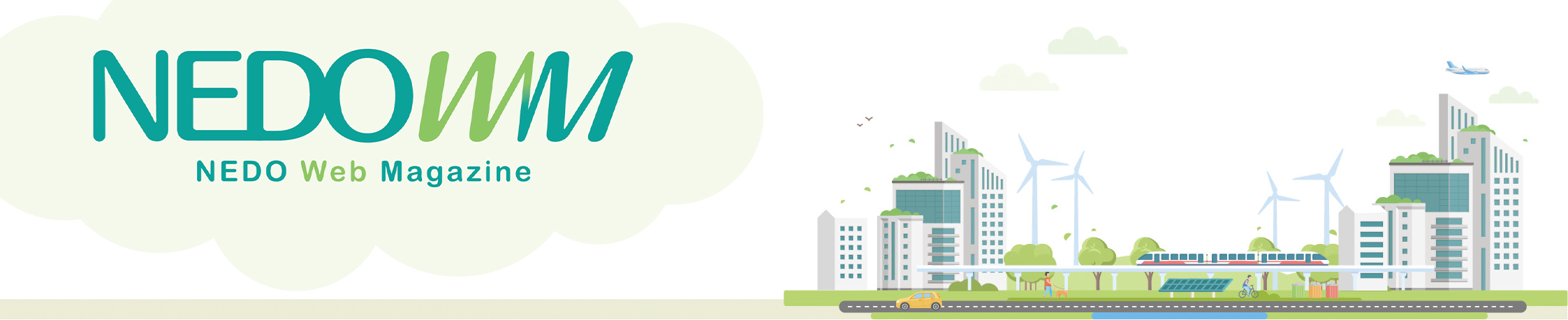
CONTENTS
INTRODUCTION
毎年、東京ドーム10個分の廃棄物を抑制BEGINNING
石炭に代わる高性能な燃料として注目される新燃料の「RPF」
BREAKTHROUGH
脱塩処理技術の確立に挑むFOR THE FUTURE
現在は原料となる廃棄物を選択して製品の発熱量や品質をコントロール
FACE
RPFを通して地球環境と社会に貢献INTRODUCTION 概要
毎年、東京ドーム10個分の廃棄物を抑制
製紙や製鉄、セメントなどの生産活動には大型の燃焼施設が欠かせません。そこでは日々大量の化石燃料が消費されています。しかし、1970年代の石油ショックによる資源不足、現在では地球温暖化防止や市場価格の不安定化により、化石燃料に代わる新しい燃料の登場が、長らく期待されてきました。そうした中、注目を集めいている新エネルギーに、「RPF(Refuse Paper and Plastic Fuel)※1」と呼ばれる燃料があります。
RPFは、古紙のうちマテリアルリサイクルが困難なプラスチック類がコートされたラミネート紙や、自然界に放置しても分解しない廃プラスチックなどを原料にした固形燃料です。同じ発熱量で換算した場合、石炭と比べてCO2の排出量が2/3、価格も割安など、多くの長所があります。そのため現在、RPFを製造、販売する企業は200社を超え、工業生産用の化石代替燃料として定着しつつあります。2010年1月には工業製品としてJIS規格化も行われました。
このRPFを考案したのが現在、「一般社団法人日本RPF工業会」会長を務める、株式会社関商店代表取締役社長の関勝四郎さんです。関さんは、家業であった資源回収業を継承、経営しながら、廃棄物の最終処分量の大幅削減と化石代替燃料の必要性を痛感し、それらを一度に解決する、リサイクル燃料の開発と普及に打ち込んできました。
そうした考えに共鳴し、川崎重工業株式会社の破砕機事業部※2では、関さんとともにRPFの実用化に二人三脚で取り組んできました。
1998~2002年度には、同事業部が、NEDO「即効的・革新的エネルギー環境技術研究開発/可燃ごみ再資源燃料化技術開発」に参画し、実証プラントを川崎重工業八千代工場内に設置して知見を集め、装置の改良を図り、RPF普及の礎をつくりました。2012年時にRPFは、年間生産量110万t、年間売上高230億円のエネルギー市場を形成するまで成長、拡大しています。
※1 2010年1月制定の「JIS」英語表記では、「Refuse derived paper and plastics densified fuel」
※2 プロジェクト後、川崎重工業から分社化、神戸製鋼所破砕機部門と統合した株式会社アーステクニカが事業を継承中(2014年3月現在)
BIGINNING 開発への道
石炭に代わる高性能な燃料として注目される新燃料の「RPF」
エネルギー資源に乏しいわが国では、化石燃料のほぼ100%を輸入に頼っています。2度の石油ショックを経験し、電力などの燃料の多様化は進みましたが、製紙業や鉄鋼業など大量の熱が必要な生産現場では血のにじみ出るような省エネルギー化に取り組みつつも、化石燃料の輸入価格の変動は、長年にわたる大きな課題です。さらに、1990年代以降、地球温暖化防止の観点からも化石燃料に替わる新しい燃料が強く求められるようになりました。
そうした中、1992年に石炭やコークスの代替燃料として開発された、リサイクル燃料「RPF」が、製紙会社を中心に注目を集め、消費量を伸ばしています。製紙業に欠かせないボイラー用燃料として、従来の石炭と代わらない熱量を維持しながら、CO2の排出量は2/3、価格も割安、さらにほぼ燃焼しきってしまうため灰の発生も少ないなど、燃料としてすぐれた特性があります。
RPFとは、紙の材料としてリサイクルが困難な古紙と廃プラスチックを主な原料とした固形燃料です。同じ発熱量で換算した場合、石炭と比べて価格も割安で国際相場に左右されることもないため、石炭をRPFに置きかえることで、生産コストの低減と安定化を図ることができます。さらに、原料が本来、廃棄物として処分されるはずだったことを考えると、焼却処理によるCO2排出抑止や最終処分量の大幅減量化など、環境に対する効果は、はかり知れないものがあります。
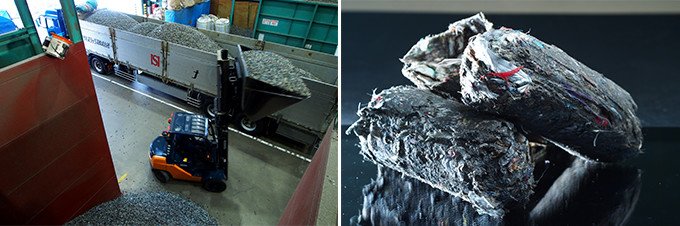
茨城県古河市の関商店茨城工場からトラックに積み込まれ全国へと出荷されるRPF(左)、新型リサイクル固形燃料RPF(右)
新燃料「RPF」のきっかけは、ラミネート加工紙の普及から
このRPFを考案した、廃棄物処理・リサイクル企業の株式会社関商店(本社:埼玉県久喜市)代表取締役社長の関勝四郎さんは、その背景を次のように語ります。
「私がRPFを最初に思いついたのは1986年のことでした。ちょうど紙をプラスチックでコーティングしたラミネート加工紙が大量に出回り始めていた時期です。ラミネート加工紙は、強度が高く、防水性がある上、装飾性も高いので、爆発的にヒットしました」
「しかしその一方で、印刷工場では印刷ミスや断裁で端切れとして生じた、製品にならないラミネート加工紙が大量発生していたのです。ラミネート加工紙は、紙の表面に接着されたプラスチックを剥がすのが容易でありません。そのため、ほかの紙と違って、紙へリサイクルするのが難しく、廃棄するしか方法がありませんでした」
「しかも、焼却処分には有毒物質の発生を抑えるため、高温での燃焼が必要でコストがかかることから、その多くが何の中間処理もしないまま埋め立て処分されていました。そうした状況を見て、実にもったいない、これをどうにか再利用できないかと考えたのです」
加えて当時、日本では、好景気もあり古紙の発生量が増大し、リサイクルの許容量を超えてしまい、大量に余っていました。埋め立て処分場もひっ迫し、古紙の処分は、大きな社会問題となっていました(図1、2)。
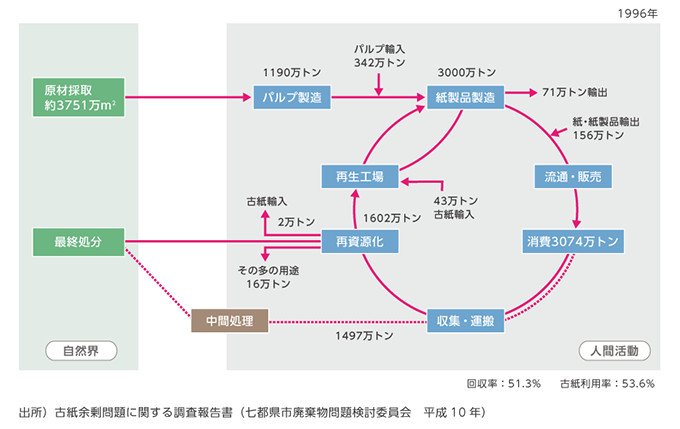
図1 プロジェクト開始当時の古紙再生フロー
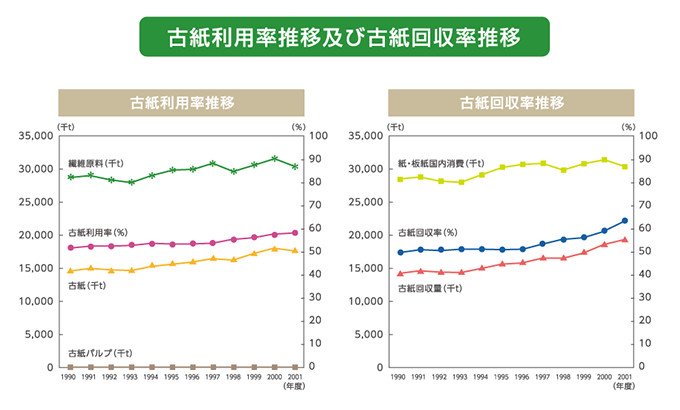
図2 古紙利用率※と古紙回収率※の推移
(※)古紙利用率=古紙消費量/製紙原料合計、古紙回収率=(古紙入荷 古紙輸入 古紙輸出)/(紙・板紙払出+紙・板紙輸入紙・板紙輸出)
結論は燃料としての再利用が持続可能な最善策
シンプルな製造工程で経済性と環境負荷低減を両立
ラミネート加工紙の再利用方法について様々な検討をした関さんでしたが、最終的な結論は、「固形燃料として使う」というものでした。ラミネート加工紙を、高品質な燃料に成形して再利用する方法が、無理に材料としてリサイクルするより、結果的に、環境負荷も低く、経済合理性もあり、持続可能な方法だったからでした。
RPFの製造法の特色の一つは、環境負荷の元となる、余分なエネルギーや化学的な添加剤などを使わずに、なるべくシンプルにすると言うことでした。廃棄処分されるラミネート加工紙を破砕機で細かく切断し、それを成形機にかけて円筒形の固形燃料を製造します(図3)。

図3 RPFの生産フロー図
ばらばらの紙片が固形燃料になる理由は、紙をコーティングしているプラスチックが、成形機内で、摩擦熱や圧縮熱によって溶け始めるためです。溶け始めたプラスチックが紙片と紙片を包み込む接着剤の役割を果たし、新たに糊や薬品などを加えなくとも、固形燃料ができあがる仕組みです。
関さんは、このRPFの製造システムを思いついたのは、視察でドイツを訪れた際に目にした『干肉から鉛筆状のドッグフードを製造する装置』に着想を得ました。そして、ラミネート加工紙を原料とするRPF製造プラントが1990年に完成することになります。
それと同時に、当時繊維染色業界の大手企業の足利工場への納入契約が成立、翌1991年に関商店では群馬県館林市に新工場を建設、2000年には埼玉工場を茨城工場に集約・増強し、本格的なRPF供給体制を整えました。
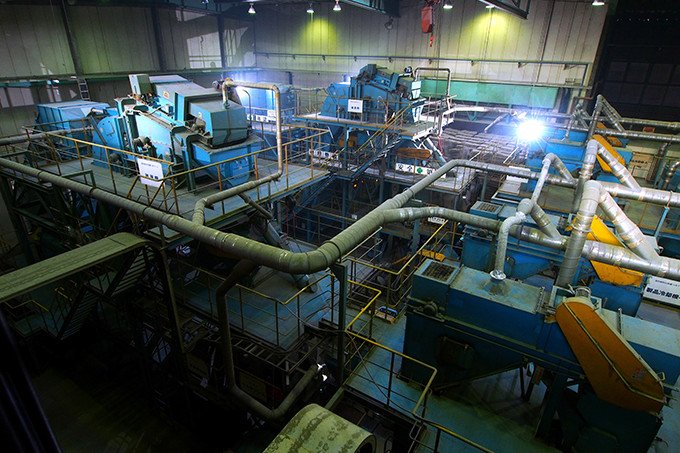
RPFの生産ライン。写真は、NEDOプロジェクトで改良された、茨城県古河市の関商店茨城工場で現在稼働中の設備
一般廃棄物もRPFにできれば処分場問題も解決できるはず、新たな挑戦を開始
これを機に関商店はRPFの生産を軌道に乗せ、石炭に替わる固形燃料として、古紙回収で縁の深い製紙会社を中心に、関心を集めるようになってきました。その一方で、関さんは、原料を廃棄処分用のラミネート加工紙に限ってしまっては、RPFの生産量に限界があると感じていました。そこで、生ゴミを除く一般の可燃廃棄物を使ってRPFを製造できないかと考え始めました。
しかしそのためには、ラミネート紙の固形燃料化とは比べものにならないほど、様々な研究開発課題がありました。自社だけで取り組むには困難なため、RPF製造プラントに関心を寄せていた川崎重工業株式会社破砕事業部(現・株式会社アーステクニカ)に共同開発の声をかけました。
川崎重工業破砕事業部では、関商店からのこの誘いにすぐに乗ることにしました。そして、RPF製造プラント実用化のため、1998年より、NEDO「即効的・革新的エネルギー環境技術研究開発/可燃ごみ再資源燃料化技術開発」に参画し、5カ年計画で、一般可燃廃棄物を原料としたRPF製造プラントの実用化に取り組むことになりました。
ポリ塩化ビニル(PVC)の選別が最大の課題
RPFの製造工程は、大きく原料の破砕と成形に分けられます。しかしながら、従来のような原料がラミネート加工紙だけの場合とは違って、一般の可燃廃棄物ゴミを対象にすると、破砕機の見直しも不可欠でした。
さらに、関商店と川崎重工業にとって最も大きな課題はポリ塩化ビニル(PVC)の脱塩素処理方法の開発でした。ラミネート加工紙に使用するプラスチックは主にポリエチレンですが、一般ゴミとして収集されるプラスチックには、ポリスチレンやポリプロピレン、ポリエチレンテレフタレート(PET)など様々な種類が含まれます。その中で厄介な存在が、PVCでした(図4)。
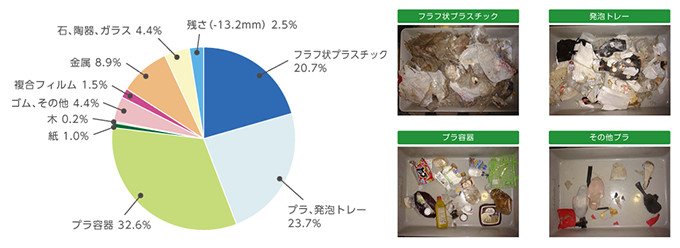
図4 一般廃プラスチック系廃棄物の組成調査結果
食品用ラッピングフィルムにも使われているPVCですが、これが不完全燃焼すると、発ガン性物質であるダイオキシンが発生してしまうおそれがあります。それを避けて高温で燃焼させると、今度は装置の腐食の原因となる塩素ガスを発生してしまいます。
ところが、ほかのプラスチック類とPVCは、重さも見た目も大きく変わらず、当時は合理的な選別方法や除去方法が見当たりませんでした。そのため、燃料としての品質を確保するためPVCをなんとかして脱塩素処理する方法・技術を開発しなければなりませんでした。
そこでNEDOプロジェクトでは、(1)一般廃棄物の選別技術、(2)多様な原料が混合しても問題なく破砕処理できる技術、(3)脱塩技術・方法の確立が、大きな目標となりました。
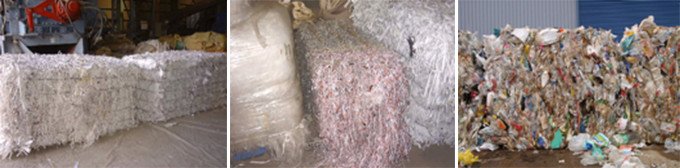
原材料別などにしっかり分別された状態で入荷する産業廃棄物の違い(左:ポリプロピレンのコート紙、中央:PET、右:プラスチック類が混合した一般廃棄物)(写真提供:アーステクニカ、関商店)
BREAKTHROUGH プロジェクトの突破口
脱塩処理技術の確立に挑む
そこで、川崎重工業が最初に取り組んだのが、ポリ塩化ビニルの処理法の検討でした。
PVCは、300~350℃の環境下に7~15分程度放置すると、塩素が抜けて塩素ガスが発生します。そこで、川崎重工業では、選別の難しいPVCが混入したままの原料を、300℃以上の高温下に置き、塩素ガスを発生させ、原料から塩素を抜き取ってしまう方法を考案しました。
開発された脱塩装置は、破砕した原料を2軸スクリューで圧縮して押し出し、熱風で高熱になった加熱部を通すことで塩素ガスを発生させ、回収するというものでした(図5、6)。
塩素の回収(脱塩)については目標どおりの効果が上がりましたが、古紙と廃プラスチックが混合したままで脱塩処理を行うと、原料中の古紙配合率が高くなると脱塩処理後製品の残留塩素濃度が高くなってしまい、また、脱塩のための加熱により、火力のもとともなる古紙中のセルロースが分解、ガス化してしまい質量が減少、燃料としての品質維持が難しいなど、実用化に向けた問題点も浮かび上がってきました。
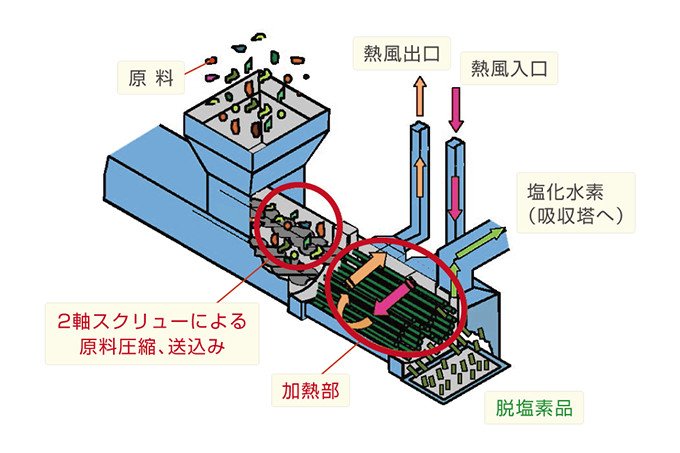
図5 RPF製造のために開発された「加熱管式2軸スクリュー減容型脱塩素装」
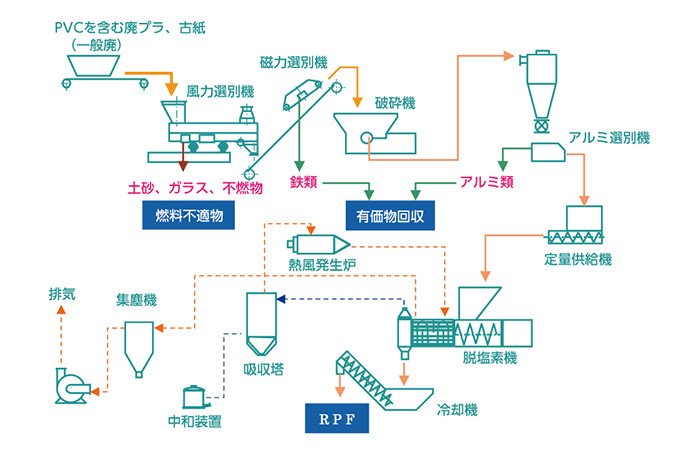
図6 ベンチスケールの選別・脱塩・成形の試験装置フロー
こうした事態に対応するため、川崎重工業ではRPFの製造フロー自体を見直すことから、問題解決を模索しました。その結果、本来、排出源の異なる一般廃棄物と、古紙やPVCが混入していない産業廃棄物系プラスチックを混ぜ合わせることなく、ラインを二重化して、PVCを含む一般廃棄物系プラスチックのみ選別や脱塩処理をする方法に改め、残留塩素の問題や加熱によるセルロースのガス化を防ぐことにしました。
また、脱塩装置も脱塩性能向上のために、一度脱塩した原料を再度スクリューで圧縮・加熱して塩化水素を発生させる、2段構造へと改良しました(図7)。
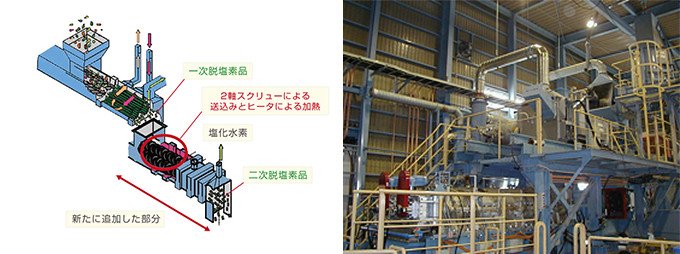
図7 改良された脱塩装置の構造図(左)と実証プラントに設置された脱塩装置(右)(写真提供:アーステクニカ・関商店)
破砕機の刃と異物を除去する選別機も開発
一方、破砕機に関しては、カッターの刃の形状を見直しました。破砕機では、先に刃がついた円筒形のローターが1分間に50~100回の速さで回転し、原料を破砕していきます。従来のラミネート加工紙とは異なり、廃プラスチックの場合、硬さも大きさも千差万別です。そこで、アーステクニカ技術・品証総括部副総括部長の西昌彦さんらはいかに高いエネルギー効率であらゆる廃プラスチックを破砕するかを目標に掲げ、刃の形状を設計していきました(図8)。
「プラスチックを、紙を固めるための接着剤として機能させるには、熱をむらなく伝えて溶解させる必要があります。そのためには、どのプラスチックもすべて10mm程度の細かさで破砕しなければなりませんでした。そこで、細かく破砕するのに最適な刃の形状を研究しました。この研究で得た知見は、のちに原料を建設廃材の木くずなどにも広げた際に大変役立ちました」と西さんは説明します。
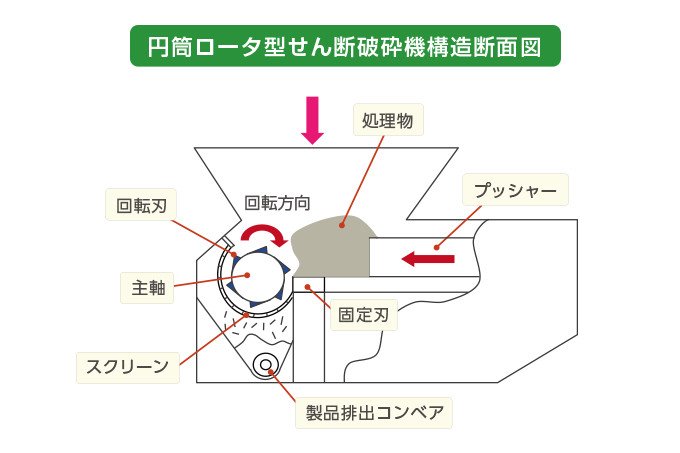
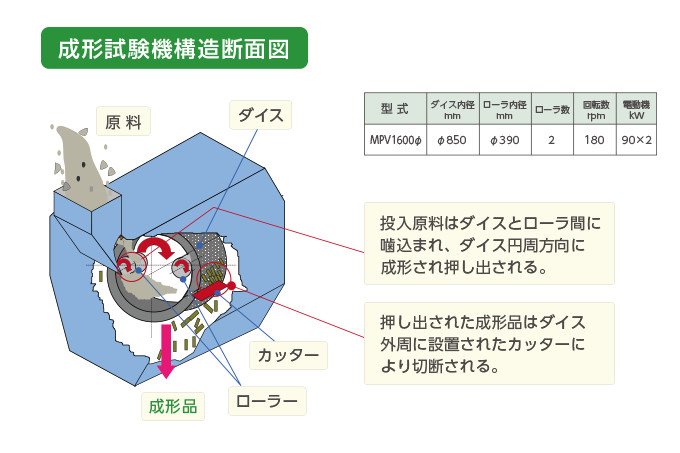
図8 破砕機の模式図(上)、成型機の構造図(下)
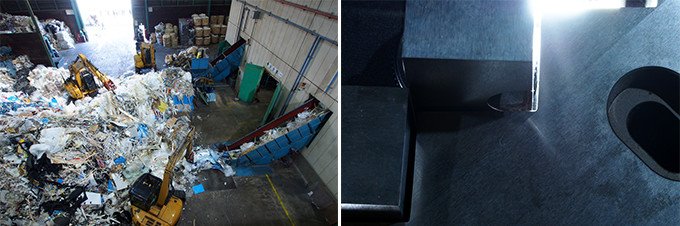
原料の破砕機へ投入口(左)、破砕機の回転刃と固定刃(右)
加えて、一般の可燃ゴミを原料とする場合、金属や石などさまざまな異物が混入しています。そこで、破砕の前工程として、風力を利用してプラスチックと異物を分ける風力選別機を開発しました。比重の低いプラスチックだけを風で飛ばして選り分けるのです。
「実際、例えば、食器のフォークやボルトなど色々な異物が含まれていました。そういったものが紛れていると、破砕機の刃を痛めたり、RPFの品質を低下させたりする原因になるので、いかに労力と時間をかけることなく除去するかということを念頭に置いて開発しました」と西さん。
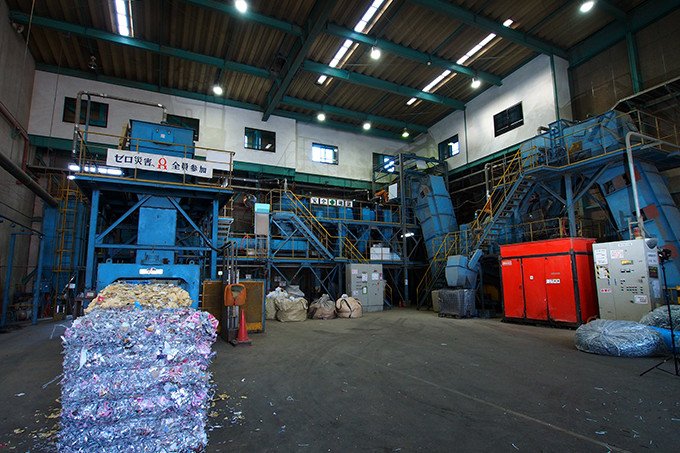
磁選機や風選機など前処理工程の装置群
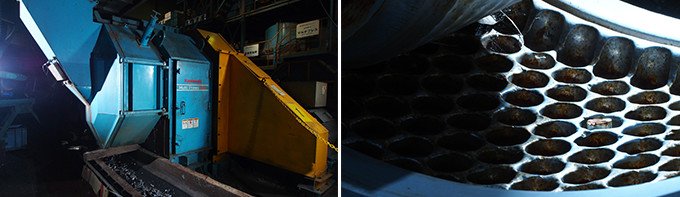
成型機からはき出されるRPF(左)、成型機の内部にあるリング状のダイス(右)。
さらに、成形機に関しては、RPFのユーザーとなる企業の多様なニーズに対応できるように、直径8mm、15mm、20mmの3種類の成形機用部品を開発しました(図8)。
このようにして、NEDOプロジェクトの最終年度に当たる2002年度、川崎重工業は一般の可燃ゴミを原料とするRPFの製造システムの実証プラントを無事完成させ、RPFのコンセプトを実証することができました(図9)。
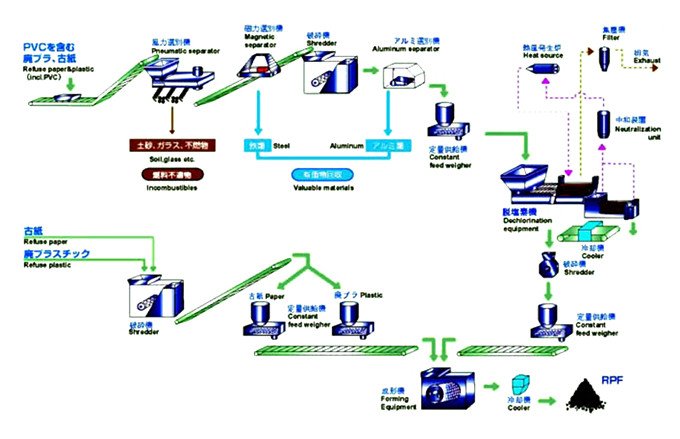
図9 実証プラントの製造フロー図
NEDOプロジェクトだからこそできた新技術の追求、その知見が事業化への現実的な選択を可能にしました
さて、実証プラントでは、プロジェクトの目標としたそれぞれの課題をクリアすることができましたが、一番手のかかった脱塩装置について、100%の除去実績を上げたものの、実用機への採用は見送られることになりました。
現在、アーステクニカ取締役で、製造総括部長兼製造部長の釜瀬俊英さんはこう打ち明けます。
「皆が一丸となって取り組み、苦労して開発した装置でした。しかし残念ながら、実用化には至りませんでした。その理由は、安全性とエネルギー効率でした。脱塩装置は別の見方をすると、腐食性が高く、またダイオキシンの元凶ともなりうる塩素ガスの高濃度発生装置ということになります。そのため、排ガス処理には細心の注意と設備が必要となり、RPFの製造システムの複雑化、高コスト化を招く要因になりました。」
「つぎに、廃プラスチックを300℃以上の高温で加熱することも大きな問題でした。燃料を製造するために大量の燃料を消費しては本末転倒です。さらに、原料組成が様々なため加熱すると、塩素ガス以外の可燃性ガス発生の可能性もあり、取扱いが容易でないことが分かりました。そのため、脱塩装置の実用化は諦めざるを得なかったのです」
しかし、長年、技術者、経営者として多くの研究開発プロジェクトに関わってきた関さんは力を込めて言います。
「新しい発想や技術が研究開発段階では成功しても、事業化には問題があると分かることも、新規製品を成功させるためには、大変重要なことです。その点、今回のNEDOプロジェクトでの脱塩装置開発は、とてもチャレンジングな取り組みであり、意義深いことだったと捉えています」
「ですから、プラントには組み込まれていなくとも、NEDOプロジェクトで脱塩装置を徹底的に研究開発したことが、現在のRPF製造プラント成功のブレークスルーの一つだったと言っても言い過ぎではないと私は思っています」
当時、川崎重工業の破砕機事業部で、RPF製造プラントの研究開発に取り組んだ、アーステクニカ技術・品証総括部副総括部長の西昌彦さんはこう語ります。
「NEDOプロジェクトで脱塩装置を実際に開発して、その効果があることを確認したからこそ自信を持って別の方法を探る決断ができました。開発した脱塩装置に変わる方法を何が何でも探し出す、という強い動機付けになりました。それが結果的に、現在のプラントに採用されているPVCを選別する光学式センサーの導入、最適化へとつながりました」
西さんの言う「光学式センサー」とは、近赤外線を使ってPVCを見分ける装置。プラスチックはその種類によって吸収する光の波長が異なります。その特性を利用して、PVCだけを選別することができるのです。この装置はNEDOプロジェクト終了後、関さんと西さんが欧州に視察に出かけ、捜しだしたものです。当然、本来は他用途向けの装置で、それをRPF用に独自の改良を加えてプラントに組み込んでいます(図10)。
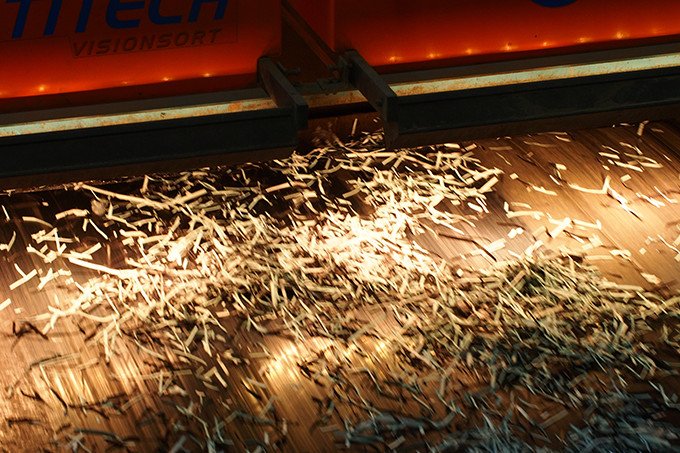
光学式センサーを利用したPVC選別機
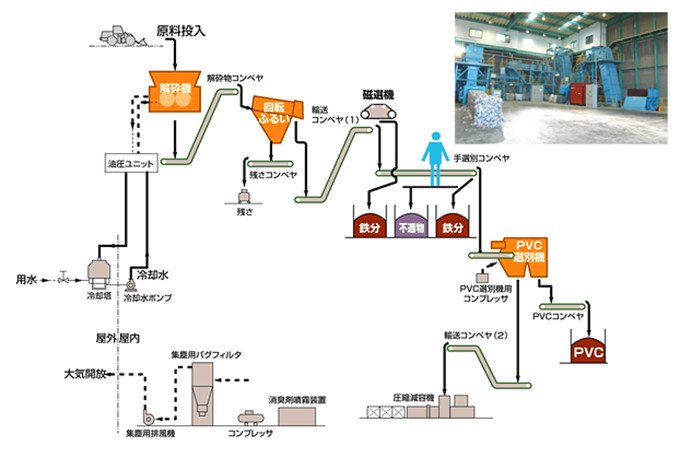
図10 現在の製造フロー図(前処理工程)
FOR THE FUTURE 開発のいま、そして未来
現在は原料となる廃棄物を選択して製品の発熱量や品質をコントロール
現在、関商店では廃プラスチック系の原料に、プラスチックの種類が予め把握できる産業廃棄物を主に、徹底的に分別された一般廃棄物を使用しています。それは、プラスチックの種類によって発熱量が異なるため、プラスチックの種類や混ぜる古紙の比率を調整して、石炭に相当する6,000kcal/kgと、コークスに相当する8,000kcal/kgの2種類の発熱量のRPFを製造するためです。
「現在は、品質管理が容易な産業廃棄物を主体に使っていますが、NEDOプロジェクトを通して多くの知見と技術を得ることができましたので、今後、産業廃棄物の量が減少したとしてもいつでも一般の可燃廃棄物でも対応できるという自信がつきました」と、関さんは語ります。
また、NEDOプロジェクト終了時の2002年度には、全国で年間8.3万tだった生産量も、2004年度には5.4倍の年間約45万t、2013年度には年間約110万tと順調に伸び続け、製紙会社、セメント会社、製鉄会社を中心に、RPFは石炭やコークスの代替燃料として、定着してきています。
2010年1月には工業製品としてJIS規格化も整い、粗悪品の流通を防ぐ手段が確立しました。RPFを製造、販売する企業も、現在では200社を超えており、市場規模も230億円を超え、2012年には、RPFの品質管理や普及拡大のために、「一般社団法人日本RPF工業会」も設立されました。
石炭と変わらない発熱量でも、CO2排出量は減少、価格も割安で注目される
市場が急成長した最も大きな要因は、同じ発熱量で換算した場合、石炭と比べてCO2排出量が約2/3、そして、価格が割安であることです(図11)。
従来、企業は廃プラスチックを、産業廃棄物処理業者に1t当たり4万~5万円で引き取ってもらっていました。それに対し、関商店は、企業からその半値以下の価格で引き取り、さらにRPFに加工して、販売しています。つまり、原料となる古紙や廃プラスチックを供給してくれる企業と、RPFを消費する企業の両方から収入を得ることで、石炭に比べて、安価な燃料を提供することができているというわけなのです。
産業廃棄物を処分したい企業は、より安価で引き取ってもらうことができますし、燃料を必要とする企業も、より安価で購入することができるわけです。しかも、CO2排出量は石炭に比べて大幅に少なく、燃焼後に残る灰も石炭の半分以下。まさに、生産からリサイクルまでのチェーンに関わるステークホルダーすべてがメリットを享受でき、しかも地球環境にもやさしい、今後の循環型社会の実現に理想的とも言える燃料です(図12)。
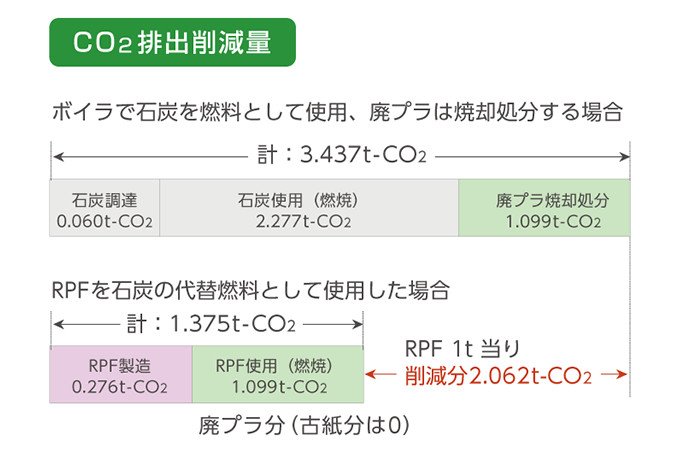
図11 RPFによるCO2排出削減効果
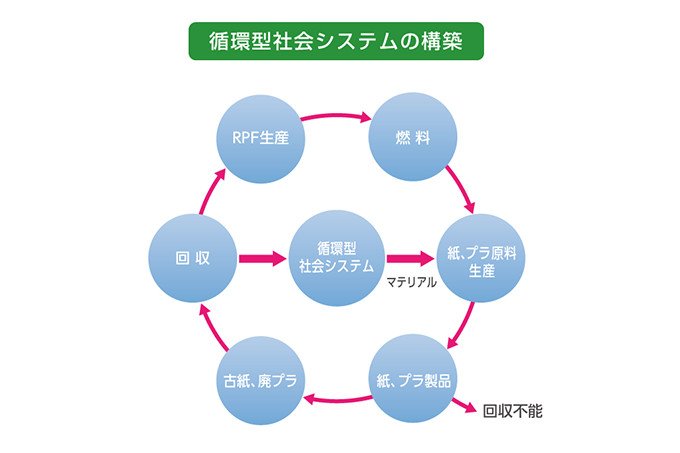
図12 だれもがメリットを享受できて、環境負荷も低いRPF
このような事業は1社だけで取り組んでも普及しない
現在、日本RPF工業会の会長を務める関さんは、RPF普及成功のポイントを、「このような事業は1社だけで取り組んでいても決して普及することはありません。ですから、製造技術を確立した後は、より多くの方に参加者になってほしいと願い、われわれ1社だけでその技術を独占することなく、希望する会社には技術指導も行い、普及に努めてきました。そのためにJIS規格化を急ぎ、工業会も設置しました」と説明します。
ラミネート紙の廃棄状況を見て思い立ったRPFの実用化を成し遂げることができた関さん。その研究開発、普及拡大の道のりを振り返って、最も感慨深かったことを尋ねると、「関商店が生産・流通するRPFだけでも、年間あたり一般的な最終処分場のおよそ1個半分を超える廃棄物の排出を抑制し、ひっ迫する最終処分場の延命に貢献できたこと」とすぐさま返答がありました。
高度成長期、生産拡大ばかりに関心が集まり、産業の静脈である廃棄物処理やリサイクル産業の未整備を感じて、大手企業のサラリーマンから、あえてリスクのある経営者の道を選んだ、関社長らしい答えと言えるでしょう。
そして、次の目標は、RPFが石炭やコークスの代替燃料なのに対し、工業用燃料として一番消費されている重油の代替として使用できる燃料を開発することだと、関さんは言います。まだ、詳細は明らかにできないが、近い将来、製品化できるめどは立っていると言うことで、次なる新燃料の登場に期待が膨らみます。(取材日2014年1月)
開発者の横顔
RPFを通して地球環境と社会に貢献
廃棄物の最終処分場の延命は私の一番の誇り
RPFの考案者である関勝四郎さんは大学卒業後、大手商社に勤めたもののすぐに退職、家業の鉄回収業を継ぎました。それは、大手企業では、自分の発想や力をいかすには時間がかかりすぎると考えてのことでした。
また、当時、日本が高度成長を謳歌する中、鉄鋼業界は生産分野の「動脈産業」だけが注目され、使用済みの鉄を処分、再生する「静脈産業」が整っていないことに、強い疑問を感じていたことも、商社を辞して、家業を継承経営することにした理由でもありました。
そこに、急速に普及が始まったのが、紙であるにも関わらず、リサイクルが困難なラミネート加工でした。本来、静脈産業が整備されていたはずの製紙業と、鉄のそれと重ね合わせ、自分でこの問題を解決しようと一大決心をしました。
「私は1986年にRPFを思いついた時から、売れる製品であること、毎日大量に処理できること、そして、継続的に消費される製品であることの三つを掲げ、事業を推進してきました。最初の出発点はラミネート加工紙の有効利用だったわけですが、事業をさらに拡大するには、原料を一般の可燃廃棄物にまで広げることが、避けて通ることのできない道でした」
「とはいえ、それには高いリスクが伴いました。それを通商産業省(経済産業省)に理解、支援していただき、NEDOプロジェクトとして実用化を推進できたことは有難かったですね。その結果、CO2排出量の削減やゴミの最終処分場の延命など、地球環境や社会に対して多くの貢献をすることができました。これは私の大きな誇りです」
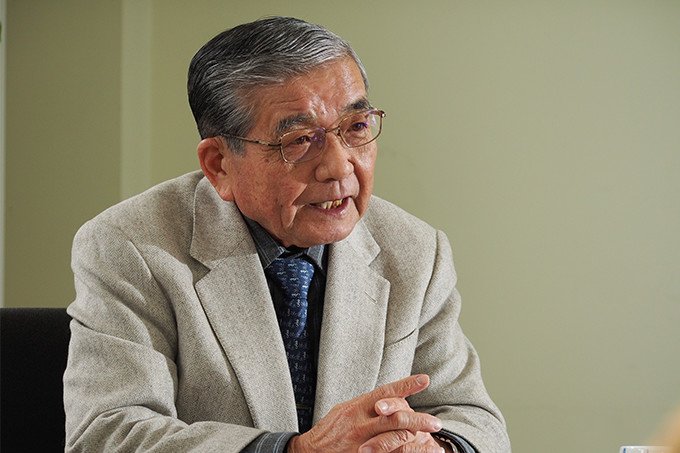
株式会社関商店
関さん
いくつになっても新たなことに挑戦するのは素晴らしい
1974年に川崎重工業に入社以来、技術者として破砕装置などの開発に携わってきた釜瀬俊英さん。現在は、2003年に川崎重工業と神戸製鋼所の破砕部門が統合し、分社化した「アーステクニカ」の取締役であり、製造総括部長と製造部長も兼任しています。
「関社長とは、関商店が1995年に群馬県・館林工場に架橋ポリエチレンを主体としたRPF設備1号機を設置して以来のお付き合いです。関社長の、『この館林工場は燃料製造工場であって廃棄物処理場ではない』という言葉に感銘しました」
「NEDOプロジェクトでは脱塩装置の研究開発に苦労しました。しかし、その経験が、PVC選別に使える光学センサーを見つけ出すきっかけになったという点で、十分意義があったと思っています。また、RPF製造システムの開発に携われたお陰で、様々な研究課題に挑戦することができました。大変好奇心をそそられましたし、やりがいを感じることができました。いくつになっても新たなことに挑戦するというのは、素晴らしいことだと思います」
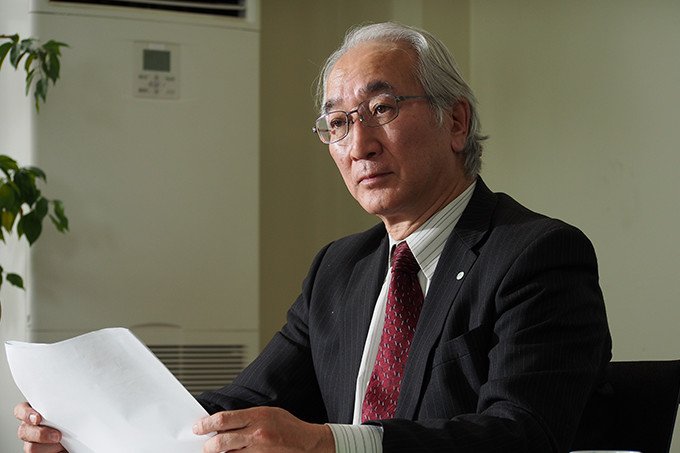
株式会社アーステクニカ
(元・川崎重工業株式会社破砕事業部)
釜瀬さん
すべて自分で勉強しながら進めていく、装置開発の仕事に大きなやりがい
大学で機械工学を学んだ後、1984年に川崎重工業に入社。以来、釜瀬取締役同様、破砕事業部で破砕装置の開発に携わってきた西昌彦さん。現在はアーステクニカの技術・品証総括部副総括部長を務めています。NEDOプロジェクトでは、研究開発の中心的役割を担いました。
「川崎重工業破砕事業部はむかしから少数精鋭がモットーで、各種装置の開発に当たって、技術者は入社1年目から、川上の計画から実設計、現場での試運転、そして川下の性能確認まですべての工程を担当します。しかも、新たな開発を行うにしても先輩が10歳も上のため、すべて自分で一から勉強しながら進めていかなければなりませんでした」
「RPF製造システムの開発においても同様で、試行錯誤の連続でしたが、その分、やりがいが大きく、期待以上の結果を出せたときは本当に嬉しかったですね。NEDOプロジェクトは今回が初めての参加でしたが、責任の重大さを感じながらプロジェクトを進めさせていただきました」
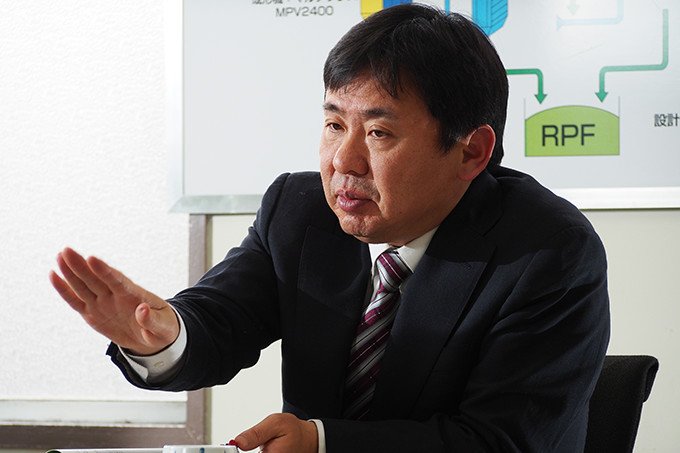
株式会社アーステクニカ
(元・川崎重工業株式会社破砕事業部)
西さん
なるほど基礎知識
「RPF」と「RDF」の違い
「RPF」とほぼ同時期に開発が進められたリサイクル燃料に、「RDF」があります。これは「Refuse Derived Fuel」の略称で、廃棄物由来の固形化燃料と言う点では、RPFと同じですが、その開発コンセプトや目的、燃料の性質は大きく異なります。
RPFとRDFの最も大きく異なる点は、RPFのもともとの原料が、民間企業から排出される分別済みの産業廃棄物系の古紙や廃プラスチックのリサイクルに端を発しているのに対して、RDFの原料は、主に家庭から排出される一般廃棄物であることです。
これは、RPFが固形燃料の製造を主眼としたものであるのに対して、RDFが廃棄物の減容や有効活用が主体でであったことからくる違いです(表A)。
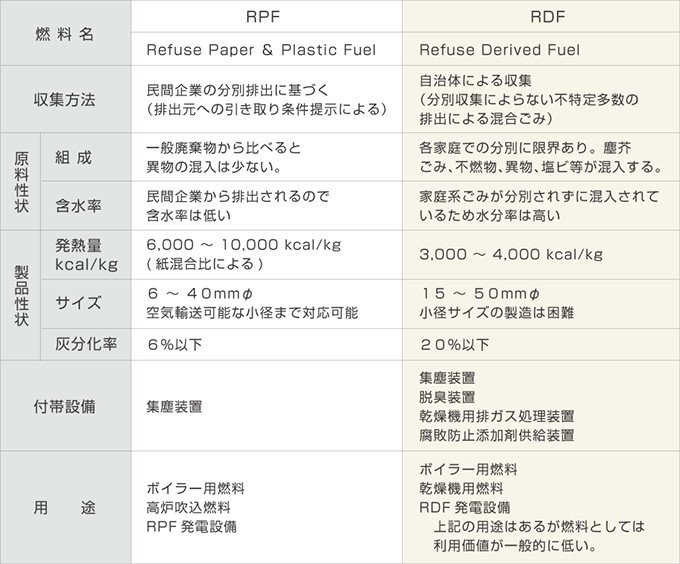
表A RPFとRDFの比較表
それゆえ、RDFの原料には、生ゴミも含めて様々な廃棄物が含まれて、水分率が高く、RPFに比べて単位重量当たりの発熱量が低いという課題がありました。また、RPFのように固形燃料製品としての品質確保のための選別とは、違う発想で選別、生産が行われていたRDFには、ダイオキシン発生の原因となるポリ塩化ビニルが含まれているケースもあり、公害の発生が危惧されていました。
さらに、追い打ちをかけるように、2003年に三重県桑名郡のRDF発電プラントで、RDFから発生した可燃性ガスが原因の爆発死亡事故が発生してしまいました。それを機に、RPFの急成長とは対照的に、RDFは急速に普及が減速していきました。
NEDOの役割
「即効的・革新的エネルギー環境技術研究開発/可燃ごみ再資源燃料化技術開発」
このプロジェクトがはじまったのは?
「即効的・革新的エネルギー環境技術研究開発」制度は、1997年12月の「気候変動枠組条約第3回締約国会議(COP3)」において採択された京都議定書合意事項「温室効果ガスを2008年から2012年までに1990年比で6%削減すること」への対応として、早期の実効性を期待でき、かつ新規のエネルギー環境技術に関する研究開発の積極的な推進を図るために設けられたものです。気候変動に関する政府間パネル(IPCC)において、バイオマス原料を由来とする食料品、木材、紙類の焼却によって排出されるCO2はゼロカウントになることから、原料に古紙を利用しているRPFに着目し、石油代替エネルギー関連テーマとしてプロジェクトを開始しました。
プロジェクトのねらいは?
温室効果ガスであるCO2排出量を削減するためには、未利用エネルギーである廃棄物エネルギーの有効利用が重要です。可燃ごみからRPFを製造し、化石燃料の代替エネルギーとして有効利用するためには、古紙及び廃プラスチックに含まれている塩素分を、燃焼の支障にならない程度まで除去して、燃焼時のダイオキシン類の発生を抑制することが不可欠です。本プロジェクトは、RPFの前処理技術、脱塩素技術等を開発して、可燃廃棄物の再資源化技術を確立することにより、地球温暖化防止および、リサイクルの推進に資することを目的としていました。
プロジェクト開始当時、塩素分を含まない廃プラスチックのみを原料としたRPFはすでに流通していましたが、RPFについての系統的な研究はありませんでした。廃プラスチックの脱塩素技術については、油化・高炉吹込みなどの前処理技術として、いくつかの研究が行われていましたが、簡便な方式でかつ、効果的な処理方法が求められていました。古紙が主成分のRPFを石炭代替燃料として製紙工場のボイラー燃料に利用することは、製紙業におけるマテリアルの循環につながります。また、一般廃棄物のプラスチックに混入するポリ塩化ビニル(PVC:Poly Vinyl Chloride)を脱塩素処理してRPFに利用することができれば、自治体の埋め立て量の減少につながり社会的な貢献度も高いと考えられました。
分別回収された古紙と廃プラスチックを主原料として、既存のボイラー等で化石燃料に代替可能な、汎用性の高い固形燃料とするために、次のような燃料品質を開発目標としていました。
NEDOの役割は?
プロジェクト開始当時、古紙および廃プラスチックのリサイクルは国家的課題となっており、実用的なリサイクル技術の早期確立が強く求められていました。また、そうした状況下で、燃料として廃棄物を再資源化する「サーマルリサイクル」については、燃焼の際に発生するダイオキシン類などの排ガス処理が深刻な問題になっていました。その対策としてリサイクル原料を脱塩素することが効果的と考えられましたが、プロジェクト開始当時、脱塩素された固形燃料の製造技術は未開発でした。廃棄物を再資源化した脱塩固形燃料の実用化は、石油代替エネルギーとして温室効果ガス削減や廃棄物の埋め立て処分量減少にも役立つ、革新的な技術として、即効的な効果を期待できることから、国の支援が必要と考えられ、NEDOでも研究開発プロジェクトを実施して、その実用化を推し進めました。
関連プロジェクト
- 即効的・革新的エネルギー環境技術研究開発/可燃ごみ再資源燃料化技術開発(1998年度~2001年度)
お読みいただきありがとうございました。
ぜひともアンケートにお答えいただき、
お読みいただいた感想をお聞かせください。
いただいた感想は、
今後の連載の参考とさせていただきます。