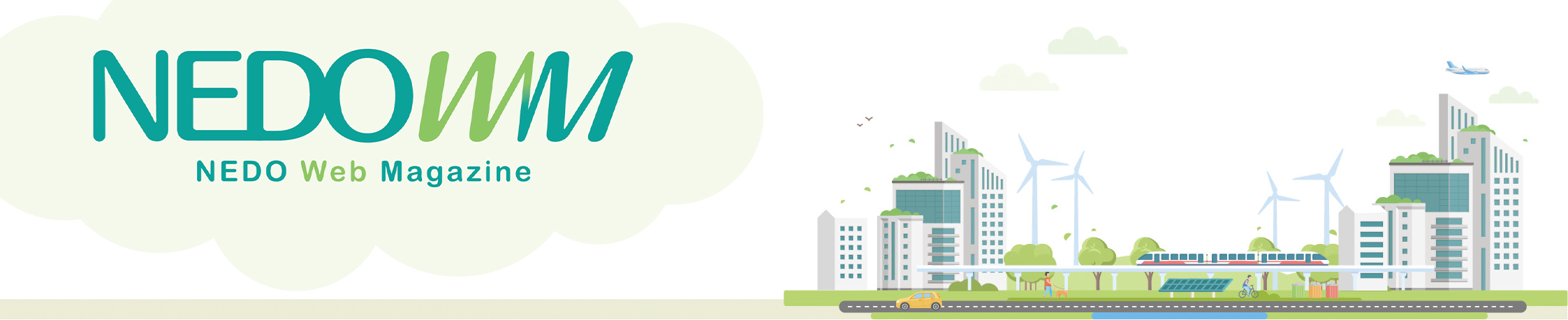
CONTENTS
INTRODUCTION
高効率なバイオエタノール生産に向けてBEGINNING
タイで見つかった「耐熱性酵母」BREAKTHROUGH
実証事業とは現場で起こる問題を解決することFOR THE FUTURE
今後、東南アジアでの普及を目指すFACE
長年めざしてきた、生物を使ったものづくりを実現
INTRODUCTION 概要
高効率なバイオエタノール生産に向けて
バイオエタノールは、植物由来の再生可能な生物資源(バイオマス)を原料に生産され、カーボンニュートラルなエネルギーとして注目されています。特に熱帯地域は生物資源が豊富であり、バイオエタノール生産に必要な原料が入手しやすいこともあいまって、東南アジアではタイに代表されるように、国家政策として燃料用バイオエタノールの増産を進めている国があります。ただし、いかに豊富な生物資源を抱えていると言っても、環境保全や食料生産とのバランスや経済合理性の観点から、どの生物資源を燃料用バイオエタノールの原料とするかが課題になっています。そこで注目されているのが、廃棄物となっている生物資源の利用です。NEDOは、タイにおいてタピオカ製造用のキャッサバの廃棄物である「キャッサバパルプ」を「耐熱性酵母」で発酵させ、燃料用バイオエタノールを製造する実証試験に成功しました。タイでこの「耐熱性酵母」を発見した山口大学に加え、磐田化学工業、サッポロビール(現・サッポロホールディングス)が参画し、産学連携でお互いの強みを発揮したことで、早期の実用化につながりました。
BIGINNING 開発への道
タイで見つかった「耐熱性酵母」
土壌・湖沼などの自然環境や、工場などの人間活動の場には、その場所の環境に適応したさまざまな微生物が生息しています。人間はその中から有用なものを発見し、利用してきました。1990年代後半、山口大学はタイのカセサート大学と研究交流を実施、熱帯地域特有の「耐熱性微生物」の探索を行っていました。
2000年代に入り、バイオエタノールが次世代エネルギー資源として注目されるようになると、山口大学はタイのウボンラチャタニ大学とチームを組み、「耐熱性微生物」のうちバイオエタノールを生産できる微生物を中心に探索するようになりました。そして、製糖工場の資材置き場から「耐熱性酵母」である「クルイベロミセス・マーキシアヌス」を発見しました(写真1)。
発見当初から関わっている、山口大学大学院創成科学研究科化学系専攻准教授の星田尚司さんは、この「耐熱性酵母」について次のように説明します。「普通、酵母と言えば、『サッカロミセス・セレビシエ』のことを指します。酒(エタノール)はこの酵母で作りますが、35℃くらいまでは普通に生きているのに、40℃になると生育が難しくなります」
「それに対して『クルイベロミセス・マーキシアヌス』は、40℃どころか50℃になっても生きていられます。これには驚かされました。加えてエタノールの生産性が高かったことから、迷わずこの耐熱性酵母を使ってバイオエタノールを作ろうと決めました」(星田さん)
星田さんは、新発見された「耐熱性酵母」の熱に対する強さは、酵母を知っている人なら誰もが驚かされると言います。そして、バイオエタノール生産に向けて、この耐熱性を持つ酵母が有利だと考えた理由を説明します。
「発酵とは、微生物の生命活動の一つです。生命活動には発熱が伴うため、試験管やフラスコで酵母を生育させ、発酵でエタノールを作らせると、培養液の温度は上昇します。普通の酵母は35℃を越えたあたりから弱り始めるので、冷却しなくてはなりません。しかし、冷却に大きなコストがかかるため、熱に強く冷やす必要のない『耐熱性酵母』があれば、バイオエタノール生産での大きなメリットになります」
写真1 山口大学で培養研究中の「耐熱性酵母」。(左)寒天培地で培養した耐熱性酵母、(中)より良い耐熱性酵母を得るための掛け合せ実験、(右)得られた酵母の発酵能力を調べるための培養実験へ
自社の発酵事業の再興へ、常識の通じない「耐熱性酵母」と格闘
2006年、山口大学の「耐熱性酵母」研究に、磐田化学工業株式会社が加わりました。同社は元々、クエン酸やイタコン酸などの有機酸を発酵生産していましたが、2000年頃から海外の安価な製品により自社工場での発酵生産量が減少していきました。
様々な発酵を行ってきた豊富な経験と設備を生かして、他社製品の受託発酵事業を続けていましたが、「いつかまた、クエン酸のような自社の発酵製品を世に送り出したいと思っていた」と同社取締役開発室長の関口喜則さんは話します。
2006年、社内に発酵の研究を行う部署を復活させようという動きが起きて、当時の研究リーダーの母校である山口大学との微生物の共同研究が始まりました。そして、磐田化学工業ではタイで新発見された「耐熱性酵母」に関する研究が、自社発酵事業の再興につながっていくのではないかと希望を託しました。
山口大学と磐田化学工業は、NEDOプロジェクトに応募して、2007~2010年度に「新エネルギー技術研究開発/バイオマスエネルギー等高効率転換技術開発(先導技術開発)/耐熱性酵母による低コスト化発酵技術の研究開発」を行うことになりました。
この先導技術開発では、山口大学が「耐熱性酵母」の菌株を作製し、それを磐田化学工業が発酵装置を使って培養して性質を評価しました(写真2)。
関口さんは、「エタノールを生産する際の最適な環境条件を知ることがプロジェクトの最大のねらいでした」と説明します。「培地組成、温度や通気量、攪拌速度のほか、培養液に植菌する酵母の量もエタノールの生産性に影響しますから、調べることは多岐に渡りました」(関口さん)
写真2 磐田化学工業での「耐熱性酵母」の培養試験。(左)シャーレに菌を蒔き生育状況を見て特徴のある株を選び出し、(中)試験管にコロニーを単離して培養後、(右)フラスコによる液体培養試験で特性を評価する
「耐熱性酵母」の特徴が徐々に明らかにされると、星田さんと関口さんは、エタノールを生産する普通の酵母ではごく当たり前の常識がこの「耐熱性酵母」には通じないことを知り、驚かされました。
そもそもエタノールは、酵母が酸素のない環境中でエネルギーを得る時に、副産物として作られる物質です。そのため普通の酵母では、通気量を減らせば減らすほどエタノールの生産量が増えます。
ところが、新しく発見された「耐熱性酵母」は通気を止めてしまうと、逆に元気がなくなってしまったのです。その理由は現在も解明中ですが、「耐熱性酵母」のこの特徴が明らかになったことで、生育を妨げることなくエタノール生産量が最適になる通気量が、新たな検討項目として加わりました。
大手ビール会社の参画が、実用化に向けてプロジェクトを加速
星田さんが、「磐田化学工業との共同研究は、『耐熱性酵母』の将来を考えると、発酵の専門家と研究を進めるのがいいだろうという気持ちで始めたことでした。実用化のためには大容量発酵を行わなければならないことはわかっていましたが、当時は、まだ先のことだと思っていました」と話すように、先導技術開発は当初、「耐熱性酵母」の特徴を調べるなど基礎研究を行うことが目的でした。
しかし、プロジェクトが始まって2年、2009年に新たなメンバーがプロジェクトに加わると、実用化に向けた研究開発が一気に加速しました。その新たなメンバーとは、ビール製造大手のサッポロビール株式会社でした。
サッポロビールではビール製造などの発酵技術や経験を生かして、2000年頃からバイオエタノールの研究を独自に行っていました。また、サッポロビールでは、キャッサバからタピオカを絞った後の残渣である「キャッサバパルプ」が東南アジア、特にタイで大量に廃棄されていることに着目していました。
キャッサバパルプを原料にしたバイオエタノール生産に、山口大学と磐田化学工業が研究していた「耐熱性酵母」が向くのではと考えたのは、当時のサッポロビール株式会社価値創造フロンティア研究所研究主幹の三谷優さんでした。
三谷さんは当時を振り返って、「山口大学と磐田化学工業が『耐熱性酵母』を研究しており、研究室レベルでの検証はほぼ終わって、なかなかいい結果が出ていることは知っていました。今後、実用化を目指すなら、工場技術が必要になるだろうと思い、『私たちならビール製造の経験もありますから、お役に立てます』と声をかけさせてもらいました」と話します。
写真3 キャッサバパルプ(左)、キャッサバパルプから製造したバイオエタノール(右)
サッポロビールの参画により、「耐熱性酵母」によるバイオエタノール製造の原料は、それまでの廃糖蜜からキャッサバパルプに変更されました(写真3)。また、ビールなどの大量生産の技術や経験を踏まえた、実用化のためのロードマップの作成など、明確なゴールを設定した研究開発へとプロジェクトが変容していきました。
そうした実用化に向けた研究開発へのシフトは、NEDOからも積極的に勧められたと関口さんは言います。
「基礎から実用化に向けてNEDOプロジェクトの進め方には何段階かのステップがありますが、『先導技術開発が終わったら、一気に大規模生産を目指して実証に入ってもいいのではないか』と提案されました」(関口さん)
そして先導技術開発が終わるとすぐに、実証事業に向けて実行可能性を調査するフィジビリティスタディ(FS調査)が始まりました。
BREAKTHROUGH プロジェクトの突破口
実証事業とは現場で起こる問題を解決すること
山口大学、磐田化学工業そしてサッポロビールが進めてきた、「耐熱性酵母」による燃料用バイオエタノール生産技術が、タイでの実証事業の成功まで漕ぎ着けられたのには、どのようなブレークスルーがあったのでしょうか。
2010年度に行われた「国際エネルギー消費効率化等技術普及協力事業/技術実証事業FS/キャッサバパルプからのバイオエタノール製造技術実証事業(タイ)」と、続く2011~2015年度に行われた「国際エネルギー消費効率化等技術・システム実証事業/キャッサバパルプからのバイオエタノール製造技術実証事業(タイ)」では、山口大学と磐田化学工業が2007年度からのプロジェクトで明らかにした「耐熱性酵母」の特性を基に、サッポロビールがバイオエタノール製造のスケールアップを図りました。
三谷さんは、「この辺りのノウハウは、ビール会社で長年エンジニアをやっていると身についているものです。しかし、実証事業では、これまでの経験に裏付けられたノウハウを活かすばかりでなく、装置や実証プラントで起こるこれまで経験したことのない問題にも対応しなければなりません。現場で試験して初めて分かる事実というものが必ずあって、それを次の装置開発やプロセス開発につなげていかなくてはなりません」と話します。
2010年度に行われたFS調査から数えると約6年に及んだ実証事業は、タイのバンコク空港から東へ約250km離れたサケーオ県で行われました。ここには、タイの大手デンプン加工会社EBPがあります。
写真4 デンプン工場から排出されるキャッサバパルプは屋外で貯蔵している(左)、キャッサバパルプの状態(右)(写真提供:サッポロホールディングス)
キャッサバからデンプン成分のタピオカを絞った後のさまざまなキャッサバパルプを大量に使用できるように、実証プラントをデンプン工場に隣接させて建設し、さまざまな条件で、バイオエタノールの製造を実験、評価していきました(写真4、5)。
現地で実証試験に携わった、現在サッポロホールディングスグループR&D本部グループ研究戦略推進部主任研究員の阿部透さんは、「エタノール発酵は放っておいても進みます。しかしバイオエタノールを燃料として使うには、効率よく生産して生産コストを抑えなくてはなりません。ですから私たちがやるのは、酵母が良い状態で発酵し生産効率があがるように条件を整えてあげることなのです」と説明します。
また、実証プラントの設計を担当した、現在同社グループR&D本部グループ研究戦略推進部シニアマネージャーの渡里彰さんは、「実験室でも温度条件の検討はできます。しかし、実際の工場では100t規模のタンクを扱います。例えば、その温度は、実験室の設備のように急激に変化させることはできません。この100tのタンクを思ったように制御するのが、産業技術です」と実験室と工場の違いを説明します。
大規模にしたことで、バイオエタノールの生産性に影響してくることは実に多く、最適の条件でバイオエタノール生産を行うには、原料をタンクに入れたり、タンクから出したりする時間さえも考慮しなくてはなりません。考えられるすべての要因について検討して、最適なタンクサイズや、バイオエタノールの製造工程を決めていきました。
写真5 タイの実証プラント。(左)工場外観、(右)採集前の原料 (写真提供:サッポロホールディングス)
キャッサバパルプからのバイオエタノール製造を可能にした三つの技術
渡里さんは、「同じエタノールでも燃料用エタノール製造の設備は、ビール製造の設備とはまったく違います。特に今回は、原料にキャッサバパルプを採用したことが、実証プラントの設計に大きく関わってきました」と設計者としての苦労の一端を覗かせます。
キャッサバパルプがこれまでバイオエタノールの原料として利用できなかったのは、繊維分を多く含んでおり、エタノール発酵させるのが難しかったからです。では、どのような技術によってキャッサバパルプは原料として使えるようになったのでしょうか。
糖からエタノールを作る化学反応はとてもシンプルですが、バイオマス原料から燃料用バイオエタノールを得るには、原料の前処理からエタノールの蒸留・脱水まで多くの工程を経なければなりません(図1、「なるほど基礎知識」参照)。阿部さんによると、たくさんの工程のうち「ドライミル」と「高温並行複発酵」「連続蒸留」の三つが最大の技術的なトピックだったと言います。
図1 バイオエタノールの製造工程 ①粉砕原料に加水しスラリー状とする、②スラリーを蒸気で連続加熱し、酵素反応を受けやすくする、③酵母を添加しアルコール発酵により濃度8%の発酵液を得る、④アルコール濃度を8%→99.5%に蒸留・脱水する (資料提供:サッポロホールディングス)
エタノールは酵母により糖から発酵作用を経て作られます。そこでキャッサバパルプに含まれるデンプン成分を糖に分解しなければなりません。まずキャッサバパルプを粉砕して水を加え、泥のようなスラリー状にします(写真6)。
写真6 粉砕したキャッサバパルプ(左)、キャッサバパルプに水を加えてスラリー状態にしたもの(右)
ここに、デンプンを糖に分解する酵素であるアミラーゼを添加します。次に配管を通しながら熱い水蒸気を吹きかけると、デンプンの分子構造が崩れアルファ化します。この状態とすることで初めて種々の酵素反応を受けることが可能となります。
この後、アミラーゼによる作用でデンプンが糖にまで分解されます。その後、繊維成分を分解する酵素であるセルラーゼを添加し、原料中のデンプン分解を進めます。通常このような操作は、大型のタンク内でバッチ処理で行われますが、大型のタンクを使用せず配管内で連続的に熱い水蒸気を吹き付けることでアルファ化を進める工程が、一つ目の技術的トピックであるドライミルです。ウェットミルに対して水分量を抑えることができるため、原料を薄めることなく発酵工程に入ることができます。
二つ目の技術的トピックである高温並行複発酵は、「耐熱性酵母」を使うことで実現した技術です。糖化は通常60℃を超えた温度領域に至適温度があります。一方、酵母の発酵至適温度はこれに比べ随分と低く、従来の酵母では35℃前後です。
「耐熱性酵母」を使用することで、従来の酵母よりも5℃以上高い温度で発酵を行うことができます。発酵期間中に糖化も同時に行う並行複発酵では、この発酵温度が糖化の至適温度により近づくことになり、効率の良いプロセス構築が可能となります。
三つ目の技術的トピックである連続蒸留では、発酵スラリー中に残存する繊維成分、夾雑物(きょうざつぶつ)により、蒸留装置内が詰まってしまうことが懸念されました。
パイロット以前の小スケールで確認済みとはいえ、スケールアップした際の挙動を十分に確認する必要がありました。実証プラントでは発酵液が初めに導入されるモロミ塔内を適宜確認できるように点検口を設け、汚れの付着状態を確認しました(写真7)。これにより汚れのレベルや、必要な洗浄頻度の目星をつけることができ、商用運転の目処をつけることができました。
写真7 (左)連続加熱後のキャッサバパルプスラリー、(右)点検口から確認された蒸留塔内部の汚れ状況 (写真提供:サッポロホールディングス)
原料のばらつきにも対応する
実証事業では、キャッサバパルプの品質によって生じる問題も明らかになりました。食べ物であるビールの原料は品質がいいものが選ばれますが、これまで廃棄されていたキャッサバパルプは、繊維成分や夾雑物が多く、時には腐りかけていることもあります。
「キャッサバパルプを原料にしたことで、終始、発酵液の粘度の高さに困らされることになりました」と三谷さん。
原料は普通のプロペラでは混ざらないほど粘度が高いので(写真8)、実証プラントには、原料の粘度を下げるための工夫が多く見られます。また、腐りかけた原料を使うと、それが原因で発酵液が酸性になり、酵素の活性が著しく低下することがありました。
写真8 スラリー状態でも高い粘度を持つキャッサバパルプ。発酵のため加温するとさらに粘度を増すため取り扱いが難しい
解決しなければならない問題はいろいろ発生しましたが、サッポロビールのメンバーをもっとも驚かせたのは、キャッサバパルプのデンプン含有量の変動でした。「実証事業期間中に、キャッサバ栽培を2シーズン経験しましたが、悪天候の影響で、品質が悪くデンプン含有量が低いシーズンがあり、それまでのバイオエタノール製造のデータが全く参考になりませんでした」と渡里さん。
阿部さんも、「キャッサバパルプはデンプン含有量が65%以上で良質のこともあれば、40%ほどしかないときもあったのです。たいへんな経験をしましたが、今にして思うと、キャッサバの出来がこれほど変わることを知り、それがバイオエタノール生産に大きく影響することがわかったのですから、良かったと思っています」と話します。
キャッサバの品質低下によって起こる問題は、原料中のデンプン量が少ないことで起こる発酵液の最終エタノール濃度の低下です。発酵液のエタノール濃度が目標値の8%に達していれば、蒸留・脱水工程で92%の水分を蒸発・分離させるとバイオエタノールを得られますが、発酵液のエタノール濃度が低下すると、それだけ多くの水分を蒸発・分離させなくてはならず、その分コストがかかり商業的に成り立たなくなります。
この問題を解決するためには、キャッサバパルプの品質によらず、ある範囲内でバイオエタノールを製造できる技術が必要でした。キャッサバパルプに加える水の量を抑えることで、発酵液の最終エタノール濃度が下がらない方法を検討し、問題を解決しました。
タイではすでに多くのバイオエタノール生産工場が稼働していますが、中には当初に予定していた生産量を達成できていない施設もあります。原料の状態や、タンク・配管内の汚れが原因で生産効率は容易に変動することもあり、工場設備を最適な状態で稼働し続けることは簡単ではありません。
そのため、実証事業ではタンクの汚れを常に確認し、ノウハウの蓄積を行いました。キャッサバパルプスラリーは装置内への付着が当初の想定よりも弱く、軽い水通しなどで容易に洗浄可能であることが分かりましたが、一度洗浄漏れがあると急速に汚れの蓄積ができることも分かりました。
実証プラントにおける工夫は大きいものから小さいものまで実に多岐に渡りました。「2011年から2015年の実証プラントの試験期間中は、やらなければならないことが多くて本当に忙しかった」と皆が口を揃えます。
実用化を牽引する体制づくり
サッポロビールは、タイに実証プラントを建設し、バイオエタノール製造試験と分析を行いました。事業がスムーズに進められたのは、しっかりした体制が築かれ、役割分担が明確になっていたからでした。
プロジェクトは、NEDOとタイ科学技術省国家イノベーション庁(NIA)が基本協定書を結んで進められました。また、タイ側からは前出のようにデンプン加工会社であるEBP社の子会社のEBP Ethanol社が参加し、実証事業をサポートしました(図2)。
図2 日本とタイの協力体制図
一方で、プロジェクトが急激に展開したことに、磐田化学工業は不安を感じていました。「世の中のためになる研究だけれど、静岡の中小企業がやるようなプロジェクトなのか。元々、自社の工場でできることを探るために始めたプロジェクトじゃなかったのか、などと社内でも事業の継続に反対する声が聞かれました」と関口さん。
それでも、ここまで関わってきた「耐熱性酵母」のことを考えると、続けたい気持ちが大きく、当時のNEDOの担当者に相談に行ったと言います。この時の話し合いで、「菌株の管理運営をする」とプロジェクトへの関わり方が明確になり、磐田化学工業はプロジェクトに関わり続けることになりました。
そして結果的には「サッポロビールという大企業との共同研究という貴重な経験をして、会社としても個人としてもたいへん得ることが多く、勉強になりました」と関口さんは振り返ります。
FOR THE FUTURE 開発のいま、そして未来
今後、東南アジアでの普及を目指す
タイではすでに廃糖蜜からの燃料用バイオエタノールが製造され、流通しています。新しい「耐熱性酵母」が優れた生産性を持っているとしても、今後の普及に向けて、工場規模での条件検討や、設備の変更が必要です。
しかし、これまで使われていなかったキャッサバパルプを原料に選んだことは、この「耐熱性酵母」を使ったバイオエタノール生産の実用化を後押ししたと言えるでしょう。キャッサバパルプの「繊維成分が多いために原料にならない」という問題を解決したのは、「耐熱性酵母」でした。繊維成分を分解させる酵素と同じ温度条件でも発酵できるという特徴が、効率的なバイオエタノール生産につながりました。
実証試験で確立した技術をサッポロビールから引き継いだサッポロホールディングスは、今後、東南アジアを中心に「耐熱性酵母」とキャッサバパルプの組み合わせでバイオエタノールを生産する商業用プラントの普及を目指しています。
「耐熱性酵母」をもっと使ってもらうために
実証事業で、「耐熱性酵母」の菌株の管理運営を任された磐田化学工業の関口さんたちは、この「耐熱性酵母」の優れた性質をもっと多くの工場で使ってもらえるように、タイで菌株を提供するビジネスを立ち上げようとしています(写真9)。
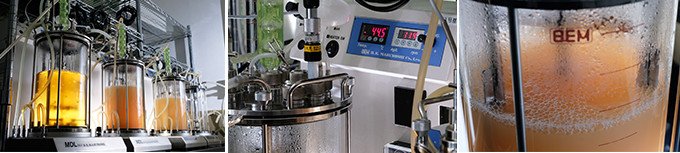
写真9 磐田化学工業では「耐熱性酵母」の大量供給に向けて培養評価の研究が続く。(左)生育環境を変えての評価(培養温度と撹拌速度がそれぞれ異なる)、(中)40℃を超える発酵温度、(右)培養が進んで濁る容器、「耐熱性酵母」は培養速度が速いのが特色
また、この酵母の耐熱性のメカニズムを明らかにしたいと話す星田さんは、もっと耐熱性も、エタノール生産性も高い酵母があるのではないかと、酵母同士を掛け合わせて、より良い「耐熱性酵母」を得たいと考えています。
これからも、このバイオエタノール製造技術は進化を続けていきます。タイで発見された「耐熱性酵母」が、タイを始めとした東南アジアでのバイオエタノール製造に変革をもたらそうとしています。
開発者の横顔
長年めざしてきた、生物を使ったものづくりを実現
星田さんが、この開発に取り組んだ背景には、学生時代に感じた「ものづくりをするなら生物を使わなくてはダメだ」という思いがありました。
「何かエネルギーに関わる研究をしたいと思っていた学生時代、植物から光合成に関わるタンパク質を取り出して研究していました。取り出したタンパク質が壊れやすかったことから、生物というシステムが優れていることに気付き、生かしたまま利用しようと思うようになりました」
「生きているという状態は複雑ですが、生きていれば継続して使用し続けられます。それは、何かを製造しようとするとき有利に働くと思います」
その言葉の通り、「耐熱性酵母」を使ったバイオエネルギー製造の実証プラントが実現しました。
山口大学大学院 創成科学研究科 化学系専攻
准教授
星田 尚司 さん
再び自社の研究開発をスタート
ヒスタミンは魚介類が腐敗すると生じる、食中毒原因物質です。関口さんは学生時代に、このヒスタミンを酸化する酵素を使い、ヒスタミンの検出センサーを作りました。
この経験から関口さんは、「人の役に立つ研究をしていきたいと思うようになりました」と言います。
磐田化学工業に入社した当初は酵母の研究をしていましたが、発酵事業がクエン酸などの自社発酵製品から受託発酵製造にシフトしていく中で、研究開発からまったく離れた時期もありました。
「しかし、この時期の経験が、現在の研究開発をより多角的に見られるようしてくれました」と関口さんは言います。
「NEDOプロジェクトに携わり成果を挙げられたことは、今後、自社の研究開発を立て直していこうと考えていた会社にとって大きな経験になりました。新しいものを研究開発していくことに自信を得て、今はメタン発酵による工場排水の処理を事業にしており、性能を上げるための改良研究を進めています」
磐田化学工業株式会社 取締役
開発室長 兼 人材開発グループリーダー
関口 喜則 さん
自分たちの持つ技術で社会に貢献したい
三谷さんは、NEDOプロジェクトで実証事業を実施していた頃は、サッポロホールディングスの前身であるサッポロビールの価値創造フロンティア研究所の研究主幹で、NEDOプロジェクトのリーダーを務めていました。
生物化学工学を専門とする三谷さんは、サッポロビールに長年勤めてきましたが、ビール製造に配属された経歴はなく、研究・開発部門に携わり続けてきました。
「2002年に何かオリジナリティのある研究開発をしたいと考え、NEDOプロジェクトなどで環境技術や新エネルギー技術の研究を始めました」
この頃から三谷さんは、NEDOプロジェクトのサッポロビールでの窓口を務めてきました。
今回のプロジェクトについて、「技術が開発されて嬉しいと思っています。私たちはほかにも社会に貢献できる技術を持っているので、もっと貢献していきたいという気持ちになります」といつも先を見据えています。
有限会社クレオ・サイエンス
代表取締役
三谷 優 さん
サッポロビール株式会社 価値創造フロンティア研究所
研究主幹(NEDOプロジェクト参画当時)
バイオエタノール製造設備の設計は、自分にとっての挑戦
設備設計を担当している渡里さんは、工場の仕事は基本的に“維持する”ことだと言います。つまり工場は壊れることなく動き続け、高品質の製品を作り続けなければなりません。
しかし、バイオエタノール製造設備の開発に関わるようになり、苦労もしましたが、世界が広がったと言います。
「海外にも行きましたし、バイオエタノール製造設備を設計するのにいろいろ勉強もしました。実際に設備を設計する際には、1回1回の原料の違いや、立地の違いを考慮に入れなくてはならないことが分かり、それも面白かったのです」
今後の商業用プラントの普及についても、「プラントが動いたときの達成感は大きいでしょうね。もう会社でやり残したことはないと思えるのではないかと思います」と話します。
サッポロホールディングス株式会社
グループR&D本部 グループ研究戦略推進部
シニアマネージャー
渡里 彰 さん
発酵の専門家としての経験が買われ、プロジェクトに参加
入社以来、仙台工場、北海道工場、大阪工場と様々な場所で、阿部さんはビール醸造技術者としての経験を積みました。
サッポロビールが2002年に、ビール製造で培った技術を生かして、環境技術や新エネルギー技術に参入したいと考えたときに、経験豊富なメンバーとして阿部さんに声がかかりました。
大きな製造工場が多いサッポロビールの中で、小さな製造プロセスを動かした経験を持つなど、その経験値の高さが認められたのです。
阿部さん自身は、「会社の中で誰も手がけたことのないことなら、やってみたいという気持ちになりました」と前向きに受けたといいます。バイオエタノール製造に関わり、経験値はますます上がったとのことです。
サッポロホールディングス株式会社
グループR&D本部 グループ研究戦略推進部
主任研究員
阿部 透 さん
なるほど基礎知識
発酵によるエタノール生産
エタノール発酵は、高校の生物で習う“代謝プロセス”の一つです。人間は酸素呼吸によって糖を分解し、水と二酸化炭素ができる過程でエネルギーを得ていますが、生物によってはエタノール発酵で糖を分解し、エタノールと二酸化炭素ができる過程で、エネルギーを得ているものがあります。
エタノール発酵を行う代表的な生物は、酵母です。酵母は通常、酸素呼吸を行っていますが、酸素が不足すると、エタノール発酵に切り替えます。そのため前出のように、一般的な酵母では通気量を減らした方が、エタノール生産量は上がるのです。
しかし、「耐熱性酵母」には、酸素をゼロにすると生育が非常に悪いという特徴があることがわかり、山口大学の星田さんはその生物学的メカニズムを現在も解明中です。
エタノール発酵の化学式は、C6H12O6→2C2H5OH+2CO2で、化学式を見ると、糖からエタノールと二酸化炭素ができる、シンプルな反応ですが、製造には何段階もの工程を経なければなりません。
まず、原料となるキャッサバパルプの塊は、このままでは酵母による発酵は進みません。そこでまず、細かく粉砕して水を加え泥のようなスラリー状にします。ここにあらかじめ、デンプンを糖に分解する酵素のアミラーゼを加えます。
これを配管に通しながら、熱い蒸気を吹きかけて蒸煮(じょうしゃ)を行います。これで原料のキャッサバパルプは滅菌されると同時に、デンプン分子の構造が崩れアルファ化が起こります。アルファ化とは、デンプンに水を加えて加熱することによって、デンプンが糊状に変化する現象です(例:炊いたお米など)。デンプンがアルファ化することで、アミラーゼで糖に分解されるようになります(糖化)。さらに、繊維成分を分解する酵素であるセルラーゼを添加し、原料中のデンプン分解を進めます。
ここに「耐熱性酵母」を加え、キャッサバパルプのデンプンが分解されてできた糖を発酵させて、エタノールを生産します。発酵液のエタノール濃度が約8%に達したら、蒸留で水分を飛ばして、燃料用エタノールを得ます。
NEDOの役割
「新エネルギー技術研究開発/バイオマスエネルギー等高効率転換技術開発」
(2004~2012年度)
(NEDO内担当部署:新エネルギー部)
「国際エネルギー消費効率化等技術・システム実証事業」
(1993年度~、2017年度より「エネルギー消費の効率化等に資する我が国技術の国際実証事業」)
(NEDO内担当部署:国際部)
バイオマスエネルギーは、カーボンニュートラルという特性を持っていることから、地球温暖化対策の一手段として重要です。NEDOは、そのような特性を持つバイオマスエネルギーのさらなる利用促進・普及に向けた事業を実施してきました。キャッサバパルプからのバイオエタノール製造技術の実用化にあたっては、国内での基礎研究からタイでの国際実証に至るまで、2つの事業で連続的に支援してきました。
国内での基礎研究を行った「新エネルギー技術研究開発/バイオマスエネルギー等高効率転換技術開発」事業では、バイオマスエネルギーが化石燃料と同程度のコスト競争力を持てるようにするための研究開発を推進しました。
また、「国際エネルギー消費効率化等技術・システム実証事業」では、日本が強みを有するエネルギー技術・システムに関する実証事業を、相手国政府機関との協力の下で実施し、日本企業の国際競争力の強化や地球規模のエネルギー環境問題の解決に貢献することを目指します。
関連プロジェクト
お読みいただきありがとうございました。
ぜひともアンケートにお答えいただき、
お読みいただいた感想をお聞かせください。
いただいた感想は、
今後の連載の参考とさせていただきます。