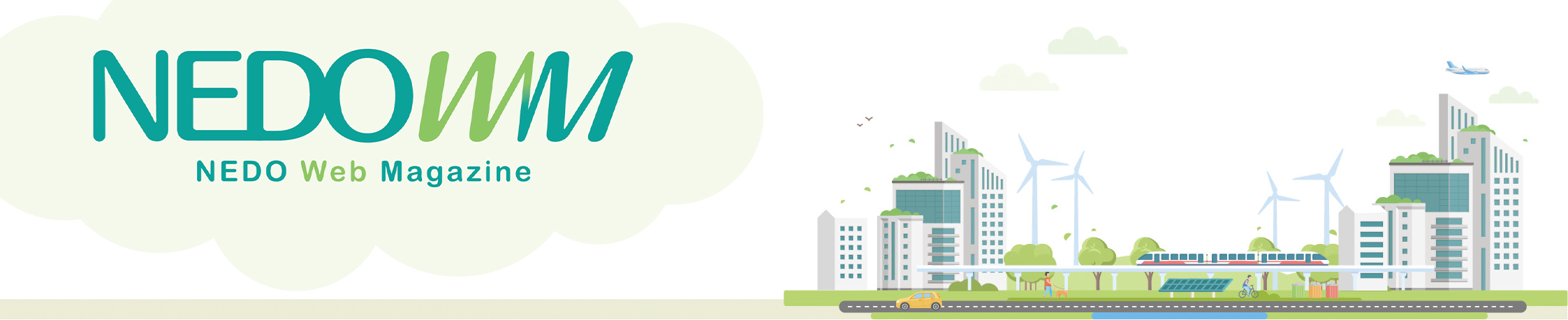
CONTENTS
INTRODUCTION
有機溶剤を使わない革新的塗装技術でVOC排出量が従来の1/3に!
BEGINNING
光化学スモッグの原因物質の一つであるVOC
BREAKTHROUGH
二酸化炭素と相性のいい塗料を見定める
FOR THE FUTURE
NEDOプロジェクト成果のおかげで、多くの企業との共同研究へ展開
FACE
東北発の技術を世界に広めたいINTRODUCTION 概要
有機溶剤を使わない革新的塗装技術でVOC排出量が従来の1/3に!
自動車ダッシュボードなどの内装部品、デジタルカメラや携帯電話などの工業製品には、ユーザーの好みを満足させる高い意匠性や品質が求められます。そうした製品に様々な機能性を付与する加工の一つが塗装です。塗装には有機溶剤(シンナー)が必要で、塗料を薄めてきれいな仕上りにするために使用されています。しかし、有機溶剤は人体や生態系に有害な物質を含み、光化学スモッグの発生など大気汚染の原因物質(VOC/揮発性有機化合物)にもなります。VOCを含む人体や環境へのリスクの高い化学物質について、わが国ではその適正管理や排出・使用削減を各種の法律や規制により進めています。部品塗装加工のトップ企業である加美電子工業株式会社では、こうした社会情勢を踏まえて、VOCを含まない革新的な塗装技術の開発にNEDOの支援を得て挑みました。有機溶剤の代わりに超臨界状態にした二酸化炭素で希釈・吹き付けが可能な塗装方法を開発し、VOC排出量を従来に比べ1/3に削減することができました。すでに自社工場で使用しているほか、大手自動車内装部品メーカーの塗装システムにも導入されています。
BIGINNING 開発への道
光化学スモッグの原因物質の一つであるVOC
VOCとは、揮発性有機化合物(Volatile Organic Compounds)の略語で、大気中で気体となる(揮発性)有機化合物の総称です。塗料、印刷インキ、接着剤、洗浄剤、ガソリン、シンナーなどに含まれるトルエン、キシレン、酢酸エチルなどが代表的な物質です。自動車の排気ガスなどとともに、光化学スモッグの原因物質の一つとされています。
光化学スモッグは、自動車の排気ガスに含まれる窒素酸化物やVOCが紫外線の影響で光化学反応を起こし、生じた有害物質(光化学オキシダント、浮遊粒子状物質等)が空中で煙状になって発生します(図1)。1970年代に発生件数がピークになり、大きな社会問題になりました。自動車の排出ガス規制などによって一時減少しましたが、2002年に千葉県で実に18年ぶりの光化学スモッグ警報が発令されるなど、近年再び発生回数が増加してきています。
こうした事態を受け、2004年に大気汚染防止法が改正され、2006年からVOCの排出が規制されるようになりました。2000年の排出量を基準に、2010年度までに3割削減することが目標となっています。
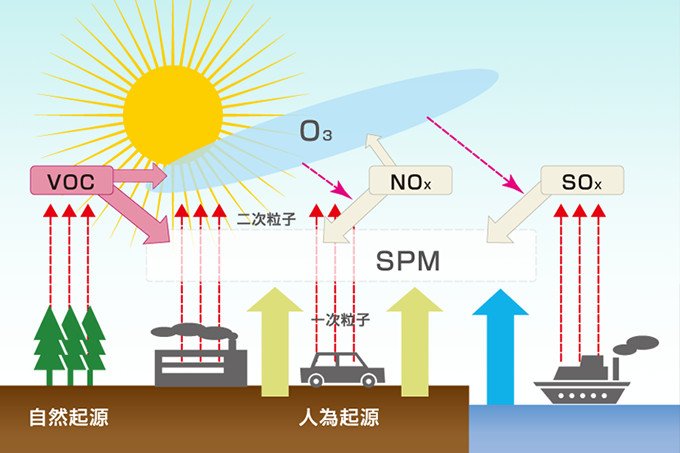
図1 VOCの大気中での反応。VOCは大気中で光化学反応、物理反応等の複雑な反応経路を経て光化学オキシダントやSPM二次粒子(浮遊粒子状物質)の生成に寄与し、光化学スモッグの発生原因にもなる
VOCの3割削減に向け、業界全体で自主規制に取り組む
環境省の発表では、工場などの固定発生源から1年間に排出されるVOCの総量は、約146.5万t(2000年度)と推計されています。その発生源としては、塗装、燃料、インキ、洗浄剤、接着剤からの排出量が全体の75%を占め、業種別に見ると塗装からの排出が一番多い結果となりました(図2)。
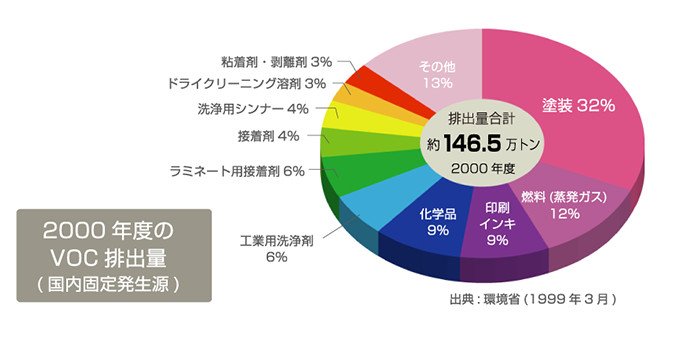
図2 VOCの発生源別グラフ
塗装で排出されるVOCは塗料および塗料の薄め液から発生します。金属や樹脂などの材料へ塗装を行うには塗料を有機溶剤で薄めて粘度を下げて調整する必要があります。有機溶剤を使用することにより、塗料が細かい粒子で噴霧でき、光沢感や色鮮やかなデザイン性の高い塗装を行うことができます。高品質・高機能な塗装を行うには有機溶剤が欠かせないことなどから、VOC排出量全体の約3割を塗装が占める結果となっています。
それ故、塗装業種でのVOCの排出・使用削減が、改正大気汚染法の掲げた削減目標の達成には重要であり、法規制だけでなく、企業や業界全体での自主規制も実施され、排出・使用削減に向けた努力が続けられています。
宮城県加美町に所在を置く加美電子工業株式会社は、金属部品やプラスチック部品への塗装を手掛け、国内外メーカーへ部品を数多く供給している企業です。塗装の塗膜品質とデザイン性を維持しながら、VOCの排出・使用削減を可能にするための技術開発を長年続けてきました。
そのような中、顧客の要望もあり水を主溶剤にして有機溶剤含有量の少ない水性塗装や、より環境負荷が少なく設備投資も少なくて済む、二酸化炭素を超臨界状態にして塗料を希釈して吹き付けする塗装装置の開発に挑戦し、実用化に成功しました。
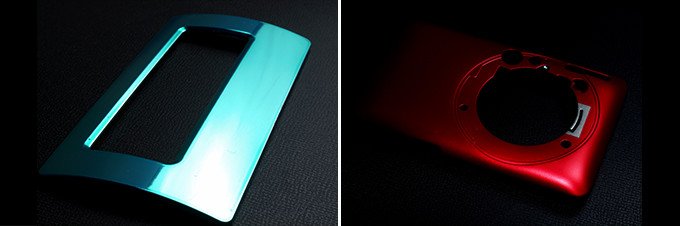
加美電子工業が塗装加工した自動車部品(左)とデジタルカメラのボディ(右)。均質な塗装面や光沢の美しさなどへの評価が高い
水系塗装でVOC削減はできたものの二酸化炭素排出量は増加
加美電子工業がまず初めに取り組んだことは、VOC削減に向けた水性塗装でした。納品先のヨーロッパ自動車メーカーが、EC環境指令に基づき水性塗料を指定したためでした。しかし、水性塗装はVOCによる大気汚染物質の発生が少ないものの、有機溶剤塗装に比べて新たな設備が必要なことに加え、別の問題も予測されました。
まず水性塗料は、水を主溶剤にしており高品質の塗装をするために、温度や湿度などの環境を一定に保つための空調整備や品質を安定させる為の洗浄装置や、新しい専用塗装装置が必要になりました。また乾燥工程では、水は有機溶剤よりも揮発性が低いために、水分を飛ばすため従来より長い乾燥ラインが必要になります。さらに部品に付着しなかった水性塗料は、塗料成分が水に溶け込んでしまっているために排水分離処理が難しくなります。
塗装装置や洗浄装置、空調設備など新たな設備を設け、塗装条件の検討を重ねた結果、有機溶剤塗装同様の塗装品質を実現できるようになりましたが、多額な設備投資、運転コストの増大などにつながりました。加美電子工業の早坂裕社長は、「確かにVOCの排出・使用は削減できましたが、空調や洗浄、乾燥などで大量のエネルギーが必要になり二酸化炭素の排出は増加してしてしまい、もっと良い環境対策はないのかと考え、新たな塗装方法を模索するようになりました」と語ります。
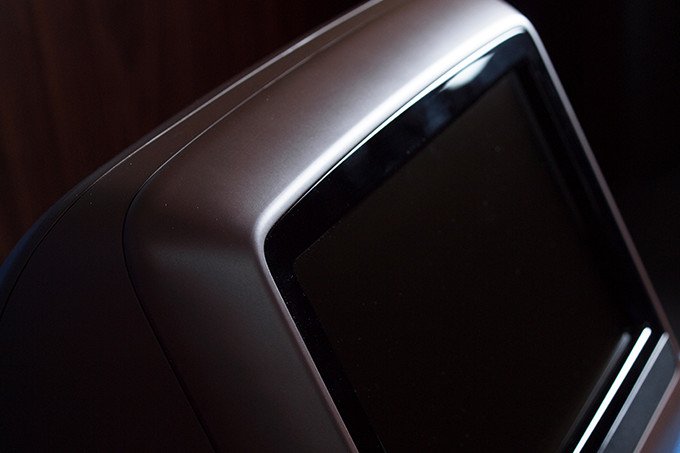
加美電子工業が水系塗装した外国自動車メーカーの内装部品。後部座席用の液晶モニターのカバー
二酸化炭素を使った塗装に着目
そこで着目したのが、超臨界二酸化炭素でした。早坂裕社長は、「最初は、電子部品の洗浄剤にフロンが使えなくなったため、超臨界二酸化炭素がその代わりにはならないかと考え、産業技術総合研究所(以後「産総研」)へ相談に行ったときに、高い溶解特性のある超臨界二酸化炭素が塗料の希釈剤の代わりになるという技術を紹介され、これは使えるかもしれないと思ったのです」と話します。それが可能ならば、有機溶剤塗装の薄め液の大部分を二酸化炭素に置き換えることができ、VOCの排出を削減できると考えたのです。
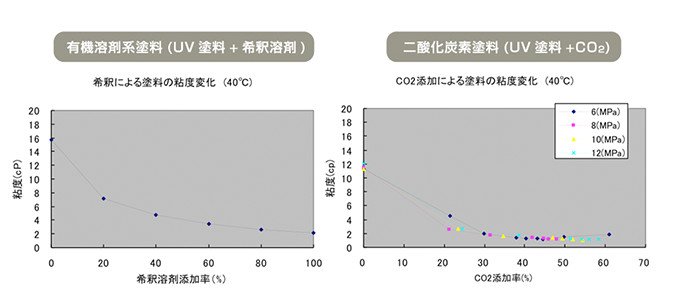
図3 高圧二酸化炭素は、塗料との親和性が強く、塗料中に容易に融解して、希釈有機溶剤同様に塗料の粘度を低下させる効果があった
当時、米国ではすでに超臨界二酸化炭素と塗料を混合し、噴霧ガンから吹き付け塗装するシステムが開発されてはいましたが、日本ではまだ実績がありませんでした。加美電子工業では、2006年に、宮城県内にあり超臨界流体の研究に実績のある産総研のコンパクト化学プロセス研究センターと共同研究を開始しました。翌2007年度からは、NEDOの「有害化学物質リスク削減基盤技術研究開発」プロジェクトの追加公募に応募して採択され、実用化に向けた研究開発を本格化させました。
プロジェクトではそれぞれの特色を活かして、加美電子工業では塗装のプロとしての経験から二酸化炭素適合塗料の開発を、産総研コンパクト化学プロセス研究センターでは、超臨界を扱うエンジニアリング専門集団として二酸化炭素塗装装置の開発を行いました。また宮城県産業技術総合センターは、高い試験分析技術から塗膜品質評価技術の確立を担当しました。
研究開発の目標は、従来の有機溶剤塗料による塗装において大量に使用される希釈溶剤(VOC)を極少量の二酸化炭素に替えることにより、有機溶剤塗装と同等の塗装仕上げ品質を確保したまま、VOC発生を大幅に低減させる塗装技術の確立と、今ある塗装設備に置き換えが可能な塗装装置の開発でした。
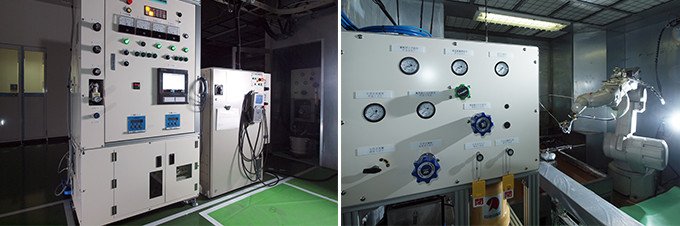
加美電子工業が開発した超臨界二酸化炭素塗装システム
従来の有機溶剤による塗装では、塗料を噴霧ができる粘度に下げるため、塗料とほぼ同量(重量比)の薄め液(有機溶剤)を使用していました。超臨界二酸化炭素塗装は、薄め液を少量の二酸化炭素に替えて塗料の粘度を下げることで、VOCの発生を塗料中に含まれる有機溶剤(真溶剤)のみに抑え、VOC排出量を従来の1/3に削減する塗装技術です(図4)。
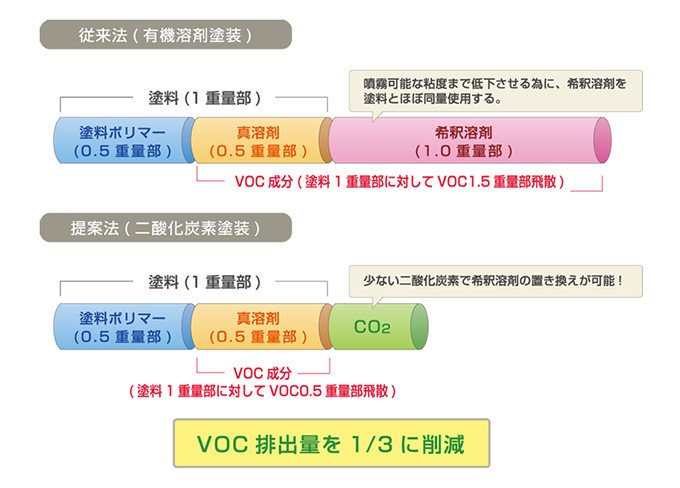
図4 超臨界二酸化炭素塗装法によるVOC排出量の削減効果
BREAKTHROUGH プロジェクトの突破口
二酸化炭素と相性のいい塗料を見定める
超臨界二酸化炭素の基礎技術は、産総研コンパクト化学プロセス研究センターにありましたが、塗装装置として実用化するには、解決しなければならない問題が山積みでした。
まずは、二酸化炭素適合塗料の開発でした。塗料を塗装に適正な粘度にするために圧力をかけた超臨界二酸化炭素を混ぜ合わせていきますが、その量も圧力も塗料の種類も手探りの状態でした。
同社技術開発室長の早坂宜晃さんは、「塗料開発の為には、膨大な種類の塗料から二酸化炭素と相性のいいものを探し出さなければならず、初めはトライアンドエラーの連続でしたが、ようやく相性のいい塗料や条件を見つけることができました」と振り返ります。その塗料を産総研コンパクト化学プロセス研究センター、宮城県産業技術総合センターに持ち込んで解析し、その理由を解明しました。
これをきっかけに、透明なクリア塗料から顔料入りカラー塗料へ、そして金属光沢のあるメタリック塗料へと徐々にステップアップしていくことができました。
また、塗料と二酸化炭素の混合方法の確立も重要な開発でした。最初は容器内でのバッチ方式で超臨界二酸化炭素と塗料を混合していましたが、量産工程を考え連続処理を行える混合方法の確立を目指しました。
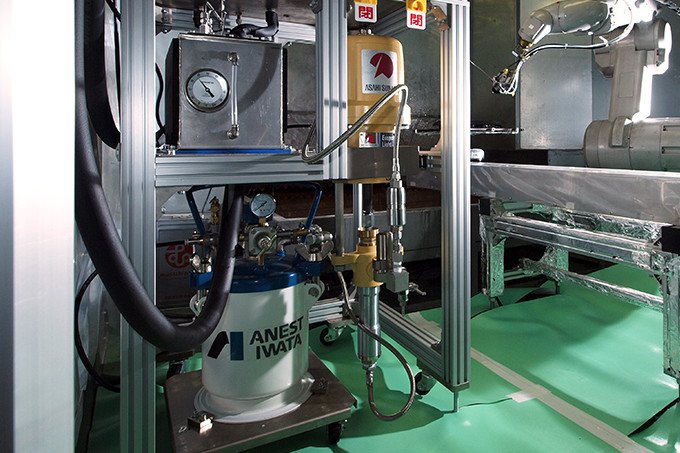
吹き付けユニットの塗料タンク
二酸化炭素と相性のいい塗料を見定める
ところが、連続処理を行うと塗料が混合器(ミキサー)で固まって詰まってしまうという不具合が起きました。早坂室長は、「当初、毎回実験しては混合器が閉塞するので、分解しては洗浄するの繰り返しでした」と話します。超臨界二酸化炭素が塗料と混合する時に、塗料中の樹脂成分を溶かし込んでいる有機溶剤を奪ってしまう為、貧溶媒化が発生し混合器中で樹脂成分が乾燥した状態になり、固体化して詰まらせてしまうのが原因でした(図5)。
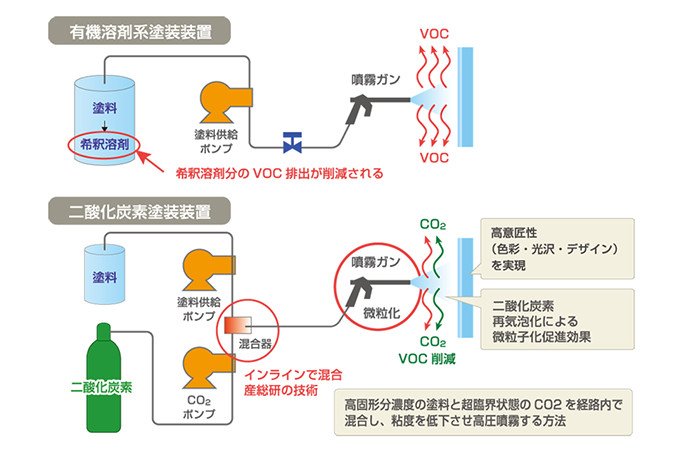
図5 有機溶剤塗装と二酸化炭素塗装の違い。混合器と噴霧ガンノズルの開発がポイントだった
温度や圧力などあらゆる条件を変えて検討を繰り返しましたが、なかなか改善されない日々が続きました。そこで、混合機の種類を変えてみることにしました。産総研コンパクト化学プロセス研究センターでは多種多様なタイプのマイクロミキサーを開発していて、その中から最適なタイプのマイクロミキサーを選定して使用したところ、超臨界二酸化炭素と塗料が瞬時に混合されることにより、詰まらずに噴霧することができるようになりました。
マイクロミキサーには、微少な空間で混合を行える、中心衝突型やスワール型などいろいろな種類があります。混合効率が極めて高いため、超臨界二酸化炭素と塗料を瞬間的に混合することができます。
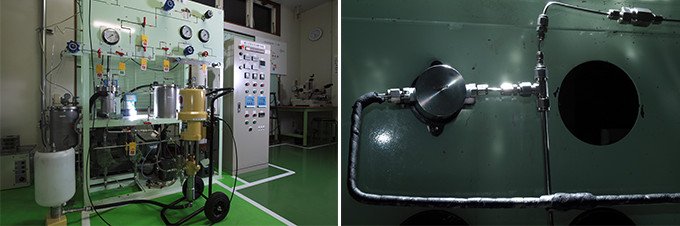
NEDOプロジェクトで研究開発に使用された試験機(左)と、マイクロミキサー(右)
ノズルも独自で開発
高圧で噴霧できる耐久性の高い極小口径ノズルの開発も大きな課題でした。加美電子工業で塗装しているプラスチック部品へは塗装の膜厚を薄くする為に、塗料の流量を少なくする必要があります。
二酸化炭素塗装は噴霧ガンで吹き付けるまで圧力を高く保たなければなりません。そのため噴霧ガンについているノズルは塗料流量が出ないように口径を0.1mm以下にする必要がありました。
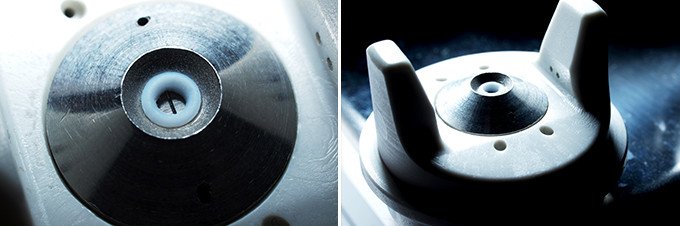
噴霧ガンのノズル部分
一方、メタリック塗料には金属のような光沢を出すためにアルミなどの無機物が含まれています。高圧で極小口径のノズルから、そうした塗料を噴霧すると無機物が研磨剤のようになりノズル口径を削ってしてしまい、極小口径を保つことができません。
耐摩擦性を持たせるためにノズルの材料を検討した結果、超硬を使用することにしました。ところが、超硬を削って極小口径のノズルを精密に安定して加工できる業者がいませんでした。「仕方無く、自分たちでノズルをつくることにしました」と早坂室長は語ります。
研究開発プロジェクトの産学官連携コーディネータを務めた産総研東北センターの小野實信さんは、「化繊メーカー用のノズルでもこれより口径が大きく、また、耐摩擦性を持ったノズルはありませんでした。しかし、まさか自力で開発するとは思いませんでした。加美電子工業のものづくりへかける思いの強さを感じました」と語ります。
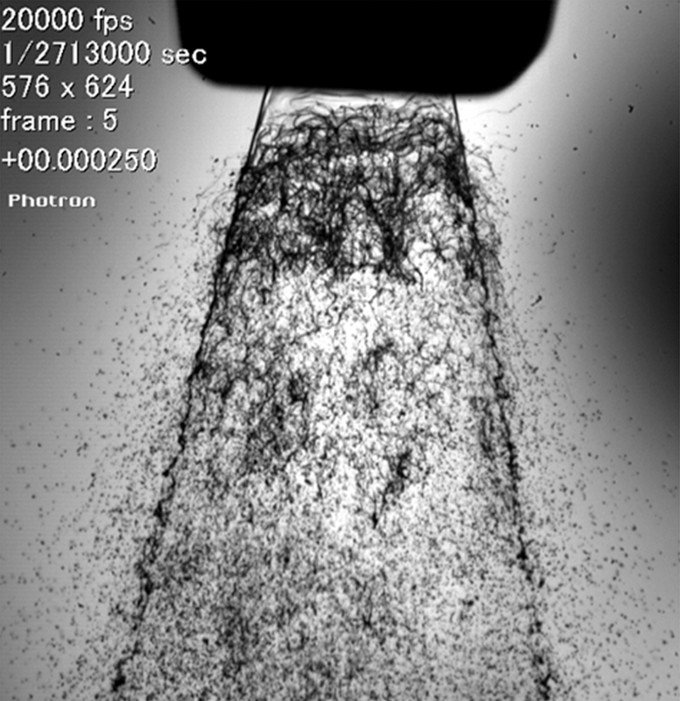
FOR THE FUTURE 開発のいま、そして未来
NEDOプロジェクト成果のおかげで、多くの企業との共同研究へ展開
超臨界二酸化炭素塗装の開発は、2007~2008年度のNEDO「有害化学物質リスク削減基盤技術研究開発」プロジェクトの一つとして実施されました。加美電子工業、産総研、および宮城県産業技術総合センターでは、プロジェクト開始から約1年でマイクロミキサーやノズルなどの主要技術を開発し、2年目にはバルブやロボットなど周辺技術の開発を行いました。
このような早いテンポで研究開発を進行できたのは、「産総研や宮城県技術総合センターなどの関係者の協力があってこそ」と早坂室長は言います。「さらにNEDOプロジェクトに採用されたことで、二酸化炭素塗装に適合した塗料の開発に対して、塗料メーカーの協力も得られるようになりました」とも話します。
また、早坂社長は、「プロジェクト実施中に開いたセミナーで、電機、光学、通信、自動車業界など大勢のお客様の前で話すことには苦労したものの、研究内容を評価してもらえることは励みになりました。研究経過を発表し、フィードバックをもらうと、この技術をなんとか使って貰わなければという気合いがこみ上げてきました」と語ります。
プロジェクト終了以降も多くの企業から共同研究の申し出があり、加美電子工業では、2010年までNEDOの支援を受けて、さらなる技術のブラッシュアップに努めました。その後も産総研や企業との共同研究を続け、超臨界二酸化炭素塗装技術の普及展開に努めています。
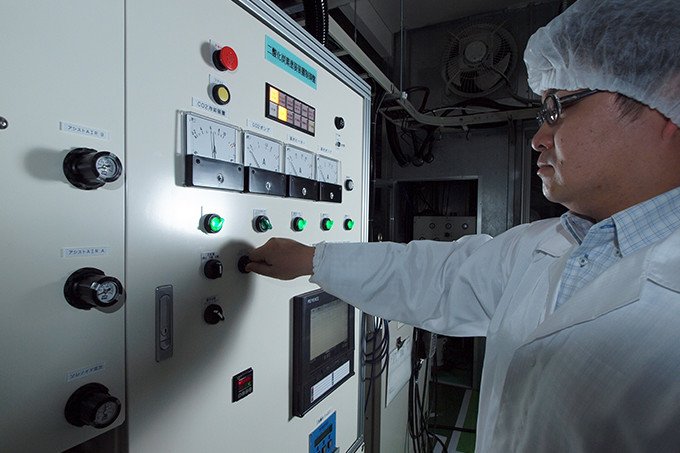
超臨界二酸化炭素塗装の普及に向けて装置の改良努力は続く
超臨界二酸化炭素塗装の数々のメリット
超臨界二酸化炭素塗装は、有害なVOCを排出しないばかりで無く、有機溶剤の代わりに工業用二酸化炭素を使用することでコスト削減にもつながります。実際のラインから算出した結果、加美電子工業での年間使用実績では有機溶剤塗装に比べ12%のコスト削減効果が推定されています(表1)。
また、水系塗装など他のVOCフリー塗装方法と比べても超臨界二酸化炭素塗装のメリットは数多くあります(表2)。早坂社長は、「VOCが削減できても塗装に二酸化炭素を使用すると、温暖化につながるのではとよく尋ねられますが、本システムに使用している二酸化炭素は発電所や工場などから排出される高濃度の二酸化炭素を圧縮して製造したもので、本来大気中に放出される二酸化炭素にもう一仕事してもらうことで、大気中に放出される二酸化炭素の排出量は増えません。また、二酸化炭素の圧縮にかかるエネルギーは、トルエン・キシレン等の有機溶剤を製造するエネルギーより少ないですし、石油資源を使用し ないことで温暖化が低減できると考えています」と説明します。
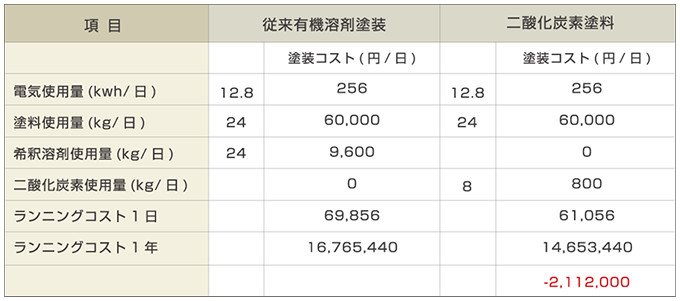
表1 加美電子工業での有機溶剤塗装と超臨界二酸化炭素塗装のコスト比較
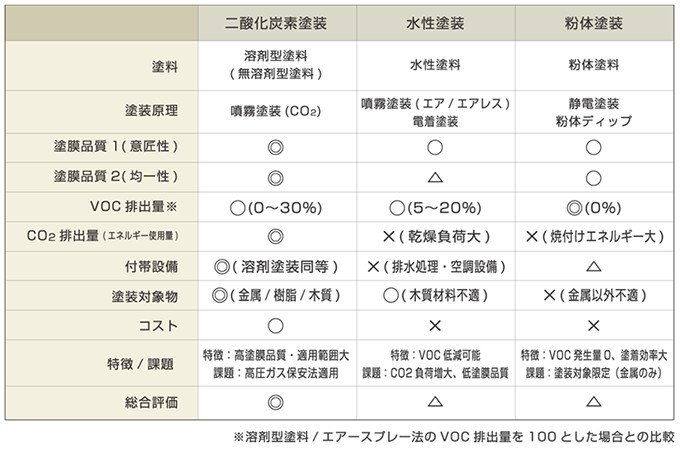
表2 他の低VOC塗装技術との比較
加美電子工業では今後、販売先からの評価を仰いで顧客満足度の向上に努めるとともに、精密加工品のノズルを安価に製造する工夫などを重ねて販売価格を下げる一方、自動車本体や家電製品、家具など多様な製品の塗装にも対応した装置を開発し、各業界へ積極的に売り込みを図っていく予定です。
有害化学物質への社会的関心や規制の網が強まるなか、VOCを削減し、エネルギー消費も少ない超臨界二酸化炭素塗装への注目度は、これからますます高まっていくことでしょう。(2011年12月取材)
開発者の横顔
東北発の技術を世界に広めたい
「私は好奇心が旺盛で、新しい人との出会いが大好きです」と話す早坂社長。代表を務める加美電子工業株式会社は1970年に宮城県加美町で設立された地元密着型の企業。その塗装技術は世界トップレベルで、国内メーカーのカメラや携帯電話の仕上げ塗装で大きなシェアを誇っているほか、海外の高級車メーカーとも取引があります。「加美町は静かな農村地帯。水田が広がる中にぽつりと立った工場では、地元の人が中心に働いています。もともと電子部品をつくっていましたが、地元の雇用を守りたいという思いに加え、新しいものをつくりたいという気持ちから塗装加工へと転身しました。これからは、超臨界二酸化炭素塗装を東北発の技術として世界に広めたいと意気込んでいます」
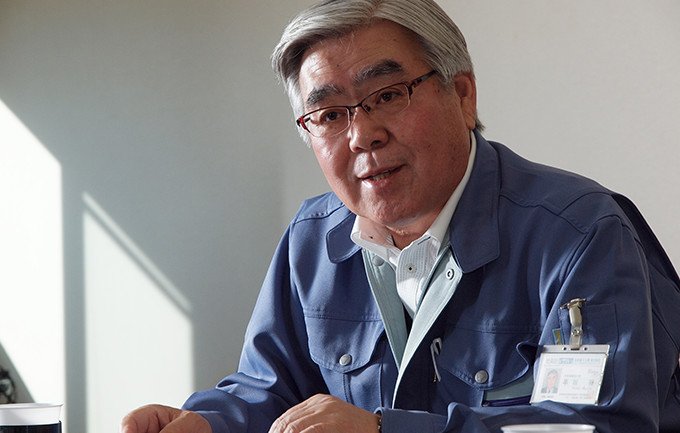
加美電子工業株式会社
早坂さん
なるほど基礎知識
液体でも気体でもない超臨界流体
物質には、固体、液体、気体の三つの状態があります。物質がどの状態にあるのかは、一般的には温度と圧力で決まります。水でいえば、温度を上げていくと氷が水になり、さらに水蒸気になります。また、圧力をかけると氷は溶け、高山に行けば大気圧が小さくなるため、水は早く沸騰し、気体になります。
温度と圧力を上げ、ある点になると液体と気体の密度が同じになります。その点を臨界点といい、臨界点を超えると、物質は液体とも気体とも区別のつかない状態になります。その状態を「超臨界流体」と言います。超臨界流体は、液体のような溶解性と気体のような拡散性を併せ持ち、通常の液体や気体とは違う性質を持ちます(図a)。
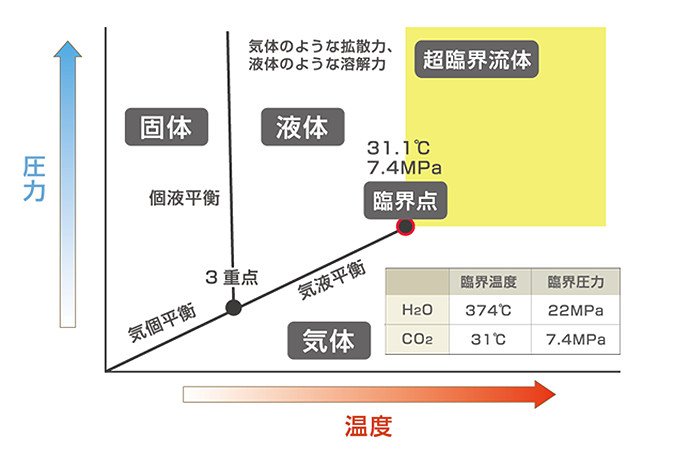
図a 物質の状態。臨界点を超えた部分が超臨界流体
二酸化炭素は、温度が31.1℃、圧力が72.8気圧と、比較的低温・低圧で超臨界状態となるため、工業用によく使用されます。圧力と温度を操作して、二酸化炭素を超臨界流体にすると、通常は溶解しない物質も溶解します。
溶解させた後、圧力を下げて臨界点以下にすると、二酸化炭素は気体となるので溶解した物質を簡単に分離させることができます。このプロセスを利用して、物質の抽出を行うことを「超臨界抽出」と言い、コーヒーからカフェインを取り除いたり、天然物から香料を取り出したりと様々な産業に応用されています。
NEDOの役割
「有害化学物質リスク削減基盤技術研究開発」
このプロジェクトがはじまったのは?
化学物質の製造から、利用、廃棄まで適切な管理を行うことが、世界の潮流になってきています。とくに、人の健康や生態系に影響を及ぼす恐れのある化学物質については、そのリスク低減が欠かせません。わが国では、「特定化学物質の環境への排出量の把握等及び管理の改善の促進に関する法律」(化管法)に基づいたPRTR制度(環境汚染物質排出移動登録)や、「化学物質の審査及び製造等の規制に関する法律」(化審法)の改正により、有害化学物質のリスク低減を図ってきました。また、2006年から、改正大気汚染法が施行され、揮発性有機化合物(VOC)についても排出規制が敷かれました。こうした中、従来から事業者の間で実施されてきた自主規制や化学物質管理をより促進し、有害化学物質のリスクを低減するための安価な回収、無害化、代替品等の技術開発を目的にプロジェクトが開始されました。
プロジェクトのねらいは?
このプロジェクトでは有害化学物質のなかでも、主に光化学スモッグなどの発生原因となり、大気を汚染するVOCの使用及び排出を削減することがねらいでした。環境省が実施したシミュレーションの結果では、2000年度のVOC排出量は146.5万tで、光化学オキシダントおよびSPMの目標を達成するためには、2010 年度までに2000 年度比でVOC排出量を3割削減する必要があるとされました。そのため、1)工場などから排出される際(煙突、排水等)に有害化学物質を抑制、回収、無害化する新技術、2)工場内の製造プロセスや製品への有害化学物質の使用を削減、廃止、代替する新技術、3)そのほかに、有害化学物質のリスクを低減させるソフトウエアやシステムを開発することがプロジェクトの目標となりました。
NEDOの役割は?
有害化学物質のリスク低減技術の開発は、社会的必要性も大きく国家的な課題でもあります。その成果は、国民の環境と調和した健全で安全、安心な生活にもつながります。環境中に一旦排出された化学物質や、それを含んだ製品の回収、無害化処理は、産業界による取り組みだけでは極めて困難です。また、技術的な対応策が無いこと、費用がかさむことを理由に、自主管理が滞ることも予測されます。そこでNEDOでは、化学物質の使用から廃棄までを管理し、有害化学物質の使用を削減、廃止するための技術開発を支援することとしました。支援に当たっては、NEDOの有害化学物質のリスクに関する知識や技術開発の実績を活かしてプロジェクトを進めてきました。
関連プロジェクト
お読みいただきありがとうございました。
ぜひともアンケートにお答えいただき、
お読みいただいた感想をお聞かせください。
いただいた感想は、
今後の連載の参考とさせていただきます。