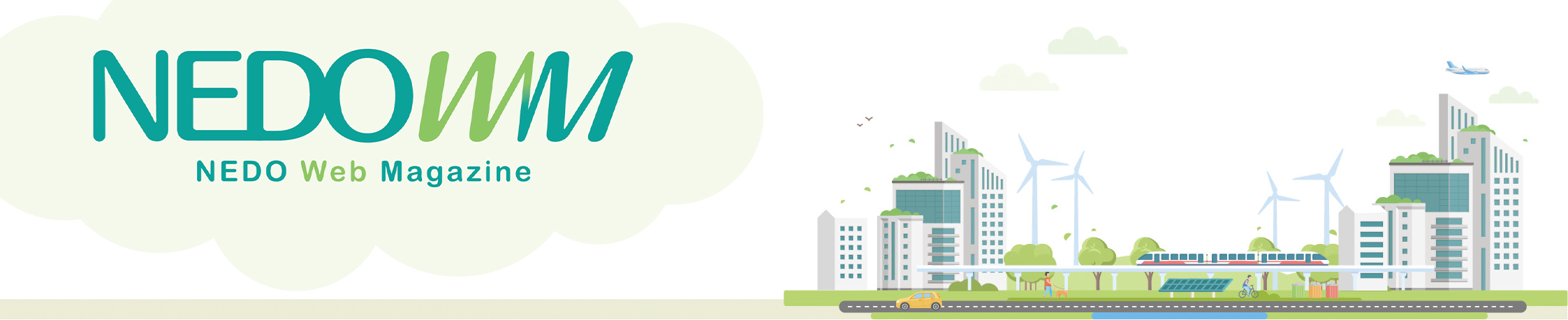
CONTENTS
INTRODUCTION
プラスチックでありながら従来材料と比べて3倍の衝撃エネルギーを吸収
BEGINNING
単一材料の限界をナノテクで突破するBREAKTHROUGH
世界初となるL/D=100の押出機を開発FOR THE FUTURE
2020年には約40億の市場規模に成長する見通し
FACE
常識では考えられない材料を実現INTRODUCTION 概要
プラスチックでありながら従来材料と比べて3倍の衝撃エネルギーを吸収
プラスチックをはじめとした高分子材料は、強度、耐衝撃性、加工性、軽量性などに優れ、様々な製品の外装、筐体、機構部品、部材などで幅広く利用されています。高分子材料へのニーズはさらに多様化・高度化しており、種類の異なる高分子材料を組み合わせた「ポリマーアロイ(合金化)」による新素材開発も活発に行われています。しかし、従来知られていたポリマーアロイでは、アロイ化前のそれぞれのポリマー本体が持つ特性を十分に引き出すことは困難でした。そこでNEDOでは、2001年より「精密高分子技術」プロジェクトをスタートしました。山形大学集中研(集中研=各参加メーカーの研究員が大学など一つの研究機関に集まる研究開発方式)の成形加工グループとして参加した東レ株式会社は、ナノメートルオーダーの構造制御技術を利用することで「硬いプラスチックに衝撃が加わるとゴムのように柔らかくなる特殊なプラスチック」の開発に成功しました。これまでにない特性を持つ新しい高分子材料は、自動車の安全部品やスポーツ用品などあらゆる分野で注目を集め、製品化に向けて進化を続けています。
BIGINNING 開発への道
単一材料の限界をナノテクで突破する
プラスチックといっても多種多様で、衝撃や熱に対する強さなどそれぞれに異なる特性を持っています。そういった単一材料にはない新たな特性を持つプラスチックを作り出すため、特性の異なる2種類のプラスチックを混合して作られるのが「ポリマーアロイ」です。
ところが、従来のポリマーアロイ化方法ではそれぞれの特性を十分に発揮することはできず、中途半端な材料になることが多くありました。少なくとも「1+1=2」を目指しているというのに「1×1=1」もしくは「1未満」になってしまうようなものでした。
この課題を解くカギとなったのが"ナノテクノロジー"でした。今回のNEDOプロジェクト「精密高分子技術」プロジェクトは、経済産業省による「ナノテクノロジープログラム基本計画」の一つに位置付けられていたもので、高分子に限らず、金属、セラミック、樹脂などといった様々な素材について、ナノレベルでの構造設計・制御による新しい特性を持った素材の創成を推進する取り組みです。
2001年に始まった「精密高分子技術」プロジェクトに参加した東レは、山形大学における集中研で、「自動車用構造材の開発」というテーマのもと、二軸押出機の中でポリマーを化学反応させながら混ぜ合わせて機能性を付加する「リアクティブプロセッシング」という技術による材料開発を進めました。
「硬いのに柔らかい」まったく新しいナイロンの誕生
これまで行われてきたポリマーアロイはミクロンオーダー(1mの100万分の1)ですが、今回のプロジェクトではナノメートルオーダー(1mの10億分の1)で複数のポリマーを混ぜ合わせる研究開発に挑みました。この技術のベースとなるのは山形大学工学部機能高分子工学科の井上研究室との共同研究による研究成果で、独自の製造技術を確立することにより数十ナノメートルオーダーで構造制御を可能にしました。
この製法で硬い性質を持つナイロンと柔らかい性質を持つ反応性ゴムを混ぜ合わせたところ、通常使用時には強度と剛性を持つプラスチックとしての性質を示し、衝突時など速くて強い衝撃に対してはゴムのように変形して衝撃を吸収するという、これまでの常識を覆す特性を有する「衝撃吸収ナイロン」を創成することに成功しました(図1)。
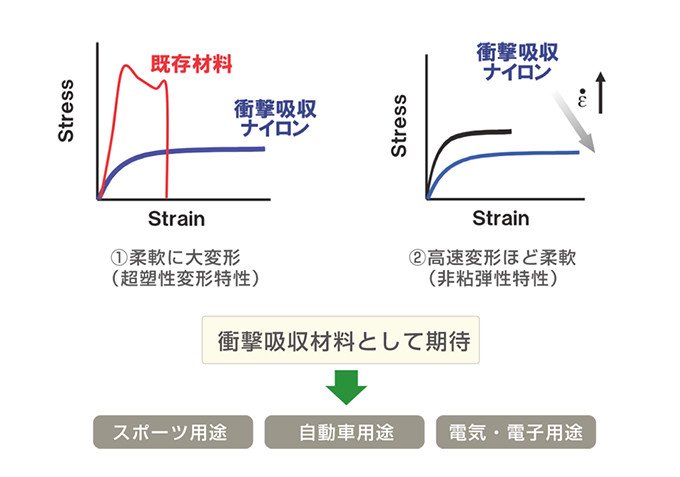
図1 「超塑性変形特性」と「非粘弾性特性」を併せ持つ衝撃吸収ナイロン
東レでは、「硬いのに柔らかい」という相反する特性を持つ高分子材料「衝撃吸収ナイロン」を2007年1月に記者発表したところ、50社以上から技術に関する説明の依頼を受けるなど、市場からの注目度も非常に高い革新的な材料であることを確認しました。
2011年度より本格的な製造段階に入り、現在、テニスラケットのガットストリングスやスノーボードのビンディングなどのスポーツ用品、ヘルメットの保護部品などで製品化が始まっています。
割れるプラスチック、壊れない衝撃吸収ナイロン
通常使用時の「衝撃吸収ナイロン」は、強度と剛性を保っているため、一見したところ一般的なプラスチックとなんら変わったところはありません。ところが、衝撃が加わると、それまで硬かった材料が柔らかくなってその衝撃力を吸収します。
普通のプラスチックと衝撃吸収ナイロンに対して行った高速大型落錘試験の結果を見ても、この特性は明らかです。この試験では、一般的なプラスチック(ナイロン)製の円筒に対して、193kgの錘(おもり)を時速約11kmで落下させます(インパクト時の衝撃は945ジュール)。
普通のプラスチックは力が加わった瞬間に亀裂が入り、最終的には割れてしまいます。一方、衝撃吸収ナイロンは錘に押しつぶされるように変形します。しかし、亀裂が生じたり、壊れることもなく、さらに元の形に戻すこともできます。
さらに実験を進めていくと、高速で変形するほど柔軟性が現れることが判明しました。この特性を活かせる分野として真っ先に想定されたのが、自動車の歩行者保護対策部品でした。歩行者と衝突したときの衝撃を軽減するにはゴムのように柔らかい素材が最適ですが、柔らかすぎると強度を保つために製品厚みが増大し重量増となるため燃費にも影響してしまいます。ところが衝撃吸収ナイロンであれば、通常走行時は硬さを保ち、事故などで強い衝撃が加わったときだけ柔らかくなり衝撃を吸収することができます。
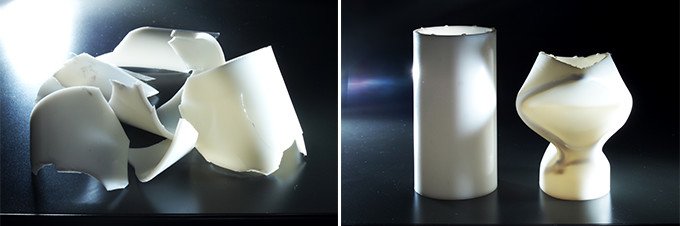
破壊試験の結果、従来品は割れてしまうが、衝撃吸収ナイロンは空き缶のように潰れただけ。この後復元も可能
リアクティブプロセッシングで「ナノミセル」を形成
このプロジェクトのベースには、ポリマーアロイ研究の第一人者である山形大学の井上隆教授のグループによる研究成果が技術背景としてあります。井上隆教授は高機能高分子材料開発の中でも、複数のポリマーを二軸押出機の中で化学反応させながら溶融混練する"リアクティブプロセッシング"という技術に着目してきました。
リアクティブプロセッシングは、2種の材料の末端につけられた官能基同士が、その接触する界面で化学反応により結合させることで界面での接着強度を高める技術のことであり、従来、こうした反応物は接触界面に留めておく思想で材料設計がなされてきました。井上教授らは発想を転換して、反応時間を長くして反応物のせん断を繰り返してみたところ、化学反応により結合した反応物が、せん断により界面から遊離しミセル化して分散していくことを発見しました。
高分子の末端部分が界面で接触して混ぜ合わされる通常のポリマーアロイは、数μmサイズの構造ですが、遊離した「ナノミセル」ならば、複数のポリマーを混ぜ合わせてナノメートルオーダーで制御することが可能です。こうしてできた「ナノミセル型アロイ」というまったく新しい概念が、相反する性質である強さとしなやかさを併せ持つ革新材料の創出に繋がりました(図3)。
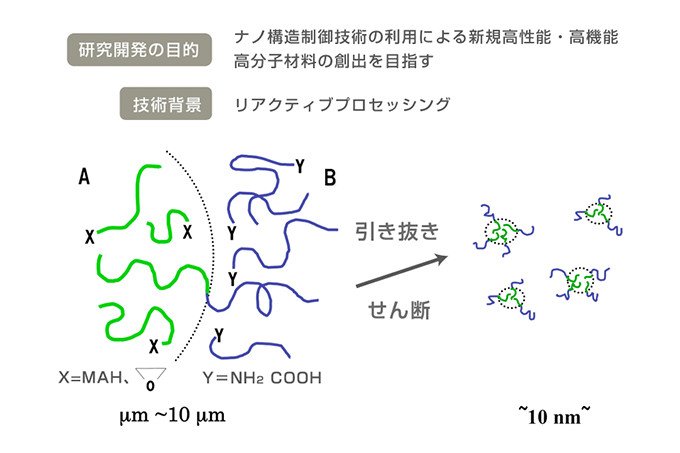
図2 従来のリアクティブプロセッシングでは材料末端の官能基同士を繋がれば混練は終了する。しかし、この研究ではあえて時間をかけて混練を継続。更にせん断を加えたところ反応物が遊離してそれぞれがミセル化することを発見。この仕組みを利用した
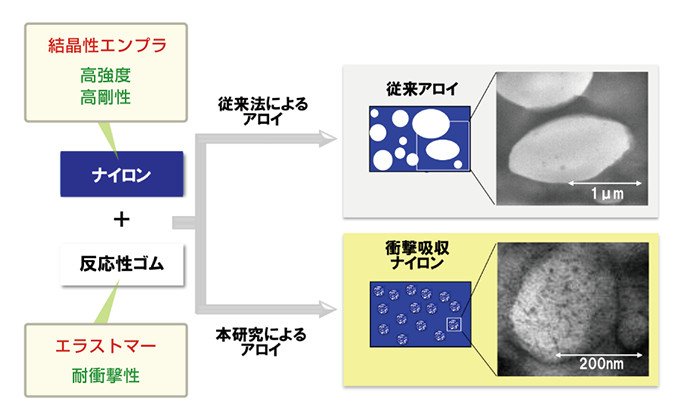
図3 従来法のアロイと本研究によるアロイでは粒子のサイズが異なる
高分子の常識では考えられない実験結果
プロジェクト開始当初から、メンバーのなかには「何かユニークな特性が発現するに違いない」という期待感はありましたが、具体的なニーズ解決を目指して進められたプロジェクトではありませんでした。多くのNEDOプロジェクトが社会ニーズを背景に研究開発が進められるのに対して、このプロジェクトはこれまでにない高機能高分子材料を作るという"シーズ"から始まったものだったからです。とはいえ、これほど革新的な材料が誕生するとは誰も予測していませんでした。
当時、山形大学集中研で研究に当たっていた小森研司さん(現・東レ地球環境研究所研究員)は、「大学の学生さんたちとポリマーアロイの作成とその特性および構造評価を繰り返し、井上教授ともディスカッションをしながら研究を進めていましたが、そのうち、実験で得られたサンプルの引張特性について、一般的な粘弾性法則と違う結果が出ることに気付きました。何かからくりがあるのではと、何度も実験してみましたが同じ結果に。これは大発見になるかもしれないと思いました」と当時を振り返ります。

図4 高分子の常識では、引っ張る速度が速くなるほどに破断伸度も低下するが(左)、開発材料は高速で引っ張るとむしろ破断伸度が増大、降伏点もない(右)
同社化成品研究所主任研究員である小林定之さんはまるで想定外だったため、最初はその結果を認められなかったほどだと言います。「できあがった材料の引張特性をテストした際、低速で引っ張ったときには特に目新しい特徴は見られませんでした。そこで引張速度を高速にしてみたところ、普通のプラスチックであれば応力の境界地点となる"降伏点"を迎えて破断してしまいますが、開発した材料には降伏点が現れずなかなか破断しません。これは高分子の常識からは考えられない結果であったため、実験にあたった研究員に『高分子のことを知らないせいで正しくない結果が出てしまった。実験者の腕が悪いせいだ。やり直せ』と怒ってしまったくらいですから(笑)。研究員は間違っていなかったのに、悪いことをしました」
BREAKTHROUGH プロジェクトの突破口
世界初となるL/D=100の押出機を開発
ナノミセル型ポリマーアロイ作りにおいて最初の壁となったのは、押出機の独自開発でした。できるだけ長い時間をかけて材料同士を反応させ、せん断を繰り返して反応物を遊離するには、押出機そのものを長くせざるをえませんが、スクリューの軸が長くなり過ぎると重みで先端部分が垂れ下がってしまい、真っすぐ回転させられなくなってしまいます。
仕組みは従来通りの押出機であっても、それほど長いスクリュー長の押出機は世の中に存在していませんでした。数社の押出機メーカーに製作を依頼してもどこにも断られ、最終的に名乗りを挙げてくれた1社によって独自の押出機開発を進めることになりました。
従来のリアクティブプロセッシングでは、スクリュー長(L)をスクリュー径(D)で割ったL/Dの値が50未満(通常は30程度)であるのに対して、本プロジェクトでは世界で初めて「L/D=100」の二軸押出機を作り出しました。スクリューから軸受け、モーター部まで、全長約5mにもおよぶ押出機ではあるものの、懸案だった先端が下垂してしまう課題については、二軸押出機の中に樹脂を充填させると丁度スクリューが浮いている状態になることで解決。この二軸押出機は「L/D=100(百)」にちなみ「MOMOKO」と名づけられました。
完成したMOMOKOによる最初のポリマーアロイの材料は、硬い性質を持つナイロンと、それとは正反対の柔らかい性質を持つ反応性ゴム。相反する2つの素材を混ぜ合わせたときに起こりうる反応への期待と同時に、MOMOKOが正常に機能するかどうかの不安も大きかったそうです。
「2種類の原料を入れて混ぜ合わせれば白色の樹脂が出てくるはずですが、スクリューがまっすぐ回らなければスクリューの金属屑などの異物の混ざった黒い樹脂が出てくるかもしれない。それだけに、スムーズに押出機が稼働して、透明感のある綺麗な白色の樹脂が出てきたときにはかなり感動して、そこにいた全員から自然と拍手が沸き起こりました」(小林さん)
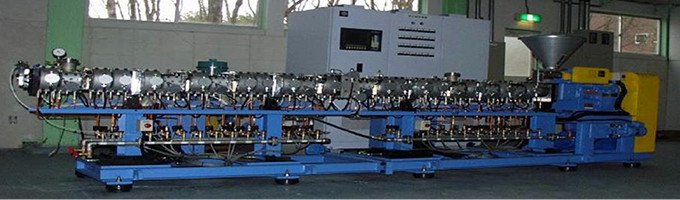
ナノミセル型ポリマーアロイのために作られた二軸押出機「MOMOKO」。従来の押出機より長い時間かけてじっくり練ってアロイ化する
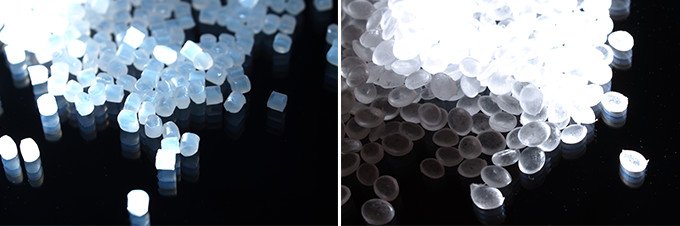
原料となる2種類の樹脂ペレット
革新的な材料特性のメカニズムを分子レベルで解明
MOMOKO によってナノミセル型ポリマーアロイ製造は可能になりましたが、なぜ相反する特性が発現しうるのかは不明なままでした。そこで、次に取り組んだのがナノ構造でのメカニズムやモルフォロジー(アロイ化したときの高分子の混ざり具合)変化の解明です。
構造評価については、東京工業大学の西敏夫教授による「弾性率マッピング(AFM)」技術を活用。この方法で従来型ポリマーアロイとMOMOKO 製のナノミセル型ポリマーアロイを比べてみたところ違いは一目瞭然でした。
ナノミセル型はナイロンと反応性ゴムの壁間距離がかなり詰まっており、密度の高い状態で連続的につながっています。2つの素材が連続的につながっている構造であるために応力集中することがなく一様な変形が可能になり、超塑性変形を引き起こすことがわかりました。しかも、引張試験時の温度変化を調べた実験では、高速で引張試験した場合のみ表面温度が上昇。均一に蓄熱して柔軟化することがわかりました(図5、6)。
小森さんに続き山形大学の集中研で研究開発を行った化成品研究所樹脂研究室の佐藤大輔さんは、「機構解明のために東京工業大学だけはなく、京都工芸繊維大学の陣内浩司准教授(現・九州大学先導化学研究所特任教授)による三次元電子顕微鏡を用いたモルフォロジー観察や産業技術総合研究所にも解析の協力をお願いしました。自分でも時速36kmでの高速引張試験などを行って物性を確かめました。こうした産官学連携による機構解明が実用化のスピードアップにつながりました」と話します。
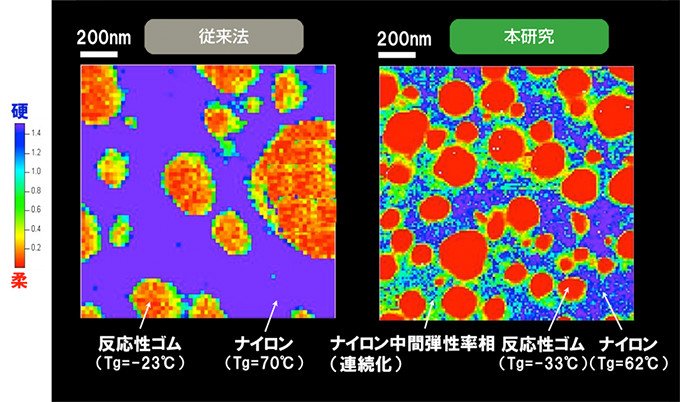
図5 弾性率マッピング(AFM)により、ポリマーアロイの混ざり具合を可視化
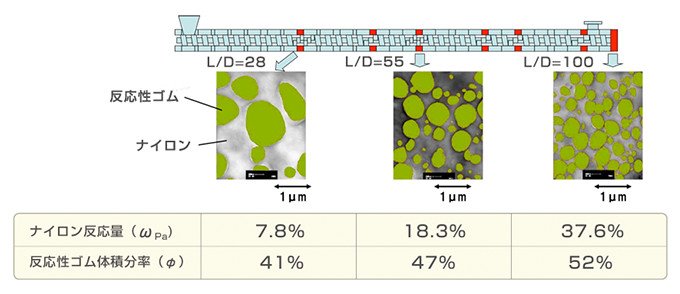
図6 反応時間ごとのモルフォロジー
※変化を検証 押出機にサンプルを取り出すためのバルブを数か所作っておき、反応時間の長さによりモルフォロジーの変化を調べた結果、反応性ゴム粒子の径、密集度ともに、L/Dが長くなるほどに小さく、密になっていくことが明らかになった。
※モルフォロジー 二種類以上の高分子を混合したときの分散状態の様子
量産体制に向けたスケールアップ
革新的なナノミセル型ポリマーアロイ「衝撃吸収ナイロン」が誕生。様々な分野のユーザーに対してサンプル提供を行ったところ、注目度はかなり高く、多くの企業から自社製品に活用したいとの強い要望が寄せられました。
しかし、ラボ実験機であるMOMOKOでは量産には対応できないため、量産化に向けたスケールアップが、次の大きな課題となりました。ただし、MOMOKOと同じL/D=100で量産しようとすると、押出機の全長を10数mにしなければならず、とても現実的ではありません。コストなどの面から考えても、L/Dを汎用押出機と同程度まで短くしつつ、ナノミセルができるようモルフロォジーを制御する必要がありました。
先に解明したナノアロイ形成メカニズムでは、リアクティブプロセッシング時に界面で生成される反応物の界面密度を最密充填値以上に制御することが重要だと分かっています。しかも、密度や充填量、粒子の大きさ次第で、変形する(柔らかくなる)速度を制御できます。こういったナノ構造を制御する方法を確立しつつ、押出機スケールアップにつなげていきました。
山形大学の集中研で3人目の研究員となった化成品研究所樹脂研究室の秋田大さんは、「山形大学で製造能力5倍のMOMOKO2号機を制作し、サンプルの大量試作を可能としたことで、ユーザーワークを飛躍的に加速させることができました。そして、東レに戻ってからはL/Dの短い生産機での量産技術を確立しました。L/Dの短い押出機でもしっかりと樹脂を反応させること、また大型の生産機でも混練時の発熱を抑制すること、この2つを両立させることは難しいことでした」と話します。
「実はここがもっとも苦労した部分」と小林さんが語るように、目標としていた汎用押出機での生産を可能とするまでに約2年を要しました。そして、2011年度末に、年産5,000トン能力の商業生産設備での稼働開始にまで至りました。
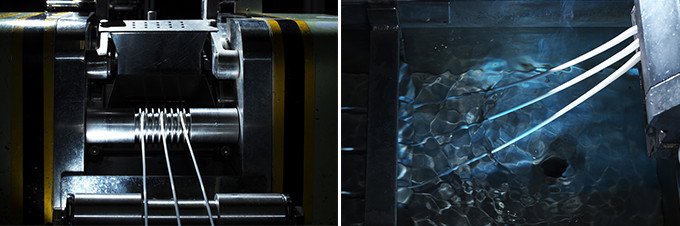
押出機から吐出される衝撃吸収ナイロン(右)、巻き取り・切断(左)されてペレット状の製品になる
FOR THE FUTURE 開発のいま、そして未来
NEDOプロジェクト・集中研方式で研究開発を推進
このプロジェクトは山形大学井上研究室に集中研を設置し、参加企業の担当者がほぼ常駐する形で研究開発が進められました。東レでは2年ごとに計3人の研究員を山形大学に赴任させました。小林さんは「ベースとなる技術開発と実用的な特性をマッチングさせながら進めることができたので、革新的でありながらも、市場でのインパクトの高いポリマーアロイを創出できました」と振り返ります。
「ポリマーアロイの分野では世界的に高レベルな研究を行っている井上隆教授がチームリーダーとなるプロジェクトで、当社をはじめ、数社の研究員たちが業界の壁を越えて活発な議論を重ねることができました。特に若手研究員たちが最先端の研究現場で修業期間を積ませてもらったことは、彼ら個人の将来にとってはもちろん、東レの今後にとっても大きな意味を持つと思います」(小林さん)
2020年には約40億の市場規模に成長する見通し
2006年のプレスリリース後は、20社以上にサンプルを提供、50社以上から技術に関する説明依頼があるなど、リリース直後から衝撃吸収ナイロンへの市場の関心は高く、その後も200件ほどのオファーを受け、2012年11月現在で約15品目が製品化に向けて進行しています。東レの試算では2020年には約40億円の売上が見込める市場規模になると考えられています。
この材料を使って最初に製品化されたのはヨネックス株式会社のテニスラケットストリングで、2007年2月から販売が開始されています。衝撃吸収ナイロンの優れた衝撃吸収性を活かし、高速のサーブを受けても腕や肩の負担軽減につながるほか、女性や高齢者の小さな力でも遠く飛ばすことができるなどのメリットがあります。
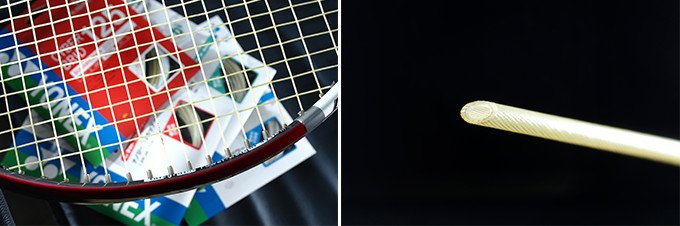
衝撃吸収ナイロンを使用したテニスラケット用ストリング(左)。その断面(右)。灰色の円形部分が衝撃吸収ナイロン
また、スノーボードのビンディング、ヘルメット部品などでも採用が決まっています。衝撃吸収ナイロンの特性を活かせば、これまで金属でしか作れなかった部品を樹脂に置き換えることも可能で、そうなれば軽量化、コスト削減にも繋がります。
問い合わせのあったもののなかには、医療・介護施設が転倒時の保護材として活用したいなど、想定外の活用法の提案を受けることも増えています。そういった依頼の増加を受けて、東レでは社内にワーキンググループを設けて用途の可能性を広げる検討を始めています。
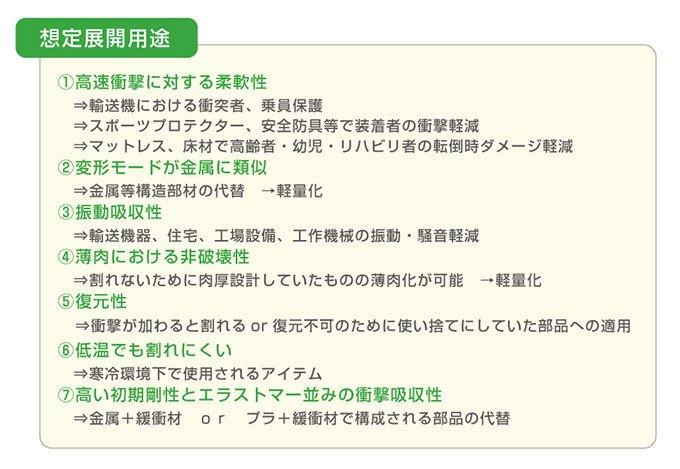
衝撃吸収ナイロンを採用したスノーボードのビンディング
小林さんは、「衝撃吸収ナイロンはこれまでにない特性を持つ材料なのですから、すでにある製品の材料に置き換えるのはもちろん、まったく新しいコンセプトの製品を生み出すポテンシャルも持っていると考えています。東レとしても材料を作って提供して終わりではなく、この特性をさらに生かした製品設計や加工まで踏み込んで提案していきたいと思っています」と語ります。(2012年11月取材)
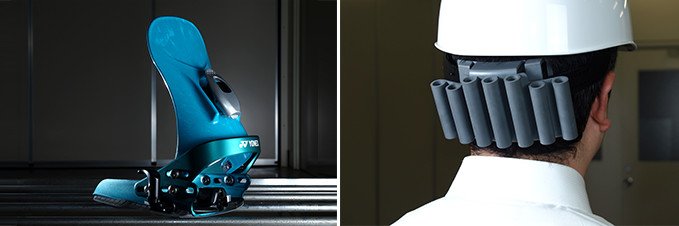
ヘルメットの頸部保護部品
開発者の横顔
常識では考えられない材料を実現
世界で初めての物性を発見
山形大学の集中研へは2001年度から2007年度までに、約2年交代で3人の研究員が派遣され「衝撃吸収ナイロン」の発見から実用化までの研究開発を行いました。最初の研究員の小森さんは、大学でケイ素ポリマーを研究、東レではエンジニアリングプラスチックの高性能化に取り組んでいました。その研究経験を買われて集中研へと派遣され、「固いのに柔らかい」という、相反する性質を持つ「衝撃吸収ナイロン」を発見することとなりました。
「押出機の設計から関わり、世界でも初の物性を発見するという貴重な経験ができました。一方、これをものにできるかというプレッシャーもありましたが、私に続いた研究員の努力のおかげで、商品化に繋げることができました。常識では考えられない発見を見逃さなかったのは、井上先生をはじめとして集中研の参加者と活発な議論ができたからだと思います」
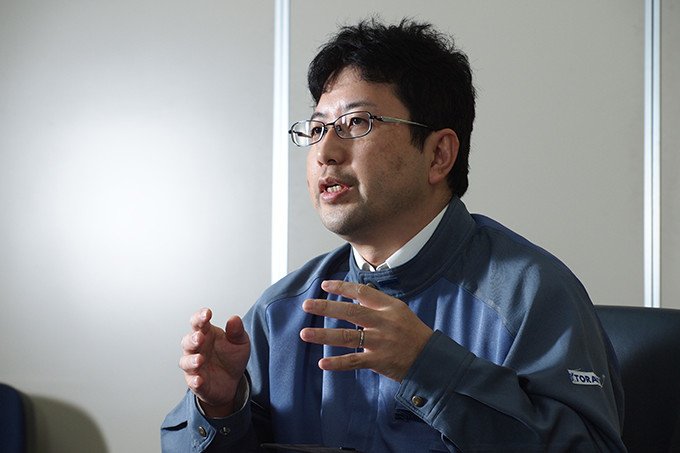
東レ株式会社
小森さん
熱い思いが衝撃吸収ナイロン使用製品第一号に
小森さんに続き、2004年から山形大学の集中研に派遣された佐藤さんは、大学院で液晶高分子について研究、入社後も液晶高分子の研究開発に携わり、新規エンジニアリングプラスチックの研究開発などを経て、衝撃吸収ナイロンに関わることとなりました。「小森さんの努力で相反性の性質は赴任前から分かっていました。その優れた特性を、どう料理すれば製品にできるか、衝撃吸収の機構解明と並行して用途開発にも力を入れました」
機構解明では先端の研究機関と協力、用途開発では研究ばかりでなく見本市や技術発表会に積極的に参加。その熱意が実り、「nanotech」展への参加がスポーツメーカーの目にとまり、衝撃吸収ナイロン使用製品第一号となるテニスラケットストリングにつながりました。「基礎研究から最終製品化まで携われることは研究開発でも希少なこと。リアクティブプロセッシング技術に関わったことは、現在の研究課題にも役立っています」
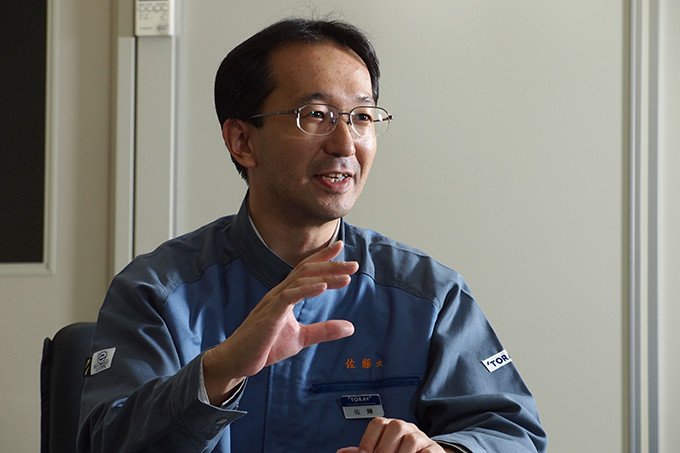
東レ株式会社
佐藤さん<
確信を持って量産化に取り組む
2006年から3人目の研究員となった秋田さんは、大学で生体触媒による高分子合成について研究、入社後は現在も在籍する樹脂研究室でナイロンの研究開発に携わり、本プロジェクトにも関わるようになりました。「実は、化学に興味を持ったのは高校で高分子合成について学んだことがきっかけ。何の役に立つのかと思っていた化学の面白さに気づかされたのがナイロンでした。ですからナイロンには深い縁を感じています」
秋田さんが取り組んだのは本格実用化に向けた量産化技術の確立。試行錯誤の連続でしたが「プレッシャーより確信があった」と言います。「量産化に先立ち、製品化の大きな目標でもある自動車部品に使用できるか、日本自動車研究所で実験を行いました。強い衝撃でも割れない実験部品を見たとき、なんとしてもこれを社会に広めなくてはと思いました」
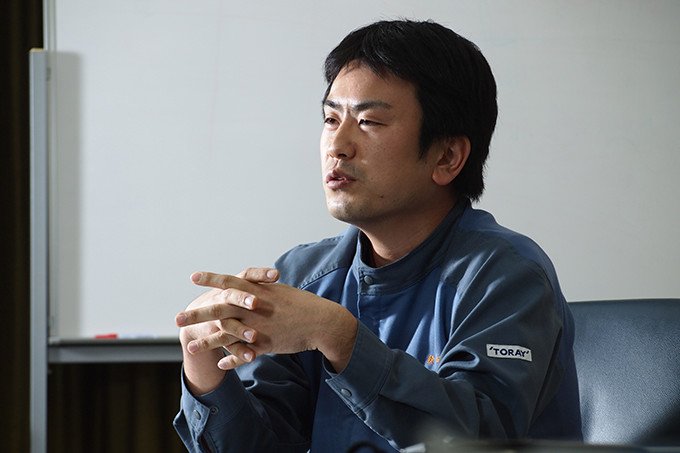
東レ株式会社
秋田さん
革新的な物性を持つ高分子材料はきっとまたできる
衝撃吸収ナイロンの研究開発でリーダーシップを発揮し、製品化を達成した主任研究員の小林さんは東工大の出身で、1995年に東レに入社するまで井上研究室(当時東工大)でポリマーアロイの研究をしていました。このプロジェクトでは学生時代の恩師とともに研究開発に取り組むことになりました。
「アロイをテーマにいくつかの研究を行っていたところ、ちょうどNEDOプロジェクトの募集があり、しかもその研究リーダーが井上先生という偶然が重なったのです。井上先生がどのような研究を進めているかは折々で拝見していますし、今回は本当にタイミングが良かった。そして、本プロジェクトのお陰で、今回とは違うアロイ化技術の可能性も見えてきました。新しい技術を使えば、新たな材料の組み合わせがあり得ますし、そうなればまた常識では考えられないような新しい物性を見つけられるかもしれない。高分子物理にはまだまだ分からないことがあり、一筋縄でいかないからこそ面白いのです」
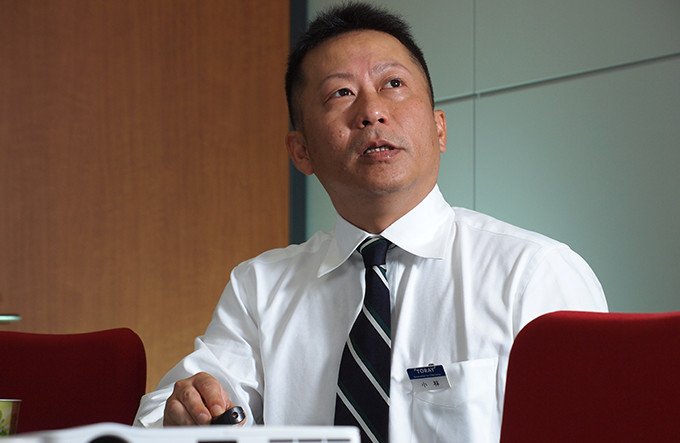
東レ株式会社
小林さん
なるほど基礎知識
プラスチックを高性能化する『ポリマーアロイ』
単一の高分子材料では特性が限られてしまうため、2種類以上の高分子材料を混ぜ合わせてプラスチックを高性能化するときに行われる手法がポリマーアロイです。「アロイ」は「合金」を意味する言葉ですが、樹脂どうしを混ぜ合わせることを「ポリマーアロイ」と称しています。
ポリマーアロイの代表格といえば、アクリロニトリル・ブタジエン・スチレン共重合樹脂(ABS)、ポリスチレン(PS)にポリブタジエンゴムを配合した高耐衝撃ポリスチレン(HIPS)など、いわゆる「プラスチック」と考えられている材料の多くがポリマーアロイです。
複数の樹脂を混合することで、耐衝撃性、耐薬品性、耐油性、耐熱性、加工性を高めるなど、高機能プラスチックを作り出してきました。また、新規に高分子を開発するよりも低コストかつ早く新しい機能を持つ材料開発ができるため、近年ポリマーアロイの研究には注目が集まっています。
しかし、混練するそれぞれの材料の特性を生かしつつ高機能高分子材料を作り出そうとしても、従来のポリマーアロイの手法ではそれぞれの特性が充分に活かせていたとはいえません。その点、このプロジェクトにおいてナノオーダーでの制御が可能になり、相反する2つの特性を有する材料ができあがったことはポリマーアロイにとっての新しいパラダイムともいえます。
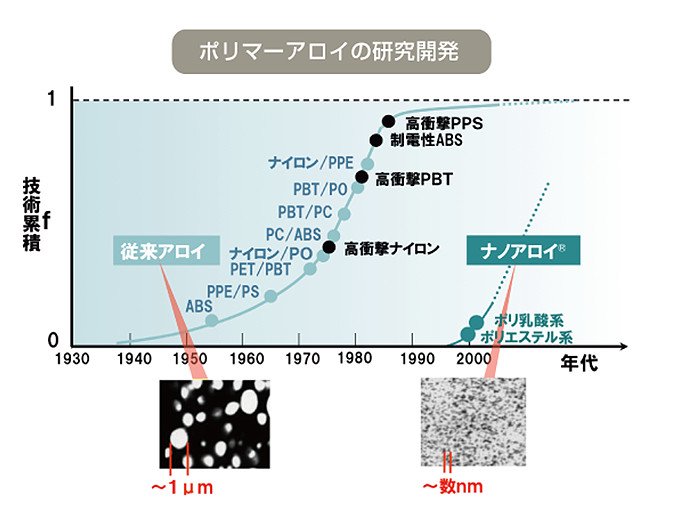
図7 ポリマーアロイの開発によってプラスチックの高性能化を実現。黒丸は東レが開発
NEDOの役割
「精密高分子技術」(自動車用構造材料の開発)
このプロジェクトがはじまったのは?
ナノテクノロジーは、物質をナノレベルで制御することにより機能や特性を飛躍的に向上させるなど産業技術分野に革新的発展をもたらすことのできるキーテクノロジーの一つと言えます。しかし、その革新性ゆえに体系化された技術基盤が未成熟でもあったため、経済産業省では、ナノテクノロジーの基盤構築、産業技術への展開を目標に2000年に「ナノテクノロジープログラム」を制定、本プロジェクトもその一環として開始されました。
プロジェクトのねらいは?
高分子は、プラスチック、ゴム、塗料といった工業材料として、また、合成繊維、タイヤ、建材などの身の回りの製品、さらには電子機器の部材にまで多様で幅広い用途で使われています。しかし、従来にない新たな機能や用途の高分子材料を生み出すためには、高分子のナノメートルレベルでの構造制御が必要で、本プロジェクトではその基盤技術の確立や人材育成、実用化への道筋を付けることが目標となっていました。その成果の一つが、急激な力が加わるほど柔らかくなるポリアミド系"ナノアロイ®"(衝撃吸収ナイロン)の発見でした。
NEDOの役割は?
ナノテクノロジーは産業発展のキーテクノロジーである一方、基礎技術の確立や研究開発の難易度が高く、そのため開発期間の長期化、投資規模の拡大などにより、研究開発リスクも大きくなるため、NEDOによる集中的な研究開発プロジェクトが必要でした。NEDOでは、プロジェクト発足にともなう基盤技術開発から研究開発をサポートし、先端的な研究および設備を備えた大学や研究機関と企業との連携を図るため「集中研」方式を採用したほか、研究の成果や達成度を評価し、実用化や事業化が有望なテーマの選択を行うなどの役割を果たしました。
関連プロジェクト
- 「精密高分子技術」プロジェクト
お読みいただきありがとうございました。
ぜひともアンケートにお答えいただき、
お読みいただいた感想をお聞かせください。
いただいた感想は、
今後の連載の参考とさせていただきます。