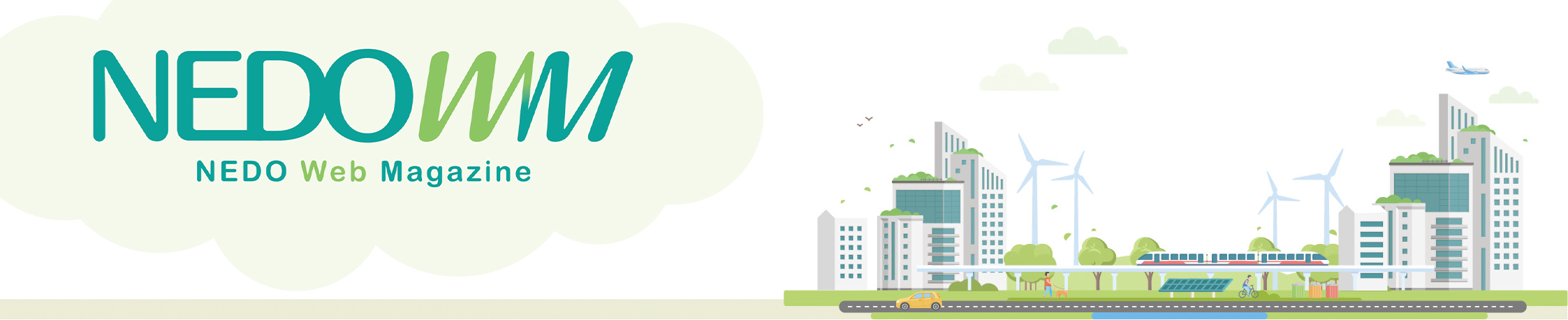
CONTENTS
INTRODUCTION
高速・大型化、後工程作業の半減を実現BEGINNING
産学官連携で世界最高スペックを目指すBREAKTHROUGH
造形スピードをアップさせる「乾いた砂」FOR THE FUTURE
世界で勝ち抜く砂型技術FACE
設計と製造の一元化INTRODUCTION 概要
高速・大型化、後工程作業の半減を実現
現在、鋳造業界における砂型の製造は、市場要求がより高精度かつ短納期・低価格化しています。しかし、従来の木型工法による砂型の製造ではコスト削減などに限界があり、技術者の高齢化も重なってその要求に応えることが困難な状況になりつつあります。そこで注目されているのが、鋳造用砂型3Dプリンタです。鋳造用砂型3Dプリンタは、ダイレクトに砂型を造形できるため精度と作業性が向上し、設計の自由度が広がります。技術研究組合次世代3D積層造形技術総合開発機構(TRAFAM)は、NEDOプロジェクト「次世代型産業用3Dプリンタの造形技術開発・実用化事業」において、毎時10万ccという世界最高レベルの速度で造形できる大型鋳造用砂型3Dプリンタ「SCM-1800」の開発に成功しました。今後は自動車や航空機エンジンの部品など、本成果の量産への適用が期待されています。
BIGINNING 開発への道
産学官連携で世界最高スペックを目指す
「鋳造」とは、金属を熱で溶かし、鋳型に流し込んで成形する金属の加工法をいいます。自動車などに使用される機械部品の多くは鋳造によって作られた部品が使われており、日本のものづくりには欠かすことができない技術です。従来、鋳造に使う砂型は、最初に原型となる木型を作り、その木型を用いて作るものでした。しかし、木型は手作りのため工数がかさみ、コスト削減にも限界があります(図1)。
こうした状況の中、自動車などの機械部品の設計・開発手法として注目されているのが、鋳造用砂型3Dプリンタです。従来、木型を用いて作製していた砂型を、砂をバインダ(結合剤)で一層ずつ固めていくことで積層造形していきます。
図1(左) 従来の木工法
(木型を製作⇒砂を用いて木型の形状を転写⇒木型を取り出す⇒溶けた金属を流し込む⇒砂型を壊し鋳造品を取り出す)
写真1(右) 3Dプリンタによる砂型造形
3Dプリンタによる砂型造形では木型を作る必要がないため、鋳造品の試作が格段に容易になります。また、多数の試作により量産前の検証を十分に行えるようになり、製品の信頼性向上も期待できます(写真1)。2008年ごろ、当時の砂型3Dプリンタは欧米のメーカーが先行していました。しかし、海外の装置だと言語の壁があります。マニュアル、サポートも全て英語だったので日本のユーザーは導入することが難しいのが実情でした。装置のトラブル等が発生しても、遠距離であること、言語問題で正確にトラブルの内容を把握できない等、対応が遅れる問題があったのです。そこで国立研究開発法人産業技術総合研究所(産総研)製造技術研究部門総括研究主幹の岡根利光さんは、海外製プリンタに見劣りしない生産性で、より複雑な鋳造物を量産できるメイドインジャパンの砂型用3Dプリンタ開発を考えました。
図2 TRAFAM 体制図(鋳造用砂型3Dプリンタ開発)
こうした背景のもと、2013年7月に経済産業省の事業として「超精密三次元造形システム技術開発プロジェクト」がスタートし、TRAFAMがその翌年に設立されました(図2)。
TRAFAMは、世界最高水準の純国産産業用3Dプリンタの開発を目的として、2014年に設立された技術研究組合で、組合員は、岡根さんが所属する産総研のほか、装置開発、材料開発、実証・評価を担当する企業および大学等で構成されています。TRAFAMは高速化、高精度化、材料の多様化を実現する砂型積層造形(バインダジェット)方式を採用した次世代型産業用3Dプリンタの技術・材料の開発を行い、評価基盤等の周辺技術を開発して、ものづくりの高付加価値化を進めています。
「超精密三次元造形システム技術開発プロジェクト」でリーダーを務めた岡根さんの力強い開発パートナーが、群栄化学工業株式会社開発本部商品技術部長の永井康弘さん、シーメット株式会社取締役開発部部長の大場好一さん、株式会社コイワイ専務取締役の小岩井修二さんでした。
産学官連携の「超精密三次元造形システム技術開発プロジェクト」で目指したのは、海外の特許に抵触せず、海外製品の性能を上回る鋳造用砂型3Dプリンタの開発でした。コイワイは鋳物の試作・量産を行っており、海外のバインダジェット方式の3Dプリンタを2008年に日本で初めて導入するなど実績がありました。それだけに海外製品の問題点も熟知しており、自分たちの困り事が全て解決できれば、世界最高峰の3Dプリンタができると確信していました。そこに化学メーカーの群栄化学工業、光造形システムの製造販売の実績があるシーメットが加わりました。
バインダジェット方式を採用
樹脂や金属の部品を直接造形する従来の3Dプリンタは作製に時間がかかり、大量生産に向かないという側面がありました。そこで岡根さんはもともと鋳物の砂型に利用され、高速造形が可能なことで知られていたバインダジェット方式を利用することを考えました。
バインダジェット方式は、紙の印刷に使われているインクジェット方式の紙とインクの代わりに、敷きつめられた砂に、バインダと呼ばれる特殊な結合剤を噴出して立体物の断面に塗布する動きを繰り返して積層造形をする方式です(写真2)。
写真2 敷きつめられた砂にバインダが塗布された状態
「バインダジェット方式と同じ原理のインクジェット方式は印刷用の版下など大きなものの速い印刷に使われていたので、このスピードを利用したいと考えました」(岡根さん)
そして岡根さんは海外メーカーで主流のバインダジェット方式をさらに独自の方式へと改善します。
造形速度を毎時1万ccから10万ccへ
岡根さんは過去に、二輪車の車体フレーム部品を砂型用3Dプリンタで開発しており、15kgあったフレームを60%軽量化することに成功していました。
しかし問題はスピードでした。当時のバインダジェット方式の積層スピードは毎時1万cc。このスピードでは一般乗用車で量産型となると能力が足りませんでした。岡根さんは、速度を一桁上げれば量産にも対応できると考えていました。 例えば、自動車部品のシリンダーヘッドの鋳造であれば、砂型が6分に1個必要です。これは、1日10時間稼働とすると1日に100個生産できるスピードとなり、毎時10万cc以上あれば量産に対応できます。そこで岡根さんはプロジェクトで、毎時10万cc以上のスピードおよび最大造形サイズ1m×1m×0.6m以上を目標に設定しました。
すでにこの目標スペックが決まっていた段階でプロジェクトに参加した大場さんは、毎時10万ccという製造スピードに驚きながらも、「やってできないことはない。テストを重ねながら感触を掴んでいきました。自社のソフトウェア、ノウハウなど3Dや造形の技術には自信がありました。それをフル活用したということですね」と当時を振り返ります。
プロジェクトでは、いきなり10万ccのハードルは高いので、まずは1万ccのバインダジェット方式の装置を開発しました。そして商品化もしてユーザーの反応を見ながら、並行して5万ccのプロトタイプの装置を開発しました。設計から製造を毎年繰り返しながら、毎時10万ccという世界最高レベルの速度で造形できる3Dプリンタの開発がスタートしました。
BREAKTHROUGH プロジェクトの突破口
造形スピードをアップさせる「乾いた砂」
世界最速のスペックを目指すには、流動性がよく、型としての剥離性がよい、後処理が短時間で済む乾いた砂の使用が必須であり、それを実現するための材料開発が必要でした。今回作った砂の特徴は、触っても手に砂がくっつかないことです。これは材料の砂が乾燥しているためです。
この乾いた砂の開発にも時間がかかりました。群栄化学工業は「超精密三次元造形システム技術開発プロジェクト」のために、砂に触媒をコーティングした3D砂型用新材料「Catalyst Coated Sand(CCS)」を開発しました。これは原料砂の表面にバインダを硬化するための触媒をコーティングしたもので、バインダの硬化反応が起こる前は乾燥した状態です。従来の触媒は乾燥した状態で使用されることはなく、バインダとの反応直前まで乾燥状態を保持するCCSは画期的な進歩でした。 バインダには、プリントヘッドから噴射して硬化反応させる1液式の有機バインダを採用しました。 「触媒というのは液体で使うのが当たり前。乾燥状態で触媒を使うこと、特に砂に触媒をコーティングするということは今までありませんでした」(永井さん)
海外製の3Dプリンタで採用されている方式では、砂に触媒を入れて練っているので湿った砂になってしまいます。触媒が含まれた湿った砂を一面に敷き詰め、その後に固めたいところにだけバインダを吐出。すると触媒とバインダが混ざったところだけ固まります。しかしこれでは、湿った砂を使っているので砂をリサイクルすることができません。今回開発されたドライ砂は液体が含まれないので、余った砂をそのまま再利用できるという特性があります(写真3)。また、使用材料として乾いた砂を用いることで、造形後の後工程の余分な砂の除去作業時間を1/2に短縮することができました。
写真3 触媒を入れて練った砂(左) 触媒をコーティングした砂(CCS)(右)
こうして、「超精密三次元造形システム技術開発プロジェクト」で開発されたバインダジェット方式の印刷技術や、CCSなどの基礎技術を元に、毎時約1万ccの積層量の小型砂型積層造形装置「Sand Casting Meister SCM-800」が完成しました。そして、このベース技術が2017年にスタートしたNEDOプロジェクト「次世代型産業用3Dプリンタの造形技術開発・実用化事業」での大型化、そして「SCM1800」の開発へとつながります。
世界最速クラス3Dプリンタの特徴
NEDOプロジェクトの成果を基に製品化された高速大型鋳造用砂型3Dプリンタ「SCM-1800」の特徴は、まず鋳造用砂型3Dプリンタとして世界最高レベルの造形速度であることが挙げられます。バインダジェット方式を採用した上で造形速度を向上させるためには、積層工程1層ごとの動作時間を短縮する必要がありました。そのため、リコータ(砂を敷きつめる部品)の高速化やプリントヘッドのラインヘッド化(多数のプリントヘッドをライン上に並べて配置)による高速化(動画1)、プリントパターンデータの転送時間短縮などにより、従来の10倍の造形速度での高速連続動作を実現しました。
そして高性能で作業性に優れた乾いた砂と1液方式を採用したことには、具体的に次のようなメリットがあります。
① 高流動性:砂を敷く際の流動性が低下しないため、凝集しやすい球形の人工砂が適用可能であり、高耐火性を利用して、鋳込み温度が高い鋳鋼にも対応可能
② 高強度:硬化反応を阻害する溶媒を減らせるため、短時間で高い鋳型強度が得られる
③ 付帯作業性:造形後の硬化部分と未硬化部分の分離が良く、エア噴射などによる砂除去作業が容易
④ 砂再使用:造形部分以外の未硬化砂は、そのまま回収して再使用が可能
大型の造形スペース
これまで砂型3Dプリンタは多くの優位性を有していても、生産性の問題から鋳型の量産設備としては考えられてきませんでした。
しかし今回開発した装置では、1.8m×1m×0.75mの造形スペースと毎時10万ccの造形速度を実現したことにより、自動車部品に用いられる複雑な形状の中子(中に空洞の部分がある鋳物をつくるときに用いられる砂型のこと)などを本装置1台で量産することも可能となります(動画1)。
動画1 SCM-1800で実際に砂型造形を行っている様子
NEDOプロジェクトから開発・製品化された「SCM-1800」は産業機械、自動車などのさまざまな分野における鋳造現場の生産性向上に期待がもたれています。岡根さんはNEDOプロジェクトの役割について「NEDOプロジェクトとして実施したことで、ユーザー企業まで含めた体制を構築し、評価までを一貫して実施することができました。テストフェーズにおける量産機の安定性確保という意味で貢献してくれました。メンバーが集まって議論する場所もあった。1対1の話し合いにならず、場面をもって全員で話し合いをしたことが一番有益な財産でした」と語ります。
FOR THE FUTURE 開発のいま、そして未来
世界で勝ち抜く砂型技術
2019年、日刊工業新聞社主催の第48回日本産業技術大賞において「SCM-1800」は審査委員会特別賞を受賞しました。さらに同年、鋳造技術の発展に大きく寄与することが認められ、公益社団法人日本鋳造工学会より豊田賞を受賞するなど、完成した最高スペックの3Dプリンタは高い評価を得ています(写真4)。
プリンタ市場ではアメリカ、ドイツ、中国などの競合メーカーも開発を続けていますが、永井さんは自分たちが開発した技術に強い自信を持っています。
「鋳造メーカーから高いニーズがある砂のリサイクル技術は、鋳造で一番難しい技術でもあります。私たちが取り組んできたフラン系のバインダは、高い鋳型速度を有し、未反応のCCSはリサイクルが100%可能なので、ロス分はありません」(永井さん)
さらに、岡根さんも「造形速度とリサイクルを持っていることが武器です。砂型を効率よく造形し、後工程も短縮できるのでニーズは広がっています。完成するまでのスピードと精度を両立させながら設計通りの形ができることが、国際的にも競争力になる部分です」と語ります。
現在、3Dプリンタを利用した鋳造用砂型市場は、試作から少量多品種生産を経て量産利用を目指した検討が進んでいます。既に秋田県や兵庫県、三重県の各公設試験研究機関で導入され、地域の鋳造企業の支援に活用される他、企業への導入では大手ポンプメーカーをはじめ航空機や油圧機器の会社などで様々な試作や製造に活用されています。
写真4 公益社団法人日本鋳造工学会 豊田賞の受賞風景
「無機バインダ」と「100万cc」へのチャレンジ
また、プロジェクトでは2016年、CCSとフラン系有機バインダを製品化しました。これまでの鋳造では、フラン系は高強度鋳型ができる、フェノールフラン系は高耐熱性鋳型となり鋳鋼品に適するなど、それぞれの鋳型に特徴があり使い分けられています。フェノールフラン系も同時に開発を行っていましたが、NEDOプロジェクトでは、噴射するバインダにフラン系を使用しました。その理由について永井さんは「同じ熱量でもバインダや砂種により受ける影響が変わってきます。材料開発自体は行っていましたが、装置に合わせなければならなかった。しかしあまり材料が変わると装置に新たな機構を付与しなければならないということがあったので固定しました」と語ります。
造形速度10倍の高速化と造形サイズ10倍の大型化に加え、造形後の後工程作業時間の半減を実現する画期的な3Dプリンタの開発に成功した岡根さん。次なる目標は「毎時100万ccの大型鋳造用砂型3Dプリンタの製品化だ」といいます。 「高速化への夢はあります。あとは無機バインダに挑戦したい。鋳造用の無機3Dプリンタなど製造現場やユーザーのニーズを満たすものを作っていきたい」(岡根さん)
無機はシンプルな素材ですが、3Dプリンタに転換するためには材料をどのように使えるのかアイデアが必要になります。素材が違えば鋳造プロセスも異なります。形状もシンプルか複雑かなどの課題もあります。それぞれのユーザーのケースに合わせて鋳物用途や環境用途を考えたシステム化が重要になります。
「カバレッジを広くしていく。いろんな材料、いろんな金属、いろんな形に適応していきたい。やはりニーズを重視して考えていきたいですね」(岡根さん)
3Dプリンタを使えば高速での試作・少量生産が可能になるとともに、中子や木型を作る必要がなくなります。また数年後に使うために型を保存しておく必要もありません。分割していた中子を一体化して造形することも可能であり(写真5)、より高精度・薄肉・軽量化が期待できます。つまり、人の手で作ると半年かかるものが、3Dプリンタであれば一日で作ることも可能になるのです。こうして、NEDOプロジェクトで生まれた技術は、製造現場の未来を大きく変えようとしています。
写真5 中子を作るために本来必要な木型(左)
3Dプリンタで造形した中子(右)
3Dプリンタを使用することで、複雑な中子も木型を使用せずに作成できる
開発者の横顔
設計と製造の一元化
長く鋳造の研究をしてきた岡根さんはプロジェクトリーダーを務め、ニーズや社会背景など全体を見ながら、目標達成に向けた方向性を示してきました。そして今後は、より薄く、軽く、コンパクトに鋳造できることを目標に掲げています。
「3Dプリンタの鋳型は、鋳造の制約を減らせるというのが大きな存在意義です。設計担当者が作りたいものをすぐ形にできる。設計と製造の一元化。設計担当者と製造担当者が一緒に考えてやっていけば、これまでにない生産プロセスと新たな製品が可能になるでしょう」
岡根さんは、ユーザーの意見をフィードバックさせながら全体的な信頼性や性能を高めていきたいと開発を進めています。
国立研究開発法人産業技術総合研究所
製造技術研究部門 総括研究主幹
岡根 利光さん
無機バインダが次なる目標
永井さんは製品で使われる砂型やプロセス全体の開発を担当しました。NEDOプロジェクト前には、自動車メーカーで鋳造のテストも実施し、担当者らのフィードバックも得ていました。その結果、見えてきたのは、ユーザーである自動車メーカーがスピードだけを求めていないことでした。
「自動車メーカーはCO2やVOC(Volatile Organic Compounds:揮発性有機化合物)のゼロエミッションを目指していて、無機系のバインダを要望されました。無機材料の利用はまだ難しい。さらに、リサイクルできるものを目指して欲しいなど、メーカーからの要求は高いですね」
使用時の制約が少なく、多種の金属に対応できる汎用性のある材料の開発は進行中です。
群栄化学工業株式会社
開発本部 商品技術部長
永井 康弘さん
国産3Dプリンタの老舗として
大場さんは装置・ハード作りや、ソフトウェア開発・砂型条件出しなどを担当しました。もともと3Dプリンタに関する装置のノウハウや技術はありました。しかし、鋳造や砂型のことは知らないところからのスタートでした。
「岡根さんが説明やフォローを実施してプロジェクト全体をまとめて頂けたのでうまく開発を進めることができました。NEDOプロジェクトとして産総研や他の企業と共同研究する体制がなければ、プロジェクトは成功しなかったでしょう」
シーメットは製品を販売する窓口です。大場さんは「装置の改良改善を繰り返し、機能UPとコストリダクションをどんどん進めていきたい」と意欲を燃やします。
シーメット株式会社
取締役 開発部部長
大場 好一さん
日本の強さを大事にして、欧州に追いつく
小岩井さんは、実際に装置を使って砂型をつくる立場からのニーズのすり合わせなどを担当し、常にユーザーの現場ニーズに応えてきました。そして今後は、発注内容に応じて様々な機械装置を使い分けたり、ランニングコストや砂の性質を見極めていく必要があると語ります。
「日本の鋳造は流体もの(渦巻型ポンプ等)を作ることに非常に優れています。しかし今後は丸形の水力タービンなどでも使えるように、サイズが倍の鋳造もできるようにしたいですね。当社では新卒をはじめとした若い技術者を積極的に採用しており、こうしたデジタルネイティブ世代と3Dプリンタは親和性が高いと感じています。若手が即戦力になれる技術だと実感しています」
株式会社コイワイ
専務取締役
小岩井 修二さん
なるほど基礎知識
3Dプリンタ
3Dプリンタは、他の加工法では作れない複雑な形状の造形、多様化する顧客ニーズに対応した究極の少量多品種生産の実現など、ものづくりに革命を起こす潜在能力を持ち、欧米を中心に活発な技術開発が行われています。その造形方式は数種類あり、方式ごとに使える材料や造形物のサイズ・特性は異なります。
3Dプリンタにはバインダジェット方式以外に、熱溶解積層方式(FDM:FusedDeposition Modeling)、光造形方式、バウダーヘッド方式など、さまざまな種類があります。
FDM(熱溶融方式)は、熱で溶かした樹脂をノズルにより細い糸状に押し出して一筆書きの要領で造形します。高い耐久性や耐熱性を得やすいので、試作品や簡易型の造形などに適しています。反面、素材を溶かして積み上げていくため、断層が目立ちやすいデメリットがあり、表面の滑らかさが求められる造形物の出力には向きません。
光造形法(光重合方式)は、光硬化性樹脂(フォトポリマー)で満たされた槽の表面に紫外線レーザーを照射し、部品の断面パターンを一層ずつ硬化させて積層していく方式です。造形速度と精度、透明性に優れており、大きなサイズの造形も可能です。反面、プラスチックの造形法の中では比較的高価であり、表面に残った未硬化樹脂の洗浄、サポート除去など後処理に手間がかかる、といったデメリットがあります。
パウダーベット方式(粉末焼結積層造形法)は、金属造形にも使われる方式で、材料粉末を敷いた層にレーザー光を走査して溶融凝固・焼結・硬化させ、ステージ(造形スペース)を下げて一層ずつ造形していきます。 複雑な形状の造形品が得られるメリットがあります。反面、装置が大きいこと、維持費が高額となることが課題です。
今回のプロジェクトで使われたのは、バインダジェット方式です。原理は一般のインクジェットプリンタの紙を粉末層に、インクをバインダに置き換えたものです。粉末材料を1層敷きつめて重ねる動作と、バインダを造形物の断面形状に塗布して結合させる動作を交互に繰り返すことにより、3次元の造形物を作成します。造形終了後には造形物が粉末材料に埋没した状態になるため、それを取り出す後工程作業が必要となります。
NEDOの役割
「次世代型産業用3Dプリンタの造形技術開発・実用化事業」
(2017年度~2018年度)
(NEDO内担当部署:IoT推進部)
日本のものづくり産業がグローバル市場において持続的かつ発展的な競争力を維持するためには、ものづくりに革命を起こす存在である3Dプリンタを核とした新たな産業形態を目指す必要があります。
そこでNEDOは、地域の中小企業等の持つ技術や資源を活用し、少量多品種で高付加価値の製品・部品に適した三次元積層造形技術や、その周辺技術の開発に取り組んできました。
その中で、本プロジェクトは、民間企業単独では取り組むことが困難な技術開発に対し、大学、公的研究機関を含めた産学官それぞれのノウハウを持ち寄る場を提供しました。
その結果、TRAFAMは毎時10万ccの世界最高レベルで造形する大型鋳造用砂型3Dプリンタの開発に成功しました。
関連プロジェクト
お読みいただきありがとうございました。
ぜひともアンケートにお答えいただき、
お読みいただいた感想をお聞かせください。
いただいた感想は、
今後の連載の参考とさせていただきます。