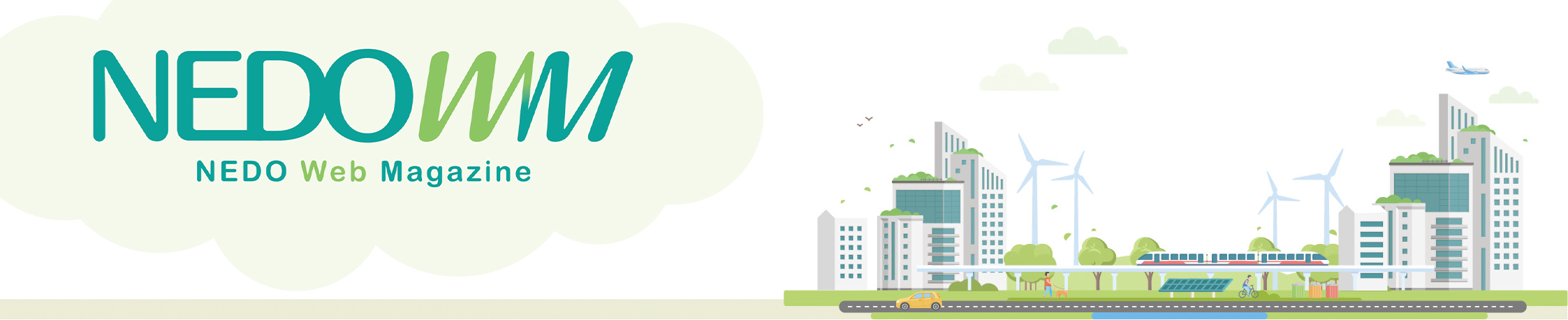
CONTENTS
INTRODUCTION
2工場間の排熱共有による省エネルギー量原油換算10,700kL/年、
CO2削減効果28,000t/年
BEGINNING
単一工場での省エネから複数工場間による省エネへ
BREAKTHROUGH
地道なデータ調査が高精度な解析実現のカギ
FOR THE FUTURE
タイの工業地帯でのNEDOプロジェクトが進行中
FACE
あらゆる産業に共通するユーティリティ部門から省エネ化
INTRODUCTION 概要
2工場間の排熱共有による省エネルギー量
原油換算10,700kL/年、CO2削減効果28,000t/年
省エネルギー先進国である日本は、省エネルギーに繋がる要素技術開発においても世界トップレベルにあります。なかでも工業分野での省エネルギー対策は進んでおり、とくに、工業地域(コンビナート)を形成する製油所や化学工場などでは、早くから各工場内での省エネ対策が進められていました。そのため、もうこれ以上の省エネルギー化は既存技術の適用だけでは望めない状況にまでなってきています。
プラントエンジニアリング企業の千代田化工建設株式会社では、単一工場ごとの省エネルギー化は限界に達している一方で、異業種の工場が隣接するコンビナート内では、工場によって利用する熱の温度帯が異なることに着目し、異業種工場間で熱融通ができれば、さらなる省エネルギーも可能と考えました。
そこで、千代田化工建設では、NEDO「エネルギー使用合理化技術戦略的開発」などに参画し、単一の工場やプラント等で物質及び熱の流れを解析し最適化を行う解析ツール「ピンチテクノロジー」を基に、コンビナートを形成する複数工場間での物質及び熱エネルギー共有解析に拡大適用する独自技術「エリアワイドピンチテクノロジー」の開発に取り組み、実コンビナートでの実証試験及び大幅な省エネルギー化に成功しました。現在、開発された「エリアワイドピンチテクノロジー」は、国内4カ所(千葉、鹿島、水島、大分)のコンビナートで適用されており、さらに、2011年度からはNEDO「国際エネルギー消費効率化等技術・システム実証事業」の一環としてタイ王国のマプタプット工業団地へと海外展開されるなど、国内外のコンビナートにおける省エネルギーソリューション技術として大きな期待が寄せられています。
BIGINNING 開発への道
単一工場での省エネから複数工場間による省エネへ
現在、日本には10カ所のコンビナートがあり、製油所、化学工場、硝子工場、発電所、食品工場、機械工場などが操業しています。これらの工場では、「エネルギーの使用の合理化に関する法律(省エネ法)」で規定されている「エネルギー原単位を年平均1%低減する」という中長期の省エネ目標値に基づいて、エネルギー使用量および温室効果ガス(CO2)排出削減のために様々な取り組みを行っています。
とはいえ、数々の既存技術を用いても、単一工場での省エネ化には限界があります。省エネ法で規定する「年1%低減」を達成することも難しくなっており、これ以上の省エネ化を推進すればコスト的な問題が生じてしまいます。
そこで、プラントエンジニアリング企業の千代田化工建設株式会社が目をつけたのが、コンビナートの複数工場間で排熱を融通し合うという方法です。そもそもコンビナートは、原料や燃料などを工場間で供給し合うことを考えて集中的に配置された工業地域ですから、排熱共有も非現実的なことではありません。
しかし実際には、コンビナートでも操業は工場単位で行われていて、ほかの工場とのプロセスやエネルギーシステムの相互融通は行われていませんでした。
熱回収ポイントを解析・設計する「ピンチテクノロジー」
複数工場連携による省エネを実現するために千代田化工建設が活用したのは、単一工場向けに活用されてきた「ピンチテクノロジー」です。基本となる理論は1970年代後半にわが国および英国で提案された熱回収システムの熱利用解析技術です。これは、熱回収量が最大となるように「解析図上で熱をピンチする(つまむ)」ことから名付けられました。千代田化工建設はピンチテクノロジーの実用化を進め、今までに国内外約160件のプラントや工場で導入された実績があります(表1)。
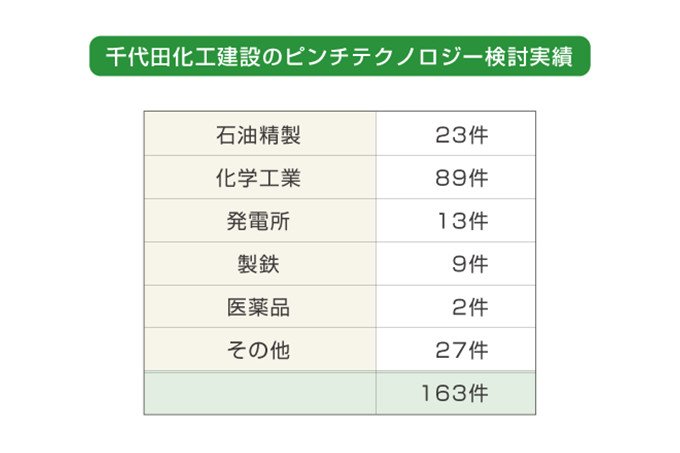
表1 千代田化工建設のピンチテクノロジー検討実績
石油・化学系工場の場合、原料の反応・分離を行うプラントを組み合わせた「プロセスシステム」と、電気や蒸気を供給するためのガスタービンやボイラーなどといった「エネルギーシステム」によって構成されています。
このうち工場のメインである生産工程は原料から付加価値の高い製品を作り出す「プロセスシステム」ですが、工場によって使用する原料や反応条件などが異なるため、複数工場間で融通することはできません。対して、熱や電気といったどの工場でも使っている「エネルギーシステム」ならば、お互いに融通することが可能です。(図1)
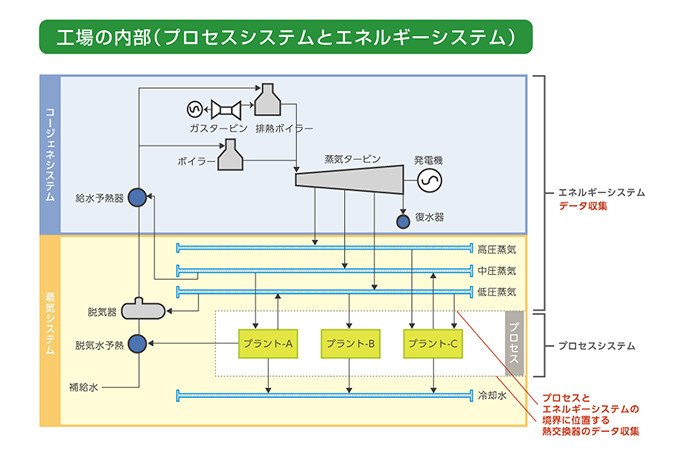
図1 どの工場でも共通している「エネルギーシステム」(水色の部分)ならば工場間での熱共有が可能になる
ピンチテクノロジーがターゲットとしてきたのは、この「エネルギーシステム」です。コージェネレーションシステムを導入することで排熱が利用されているとはいえ、プロセスとエネルギーシステムの境界にある熱交換器(温めるスチームヒーター、冷やすエアフィンクーラーなど)により、かなりの熱が未利用のまま捨てられてしまっています。この無駄をなくして熱回収するシステムを構築するための解析技術が「ピンチテクノロジー」なのです。
第1世代といわれる1970年代後半からのピンチテクノロジーは、単一工場やプラント設備のプロセスシステムを対象としていましたが、90年代に誕生した第2世代では工場内のいくつものプロセスに熱電を供給するエネルギーシステムを対象とする省エネ手法として活用できるものです。
今回のNEDOプロジェクトによる「エリアワイドピンチテクノロジー」は第2世代のさらなる拡大版という位置づけで、複数の工場を組み合わせ、コンビナート全体でのエネルギー使用の最適化解析が可能になりました。「エリアワイドピンチテクノロジー」では、文字通り、広範囲で省エネルギー余地を解析し、エネルギー使用最適化のための改善案を検討します。
具体的な流れとしては、まずそれぞれの工場に対してピンチテクノロジー解析を行い、それらを全てまとめ上げて一大仮想工場を作り上げます。そして、その仮想工場に対して再度ピンチテクノロジー解析を行い、全体での省エネ診断を行います(図2)。
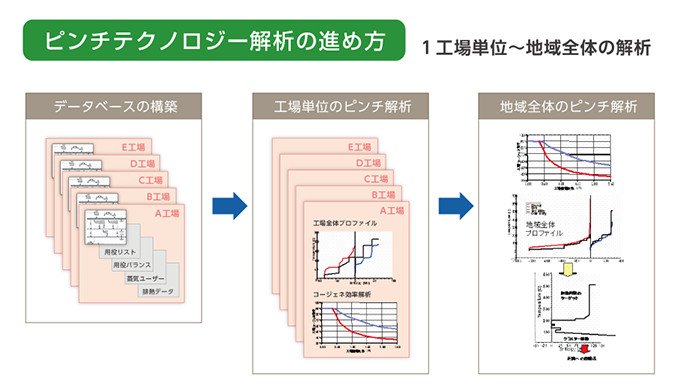
図2 エリアワイドピンチテクノロジー解析の流れ
「熱プロファイル解析」と「R-曲線解析」で省エネ余地を可視化
基盤技術であるピンチテクノロジーでは、どの温度帯の熱をどのように融通し合うかを判断するために、最初にエネルギーシステム全体のデータを収集します。タービンやボイラー、発電機などによるコージェネレーションシステム、低圧・中圧・高圧と圧力別の蒸気システム、さらにプロセスとエネルギーシステムの境界にある熱交換器と、それぞれがどのような温度帯を使い、捨ててしまっているかを解析します。
解析手法として用いるのは、「熱プロファイル(SSSP解析)」と「R-曲線解析」です。工場内には様々な温度帯の流体(蒸気や温水/冷水)が使われていますが、そのままでは全体として把握できないため、異なる温度帯の流体をビジュアルにより一本化したのが図3に示した「熱プロファイル解析図」です。黒い実線と点線の落差が大きいほど、省エネルギーの余地が大きいことを意味しています。
例えば、図3の左側を見ると、破線では100℃から20℃まで熱が捨てられていることになりますが、実線のように、110℃付近の熱を工場間で融通する(左側のグラフから右側のグラフに熱を供給する)ことや、90℃付近の熱を温水として回収して融通する(左側のグラフから右側のグラフに熱を供給する)ことが可能であることが明らかとなります。つまり、「熱プロファイル解析」を行うことで、回収・利用できる分がひと目でわかることになります。
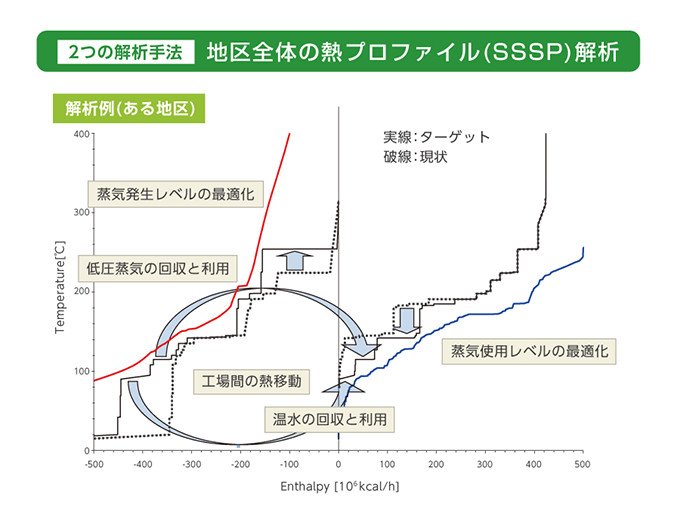
図3 熱プロファイル解析の例
次に、「R-曲線解析」は、エネルギーシステムの省エネの余地を把握するための解析手法で、その工場の言わば「省エネ偏差値」がわかります(図4)。
工場の使用電力(購入電力と自家発電)とコージェネレーションによる熱供給(蒸気)から、工場における熱電比を算出します(図4 破線)。さらに、発電に使用する燃料から統合エネルギー効率を算出し、ボイラーとタービンを導入した場合(図4 赤線)、さらにガスタービン複合システムを導入した場合(図4 青線)などの理想のエネルギー効率を割り出し、それに対して現状のエネルギー効率がどの程度であるかを算出します。
たとえば理想のエネルギー効率に対して現状の統合エネルギー効率が低すぎるというのであれば、熱利用を増やすことで熱電比を下げ(図4グラフで左方向に移動し)統合エネルギー効率を高めるか、もしくは、新たにガスタービン複合システムを導入することで(図4グラフで上方向に移動し)統合エネルギー効率を上げるなど、現状を分析したうえで、今後どのような対策が可能かといったソリューション提案が可能となります。

図4 工場の"省エネ偏差値"がわかる「R-曲線解析」
千葉コンビナートの23工場で調査実施
「これまでに多くのコンビナートの環境保全に取り組んできた中で、ある温度帯を捨てている工場がある一方で、わざわざ電力を使って、その温度帯を作り出している工場があることはよく聞く話でした。しかし、それぞれの会社は他社のことを知りませんから、議論は各社のなかで止まってしまっていました」と、話すのは千代田化工建設でプロジェクトリーダーを務めた、エネルギーインフラプランニングユニットの松田一夫さん。
松田さんは続けて、「しかも、各社とも単独工場での省エネ対策をやりつくし、困り果てていました。その点、当社であればその全体を俯瞰し、データを構造化することが可能だと気づき、ピンチテクノロジーを使い、コンビナート全体での省エネを実現しようと考えました」と説明します。
千代田化工建設では、2000年からのNEDO「エネルギー使用合理化技術実用化開発事業/ピンチテクノロジーによる工場地域のエネルギー共有技術の研究開発」で、千葉コンビナートでの調査を開始しました。千葉コンビナートは、3つの石油化学コンビナートが連なっていて、製油所4、化学工場18、その他工場1の計23工場が集まっています(解析当時)。これらの工場はパイプラインで繋がれていて、石油精製から各種化学製品の生産までを連携して行います(図5)。
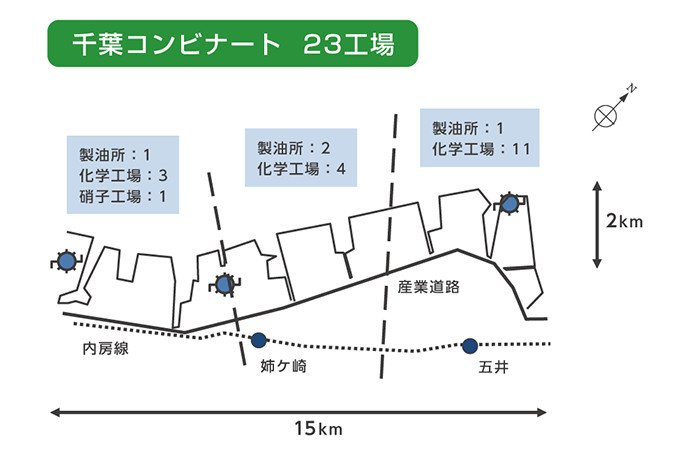
図5 調査研究を行った千葉コンビナートは約5kmごとに三つの地区に区切り検討を進めた。結果的に熱共有配管の新設はその5km程度が経済性の観点から適切と判った。
単一工場での省エネ化が限界に達している中、「コンビナート全体で省エネ」という提案に対して多数の工場が協力を承諾してくれました。当時、燃料費が高騰していたことも同社にとっては追い風でした。1社1社説明と提案を行う中、自ら周辺の他社工場に声を掛けてくれた工場もあったほどです。
その背景として松田さんは、「それほど化学プラントにおけるピンチテクノロジーへの認知度や信頼度、そして期待度が高かったのだと思います」と話します。
最初に取り組んだ省エネ余地解析フェーズでは、千葉コンビナートの23工場全てに対して、エネルギーシステム、熱交換器、蒸気システムなどの運転状況などのデータを提供してもらい、工場ごとにピンチテクノロジー解析を行った上で、三つの地域ごとに統合して省エネ余地を導き出しました。
この解析により、千葉コンビナート全体での省エネ余地(理論値)が原油にして年間65万kl相当であることが判明しました。製油所では120~150℃の排熱が利用されずに捨てられている一方で、化学工場では100℃程度の熱を求めていることもわかりました。この部分を融通すれば、13万klの省エネが可能になる試算です。
こうした解析結果を受けて、松田さんらはいくつかの改善案を作成しました。改善にあたっては数億~数十億円単位の投資が必要になりますが、5年以内で回収できることを目安に、費用対効果の上でも現実的な提案を行いました。
さらに、千葉コンビナートでの基盤調査の後、水島(35工場)、鹿島(30工場)、宇部(3工場)、大分(15工場)のコンビナートでも、NEDOの調査事業が行われました。中でも、規模が大きく設備の古い水島コンビナートの省エネ余地は大きく、省エネ理論値は121万kl、熱共有することでの省エネ理論値は21万klにものぼることがわかりました(表2)。
「メインの製造ラインであるプロセスシステムについては優先的に設備投資がなされる反面、エネルギーシステムについては後回しになりがちで、設備が老朽化していることも少なくありません。しかし、老朽化しているからこそ改善の余地が多いともいえます」と松田さんは説明します。
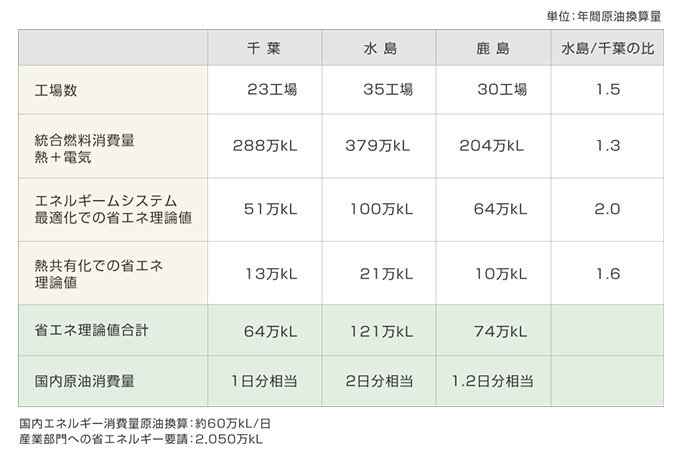
表2 千葉、水島、鹿島で行った各コンビナートの省エネルギー理論値。この三つのコンビナートだけで国内原油消費量の4日分に相当する
2工場による省エネ共同事業で省エネ実現
2003年には、「エネルギー使用合理化技術戦略的開発/エネルギー使用合理化技術実証研究/コンビナート低位熱エネルギー統合回収技術の開発」により、千葉コンビナートの富士石油株式会社と住友化学株式会社との共同事業がスタートしました。富士石油袖ケ浦製油所では、石油精製の過程で生じる80~150℃の熱を排熱として捨てていました。一方の住友化学千葉工場では、重油などを燃やして蒸気を作っていました。
そこで、富士石油のクーラーで廃棄していた熱を約1.5km離れた住友化学まで繋いだパイプで送ります。住友化学ではこの熱を使ってボイラーの補給水を加熱し、ボイラーの燃料を削減します。(図6)。
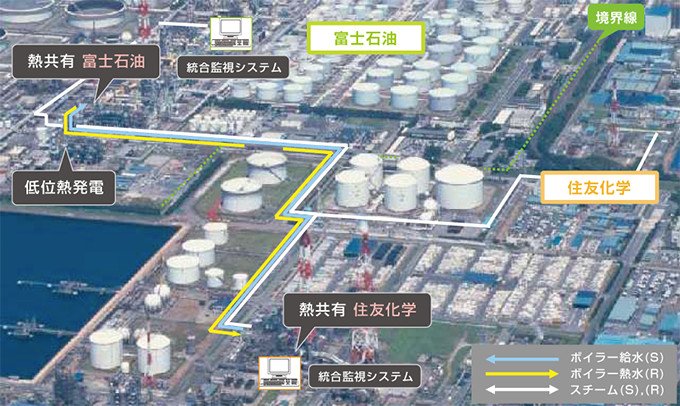
図6 富士石油と住友化学との共同事業。配管は片道約1.5km
富士石油では、従来、蒸留塔の塔頂ガス(120℃程度)を、エアフィンクーラーで処理していましたが、その低温排熱を熱源として利用する、世界で初めてカリーナサイクルを採用した低位発電システムによる蒸留塔を設置しました。このシステムでは、工場の排熱を利用して4,000kWの発電を行うことができます。
また、熱共有を行うそれぞれの工場の最適運転を行うと同時に、連携による最適化を行うための「統合エネルギー監視システム」を独自に開発。安全かつ高効率に熱共有を行うためのシステムとして、特許も取得しました。
これによる省エネルギー量は、原油換算10,700kL/年、CO2削減効果は28,000t/年にのぼり、住友化学では年間数億円の燃料費を節約できることになります(削減費用の一部は富士石油に還元)(図7)。
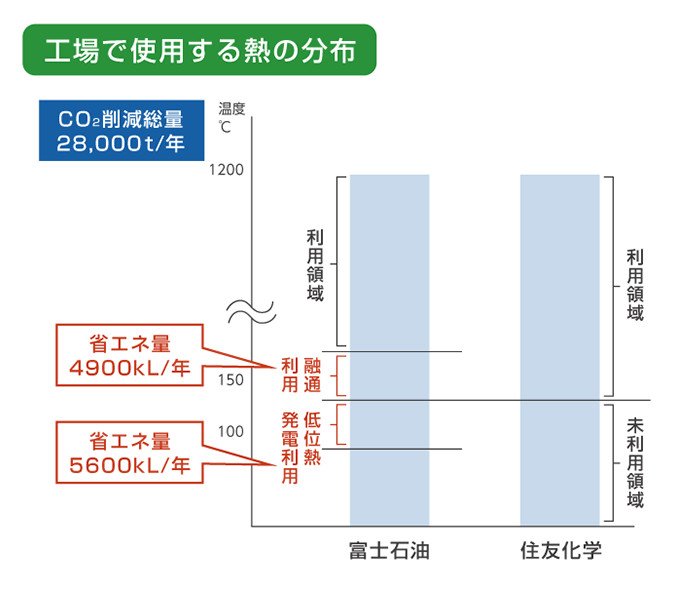
図7 富士石油から出ていた200℃以下の排熱のうち、高温部分は住友化学と熱共有し、120℃以下の低位熱については発電で利用する
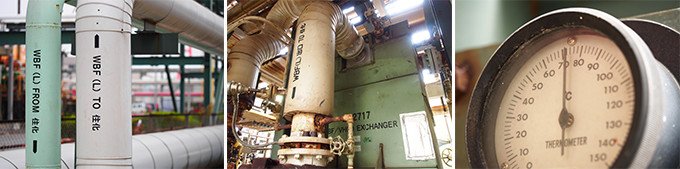
(左)富士石油と住友化学を結ぶ配管(中央)富士石油プラント内の熱交換器(右)住友化学から受け取った排水熱の温度ゲージ
BREAKTHROUGH プロジェクトの突破口
地道なデータ調査が高精度な解析実現のカギ
個別の工場を対象とした「ピンチテクノロジー」を、複数工場による熱共有で利用できるよう拡張したのが「エリアワイドピンチテクノロジー」です。解析は、データの収集、エネルギーシステムフロー図の作成、熱プロファイル解析、R-曲線解析という4つの作業で構成されますが、個別工場→複数工場→一大仮想工場というような新たなエネルギーシステムフロー図を作成することで「地域全体での解析」を可能にしています(図8)。
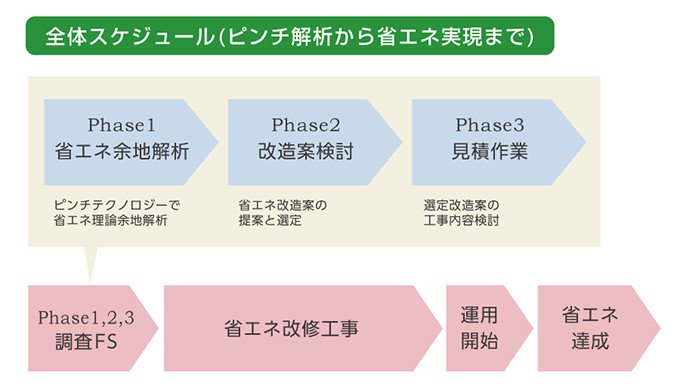
図8 ピンチ解析から省エネ実現までのフロー
なかでもデータの収集については、個別工場を対象としてピンチテクノロジーよりもかなりスケールアップする必要がありました。各工場の実態を把握した上で省エネ診断を行うのですから、最初のデータ収集がかなり重要であることは自明です。
個別工場だけを対象としているならば、工場によってデータの体裁が若干異なっていたとしても、最終的な省エネ診断にはそれほど影響はありません。ところが、複数の工場を対象として等しく解析するためには、整理・標準化されたデータであることが必須です。
そこで、データ収集のために統一・標準化したデータ調査票(アンケートシートと名付けた)を作成。データを管理するソフト(Excelで作成)には、漏れがあった場合などにアラートを出すなど、オートチェック機能を搭載しています。
工場側は膨大な量のアンケートに答えなければならず、具体的な数字を集めながらシートに記入していくだけで2週間程度はかかります。アンケートシート作成のためのマニュアルの作成や説明会なども開催しましたが、中には回答に悩む質問項目などもあり、そうした疑問に一つ一つ対応しながらデータをまとめていきました。
「私たちとしても大変手間がかかる作業でしたが、マニュアルの作り方などは企業からのフィードバックを受けて少しずつブラッシュアップしてきました。実は、このフェーズこそノウハウの塊で、当社の知財担当者から『どうしてここの部分の特許を取っておかなかった』と言われたほどです」と松田さんは話します。
高い機密性を保ちデータ最適化を行う独自システムを開発
富士石油と住友化学による共同事業を機に、複数の企業のデータを扱うためのシステム「統合エネルギー監視システム」も独自に開発しています。
複数企業間の熱共有システムを管理する上で、最大の問題となるのは機密性です。会社が違っても扱っている製品が同じ製油所は比較的情報がオープンであるのに対して、化学系工場は情報の扱いが大変に慎重で、ほとんどの情報がオープンにされていません。製油所との2工場間とはいえ、情報の機密性が担保できなければ、そもそも今回の共同事業にも参加しなかったはずです。
当初は1階層のネットワークで情報のやりとりをしようと考えていましたが、それではセキュリティなど諸々の問題が生じます。1階層のみのデメリットはほかにもあり、たとえばA社のデータを改変したとき、変更のないB社の分まで含めて全て直さなければいけなくなります。
また、データ解析では各社400~500のデータが必要になりますが、それほど膨大な量のデータ全てに対して何重ものセキュリティを施したうえで統合しようとすればかなりシステムが重くなってしまいます。
そこで最終的に構築したのが、2階層構造による「統合エネルギー監視システム」です。A社、B社それぞれの400のデータは各社レベル(第1階層)で解析を行い、連携する上で必要な温度、流量、コストなど最低限のいくつかのデータ(共有パラメータ)だけを統合システム(第2階層)にアップするようにしました。
しかも、生データ(実数)ではなく、前回計算値との差分値だけを送ります。こうすれば、工場の生産量などを一方の会社に知られることはなく、かつホストコンピュータの負担を大幅に軽減することができます。
クラウド化などを含め、データの持ち方についてはまだ改善の余地がありますが、このシステムで特許を取得。今後、広く展開できる可能性が持っています(図9)。
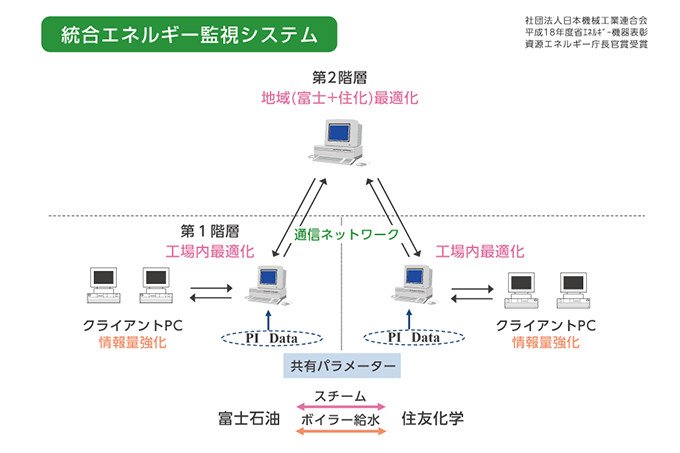
図9 第1階層では各工場内で最適化を行い、第2階層では連携する情報(パラメータ)のみやりとりすることで、各社の機密情報への対応も可能とした。
世界で初めてカリーナサイクルを実用化した低位熱発電システム
もうひとつ、個別工場から複数工場化したことで新たに発生したのが、80℃~200℃程度の"低位熱"の利用です。
低位熱の中でも、120℃以上の高温の部分は熱として融通します。熱は熱として使うのがもっとも効率がいいからです。それでも余った低温な熱を発電に利用します。そのときの発電方法として、今回新たに開発したのが「低位熱発電システム」です。
このシステムは、1985年に米国の科学者カリーナ博士によって考案された「カリーナサイクル」を製油所の分野において世界で初めて実用化したものです。蒸発器、タービン、濃縮期、作動流体ポンプ、セパレーター、再生器、減圧弁、吸収器によって構成されたサイクルで、アンモニアと水の混合媒体を使うことが最大の特徴です。
従来の発電方法(ランキンサイクル)では、ボイラからのスチームでタービンを動かし、水に戻ったらまた蒸気にします。低位熱を利用する場合では、作動流体にアンモニア純物質を使います。
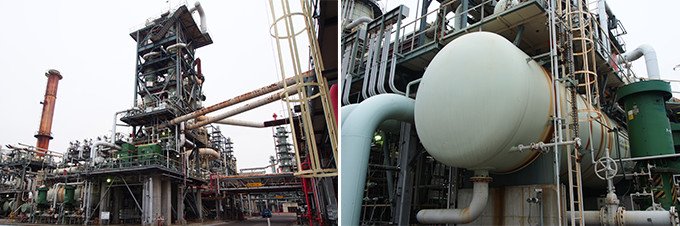
(左)低位熱発電システム(右)作動流体に使用するアンモニア貯蔵槽
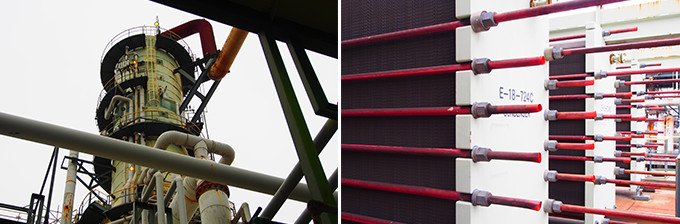
(左)登頂部の蒸発器 (右)凝縮器
それよりもさらに熱効率を高めるのがカリーナサイクルで、作動流体に高濃度アンモニア水(アンモニア90%~95%)を使います。水よりも沸点の低いアンモニア(沸点=-33℃)は、水よりも低温での熱利用が可能になります。
また、混合媒体は純粋物質のように一定温度で蒸発するのではなく、水蒸気の蒸発が始まるまで連続的に温度が上昇していくため、その分仕事への変換量が大きくなります。同様に、凝縮する際も連続的に温度が下がるので、仕事への変換量が大きくなります。
蒸発したアンモニアガス中に混入した水の水滴が多いと、その水滴がタービンのブレードを摩耗させやすくなります。そこで、タービンの摩耗を軽減させるために、余った蒸気を利用したスーパーヒーターを導入し、アンモニアガス中の水滴を減らすとともにアンモニアガス温度を上げて発電量の増加を図ります。これにより余った蒸気を有効利用しつつ、発電量・発電効率ともに高めることが可能になります。
また、一般に高温側流体と低温側流体の温度差が大きいほど熱交換器の伝熱面積(サイズ)が小さくて済むのですが、低位熱発電システムの場合、高温と低温での温度差が小さいため、熱交換器の伝熱面積がかなり大きくなってしまうという課題があります。そこで今回は、できるかぎり設置スペースをコンパクトにするため、凝縮器ではプレート型熱交換器を用いました。「このケースの場合は、低温の熱が余ったのでカリーナサイクルを採用しましたが、高温ならば従来サイクルのほうが高効率です。どのサイクルを使うかはあくまでも対象となる工場排熱の温度条件によって決まります」(松田さん)
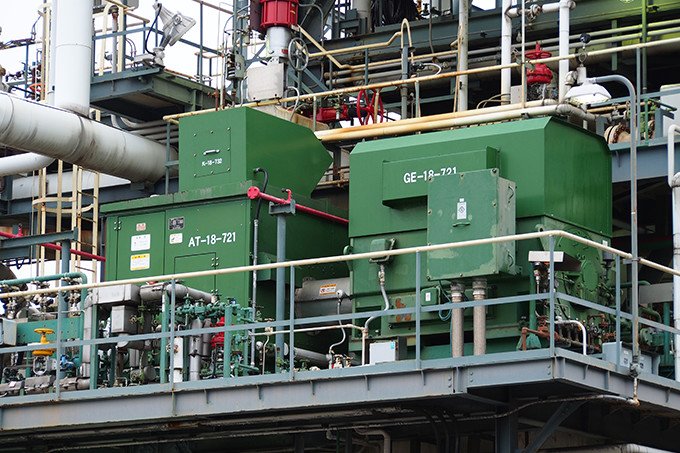
アンモニアタービン
FOR THE FUTURE 開発のいま、そして未来
タイの工業地帯でのNEDOプロジェクトが進行中
千葉コンビナートでの調査研究から富士石油と住友化学による共同事業を経て確立された「エリアワイドピンチテクノロジー」は、2007年に社団法人日本機械工業連合会による第27回優秀省エネルギー機器表彰の「資源エネルギー庁長官賞」を受賞しました。海外からの注目も高まっています。
2011年からは、タイ工業省(MOI)と連携したNEDO「国際エネルギー消費効率化等技術・システム実証事業/基礎事業/タイ工業団地のピンチテクノロジー等の工場間エネルギー利用解析による省エネ診断事業」がスタート。マプタプット省の15工場を対象に、省エネ余地調査、実施計画の策定を行い、個別企業への具体案提示を行うフェーズまで到達しています。
「タイのプロジェクトでは、日本以上にデータ収集が大変で、省エネ余地解析からコンセプト案の提案まで約2年もかかりました。しかし、今後は海外展開がメインになるのは明らかです。東南アジアや中近東からも問い合わせがあるなど、海外展開に向けて可能性を広げているところです」(松田さん)
本プロジェクトを通じて、産業間連携、企業への補助が拡大
今回のNEDOプロジェクトは、国からの支援策の拡充にも繋がりました。従来の支援事業の場合、導入促進事業に対する支援が、単年度に限られていました。しかし、複数企業による大規模プロジェクトであることを考慮するように現場からの強い声が上がるようになった結果、それまで1/3だった補助率を1/2へ、さらに単年度事業から複数年事業化することが認められました。
また、本プロジェクト以降、産業間連携のプロジェクトが増加。単一事業者によるプロジェクトに比べて、複数事業者による産業間連携プロジェクトの省エネ効果がかなり大きいことがわかりました。こうした結果を受け、産業間・複数事業者間連携の促進が期待できます(図10)。
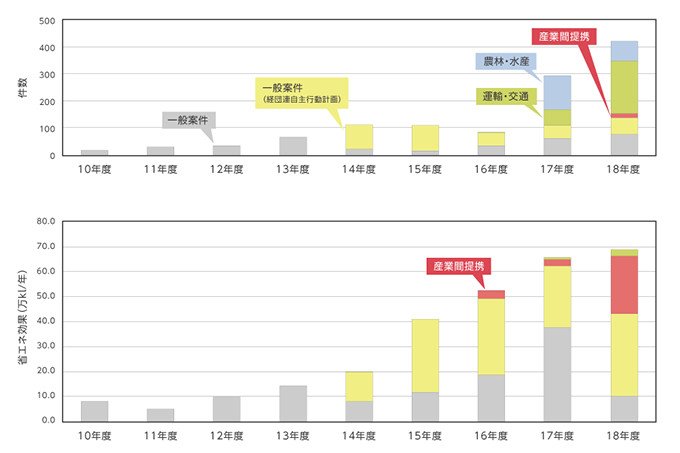
図10 NEDO事業における採択件数の推移と省エネ効果の推移。産業間連携ではより大きな省エネ効果が得られている
エネルギーだけでなく物質まで融通し合う解析技術も検討中
エリアワイドピンチテクノロジーは、2000年の千葉コンビナートによる調査研究から始まり、2工場による共同事業、水島、鹿島、宇部のコンビナートの調査研究、さらにタイ工業地帯と、約15年にわたってNEDOプロジェクトを推進してきました。
ここまで幅広く展開する上では、NEDOの支援が欠かせなかったと松田さんは振り返ります。「調査、研究、具体化と、それぞれの取り組みを認められて支援策も拡充してもらいました。その支援があったからこそ、新しい概念やツールを形にすることができ、今回の成果につながったのだと思います。また、秘密保持の問題などがある企業間連携が可能になったのも、NEDOプロジェクトであることへの信頼感が大きかったはずです」。
今後は、エネルギーだけでなく物質まで地域間で融通し合う「コプロダクションピンチ解析」を開発中だという松田さん。日本のテクノロジーで世界の工場の省エネ化を実現していこうとしています。
開発者の横顔
あらゆる産業に共通するユーティリティ部門から省エネ化
日本の省エネ技術で世界の省エネに貢献していく
千代田化工建設入社以来、触媒研究や石油プロセス設計、タイやマレーシアでの省エネ指導などに従事してきたエネルギーインフラプランニングユニット の松田一夫さん。1999年、社内に省エネルギー(ESCO)チームを設立(チームリーダー)し、翌年からNEDOプロジェクトのエリアワイドピンチテクノロジーの開発を担当してきました。エリアワイドピンチテクノロジー開発を通じて何本かの論文を発表したこともあり、2013年に東京大学大学院で工学系(機械工学)にて博士(工学)を取得しました。
「エリアワイドピンチテクノロジーについては、国内外で説明を求められることが多く、わかりやすく説明する目的もあり、学会発表や論文発表を行ってきました。気づいたらその成果がいくつかになっていたので、今回の博士号取得に繋がりました。こうして博士号を取得したことで、海外の人たちに対して説明しやすくなりましたし、さらに広い世界へピンチテクノロジーを普及させていきたいと思っています」
「最近は簡易な内容のプロジェクトの受注競争は人件費の安いアジアの国々が優位に立っていますが、エリアワイドピンチテクノロジーのような日本オリジナルの解析技術を適用して複数工場間をつなぐような複雑なシステムを提案していけば、まだまだ世界でトップに立てると信じています」
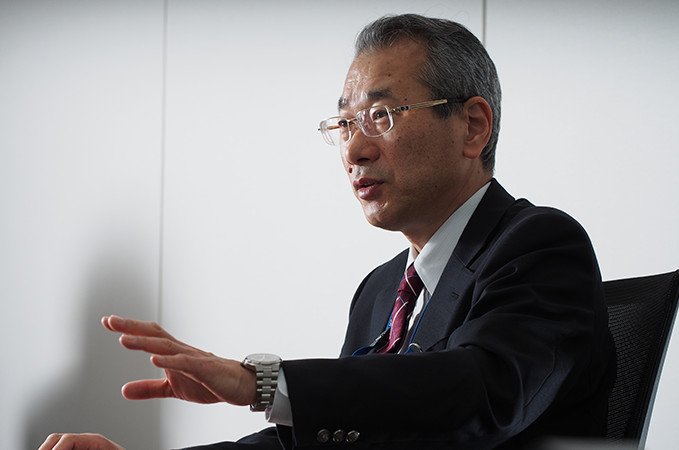
松田さん
なるほど基礎知識
排熱回収は省エネの基本
燃料を燃やして電気や水蒸気を発生させると、そのエネルギーの一部は熱として放出されてしまいます。こうした「排熱」は、大気中や冷却水にそのまま捨てられてしまうことが一般的でした。
しかし、地球温暖化対策やCO2削減についての意識が高まるのに併せて、こうした「排熱」を有効活用しようという動きが活発になってきました。とくに、発電とは別に、原料の反応などに使う蒸気を作っていた石油化学系プラントでは、排熱利用は省エネルギーと同時に生産コスト削減に繋がる重要な課題でした。
発電、温水、蒸気など、回収した熱の温度によって、その再利用方法は異なります。ただし、200℃以下の排熱は、低温であるがゆえに回収が難しく、放出される割合も大きいのが実態です。対して、回収しやすい高温排熱(250℃以上)は、発電や熱源などに直接利用することができ、利用価値が高いとされてきました(図A、B)。
排熱利用の代表ともいえるのは、エンジンやタービンを駆動源として発電すると同時に、回収した排熱を蒸気や冷却に利用する「コージェネレーションシステム」です。
さらに効率的に排熱を利用しようとするのが「ヒートカスケーティング(多段階利用)」で、熱交換するに従って温度が下がっていくのを利用して、段階的に必要とされる場所で使っていこうという考え方です。高温の熱で発電→プロセス加熱→蒸気→空調というように、1,500℃程度の熱から50℃程度まで徐々に温度を下げながら利用していきます(図C)。
「ヒートカスケーティング」では、本プロジェクトのように広域で複数の施設を対象にすることで、より効果を発揮すると考えられており、コンビナート内で熱共有として利用した排熱を、最終的には周辺地域の温水プールなどで利用することまで考えられています。
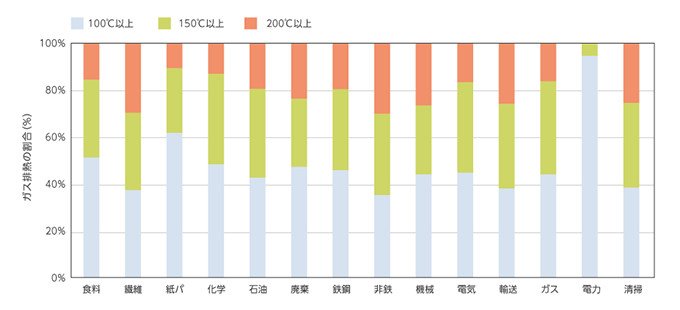
図A 業種別のガス排熱の割合。どの業種でも、回収しにくい150℃以下の低温排熱が多い
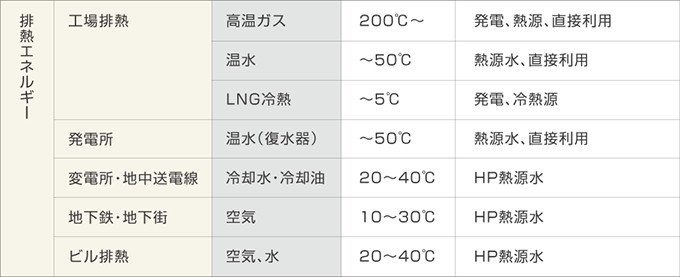
図B 未利用熱エネルギーの種類・温度レベルと主な利用方法
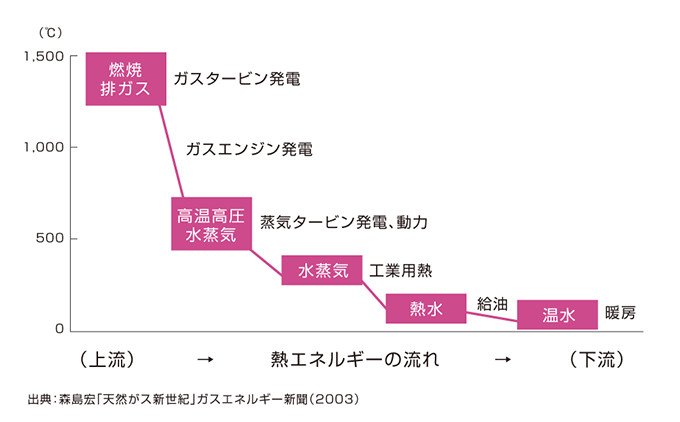
図C 1,500℃から50℃まで段階的に排熱を利用するヒートカスケーティング
NEDOの役割
「エネルギー使用合理化技術戦略的開発」
このプロジェクトがはじまったのは?
我が国は第1次石油ショック以来、強力に省エネルギーを推進し、そのエネルギー利用効率は世界トップレベルに到達しています。他方で、地球温暖化対策に対する要求が高まる中、温室効果ガスの大半を占めると言われているエネルギー起源の二酸化炭素排出量は、2005年度の実績において1990年度比+13.6%であり、新たな省エネルギーに関わる技術の研究開発の推進は喫緊の課題でした。また、2006年5月に策定された「新・国家エネルギー戦略」の「省エネルギーフロントランナー計画」では、技術革新と社会システム改革の好循環を確立させることにより、2030年までに少なくとも30%のエネルギー消費効率改善(GDP当たり)を目指すことを定めました。
これを踏まえ、経済産業省では、省エネルギー技術の大きなブレークスルーを目指し、産学官や異なる事業分野の様々な主体の連係を図り、中長期的視点に立った技術開発を進めるために、2007年4月に「省エネルギー技術戦略」をとりまとめました。NEDOでは、上述の「新・国家エネルギー戦略」及びこれに基づく省エネルギー技術戦略で示された、産業、民生(家庭・業務)、運輸の各部門における需要側の省エネルギーに係る課題を克服するために、本プロジェクトを実施しました。
プロジェクトのねらいは?
技術革新と社会システム改革の好循環を確立させることにより、2030年までに少なくとも30%のエネルギー消費効率改善(GDP当たり)を目標としました。 2011年度に実施した本制度の制度事後評価報告書によると、既に商品化もしくは今後商品化される可能性があるテーマにおける2030年時点での省エネルギー削減量は、約3,000万klに上ると想定しています。
NEDOの役割は?
NEDOは、本制度の実施にあたり、先導研究フェーズ、実用化開発フェーズ及び実証研究フェーズの3つの事業フェーズ並びに事前調査を設けることで、市場投入の確実性をより向上させるための制度設計を行いました。また、研究開発期間が3年間となる研究テーマについては、2年目終了時に外部有識者らによる中間評価を実施し、資源配分や事業計画の見直しを行い、「目標値や計画の見直し」や「中止または抜本的な改善」など、適切な研究開発マネジメントを実施してきました。
関連プロジェクト
お読みいただきありがとうございました。
ぜひともアンケートにお答えいただき、
お読みいただいた感想をお聞かせください。
いただいた感想は、
今後の連載の参考とさせていただきます。