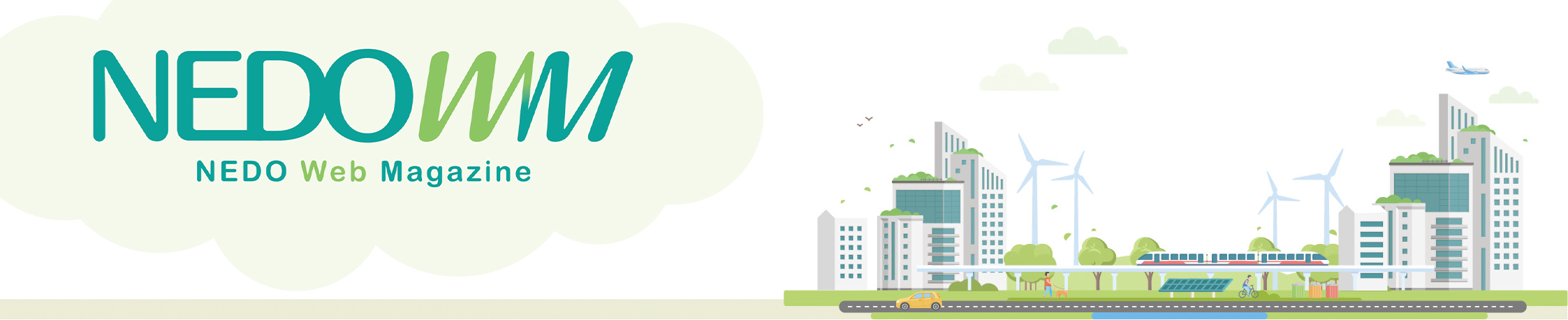
CONTENTS
INTRODUCTION
接着剤からフィルムへ半導体パッケージの積層数10倍
BEGINNING
電子機器の小型軽量化・大容量化に貢献するフィルム状接着剤
BREAKTHROUGH
基礎研究から実用化開発への転機FOR THE FUTURE
新しい分野への挑戦FACE
製品化とは理論と現実の差を埋めることINTRODUCTION 概要
接着剤からフィルムへ半導体パッケージの積層数10倍
携帯電話やスマートフォン、タブレット端末、携帯音楽プレーヤーなど、最近の電子機器の高機能化には目を見張るものがあります。これらの製品に欠かせないのが高度に集積化された半導体パッケージです。半導体内部には半導体チップと呼ばれる電子回路を収めたシリコン基板が何層にも積み重なっており、この積み重ねを多段化するほど半導体メモリは大容量化します。この積層度アップに大きく貢献しているのが、フィルム状接着剤「ダイボンディングフィルム」です。ダイボンディングフィルムの登場により、従来の接着剤では不可能だった多段化が実現し、半導体メモリの小型大容量化が飛躍的に進んだのです。日立化成工業株式会社はNEDOプロジェクトを通して、このダイボンディングフィルムの開発にいち早く成功しました。この製品は今や世界規模で採用され、現在では年間100億円を超える売り上げを達成しています。私たちが手にしている電子機器にも、この製品がきっと使われていることでしょう。
BIGINNING 開発への道
電子機器の小型軽量化・大容量化に貢献するフィルム状接着剤
近年、急速に普及し、私たちのライフスタイルに大きな変化をもたらしている電子機器。携帯電話やスマートフォンをはじめ、タブレット端末、携帯音楽プレーヤー、携帯ゲーム機など、今や便利で快適な日々の暮らしに欠かせないツールとなっています。これらの電子機器は新製品が登場するたびに小さく軽くなっていくのに対し、データを保存できる容量は飛躍的に向上しています。
このような、今日の電子機器の小型軽量化と大容量化を支えているのが、進化を続ける半導体パッケージとその製造技術です。電子機器を構成する半導体は集積化が進み、その製造にはナノレベルでの回路集積化技術や積層化技術が要求されています。特に積層化は近年になって注目を集め始めた技術で、半導体の集積化を大幅に進展させています。その積層化技術の実現に欠かせないキーとなるのがダイボンディングフィルムです。
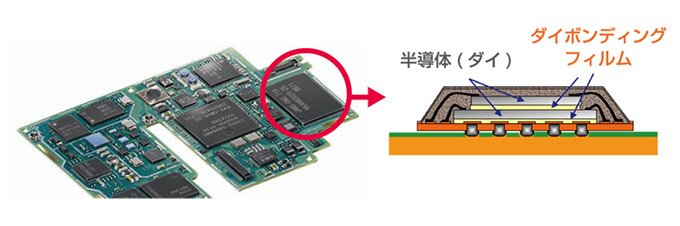
図1 半導体パッケージの断面図。
複数の半導体チップ(ダイ)が積層されており、半導体チップを固定するためにダイボンディングフィルムが採用されている(図は全て提供データによる仮図です)
半導体チップ積層化のために解決すべき課題
半導体の高性能化は1枚の半導体チップに微細な回路を描き込む集積化技術の進展によって支えられてきました。ところが2000年頃から現場のニーズに対して半導体メモリの記憶容量が不足するという問題が指摘がされ始めたのです。
その解決策として登場したのが複数の半導体チップを積み重ねる多段積層化という概念です。平屋の家にこれ以上の数の部屋を作るのは難しいので、マンションのように階数を増やすことで飛躍的な大容量化を実現しようというわけです。
しかし、多段積層化技術の実用化は一筋縄では行きませんでした。当初、半導体チップの積層化にはペースト状接着剤が使われていましたが、接着剤を薄く均一に塗布することが難しく、さらに衝撃やたわみへの耐性も確保しなくてはならないなど、解決すべき課題が山積していたのです。
その課題を解決したのが接着剤をフィルム状にするという着想でした。フィルム状にすることで接着剤の塗布・乾燥工程が減るとともに、事前にフィルムを貼っておくことで薄膜化した半導体ウエハを扱いやすくすることもできます。この着想を実用化したものがダイボンディングフィルムです。
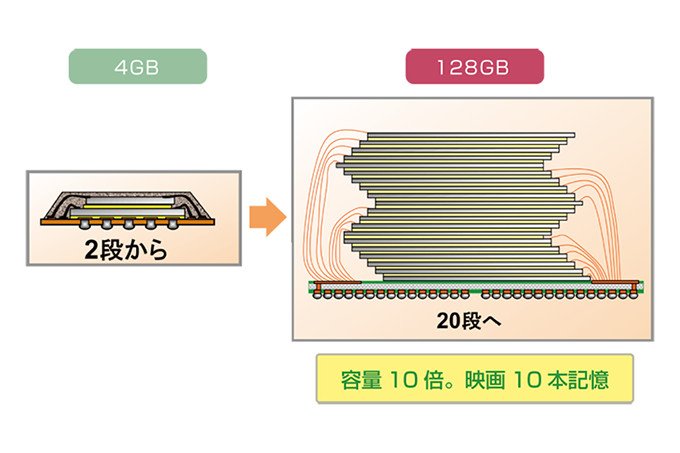
図2 半導体パッケージ内部で進む半導体チップの多段積層化だが、単純に積み重ねるだけでは半導体パッケージの厚みが増えてしまう。半導体パッケージの厚みを変えずに積層化するには半導体ウエハの薄膜化技術と薄膜化された半導体チップを積み重ねる技術が欠かせない
良く知られた2種類の材料から新しいフィルムを創り出す
日立化成工業のダイボンディングフィルム高性能化のきっかけは、2001年から始まったNEDO「精密高分子技術プロジェクト」への参加にあります。ダイボンディングフィルムの実用化を検討していた日立化成工業は、その当時、山形大学の井上隆客員教授が確立した「反応誘起型スピノーダル分解」に注目していました。ちょうどその頃、NEDOプロジェクトに参加するチャンスがあり、2001年より山形大学との共同研究が始まりました。
NEDOプロジェクトでまず着手したのは、材料の組み合わせ選定でした。ダイボンディングフィルムは、アクリルとエポキシ樹脂からなりますが、2種類の材料の組み合わせはスムーズに決まったわけではありません。同社主管研究員の稲田禎一さんは、材料選定の難しさについて次のように話します。
「最初に決めたのがアクリル系とエポキシ系の組み合わせです。業界内では耐熱性を求める接着剤の原料としてアクリルを選択したことへの懐疑的な意見も出ていましたが、社内で蓄積してきたデータからこの2種類の材料の組み合わせに期待して決定しました」
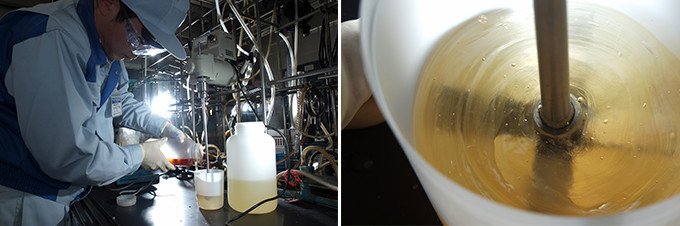
2種類の材料の混合作業
材料については様々な意見がありましたが、まず組み合わせを決め、このアクリル系とエポキシ系の高分子材料が熱硬化反応にともなってどのような構造変化をするのか、それをどうやって制御するかという基礎研究に取り組みました。
いくつかの材料の組み合わせを検討して、最適な組み合わせを見つけるという手法もありますが、まずは組み合わせを仮定し、構造や変化を丁寧に研究しようというアプローチです。
こうした研究方針について、同社専任研究員の宮内一浩さんは、「熱硬化反応による構造変化の理解と制御などの基礎研究に十分な時間を確保できたことは、ダイボンディングフィルムの開発全体を振り返ってみても、非常に大きな意味があったと思います」と当時を振り返ります。「2種類の材料はその構造によって、1+1が2ではなく1にもなることもあります。また、3にも4にもすることができます。構造制御がいかに大切であるかを学ぶことができ、そこで積み重ねた経験が、結果としてその後の製品開発段階に大きく役立ちました」(宮内さん)
NEDOプロジェクトへの参加により基礎・基盤研究を積み重ねた結果、10μmという薄さのフィルムを実現することができました。これは髪の毛の太さのわずか1/8ほどです。しかも、薄いだけでなく、エポキシ材料由来の高い接着性と、アクリル材料の柔軟性をあわせもつ高い機能性も備えることができました。
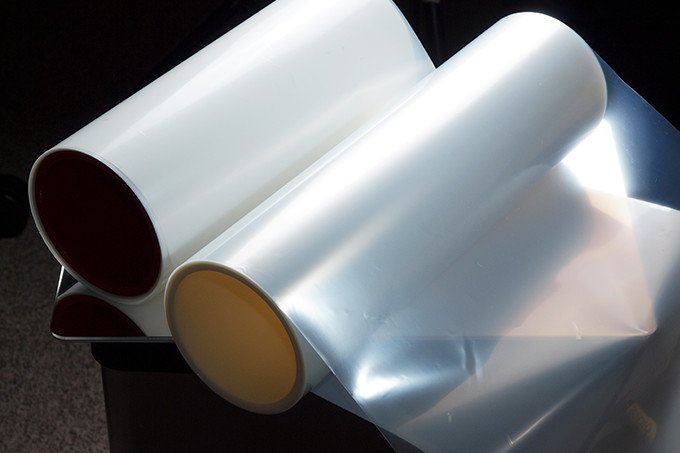
日立化成工業により開発されたダイボンディングフィルム。右側のロールのフィルムが厚さ10μm
BREAKTHROUGH プロジェクトの突破口
基礎研究から実用化開発への転機
2001年に始まった、このNEDOプロジェクトは、高分子材料の構造制御と製造技術の基盤確立を目的に開始され、その中で、日立化成工業は、アクリルとエポキシ樹脂の混合系に、山形大学の井上隆客員教授が別の材料で研究してきた「反応誘起型スピノーダル分解」を適用して、構造や特性を制御する研究に取り組んできましたが、2005年には実用化開発への転換が図られました。
この方針転換は半導体パッケージの高集積化要求の高まりと無関係ではありません。時期を同じくして、半導体パッケージのさらなる集積化要求に対して既存技術による対応の限界が問題視されはじめ、次世代の技術として期待されていた半導体チップの多段積層化技術に注目が集まりつつありました。
また、同社ではNEDOプロジェクトに取り組む一方で製造技術の改良や半導体メーカとの共同研究なども並行して行っていて、関連技術の実用化研究も同時に進めていました。これらの研究活動の蓄積から、アクリルとエポキシ樹脂の混合系でダイボンディングフィルムの実用化を目指すことになったのです。
ダイボンディングフィルム高性能化に大きく貢献した「反応誘起型スピノーダル分解」とは、2種類の高分子材料からなる混合物の熱硬化反応の際に、2種類の材料が次第に海と島のように分かれ、その構造がついには固定化される現象です。
日立化成工業は、アクリルとエポキシ樹脂の配合比などについて井上教授の指導を受けながら研究を進めることで、「接着性を持つエポキシ樹脂が界面に集まってくる現象」を発見しました。稲田さんは、「実は、当初は界面に集まる塊はボイド(空気の空隙)ではないかと考えていましたが、九州大学による走査粘弾性顕微鏡観察により、硬い成分であるエポキシであると明らかになりました」と説明します。この現象を制御することができれば、接着性を制御することも可能になります。実用化への道が開いた瞬間でもありました。
半導体パッケージの製造工程で高い接着性と優れた柔軟性を発揮
ダイボンディングフィルムは、常温ではアクリルとエポキシ樹脂が混じり合った構造をとっており、接着性はありませんが、半導体パッケージの製造工程において、温度によってその特性を変化させていき、最終的に高い接着性と優れた柔軟性を発揮します。
また、80℃程度に加熱するとフィルム表面が粘性を持ち始めるので、まずこの状態で半導体ウエハと貼り合わせます。するとダイボンディングフィルムの粘性によって密着するので、そのままウエハからチップを切り出すダイシング工程へと進みます。この際、ウエハはダイボンディングフィルムごとチップに分割されます(図3の1~2)。
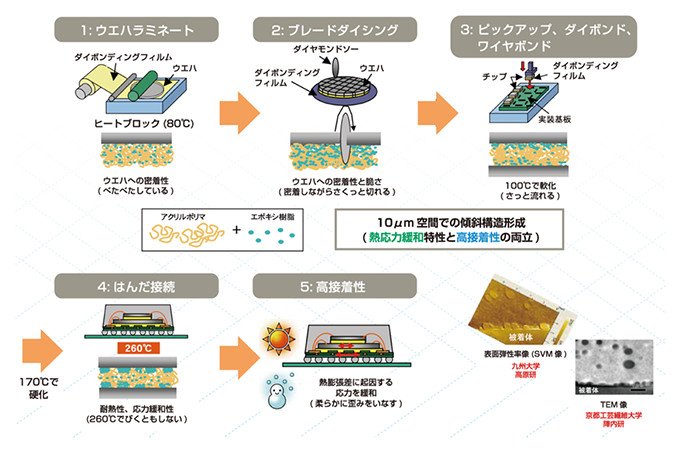
図3 半導体パッケージの製造工程とともにその特性を変化させていくダイボンディングフィルム
次に実装基板に積層するボンディング工程に入ります。これは半導体チップを実装基板上に積層し、配線を行う工程です。その後170℃の加熱工程でダイボンディングフィルム中の接着性を持つエポキシ樹脂が界面に集まり始め、積層されたチップ同士が動かないように固定されます(図3の3)。界面に集まったダイボンディングフィルム中の接着性のあるエポキシ樹脂は完全に硬化し高い接着性を発揮します。しかも、この時、ダイボンディングフィルムの中間層はその大半がアクリルで占められ、それにより高い柔軟性を持つことができます(図3の4~5)。
このように、実用化のきっかけとなった「接着性を持つエポキシ樹脂が界面に集まってくる現象」を巧みに利用することで、生産工程を増やすことなく多段積層化を実現できるダイボンディングフィルムが開発できたのです。
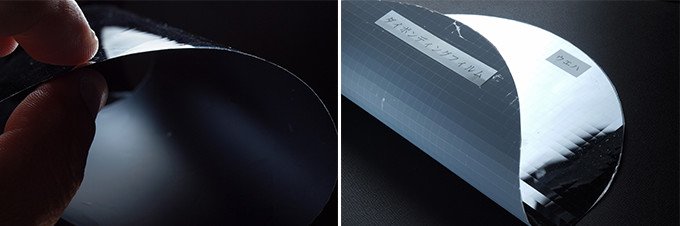
厚さ30μmの半導体ウエハ(左の写真)と、それに貼り付けられたボンディングフィルム(右の写真)
高い接着力の秘密は、ナノレベルで細かく絡み合った構造にあり
完全に硬化したダイボンディングフィルムは非常に強い接着力を発揮しますが、これは単に界面にエポキシ樹脂が集まっているからだけではないこともわかってきました。これに関して、同社専任研究員の郷豊さん(現在ディーエイチ・マテリアル 技術開発部 山崎技術開発グループ主任研究員として出向中)は次のように説明します。
「半導体パッケージの中で硬化したダイボンディングフィルムは、チップとの熱膨張率の差に起因する応力でチップから剥がれてしまうことがあります。私達は、プロジェクトの研究の中で反応誘起相分解によってエポキシ樹脂リッチ粒子を自発的に被着体付近に多く偏在させ、そのすぐ内側は逆に少ないナノ相分離構造制御に成功しました。この構造制御技術により、接着性と応力緩和性を両立する、すなわちダイボンディングフィルムとチップの剥がれを抑制可能な接着材料を開発できる見通しが得られました」
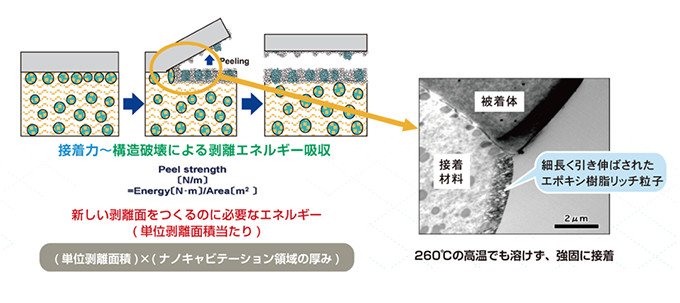
厚さ30μmの半導体ウエハ(左の写真)と、それに貼り付けられたボンディングフィルム(右の写真)
このようなナノ相分離構造は、硬化反応初期においてエポキシ樹脂の分子量増大によってスピノーダル分解がおこり、この段階でエポキシ樹脂分子量増大や部分的な架橋によって系の粘度が上昇するためマイクロメートルオーダーでの構造はそのままに固定され、エポキシ樹脂リッチ領域と低弾性のゴムリッチ領域それぞれにおいて第2段階のスピノーダル分解が開始して短い周期のゆらぎが発生し形成されると考えられます。
被着体をはがすときには、形成されたアクリルリッチ領域は、剥離による膨張応力でナノキャビテーションが起こってスポンジ状になり、エポキシ樹脂リッチ粒子は三次元架橋体であるにもかかわらず大塑性変形したのちナノキャビテーションをともなって寸断化されることで高い接着性を示すと考えられます。この塑性変形はエポキシ樹脂リッチ粒子がエポキシ樹脂単独の架橋体ではなく、濃度ゆらぎを有することに起因すると考えられます。
硬化後のダイボンディングフィルムにこうした構造を持たせ、なおかつ薄膜化も実現するにはナノメートルオーダーでの制御技術が必要不可欠です。早い段階から将来必要とされる薄膜化に備え、ナノメートルオーダーでの構造制御や解析を丁寧に研究開発してきたことが今日の成功につながったといえます。
FOR THE FUTURE 開発のいま、そして未来
新しい分野への挑戦
日立化成工業が提供するダイボンディングフィルムは、現在では年間100億円の売り上げを達成し、全世界シェアの過半を獲得するなど、半導体チップの多段積層化における事実上の世界標準(デファクトスタンダード)となっています。
この成果は、第9回産学官連携功労者表彰(2011年9月)において、「電子機器の小型化・大容量化を可能とする半導体接着技術 ~ダイボンディングフィルムの開発~」として最高賞である内閣総理大臣賞を受賞しました。
さらに本プロジェクトをきっかけにこれまで約400件の関連特許を出願しており、接着技術分野の技術革新に貢献しています。特許の出願について稲田さんは、「通常、産学共同開発でも関連特許の出願人を誰にするかは微妙な問題になることが多く、使わなくていい神経を使うことも少なくありません。しかし、プロジェクト関連特許に関する契約についてはNEDOにコーディネートしていただけたので、スムーズに出願することができました」と当時を振り返ります。
現在、同社では高分子材料が実際に熱硬化反応する時の成形プロセスについて、その原理解明を手がけるなど、基礎・基盤研究の成果を踏まえた実用化技術を開発しており、従来とは違う仕様や用途への対応も可能になっています。同社 専任研究員の岩倉哲郎さんは今後の展開について次のように話します。
「ダイボンディングフィルムで実現した高い接着性と柔軟性を活かし、LED照明やインバータ、電気自動車用制御装置など、別分野での製品開発も検討しています。特に接着力が非常に強いため、耐熱性や柔軟性といった付加特性を比較的自由に設定することができるのが特長です」
また、稲田さんは、今後の高付加価値製品について次のように話します。「多層半導体パッケージ用では、今後は薄膜化だけでなく、熱伝導性を付加してチップからの発熱を放熱させるといった高付加価値製品の開発にも取り組む予定です。集積化に伴う熱問題の解決策としても展開できると考えています」(2011年10月取材)
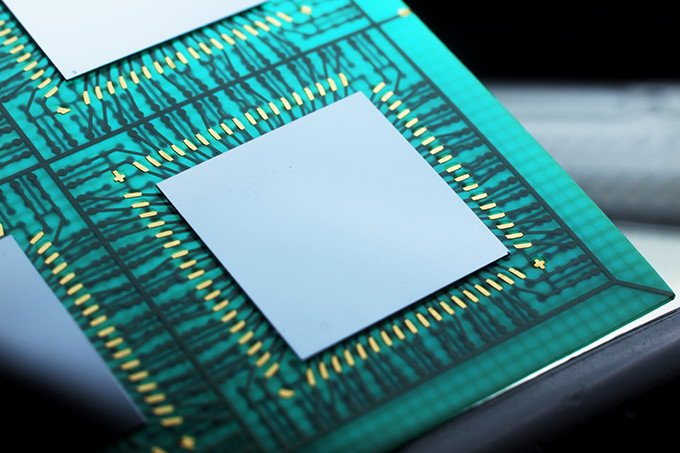
ダイボンディングフィルムを用いて基板に貼り付けられた半導体チップ(ダイ)
開発者の横顔
製品化とは理論と現実の差を埋めること
アクリルの可能性を改めて実感
同社主管研究員の稲田禎一さんの専門は高分子材料の物性研究。入社してからの約20年間、アクリルとエポキシ樹脂の接着フィルムに関わってきました。「2種類の高分子を混ぜ合わせたポリマーブレンドの面白いところは、確立された美しい理論がある一方で、すべての現象がその理論では予想できないところです。研究者の仕事は、この理論の世界と実験室での厳しい現実との隙間をいかにして埋め、製品化を進めていくかにあると思っています。そういう意味でもダイボンディングフィルムの製品化は嬉しい結果となりました」
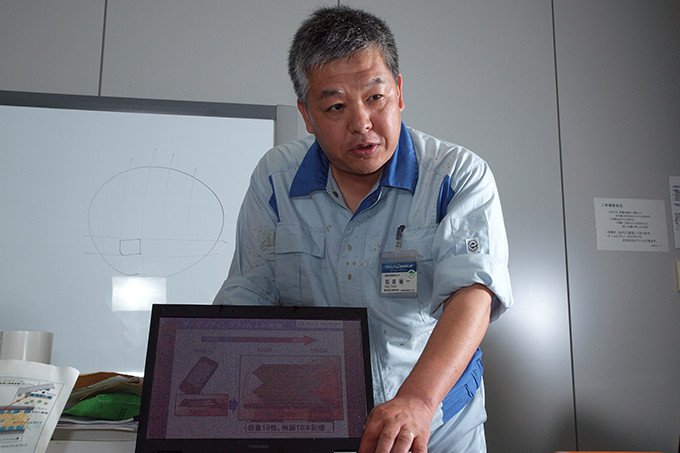
日立化成工業株式会社
稲田さん
基礎研究の重要性を肌で実感
同社専任研究員の岩倉哲郎さんが入社3年目の時、NEDOプロジェクトがスタート。その年からの2年間は山形大学に出向き、井上先生との共同研究に明け暮れました。「ダイボンディングフィルムは私が入社して初めて本格的に関わった仕事です。しかも、基礎研究から実用技術の開発、製品化という一連のプロセスに最初から参加できたのはよい経験でした。大学との連携も企業にはない学術的な刺激がありました。これからもそうした機会を積極的につくっていきたいです」
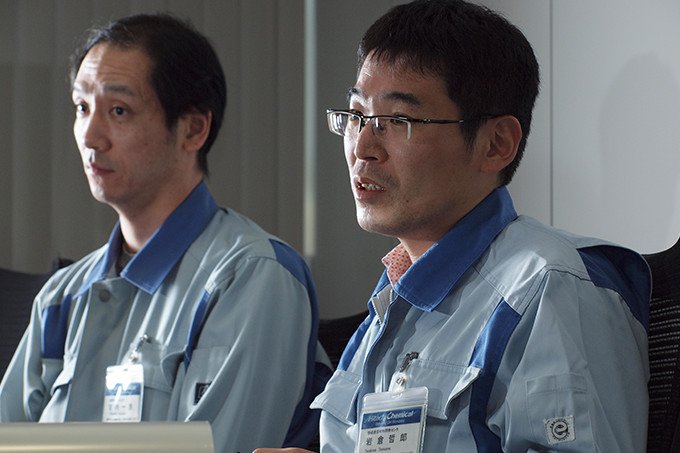
日立化成工業株式会社
岩倉さん
ナノレベルでの相分離現象の面白さに刮目
同社専任研究員の宮内一浩さんは、それまでプリント配線板材料関係の研究をしていたこともあり、電子材料全般に関わってきた経験を見込まれて今回のプロジェクトに参加。反応に関する領域を担当しました。「ダイボンディングフィルムを担当したのはこれが初めてでしたが、ナノスケールでの相分離現象解明に関われたのはよかったと思います。今はまた別の半導体関連材料の製品開発に携わっていて、この相分離制御の技術を他の製品にも適用できないかと考えながら新たな挑戦を始めています」
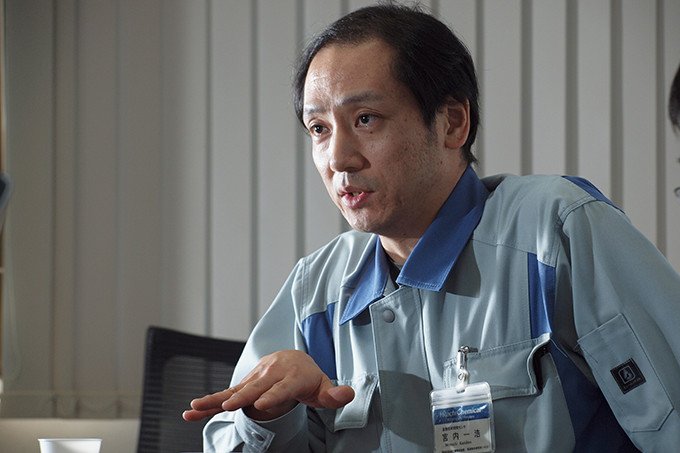
日立化成工業株式会社
宮内さん
刺激的だった大学など、企業以外の方との技術交流
同社専任研究員の郷豊さんは入社以来、FRPに用いられる熱硬化性樹脂の研究開発に従事。基礎研究よりも主に実際に市場に投入される製品の開発に関わってきました。「プロジェクトに参加することで、山形大学の井上先生をはじめとして、九州大学や京都工業繊維大学の先生方から基礎研究に関するご指導をいただけ、自分が一回り大きく成長できたように思います。今はディーエイチ・マテリアルに出向し、この経験を活かして熱硬化性樹脂製品の開発に取り組んでいます」
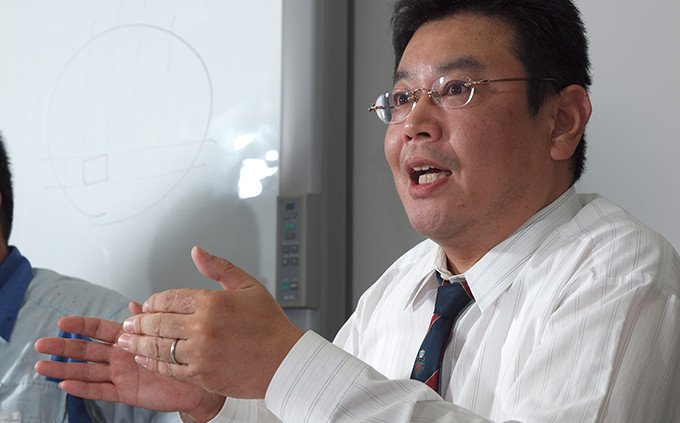
日立化成工業株式会社
郷さん
なるほど基礎知識
半導体パッケージの積層化に欠かせないダイボンディングフィルム
半導体パッケージとは、電子機器のカバーを開けると飛び込んでくる黒色の小さな部品です。この黒色は半導体チップを外界の影響から遮断し、保護する役目を持つ封止材で、内部には半導体チップが収められています。
半導体チップとは電子回路が描き込まれた薄いシリコン基板のことで、一般に四角い形状をしているためにダイと呼ばれることもあります。半導体チップは、ウエハと呼ばれる円盤状のシリコン基板に一度にたくさんの電子回路を描き込み、このウエハを四角く切り出すことでできあがります。
現在の半導体パッケージは高度に集積化(大容量化)されています。集積化技術も進歩しており、半導体チップに書き込む電子回路をより微細にして集積する技術に加え、集積化した半導体チップを何層にも積み重ねる多段積層化も進むなど、複数の技術を組み合わせています。
この複数の半導体チップの積層化に欠かせないのが半導体チップを積み重ねて固定する技術です。半導体パッケージはその製造工程において、次工程に搬送する時の振動や約260℃の高温環境にさらされます。製品に組み込まれた後も振動や周辺温度の変化に耐え続けなくてなりません。そのため、積層した半導体チップの固定化では、振動、さらには高温や経年劣化への耐性が求められます。
しかし、従来の液体接着剤は、これらの要求仕様に応えられませんでした。また、薄く均一に塗るのが難しい、接着剤がはみ出す恐れがあるなどの問題がありました。こうした問題を解決したのが、接着剤をフィルム状にしたダイボンディングフィルムです。
ダイボンディングフィルムは、優れた接着性能と操作性をもつだけでなく、工程を減らす効果もあります。フィルムを貼ったシリコンウエハから半導体チップを切り出すことで、多数のチップに一度にフィルムを付着させることができ、1個1個のチップに接着剤を塗布する工程が不要になるからです。
NEDOの役割
「精密高分子技術」(高性能ダイボンドの開発)
このプロジェクトがはじまったのは?
半導体パッケージの高集積化を求める市場からの要請に従い、半導体チップ上に電子回路を形成する技術は微細化が進み、その密度を極限まで高めてきましたが、経済的な理由も含めると1枚の半導体チップに集約させる手法の限界点も見え始めています。そこで、さらなる集積化の1つの方向として、半導体チップを積み重ねるという、縦方向の積層化技術が現在では進んでいます。本プロジェクトでは、そうした半導体の集積化を支える技術の一つとして、高性能半導体接着フィルム(ダイボンディングフィルム)の開発を行いました。
プロジェクトのねらいは?
ダイボンディングフィルムとは、半導体チップ同士を貼り付ける接着剤(ダイボンド)の一種で、フィルム状のものです。半導体パッケージの製造工程は温度変化も大きく、また、製品として市販された以後は使用時や持ち運び、落下など、さまざまな振動も加わります。そのため、ダイボンディングフィルムには、接着剤としての機能はもちろん、熱や衝撃に対する耐性も求められます。そして最も重要なことが、こうした要求に応えつつ、複数の半導体チップを積層しても厚みを増やさない薄膜化の実現でした。
NEDOの役割は?
ダイボンディングフィルムのような高分子材料は高いポテンシャルがある一方、研究開発の難易度が高く、研究期間の長期化、開発投資の大規模化が伴います。NEDOでは、高分子材料の高度化を目指して、2001年度よりプロジェクトを開始し、基盤技術と、実用化技術の双方の研究開発を推進してきました。また、ナノスケールの観察技術を担う学との連携強化を図ったことにより、実用化に向けたメカニズム解明が大きく飛躍しました。ダイボンド分野では、従来にない高性能接着フィルムの製品化を達成し、半導体パッケージの高集積化を後押しし、電子機器の小型化や高性能化に貢献しています。
関連プロジェクト
- 精密高分子技術(高機能ダイボンドの開発)
お読みいただきありがとうございました。
ぜひともアンケートにお答えいただき、
お読みいただいた感想をお聞かせください。
いただいた感想は、
今後の連載の参考とさせていただきます。