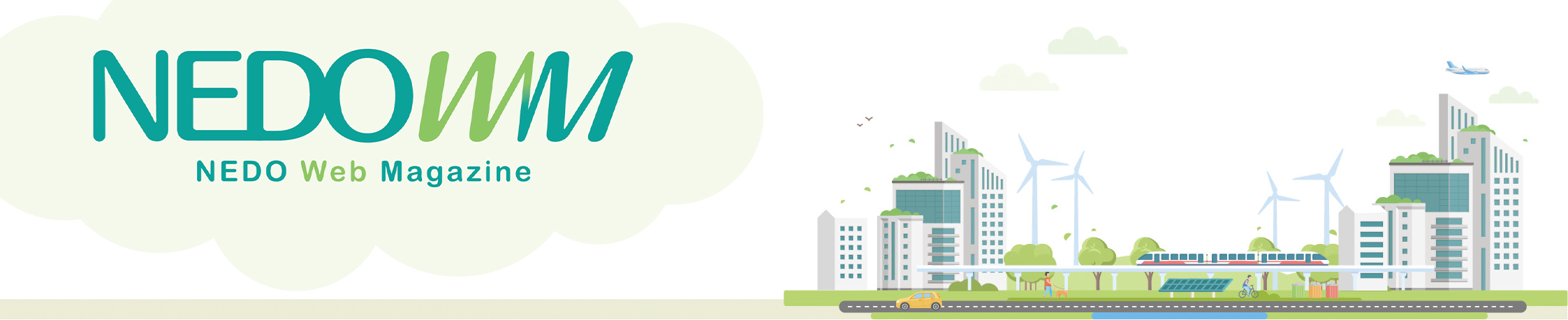
CONTENTS
INTRODUCTION
水素製造効率80%、従来設備比でサイズ1/2
BEGINNING
燃料電池自動車の普及には、水素ステーションが不可欠
BREAKTHROUGH
水蒸気使用量を抑えてエネルギー効率を向上FOR THE FUTURE
水素ステーションが身近な街の風景になる日のために
FACE
水素エネルギーの時代を切り拓くINTRODUCTION 概要
水素製造効率80%、従来設備比でサイズ1/2
走行時に有害物質もCO2も排出せず、しかもエネルギー効率が高く、ガソリン車と同等の走行距離が確保できる「燃料電池自動車」は、長らく"夢の自動車"として語られてきました。しかし、ついに2014年度から、一般ユーザーを念頭に置いた燃料電池自動車の生産、販売が始まろうとしています。
それに合わせて、燃料となる水素を車に供給する「水素ステーション」の整備が急がれており、既存のガソリンスタンドとの併設や液体水素の運搬・流通網を確保するなど、2015年度末までに全国100カ所程度の水素ステーションを整備することを目標とした産学官の取り組みが行われています。
「水素ステーション」には、ステーションへの水素供給方法が重要となります。その方法としては、水素ステーションの現場で液化石油ガス(LPガス)や都市ガスから水素を製造する「オンサイト型」と、圧縮水素や液体水素を水素ステーションの外部からトレーラーなどで運び込む「オフサイト型」があります。
工業用の大型水素製造装置を長年手がけてきたプラントメーカーの三菱化工機株式会社では、その実績を生かし1998年から、小型のオンサイト型水素製造装置の開発に取り組んできました。しかし、既存のガソリンスタンドに設置して、ガソリンと変わらぬ手軽さで利用できるようにするためには、これまで開発してきた水素製造装置を、さらに高機能かつ小型化する必要がありました。
そこで、三菱化工機は、2008年度よりNEDO「水素製造・輸送・貯蔵システム等技術開発」に参画し、従来比1/2の大きさで、改質効率85% (製造効率80%)の小型水素製造装置の開発に取り組み、水素製造装置「HyGeia-A」の製品化に成功しました。
現在は、 「HyGeia-A」の商用第1号機が、愛知県名古屋市緑区にあるガソリンスタンド併設型の水素ステーションへ納入され、現在も稼働しています。
BIGINNING 開発への道
燃料電池自動車の普及には、水素ステーションが不可欠
燃料電池自動車は、水素と酸素から電気をつくる燃料電池を搭載して、モーターを駆動、走行する自動車です。水(水蒸気)を排出するだけで、大気汚染物質もCO2 も排出しないことからエコカーの理想型と考えられていますが、それだけでなく、エネルギー効率も高いことが特色です。加えて同じ低公害型自動車である電気自動車と比べても、燃料充填時間の短さと航続距離の長さが利点とされています。
その燃料電池自動車が、2014年度からいよいよ販売が開始されようとしています。そこで、ガソリン自動車が給油所で燃料を補充するように、燃料電池自動車も水素を充填する場所が必要になります。
水素供給場所となる「水素ステーション」の新設、または既存のガソリンスタンドへの併設など、水素の供給インフラの整備が急がれます。この専用インフラ整備を必要とする点は、この点は、時間がかかっても、家庭用電源からでも充電できる電気自動車に比べると不利な点とも言えます。
NEDOでも、燃料電池自動車の普及拡大を見据えて、2005年から水素の製造や供給などに関わるロードマップをつくり、2015年ごろを燃料電池自動車の一般利用者への「普及開始」時期として、長期的な技術開発を行ってきました(図1)。また、国も、2015年に、先行整備として水素ステーションを全国100か所程度に設置することを目指しています(図2)。
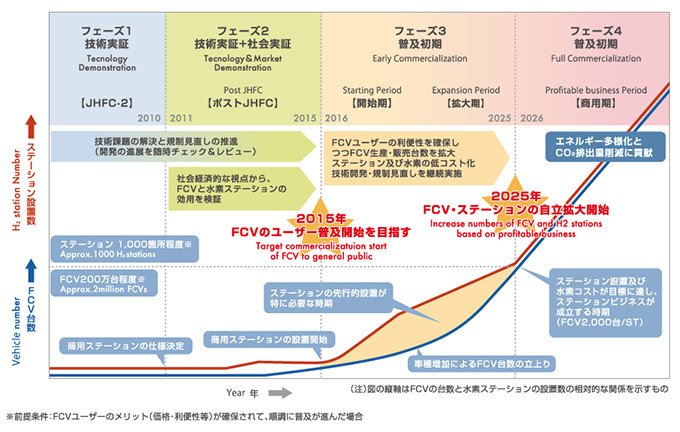
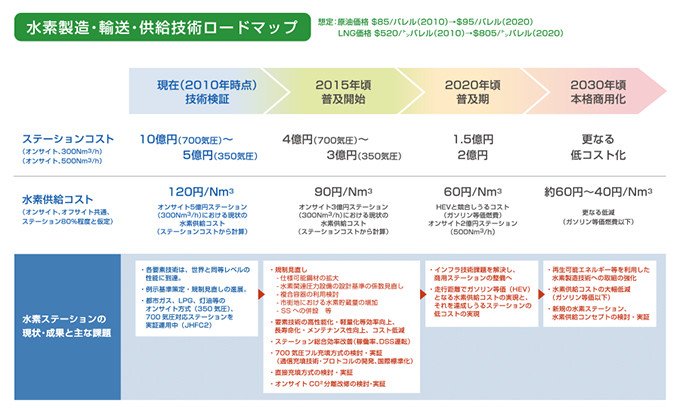
図1 FCCJ(上)とNEDO(下)が作成した水素製造・輸送・供給技術ロードマップ(2010年版)
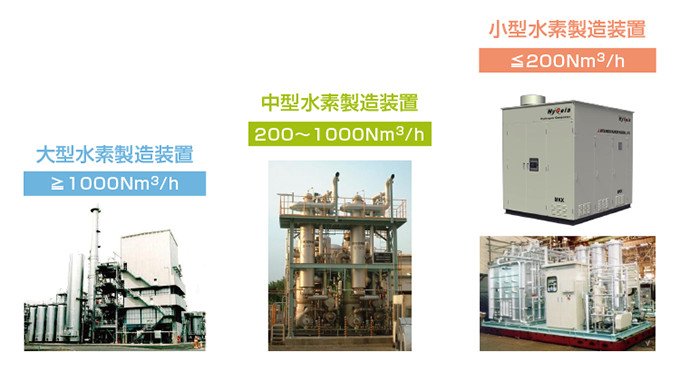
図2 大型・中型・小型に分類される水素製造装置(写真提供:三菱化工機株式会社)
ステーション内で水素を製造する装置を開発
石油精製や化学品原料用の大型水素製造装置や、光ファーバーの製造、半導体製造時に金属熱処理に使用される、中・小型水素製造装置を、各地の工場に納入してきており、これまでに120基以上の実績があります(図2)。
その実績をもとに、2001年からは水素ステーション用途の水素製造装置も研究開発してきました。工場で生産された水素をトレーラーなどで運んで貯蔵する「オフサイト型」ではなく、液化石油ガス(LPガス)や都市ガスから、水素ステーション内で水素を製造する「オンサイト型」水素ステーションの実用化と普及を、三菱化工機は目指してきました(図3)。
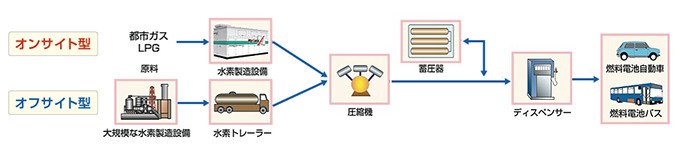
図3 オンサイト型とオフサイト型の違い
同社は、2008~2010年度にかけてNEDO「水素製造・輸送・貯蔵システム等技術開発」に参画し、水素ステーション向け小型水素製造装置の開発に取り組み、高性能化・低コスト化・コンパクト化を目指しました。
その結果、新しい小型水素製造装置「HyGeia-A」の製品化に成功し、2011年度には商用第1号機を、愛知県名古屋市緑区にある、ガソリンスタンド併設型の水素ステーション(建設・運営は、JX日鉱日石エネルギー)へ納入することができました。納入された商用機は、現在も稼働しています。
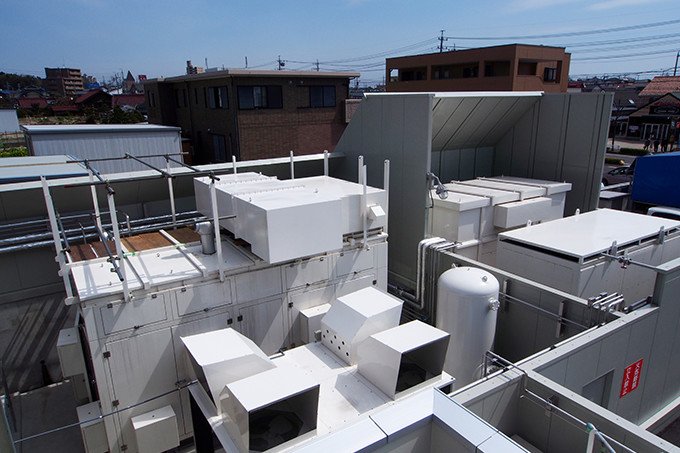
神の倉水素ステーションの一角に設置されたHyGeia-A(奥の装置)
改質、シフト反応、吸着で、高純度の水素を製造
愛知県名古屋市内にあるガソリンスタンド併設型の水素ステーション「神の倉水素ステーション」では「HyGeia-A」が使われています。「HyGeia-A」でつくられた水素は圧縮された状態で貯蔵されており、燃料電池自動車に水素を補給するときは、まるでガソリンをタンクに給油するように、ノズルをタンクに差し込み、数分で充填は完了します(図4)。
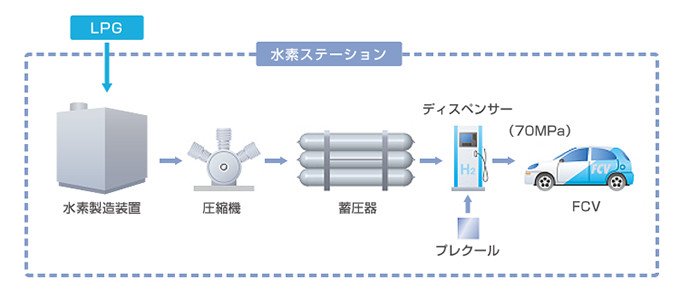
図4 神の倉水素ステーションのシステムフロー図
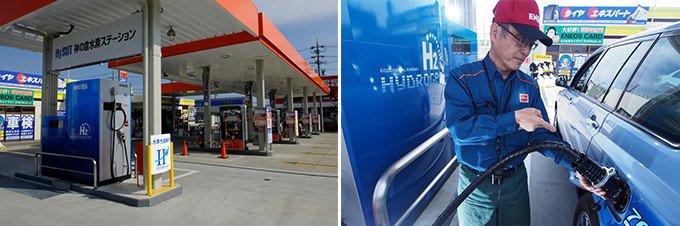
既存ガソリンスタンドに併設された神の倉水素ステーションと(左)、その充填風景(右)
神の倉水素ステーションの「HyGeia-A」では、LPガスから水素を製造しています。図5は、「HyGeia-A」における水素製造その流れを示した図になります。「HyGeia-A」では、LPガスや都市ガス等の炭化水素原料を水と高温で反応させて水素を生成します。このように原料の他に水を用いる方式は「水蒸気改質」と呼ばれます。
CnHm + nH2O → (n+m/2)H2+nCO
まず、原料ガスを圧縮機で圧縮し、原料中に含まれる硫黄分を化学反応を利用して除去(脱硫)します。脱硫された原料ガスと、装置の余剰の熱を利用して発生させた水蒸気を混合し、改質器に送ります。改質器では水蒸気改質により水素を主成分とする「改質ガス」が生成されます。
改質ガスを変成器に送り、改質ガス中の一酸化炭素と水蒸気を反応させることによりさらに水素が生成されます。この反応は「シフト反応」と呼ばれます。
CO+H2O→H2+CO2
変成器からでた「変成ガス」には水素の他に水、二酸化炭素、一酸化炭素、メタンが不純物として含まれています。これらの不純物を圧力スイング吸着(PSA:Pressure Swing Adsorption)という工程で除去し、高純度水素を精製します。
PSAでは吸着剤が充填された吸着塔に変成ガスを供給すると、不純物が吸着剤に取り込まれ、水素はそのまま吸着塔から出て行きます(吸着工程)。吸着剤が不純物を取り込む量は限りがあるので、一定時間経過後、変成ガスの供給を停止します。
このまま吸着塔の圧力を下げると吸着剤から不純物が脱着されます(脱着工程)。さらに、高純度の水素を流すことによって吸着剤が元の状態となります(洗浄工程)。
PSAには吸着塔が複数本あり、1塔が吸着工程で水素を製造している間、他の塔は脱着工程や洗浄工程を行なっており、1塔が吸着工程を終えると、違う塔が吸着工程となるようになっており、連続して高純度の水素を製造することが出来ます。
また、脱着工程や洗浄工程で排出される不純物を含んだガスは「オフガス」と呼ばれ、HyGeia-Aではこのオフガスを改質器のバーナーで燃焼させ、水蒸気改質で必要な熱として無駄なく利用しています。
こうした過程を経て、99.999%という極めて高い純度の水素ガスができあがります。その水素ガスの圧力を高めて容積を圧縮し、燃料電池自動車に供給します。
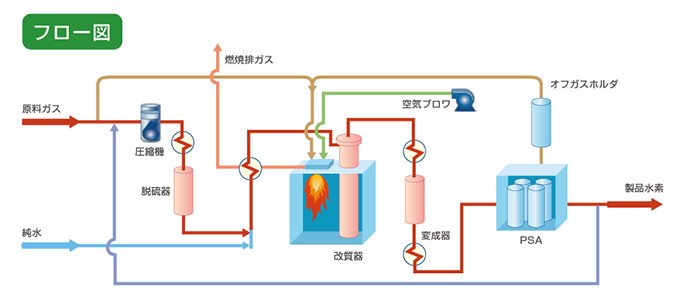
図5 「HyGeia-A」の水素製造フロー
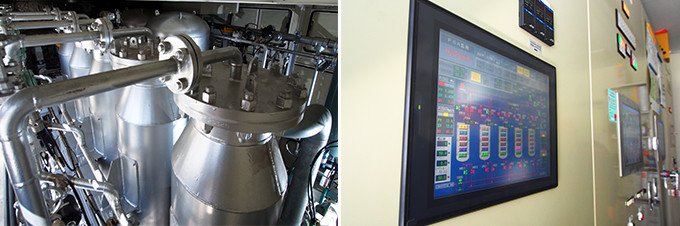
左・不純物の吸着と脱着を繰り返し、水素の純度を上げる圧力スイング吸着装置(PSA)、右・5塔のPSAを切り替え、その状況を示す制御盤
製造効率80%、サイズ1/2を実現
今後、燃料電池自動車が普及して、社会全体で広く水素を消費する時代を見据えると、より効率的に、低価格で、場所をとらずに、水素をつくることが必要になってきます。
そこで、三菱化工機では、水素エネルギーの時代にふさわしい、水素製造装置の実用化を目指してきました。NEDOプロジェクトの基で開発された「HyGeia-A」には、水素ステーション向けの水素製造装置として次のような特長があります。
燃料製造に必要な原料と電力エネルギーの和に対し、製造される水素のエネルギーは80%にもなります。この投入したエネルギーにに対する製造された水素のエネルギー比を「水素製造効率」と呼んでいます。
コンパクト化も進みました。1時間あたり300m³の水素を製造する装置の据え付け面積は24m³です。これは三菱化工機の従来製品の半分以下の面積です。製品価格も、今後の量産化によって従来製品の1/2程度になることが期待されています。
水素の製造コストは、水素の小売り価格に直結します。今後、水素エネルギー社会を拡大するためには、その水素価格そのものを他のエネルギー価格に近づけなければなりません。効率的に水素をつくる「HyGeia-A」は、今後のエネルギーの価格競争時代に一歩前進を果たした装置といえます。
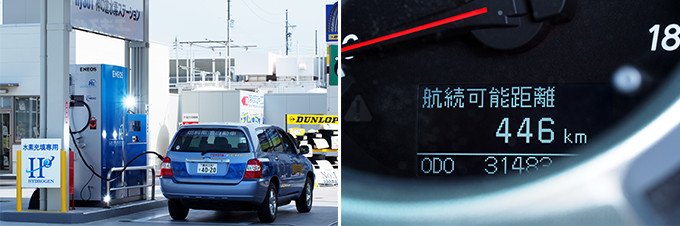
神の倉水素ステーションには、トヨタ自動車株式会社名古屋本社で使用されている、プロトタイプ燃料電池自動車が充填に訪れる、満充填になると航続距離は500キロを超える
目標は効率を上げ、コストを下げ、小さくすることだった
「HyGeia-A」の開発は、三菱化工機の水素製造技術と実証が積み重なった集大成の成果といえます。工業用途での水素製造装置の実績を積み重ねてきた三菱化工機は、小型の水素製造装置を実用化するために、1997年度から小型水素製造装置開発をスタートし、商品化するとともに、2000年度から、NEDO「固体高分子形燃料電池システム化技術開発」にも参画、「HyGeia-A」に至る、水蒸気改質型水素製造技術をブラッシュアップしてきました(図6)。
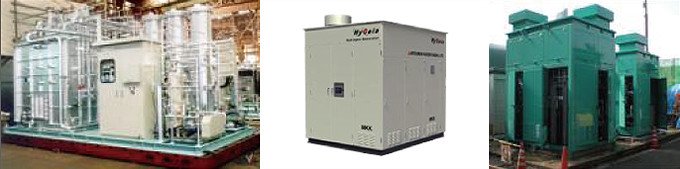
図6 歴代の小型水素製造装置。左・1999年、小型水素製造装置TM式。中・2004年に開発された小型水素製造装置 HyGeia。右・2012年、ステーション用水素製造装置 HyGeia-A(プロトタイプ型)(資料提供:三菱化工機株式会社)
また、経済産業省の呼びかけで民間企業が参加して2002年に始まった「水素・燃料電池実証プロジェクト(JHFCプロジェクト)」の初期段階から水素製造装置の納入、水素ステーションの建設に関わり、神奈川県横浜市の「横浜・旭水素ステーション」、東京都荒川区の「千住水素ステーション」などでの実証運転に寄与してきました。
しかし、燃料電池自動車の普及を促進するためには、さらなる効率の向上と装置コストの大幅低減が必要です。そこで、三菱化工機は、2008年度からNEDO「水素製造・輸送・貯蔵システム等技術開発事業」に参画しました。
その際の開発目標が、製造効率80%、改質効率85%、装置コスト9,000万円、メンテナンススペースを含んだ設置エリア55m³といったものでした。効率を上げ、コストを下げ、かつ小さくするという、矛盾だらけの条件を突破するような目標に挑むことになりました。
同社は、水素製造装置の主要機器である、改質器とPSA(圧力スイング吸着装置)を中心に3年間の事業期間で高性能化、小型化、低コスト化の開発を進めました。
BREAKTHROUGH プロジェクトの突破口
水蒸気使用量を抑えてエネルギー効率を向上
三菱化工機では、こうした高い目標を達成するために、水素製造技術のレベルアップをどのように実現していったのでしょうか。
まず、水素製造装置の心臓部となる改質器について、改質効率を高めることに取り組みました。三菱化工機株式会社新事業本部HyGeiaチーム部長代理の内山賢彦さんは、「そこで、S/C比を下げることを目指しました」と言います。
S/C比(Steam per Carbon)とは、メタンなどの原料に含まれる炭素の量(モル数)に対して使われる水蒸気の量の比です。都市ガス原料では、通常S/C比は3.0程度の値で、反応により消費される水蒸気は供給された量の半分程度です。
水素改質では、原料ガスと水を700℃以上の高温にしますが、変成ガスをPSAに供給する前に常温まで冷却する必要があります。
この冷却工程で、ある程度のエネルギー回収は可能ですが、その大部分は大気中に排出されてしまいます。そのため、S/C比が高いと、反応に不要な水蒸気が多くなり、水蒸気を作るエネルギーと冷却による廃熱が増加しエネルギー損失が大きくなってしまいます。
内山さんは、「水の使用量を減らしてS/C比を下げれば、エネルギー効率は高まります。しかし、S/C比を下げすぎると、改質器のなかで炭素の粉末が生まれて装置を詰まらせてしまうのです。トラブル発生を防ぎながら、できるだけS/C比を下げることを目指しました」と説明します。
ここで内山さんたちが着目したのが、改質をするときに使う触媒です。「触媒メーカーから各種のサンプルを入手し、触媒試験設備でさまざまな条件を設定してテストしていきました」(内山さん)
改質触媒の候補には、炭素粉末が発生しにくいとされているルテニウムなどの貴金属系の物質も候補として上がりましたが、より安価に入手可能なニッケル系の触媒で試すことにしました。4,000時間にもわたる長期試験の結果、ニッケル系触媒でも、炭素粉末の発生が抑えられることを確かめることができました。これにより、都市ガス原料ではS/C比を従来の3から2.5以下に下げた装置設計が可能となりました。
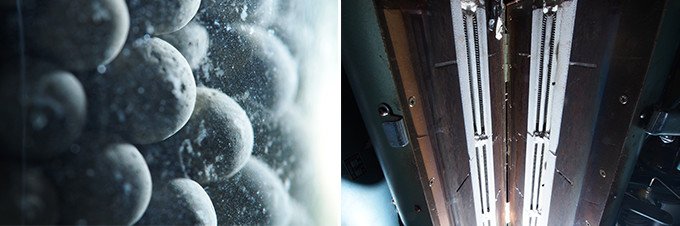
触媒(左)と触媒試験設備(右)
バーナーを内製化し、設計を大幅に変更
改質器についてはもう一つの挑戦がありました。同社はバーナーの内製化を決断したのです。
内山さんとともに水素製造装置の開発に携わってきた、新事業本部HyGeiaチーム部長代理の谷口浩之さんは、「従来装置では、バーナーは購入品であったため、そのまま「HyGeia-A」に採用するには、コスト面で設計の自由度が制限されてしまうという課題がありました。当時、燃焼系の専門家は社内に在籍していませんでしたが、自分たちで開発することを決めました」と振り返ります。
バーナーを自社化できれば、反応器全体の設計を柔軟に変えることもできます。谷口さんは、「燃焼用の配管やバーナーが天井側にあると複雑な構造になります。バーナーを下にもってくると空間に余裕ができ、コンパクト化させることができることに気づいたのです」と説明します。
シミュレーションで試験用の模擬改質器などを使って、空気の流れ、原料の分量、バーナーのノズルの形状などを地道に変えてみて、最適条件を見つけていきました(図7)。
また、従来機で採用していたリジェネバーナーという方式も変更しました。リジェネバーナーは蓄熱体により排熱回収を効率よく行うための方式ですが、バーナー自体が大きく、構造が複雑になるという問題がありました。
加熱器の設置などでリジェネバーナーで実現していた温度に近い燃焼温度を達成できたため、より単純なバーナーの方式を採用することにしました。
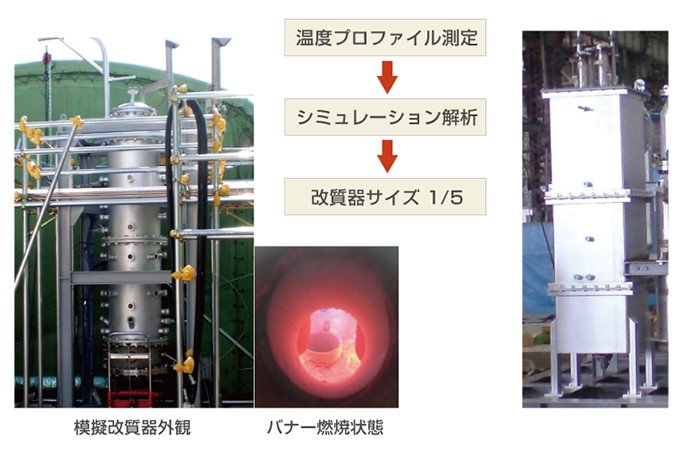
図7 内製化を目指し、バーナーの開発にも取り組んだ(写真提供:三菱化工機株式会社)
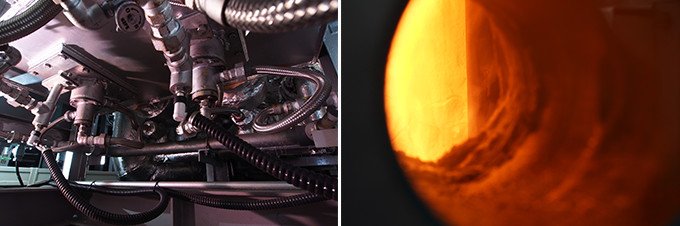
神の倉水素ステーションに設置されたHyGeia-Aのバーナーと(左)、改質器内部(右)
圧力スイング装置に真空方式を採用
圧力スイング吸着装置(PSA)に対しても、効率性向上とコンパクト化を目指しました。水素の純度を確保しつつ、水素製造量を増加させることが水素製造装置の効率向上に重要となります。圧力を高めることで、不純物を吸着し、圧力を戻すことで吸着した不純物を除いていきます(図8)。
「今回の装置では、新たに真空により不純物を取り除く『真空再生方式』を採用しました」と、内山さんは説明します。
従来は、脱着工程の圧力を大気圧程度とする「常圧再生方式」を採用していましたが、「真空再生方式」で、様々な利点が得られるようになったと内山さんは言います。
「吸着剤の量を減らし、吸着塔のサイズを小さくすることもできます。また、不純物を洗い流すために水素を使いますが、真空方式を使うことで洗い流しのために使う水素の量を減らすこともできます」(内山さん)
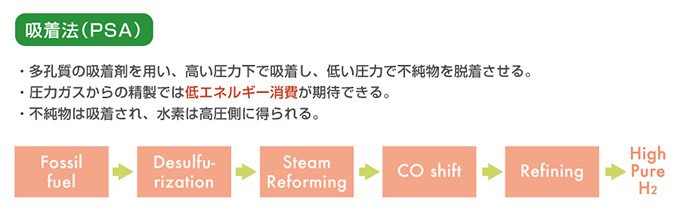
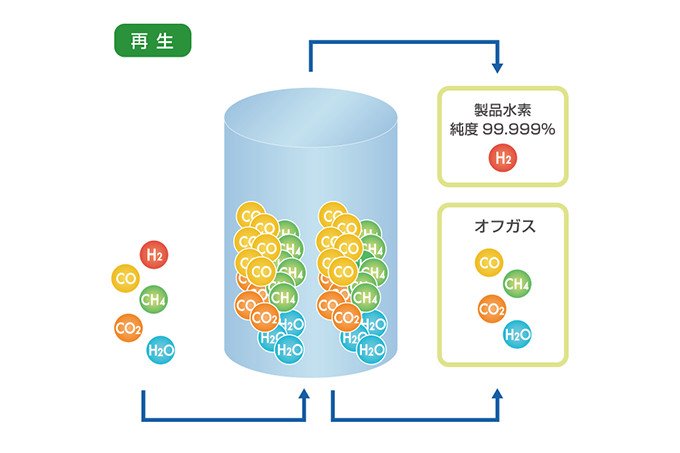
図8 PSAの精製の仕組み(上)と原理(下)
さらに、PSAの小型化のため、運転サイクルを短くすることで吸着塔のサイズを小さくすることとしました。しかし、運転サイクルを短くすることは、「使い方としては過酷なもの」(谷口さん)になります。そのため、PSAの設計には詳細なデータが必要でした。
「小型の試験装置でデータを取得しようとしましたが、なかなかうまくいきませんでした。ある程度のデータを取得し、あとは塔の切り替えのタイミングなどの実際の運転方法を試作機で詰めていきました」(谷口さん)
こうして、改質器とPSAそれぞれに改善を重ねていって、プロジェクトで課せられた目標を実現していったのです。
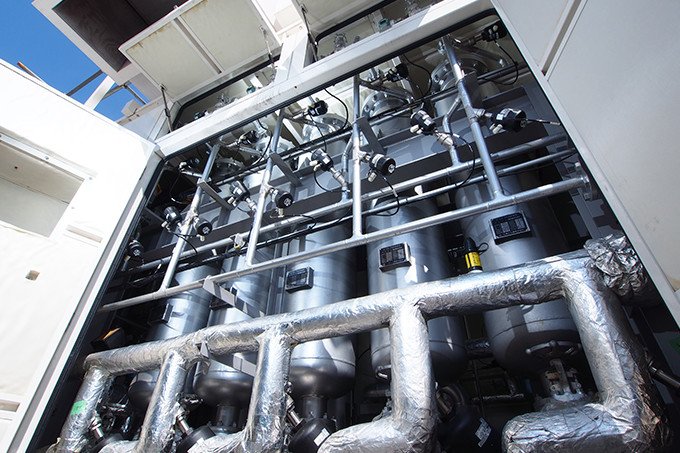
効率化とコンパクト化を実現したPSA
FOR THE FUTURE 開発のいま、そして未来
水素ステーションが身近な街の風景になる日のために
水素ステーションの普及に向け、こうして、効率化、低価格化、コンパクト化を目指して研究開発を進められた「HyGeia-A」は、2011年度より、HySUTが受託したNEDO「地域水素供給インフラ技術・社会実証」の一環として、東京ガス株式会社が運営する「千住水素ステーション(東京都荒川区)JとJX日鉱日石エネルギー株式会社が運営する「神の倉水素ステーション(愛知県名古屋市)」にそれぞれ設置されています。
2015年に水素ステーション100カ所程度の普及が目標として掲げられており、全国各地で「HyGeia-A」が使われる機会が増えていくことが見込まれています。
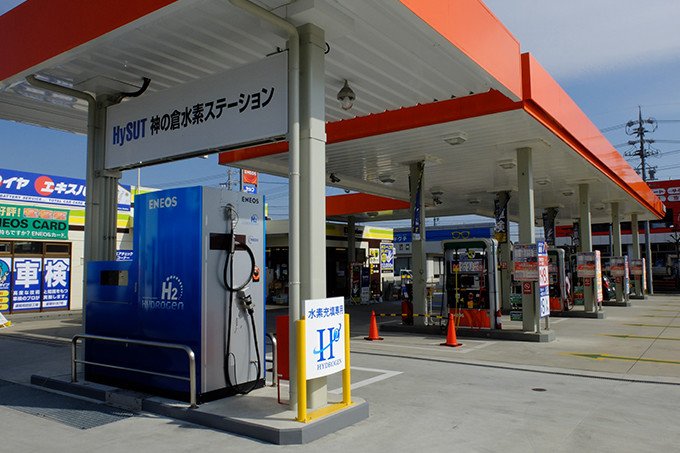
神の倉水素ステーション
2020年、2030年の水素社会へ
燃料電池自動車への水素供給は、これまでにないエネルギー供給方式です。これを全国で普及させるには、国やNEDOなどの機関が主導する計画と、それに応える企業の挑戦が必要です。
谷口さんは、「NEDOがロードマップで目標を示すなかで、研究成果が社会実証につながっていくことができるので、研究開発はとても進めやすいものとなっています。さらに、NEDOプロジェクトに参画することで、三菱化工機の存在が広く認知されるようになりました」と言います。
NEDOが示している水素の製造や供給などに関わるロードマップでは、さらに2020年ごろの「インフラ技術課題を解決し、商用ステーションの整備」や、2030年ごろの「走行距離でガソリン等価となる水素供給コストの達成」が掲げられています。これらを実現していくため、「HyGeia-A」の上市まで蓄積されてきた技術の進歩の道は、さらに続いていくことになりそうです。
「水素の価格が燃料市場のなかで他の既製燃料と見合わないと、水素エネルギーの時代は実現されません。ロードマップに書かれているのは厳しい目標ではありますが、それに挑んでいく必要性を感じています」と内山さんは話します。
開発者の横顔
水素エネルギーの時代を切り拓く
水素製造装置の製品化に大きな喜びを感じています
新事業本部HyGeiaチーム部長代理の内山賢彦さんは、大学時代に粉体工学を専攻。入社後は異分野の超臨界水の研究に携わってきました。その後、2000年ごろから、燃料電池関連分野での研究開発に移っていきました。水素製造装置の開発では、各技術の設計をとりまとめるマネージャー的な役割を担っています。
「燃料電池システムの開発にも携わったこともありますが、そのときは結局、製品化までには至ることができませんでした。しかし、今回の水素製造装置では、開発、試作と進み、製品化、商用機まで至ることができました。これには大きな喜びを感じています」
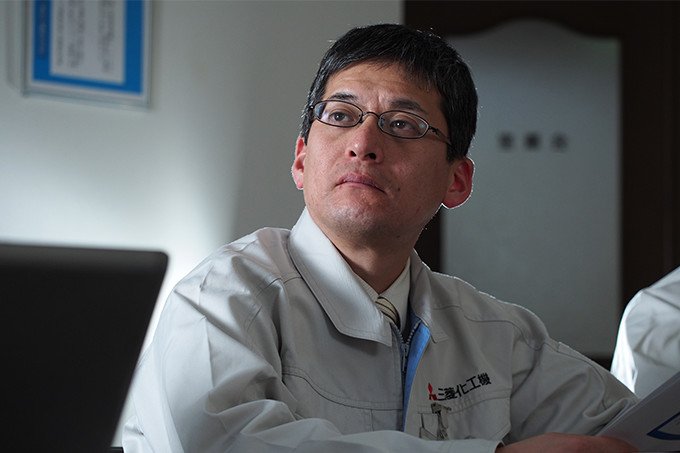
内山さん
技術を積み上げて、コストダウンに向けた挑戦を続けます
同じく新事業本部HyGeiaチーム部長代理として、水素製造装置の開発に携わってきたのが谷口浩之さんです。水素ステーション関連のアフターサービスなども行い、現場での使われ方などについて、豊富な知見を蓄積してきました。
「コストダウンに向けた挑戦はまだまだ続きます。水素製造装置は構成ユニットがとても多いものです。これをやったら一気に効率がよくなるといった、決定的な方策があるわけではありません。ひとつひとつの技術を積み上げて、目標に達成していくことが必要だと思っています」
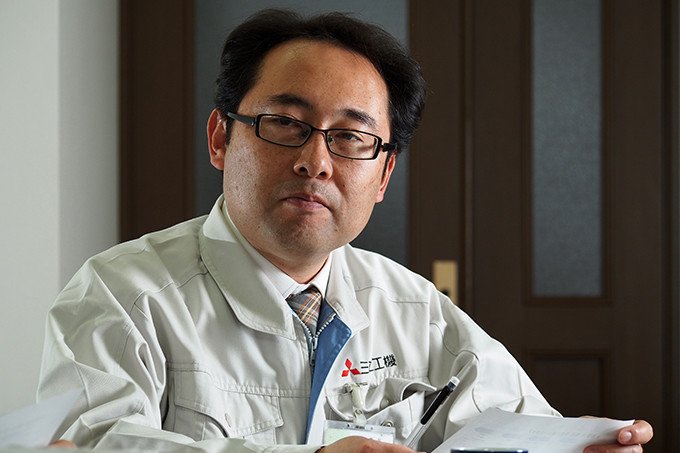
谷口さん
なるほど基礎知識
水素をつくる
水素分子(H2)は地球上に天然には存在しないため、燃料として使う場合には、人工的に水素分子をつくる必要があります。
水素分子の製造には、製油所・製鉄所で副産物として水素が製造される「副生水素」、天然ガスや石油といった化石燃料を材料に、化学変化を起こして水素分子を生成する「化石燃料改質法」、電気により水(H2O)を電気エネルギーにより、水素分子(H2 )と酸素分子(O2 )に分解することで水素分子を生成する「水電解法」、熱エネルギーにより水を分解する「熱化学水素製造法(熱分解法)」、光があたることで触媒機能を発現する光触媒を用いて、太陽光のエネルギーにより水を分解する手法など、複数の製造方法が存在します(図A)。
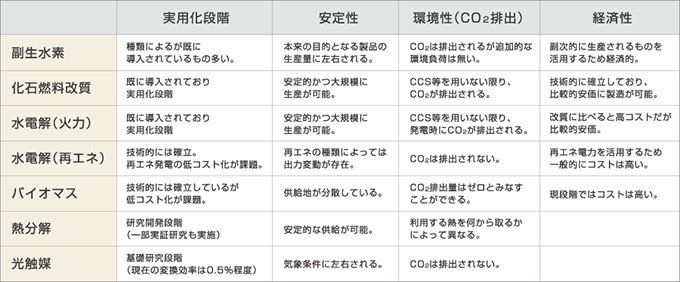
図A 水素製造方法の比較(出典:資源エネルギー庁 燃料電池推進室 「水素・燃料電池について」第1回水素・燃料電池戦略協議会(2013年12月19日)【参考資料 [3]】)
現在、水素製造手法として主流であるのが、「短時間で、大量に、安価に」製造可能な「化石燃料改質法」です。ただし、水素製造過程で二酸化炭素が排出されることが課題とされています。そのため、放出される二酸化炭素を人工的に地中・地下に貯蔵するCCS(Carbon dioxide Capture and Storage)を組み合わせることで、大気中に二酸化炭素を排出することなく、水素を製造する取り組みも行われております。
また、最もクリーンな水素製造方法としては、太陽熱・太陽光・風力など、発電時に二酸化炭素を生成しない再生可能エネルギーにより水を電気分解する手法も注目を集めております。ただし、現状では水素製造コストが高く、経済性の観点での課題克服が求められております。
なお、「副生水素」については、既存のプラントで大量に生成できるため経済性に優れる一方で、多くの副生水素が所内プロセスで消費されており、水素製造量が目的となる製品の生産量に左右されるなどのデメリットがあります。
このように、水素が社会の基盤エネルギーとして広く普及する「水素社会」を実現するためには、水素の製造方法についても多くの課題をクリアしていく必要があります。
NEDOの役割
「水素製造・輸送・貯蔵システム等技術開発」
このプロジェクトがはじまったのは?
資源に乏しい我が国が、将来にわたり持続的発展を達成するためには、革新的なエネルギー技術の開発、導入・普及によって、各国に先んじて次世代型のエネルギー利用社会の構築に取り組んでいくことが不可欠です。本プロジェクトで対象としている水素技術は、上記目的達成に向けたキーテクノロジーとして、その実用化への期待が高く、産官学が一体となった取り組みが行われています。
本プロジェクトは、来るべき水素エネルギー普及のための燃料電池自動車及び水素供給インフラ市場立上げ(2015年頃を想定)に向けて、水素製造・輸送・貯蔵・充填に関する低コストかつ耐久性に優れた機器及びシステムの技術開発、要素技術開発、次世代技術開発及びシナリオ策定、フィージビリティスタディ等を行い、水素エネルギーの導入・普及に必要な一連の機器及びシステムに関する技術を確立することを目的として実施されました。
2011年1月には、自動車メーカー及び水素供給事業者13社が燃料電池自動車の国内市場導入に向けて共同で取り組むことに合意し、2015年に自動車会社が燃料電池自動車量産車を販売すること、水素供給事業者が4大都市圏を中心として必要な規模(100ヵ所程度)の水素ステーションを先行的に整備することを目指する共同声明が発表されています。
プロジェクトのねらいは?
2010年度末を目途に、水素エネルギーの導入・普及に必要な低コスト機器及びシステムを試作開発し、その試作開発結果を基に2012年度までに耐久性評価等を行うことを目的としました。三菱化工機株式会社は、本プロジェクトの内、要素技術開発として、「水素製造装置の高性能化・低コスト化・コンパクト化に関する研究開発」に参画し、首都圏等の狭小エリアへの設置を可能とする小型・高効率・低コストな水素製造装置の仕様明確化と、その実現に向けた開発に取り組みました。開発された水素製造装置は、NEDO「地域水素供給インフラ技術・社会実証(2011年度~2013年度)」内において、ガソリンスタンド併設型水素ステーション等に設置され、実証研究が行われました。
NEDOの役割は?
NEDOは、技術検討委員会等を設置することで、当該分野に関する外部有識者の意見を本プロジェクト運営管理に反映させる他、プロジェクトに参画した産学官関係機関及び研究者の間で、その実施内容、進捗状況などを報告、共有化を図るために報告会等の開催を行いました。また、「水素先端科学基盤研究事業」「水素貯蔵材料先端基盤研究事業」「燃料電池等システム実証研究」「地域水素供給インフラ技術・社会実証」等の関連する他事業との間での、データ及び成果の共有化や評価・試験に関する共同研究などを実施することで、当該分野における効率的なプロジェクト運営に取り組みました。
関連プロジェクト
お読みいただきありがとうございました。
ぜひともアンケートにお答えいただき、
お読みいただいた感想をお聞かせください。
いただいた感想は、
今後の連載の参考とさせていただきます。