TEMPOを触媒量入れた水にパルプを入れ、超音波で振動を加えたら、あれほど溶けなかったパルプが水に溶けたのです。白濁していた溶液が次第に透明になったと、興奮気味で連絡してきました」(磯貝さん)
調べてみると、パルプを構成しているセルロースミクロフィブリルが、一本ずつ分離していました。ミクロフィブリルの太さは3~4nm。対して光(可視光)の波長はおおよそ400~800nm。ミクロフィブリルは光の波長と比べてもはるかに細いため光が反射せず、透明に見えるのです(写真2)。
写真2 (左)透明TEMPO酸化セルロースナノファイバー/水分散液の写真。(右)直交偏光板間で観察すると、液晶状の模様が観察できる。(写真提供:東京大学 磯貝教授)
磯貝研究室ではその後も実験を続けて反応条件を調整し、均一なCNFを安定的に作る技術を確立しました。
繊維を⼀つずつ解きほぐす電気の⼒
TEMPOを触媒に使う方法で、それまで困難だったセルロースミクロフィブリルの単繊維化が可能になったのはなぜでしょうか。
ミクロフィブリル同士は、表面が水素結合によって緊密に結び付いています。それがミクロフィブリルの単繊維化を困難にしていた大きな理由です。従来の方法は、このミクロフィブリル同士のつながりを、機械的に(物理的に)解きほぐそうとしていましたが、ミクロフィブリルの束を作るところまでが限界でした。この従来の方法を「機械解繊」といいます。
「パルプをTEMPOによって処理すると、ミクロフィブリルの表面のみがイオン化され、ミクロフィブリル同士が電気的に反発する力が生じます。すなわち、ミクロフィブリル同士の結び付きが弱まります。その状態で、超音波やミキサーなどで物理的せん断力を加えると、ミクロフィブリルが一本ずつほぐれていきます。その結果、単一のミクロフィブリルを安定して取り出せるようになりました(図2)」(磯貝さん)
図2 セルロースミクロフィブリル表面に、マイナス荷電を有するカルボキシ基を規則的に、高密度で生成することにより、3nmの超極細均一幅セルロースナノファイバーへの完全分離・分散が可能(資料提供:東京大学 磯貝教授)
この、単一のセルロースミクロフィブリルこそがCNFです。こうして単一のミクロフィブリルを安定して取り出せるようになったことが、TEMPO酸化法の画期的なところです。
BREAKTHROUGH プロジェクトの突破口
企業を動かしたCNFの魅力とは
ところが磯貝研究室では、できたこのCNFをどう活用すればよいか分からなかったと、当時を振り返ります。
「植物からナノ材料ができた。直感的に面白そうだとは思いましたが、これを何にどう使えばいいかは、正直まったく見当がつきませんでした。そこで、我々の研究室の先輩や教え子たちがいる企業にできたばかりのCNFを持ち込んで、一緒に研究開発しませんか、と持ち掛けました」(磯貝さん)
多くの企業が、何に使えるか分からないこの新たな素材に対して渋い反応を見せる中、「面白そうだね」と共同研究に乗った数社のうちの一社が日本製紙でした。
磯貝さんが日本製紙を訪ねた2006年、打ち合わせの場に同席していたのが、今では同社の研究開発本部長代理にして、CNF研究所所長を務める河崎雅行さんです。河崎さんは、その時の印象を次のように語ります。
「磯貝先生が透明なドロっとした液体を持ってこられたのをよく覚えています。正体は水に分散させたCNFです。非常に粘度が高く、これだけドロドロしたものを工業的に扱えるのか。そもそもどういう用途があるのか。いろいろ疑問に思っていたら、横に座っていた当時の研究開発本部長が『何に使えるか分からないけれど、面白そうな材料だから一緒にやりましょう』と。その場で共同研究を始めることが決まりました。当時はまだ紙の需要も伸びている状況でしたが、紙以外の未来事業を開拓する目的で、私自身も紙の研究に取り組みながら、CNFの研究を始めました」(河崎さん)
磯貝さんも、当時のことを次のように振り返ります。
「研究開発に協力してくださった企業の方々からは、CNFの均一性に、先端素材としてのポテンシャルを感じる、と口々に言われました。均一でなければ一定の性能が出せないからです。CNFの太さが3~4nmで安定するのは、TEMPO酸化法ならではの特長です。企業の方々は、そこに素材としての魅力を感じてくださったのです」(磯貝さん)
従来の機械解繊の技術でも、ナノスケールのミクロフィブリルの束は実現されていて、一部は市販もされていましたが、それらは不均一で水に分散させても透明になりませんでした。TEMPO酸化法ならではの均一性が、企業を動かす決め手になったのです。
写真3 (左上)機械処理のみの白濁したCNF分散液(固形分1%)。(右上)白濁したCNF分散液の顕微鏡写真。ミクロフィブリルの束が分散。(左下)TEMPO酸化と機械処理を組み合わせることで完全ナノ分散が可能になり、高透明性のCNF分散液が得られる(固形分1%)。(右下)高透明性のCNF分散液の顕微鏡写真。ミクロフィブリルが一本ずつ分離(青矢印、黒矢印)(写真提供:日本製紙)
CNFの研究を始めた日本製紙は、CNFに関する知見が社内でなかったため、東京大学で行われていた実験の再現から開始しました。用途も含め本当に実用化が達成できるのか道筋が見えなかったことが大きな課題でした。そこで2007年に、東京大学と日本製紙は製品メーカー数社と連合チームを組み、NEDOの「ナノテク・先端部材実用化研究開発/セルロースシングルナノファイバーを用いた環境対応型高機能包装部材の開発」プロジェクトに応募し採択されました。
生産効率をとるか、扱いやすさをとるか
日本製紙が最初に直面した困難は、あるトレードオフをいかにして解決するかでした。
「CNFは、水に数%分散させただけで粘度が高くなってドロドロになります。直感的に、粘度の高いものは工業的に扱いにくい。濃度を下げれば粘度も下がりますが、それではほとんど水を扱うことになって生産効率が低下します。生産効率を考えれば濃度を高くしたいですが、扱いやすさを考えれば濃度を低くしたい。そのトレードオフをいかに解決するかが最初の難題でした」(河崎さん)
この難題をクリアするため、NEDOプロジェクトにおいて生産効率を向上する検討を始めました。
「100LのタンクでCNFを効率的に生産するさまざまな方法を検証しました(写真4)。一連の検証作業の結果、CNFを配管で送るには非常に特殊なポンプや攪拌装置などが必要であることが判明しました。それでも、扱える濃度の限界は数%程度。100Lのタンクで固形のCNFがやっと数kgできる計算です」(河崎さん)
写真4 CNF研究所に設置されているTEMPO酸化CNF製造装置
CNF実用化に向けた取り組み
「NEDOプロジェクトの前半の3年間ではTEMPO酸化の基礎的な技術開発や、基本特許の取得を目的に、多くの基礎データを蓄積することができました。そのデータを活用し後半の3年間では、製品化・実用化を目的とした検討を進めました。製品化・実用化に関してはできるだけ口を挟まないように企業主導で個別に進め、技術的課題が出てきた場合には、大学も含めて議論するようにしました」(磯貝さん)
さらに日本製紙の奮闘ぶりを、磯貝さんは次のように評価します。
「日本製紙さんに進めていただいたことの中で一番大きいのは、TEMPO酸化の反応条件を最適化して、製造コストを劇的に下げたことでしょう。私たちが研究室で確立した方法だと、乾燥CNFを1kg作るのに数万円はかかっていました。触媒に使うTEMPOがとにかく高い。触媒量とはいえ、CNFを大量に作ろうとすると、このTEMPOの価格がボディブローのように効いてきます」(磯貝さん)
TEMPOをいかに少量にして、反応収率を上げるか。日本製紙はそういう基礎的な研究を繰り返し、TEMPO酸化法でCNFを効率的に作るための方法を洗練させていきました。まずはビーカースケールから100L程度の実験機スケールでの検証をしました。原料パルプの種類を選定し、TEMPO触媒の種類、酸化剤、助触媒などの添加量、添加方法の最適化を行いました。それにより製造コストが劇的に下がり、日本製紙はCNFの製法に関連する周辺特許をいくつも取得しました。そして、NEDOプロジェクト後半で検討を行ったのは、高機能な包装部材の用途開発でした。
「プラスチックフィルムや紙にCNFを塗ると、酸素を通しにくくなる性質があることが分かっていました。そこで、CNFを食品や医薬品の包装部材として使えば、食品・医薬品の酸化防止になって賞味・消費期限を延ばすことができます。しかも、ほとんどの包装部材は使い捨てです。プラスチックでできたフィルムを燃やすとCO2の放出になりますが、植物由来のCNFを用いることでCO2の低減につながります」(磯貝さん)
“脱製紙”へ向け、世界で初めてCNFを商品化
展示会を通じたCNFの宣伝活動、経済産業省への働き掛けなど、ユーザー開拓のためのNEDOの支援を受けてCNFの研究開発を加速させた日本製紙は、CNF実用化への手応えを得ます。2010年ごろから紙の需要が急激に落ち込み始めたのをきっかけに、CNFを、“脱製紙”を見据えた次なる事業の柱として育てるべく、矢継ぎ早にいくつもの手を打ち始めました。CNFへの期待が高まり、人的な補充がされるなどプラスの影響があったと、河崎さんは当時を振り返ります。
NEDOプロジェクト終了後、プロジェクトで得られた原料パルプや薬品などの基本処方を100L規模から数千L規模までスケールアップし、連続操業できる設備を完成させました。それが岩国工場の実証設備です。
「2013年11月には、固形換算で年産30tのCNFを作る実証機を岩国工場(山口県)に設置しました。そこでCNF量産化に向けたノウハウを蓄積し、2017年4月には、固形換算年間500tの量産ラインを石巻工場(宮城県)で稼働させました(写真5)。現状のCNF固形分濃度はまだ低いと考えており、高濃度化により生産量は年間500t以上にすることが可能と考えています」(河崎さん)
写真5 (左)新聞古紙パルプの製造建屋(4,700㎡)を有効利用した石巻工場の外観。(中央、右)2Fの量産設備で反応・洗浄・除塵・解繊処理などが行われている(写真提供:日本製紙)
その間の2015年に、日本製紙は子会社の日本製紙クレシアを通じて、CNFを使った商品を世に送り出しています。大人用紙おむつ「肌ケア アクティ」シリーズと、女性用吸収ケア専用品「ポイズ」シリーズです(写真6)。
これらの商品で、CNFがどのように使われているのでしょうか。
「TEMPO酸化法で作ったCNFは、単一のセルロースミクロフィブリルの表面に、多くのマイナスイオンを持ちます。そこに金属イオンなどを結合させることで、さまざまな機能を持たせることができます。消臭・抗菌効果がある銀イオンを結合させたCNFのシートを紙に折り込み、おむつや女性用ケア用品の消臭・抗菌効果を高めています。2013年ごろから、日本製紙クレシアと共同で商品化に向けて開発を進めてきました」(河崎さん)
写真6 CNFを用いて世界で初めて商品化に成功した大人用紙おむつ「肌ケア アクティ」(右)と、女性用吸収ケア専用品「ポイズ」(左)
FOR THE FUTURE 開発のいま、そして未来
食べられるCNFの開発
日本製紙は、石巻工場設立後も、CNFの事業を拡大する手を立て続けに打ちました。2017年6月には、富士工場(静岡県)にCNF配合強化樹脂を年産10tで製造する装置を導入。同年9月には、江津事業所(島根県)で年産30~100tのCNF製造装置を稼働させました。ただし、この2つの製造拠点で作るCNFは、磯貝教授が開発したTEMPO酸化法とは異なる方法が採用されています。
富士工場で採用されているのは、現在NEDOプロジェクトで進めている機械解繊によるリグノCNFです。
「現状、機械解繊のリグノCNFは、パルプよりも繊維がほぐれているけれど、単一のミクロフィブリルまではほぐれていないというレベルです。機械解繊の魅力は、製造コストの安さと樹脂の中にCNFを分散させやすいことにあります。自動車の車体に使うようなCNF強化樹脂を用途として想定するのであれば、今の時点では機械解繊のリグノCNFの方に分があると考えています」(河崎さん)
一方の江津事業所で採用されているのは、日本製紙が従来持っていた技術を応用し、CNF化することに成功した方式です。それを「カルボキシメチル化(CM化)CNF」と呼びます。 日本製紙がもともと持っていたのは、食品や化粧品の増粘剤として使われている「カルボキシメチルセルロース(CMC)」を作る技術です。
「CNFが単一の繊維として存在していますので、金属イオンなどを付着させてCNFに機能を持たせるには、TEMPO酸化CNFの方が優れています。また、塗料の増粘剤にもCNFを使用することができますが、これもやはり完全ナノ分散しているTEMPOの方が使い勝手のよさは高まるはずです。CM化CNFの利点は、CMCと同様に食品に利用できることです。CNF一つとっても、さまざまなラインナップを揃えているのが弊社の強みです」(河崎さん)
CNFが超えなければならない壁
次世代素材として期待が高く、応用展開も広がっているCNFですが、課題もあります。 まずはまだ価格が高いこと。そのため、従来品と同等の機能であるという程度では、CNFへの置き換えがなかなか進みません。生産量が増えれば価格も低下しますが、需要が先か供給が先かは新素材が必ず直面するジレンマと言えるでしょう。
「まずは、現状の価格でも利用可能な高付加価値の用途を多く見つけることでしょう。それによって、少しずつCNFの生産量が増え、価格が低下していくことを期待しています」(磯貝さん)
続いては素材としての信頼性です。CNFは生まれたばかりの素材です。ガラスや紙や金属やプラスチックのように、何十年・何百年と使われてきた馴染みの素材と比べると、どのような条件でどんな変化が起こるのかが未知数です。
「セルロースはバイオ系の高分子ですので、温度や湿度に敏感で、紫外線による変化を受ける可能性もあります。例えば酸素を通しにくい性質も、湿度に大きく左右されます。湿度が限りなくゼロ%に近い絶対乾燥状態では、CNFは確かに酸素を通しにくいのですが、湿度が高くなると酸素を通してしまうことが分かっています。また、CNFは熱膨張には強い性質がありますが、セルロースからなる紙が燃えやすいのと同じで、耐熱性はそれほど高くありません。数百℃で炭化や変色という変化が起こるので、高くても200℃以下、基本的には100℃を超えない環境での用途を考えるべきでしょう」(河崎さん)
もう一つは、曲げたり引っ張ったりという力に対しては強度を示す一方、衝撃に対しては弱く、局所的な力が加わると割れやすい脆さがあることです。「ガラスのようなイメージ」と河崎さんは言います。
タイヤの色が黒でなくなる日
この性質は、自動車車体への導入を目指すのであれば、非常に大きな弱点になると見られています。それをどうすれば克服できるのか。
「ゴムやプラスチックにTEMPO酸化CNFを配合し、耐衝撃性の問題を克服しようという研究もかなり進んできています」(磯貝さん)
その技術の応用例の一つとして注目されているのが、タイヤにCNFを配合することです。
「タイヤの重量の60%は、カーボンブラックという石油の精製残渣が使われています。ゴムに炭を入れると強くなる、安定性が増すことが1920年代にアメリカで偶然発見されました。それ以来、タイヤの色は黒と決まっています。カーボンブラックをCNFで置き換えられるようになれば、タイヤの色が黒である必要はなくなります。また、タイヤの摩耗による粉塵にも、カーボンブラックが含まれています。石油系微粒子ですので主にヨーロッパで問題視されつつあり、環境対策としてもCNFは有力な代替候補になっています」(磯貝さん)
「強度は鉄の5倍で重さは鉄の5分の1」と謳われるCNF。自動車車体にCNF強化樹脂を導入する研究開発も進んでいます。おむつ・食品添加物用途はすでに実用化され、今後も私たちの日常生活の中で使われていくでしょう。CNFに懸ける人々の思いは大きく広がっています。
開発者の横顔
ニーズではなくシーズから生まれた研究成果
磯貝さんは、最初からCNFの実用化を目的に研究していたわけではありません。TEMPO酸化によるセルロースの化学反応を長年にわたり調べていたら偶然に生まれた技術です。
「TEMPO酸化法CNFは、ニーズではなくシーズから生まれた研究成果です。私たちだけではどう利用価値があるのか、まったく見当もつきませんでしたが、企業の方が応用展開のさまざまなアイデアを出してくれました」
その結果、CNFは多分野で実用化に成功、もしくは実用化を目指して多くの研究が進んでいます。こうした産業応用展開の礎をつくった技術の画期性が評価され、2015年に「森林分野のノーベル賞」といわれるマルクス・ヴァーレンベリ賞を共同研究者と共に受賞しました。
東京大学大学院
農学生命科学研究科 教授
磯貝 明さん
CNFが事業の柱の一つに
河崎さんは、磯貝さんがTEMPO酸化法CNFを日本製紙に持ち込んだその時から、CNFの研究を始めた“CNF事業の産みの親”です。
「当時はCNFがここまで注目される素材になるなど夢にも思いませんでした」
2015年10月以降、CNF事業推進室、CNF研究所と研究開発本部内での独立した組織の長を務め、日本製紙の“脱製紙”を推し進めるべく、CNF事業の拡大のために連日奮闘しています。CNFを混練したCNF強化樹脂の開発を行うNEDOプロジェクト「非可食性植物由来化学品製造プロセス技術開発」(リグノCNF)も進行中です。
「開発されてからの歴史が浅く、実績の少ない“未知の素材”であるCNFを、自動車部材などに使おうとしてくれているのがありがたい」と、CNFに大きな期待が寄せられていることを実感しています。
日本製紙株式会社 研究開発本部長代理
CNF研究所所長
河崎 雅行さん
なるほど基礎知識
植物の主成分セルロースの力
植物は動物と違って細胞壁を持ちます。特に樹木の細胞壁は強固で、重力に逆らって何メートルも何十メートルも背を伸ばすことができるのは、この強固な細胞壁があればこそです。 樹木の細胞壁のほとんどは、セルロース、ヘミセルロース、リグニンの3主成分からなります。セルロースが直鎖上に連なったミクロフィブリル(CNFの実体)が幾重にも階層構造をなして植物繊維を構成し、それがさらにリグニンやヘミセルロースと複合化して繊維複合体を形成して、強固な細胞壁を実現しています。
植物細胞壁のこの構造は、よく鉄筋コンクリートにたとえられます。セルロースからなる植物繊維は引っ張られる力に対して強く、鉄筋と同じ役割を果たします。一方、重力の圧縮に耐えるコンクリートと同様の働きをするのがリグニンです。リグニンは、植物繊維や細胞壁どうしの隙間を埋めてそれらをつなぐ接着剤の役割を担っています。 また、鉄筋コンクリートには、鉄筋同士をつなぐ「帯金」と呼ばれる針金が使われています。その役割を果たしているのがヘミセルロースです。このように、人工建造物を支える鉄筋コンクリートとまったく同じ構造で、細胞壁は樹木を支えています。
こうした特長を持つ樹木は、さまざまな分野で応用されています。中でも樹木成分の過半を占めるセルロースは、私たちの身の回りで最も身近な素材と言えるかもしれません。 樹木の細胞壁の成分から、セルロースからなる植物繊維だけを抽出したもの、すなわち樹木から(正確には木材チップから)ヘミセルロースとリグニンを取り除いたものがパルプです。紙はこのパルプを元に作られます。情報端末の普及でペーパーレス化が進んでいるとはいえ、紙にまったく触れずに一日を過ごすことは難しいのではないでしょうか。
鉄筋コンクリートのイメージ図
左から木材チップ、パルプ、TEMPO酸化パルプ
NEDOの役割
「イノベーション推進事業/ナノテク・先端部材実用化研究開発」
(2005~2013年度)
(NEDO内担当部署:材料・ナノテクノロジー部)
日本の産業競争力を強化し持続的な発展を達成するためには、社会ニーズに対応する技術課題の解決に向けて、大学などの有する優れた技術シーズを活用し、技術開発成果の実用化を推進し、新規市場の創出により社会実装させることが重要です。
NEDOは、ナノテクノロジーのシーズ技術を有する川上機関(大学、材料メーカーなど)と、その実用化を担う川下機関(製品メーカーなど)が一体となった垂直連携体制を構築し、プロジェクトを推進してきました。
この垂直連携体制により、シーズ側の視点だけでなく出口を見据えた研究開発を実施する環境を整えた結果、日本製紙はセルロースナノファイバーの実用化に成功し、関連技術も続々と実用化しつつあります。
関連プロジェクト
お読みいただきありがとうございました。
ぜひともアンケートにお答えいただき、
お読みいただいた感想をお聞かせください。
いただいた感想は、
今後の連載の参考とさせていただきます。