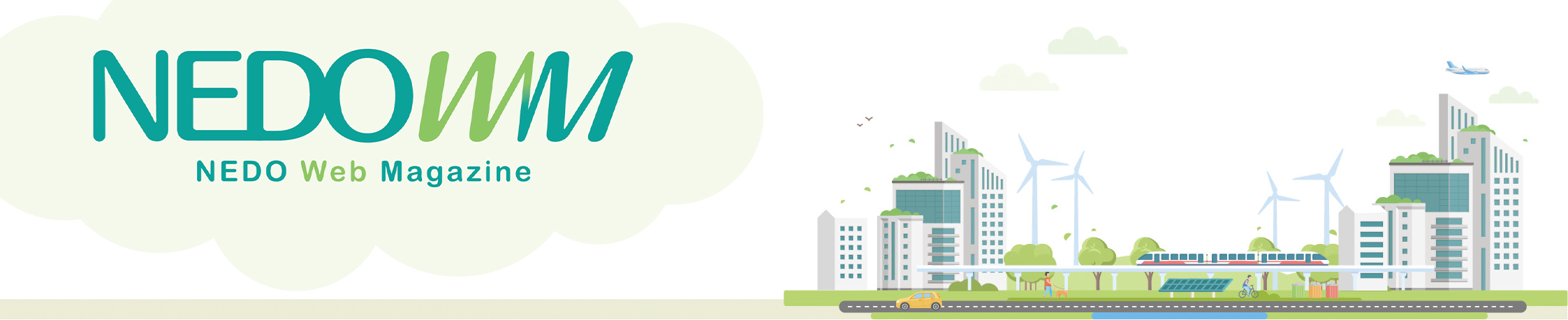
CONTENTS
INTRODUCTION
100インチ以上の巨大画面同サイズ従来方式ディスプレイの消費電力1/2
BEGINNING
"関空"に出現した新方式の大型ディスプレイ装置
BREAKTHROUGH
プロジェクトの突破口FOR THE FUTURE
目標を高く設定したことが、世界トップレベルの製品を実現
FACE
プラズマチューブアレイに惚れ込んでINTRODUCTION 概要
100インチ以上の巨大画面
同サイズ従来方式ディスプレイの消費電力1/2
(従来の100インチ級プラズマディスプレイで500W/m²現状プラズマチューブアレイ製品で200W/m²、目標値150W/m²)
映像ディスプレイ装置は厚みのあるブラウン管方式から、薄型のプラズマ方式や液晶方式へと変遷し、画面サイズも大型化の一途を辿ってきました。しかし、100インチを超えるような巨大画面の製造やディスプレイを曲面にするのは難しいことでした。例えば、液晶ディスプレイでは、画面の巨大化に合わせて製造装置も大型化する必要があるほか、曲面状態のディスプレイを製造することは製造原理上、困難です。さらに、巨大化に伴う重量や消費エネルギーの増大も課題です。兵庫県神戸市のベンチャー企業・篠田プラズマ株式会社では、NEDOの支援を得てこうした難点を克服し、超大型画面でも軽量で消費エネルギーも少ない映像ディスプレイ装置の開発に成功しました。新技術の「プラズマチューブアレイ(PTA)」方式による、観る人を包み込むような100インチ超の巨大な曲面ディスプレイは、すでに空港ロビーや美術館など全国8か所に設置されているほか、見本市等の展示会場でも活用されつつあります。
BIGINNING 開発への道
"関空"に出現した新方式の大型ディスプレイ装置
関西国際空港のターミナルビル3階の出国エリア免税店街に、一風変わった超大型映像ディスプレイ装置が設置されています。ディスプレイ装置の大きさは、3m×4m(200インチ)。画面には日本の観光地や産業を、海外からの渡航者へPRする映像が流されています。
このディスプレイ装置は縦に曲げられているのが特長で、足下からせり上がるように曲面を描いています。従来の大型ディスプレイや、複数のディスプレイを組み合わせたマルチディスプレイでは考えられない形と大きさの巨大画面です。
これを可能にしたのが、篠田プラズマが開発した新技術「プラズマチューブアレイ(PTA)」です。プラズマテレビの原理を応用して、細いガラス管を発光させることで映像を表示します。従来のディスプレイ装置より軽量に大画面を実現できるほか、ガラス管を並べるスダレのような構造から、曲面状の画面も自在につくり出すことができます。
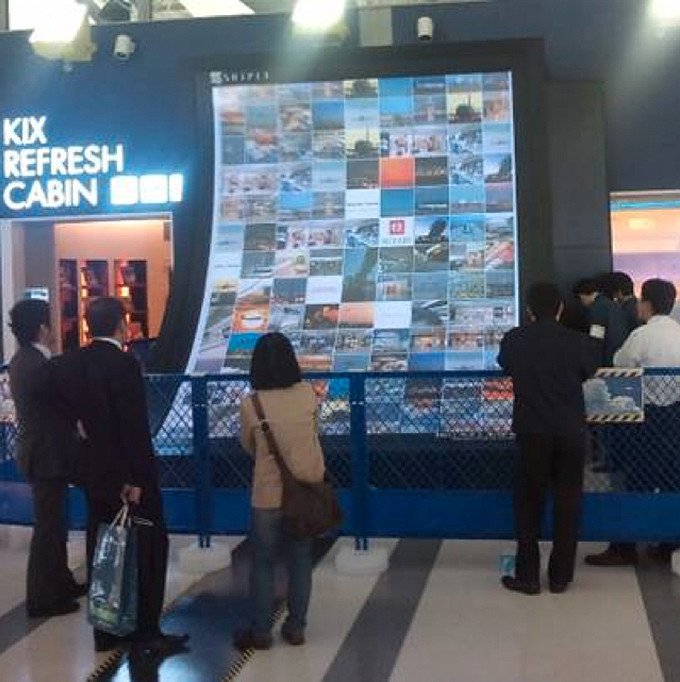
関西国際空港3階出国エリアに設置された曲面巨大ディスプレイ
人間が等身大に映るリアリティのある映像世界を表現したい
篠田プラズマでは、PTA技術により、2009年に屋内向けの150〜300型の曲面ディスプレイ(製品名:SHIPLA)を実用化。同年9月には、東京駅でJR東日本企画と共同でデジタルサイネージの実証実験を実施、11月には兵庫県の明石市天文科学館に常設使用されることになりました。
天文科学館では、惑星や銀河などの映像が巨大画像で映し出され、子どもから大人まで宇宙を体感することができます。画面サイズは3m×2m(145インチ)の曲面で、表示部分の質量だけなら7.2kg、表示部の横・裏に装備された制御装置、セットフレームなどを含めても約180kgと画面の大きさからは考えられないほど軽量です。
液晶やプラズマテレビなど従来方式のディスプレイ装置で同様の大きさを実現しようとすると、重さが1t近くになり、床面の補強が必要な上、消費電力も2,500Wを超えてしまいます。PTA方式なら、重量だけでなく消費電力も1,200Wに抑えることができます。さらに、大型の製造設備が不要なため、製造時の消費電力も大幅に削減できます。
こうした超大型映像ディスプレイ装置の開発は、1998年、同社の篠田傳代表取締役会長兼社長が、富士通に在籍していた当時から始まります。篠田社長は、世界で初めてフルカラープラズマディスプレイを実用化させた開発技術者で、50インチの大型プラズマテレビを誕生させた後、さらに大型の巨大ディスプレイの開発を構想しました。
「人間が等身大に映り、リアリティのある映像を映し出すことができれば、例えばニューヨークの街並みの映像を見て、まるでそこを旅行しているかのような気分を味わえるのでは……。また、取引先の会議室を映し出せば、実際に同じ場所に居るように、ビジネスの打ち合わせをすることができるのでは……」
篠田社長は将来のネットワーク社会も見据え、「人と人、人と環境をリアルな映像で結び、多くの人々に映像を通して様々な世界を、労する事なく心から楽しんでもらいたい」と巨大ディスプレイの開発に取り組み始めました。
しかし、従来のプラズマディスプレイの技術では重量と消費電力が大きくなり過ぎ、広く市場に受け入れられない製品となってしまいます。それを克服するには、これまでとは全く異なる新技術の開発が必要でした。それが「プラズマチューブアレイ(PTA)」です。
新方式を考案も会社が事業撤退、ベンチャー設立で製品化へ挑む
「プラズマチューブアレイ(PTA)」方式のディスプレイ装置の基本的な構造は、チューブ状の発光素子をつくり、それを並べたガラス管に電極フィルムを貼り合わせて、超大型画面にするというものです。
篠田社長ら開発チームは2000年初めに極細のガラスチューブにそれぞれ赤・青・緑の蛍光体を塗りつけて放電ガスを封入し、3色を順に並べてそれを表示電極の付いた樹脂フィルムで覆うことに成功、2003年には、蛍光体が入った1mmチューブを1,000本並べて1m四方の大きさにした「PTAディスプレイ」の試作・動作確認まで至りました。
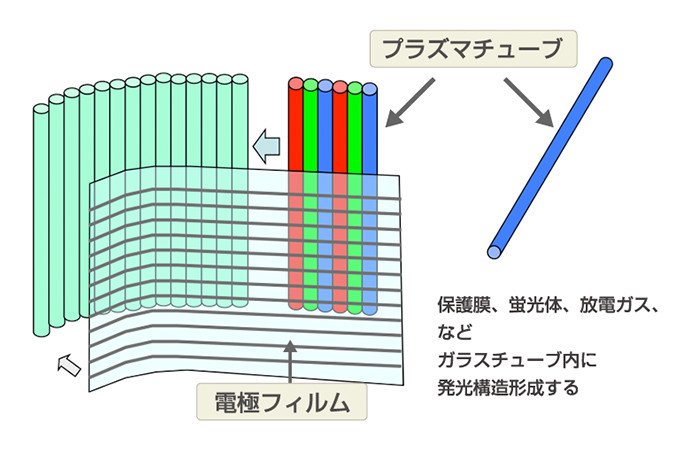
図1 PTAディスプレイの基本的な構造
ところが、2005年、いよいよ実用化へ向けた製品開発に取り組もうという段階で、富士通ではプラズマテレビ事業からの撤退が決定してしまいました。しかし、PTA方式に将来性があると確信していた篠田社長らはそこで諦めず、同年、篠田プラズマ株式会社を兵庫県神戸市のポートアイランドに設立しました。
2007年には富士通で研究開発した新技術の特許や開発設備などを買い取り、富士通の開発チームメンバーの転籍も完了、NEDOのテーマ公募型制度「エネルギー使用合理化技術戦略的開発」に採用され、いよいよ製品化に取り組むこととなりました。
篠田プラズマの開発チームでは、「作る時も、使う時も、省エネルギー」を開発コンセプトに、150インチの超大型ディスプレイで、従来のプラズマディスプレイの1/3の消費電力、1/10以下の製造エネルギーを実現することを目標としました。
富士通の開発チームのメンバーで、現在は篠田プラズマの主監を務める、粟本健司さんは、「世界一小さな工場から、世界一大きなディスプレイが生まれる。それを実現できれば素敵じゃないかと開発メンバー全員で夢見ました」と当時を振り返ります。
プラズマチューブの開発
従来のプラズマディスプレイでは、蛍光体を封入するためにガラス板を使用します。しかし、ガラス板を曲げることは難しく、富士通で開発を始めた当初はフィルムを用いて曲面をつくり出すことも考えました。ところが、フィルムをガラス板と同様に用いると、わずかな水分が浸入して蛍光体を汚染してしまうことがわかりました。
そこでやはり蛍光体はガラスに封じ込めることにしました。そしてガラス板の代わりに細いチューブを敷き詰め、フィルムで覆うことで画面を巨大化する方式が考え出されました。
篠田プラズマでは、NEDOプロジェクトにあたり、この蛍光体を入れる細いガラスチューブの量産化技術の確立から着手しました。できるだけ細いガラスチューブをつくることができれば、それだけ薄く、かつフレキシビリティのあるディスプレイ装置を実現することができます。富士通時代にも試作していたとは言え、150型を実用化するには、1回の試作用だけでも1,000本以上のガラスチューブが必要で、量産化技術の確立は急務でした。
そして篠田プラズマではプロジェクト開始からおよそ12ヶ月で、目標の直径1mm、長さ1mのガラスチューブと、その細いガラスチューブ内面に蛍光体膜を形成する量産化技術の確立に成功しました。
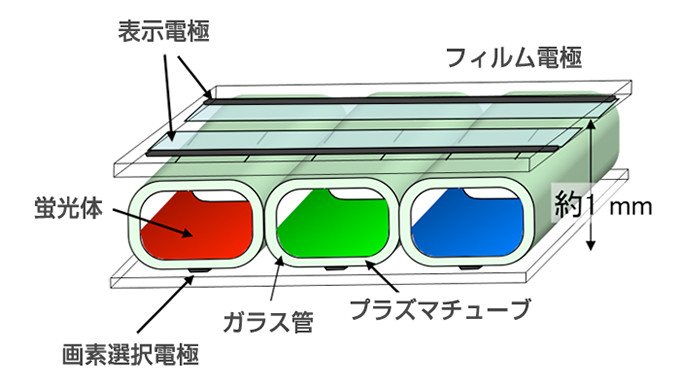
図2 PTAディスプレイの基本構造。チューブは発光効率を考えて、あえて正円形でない形状になっている
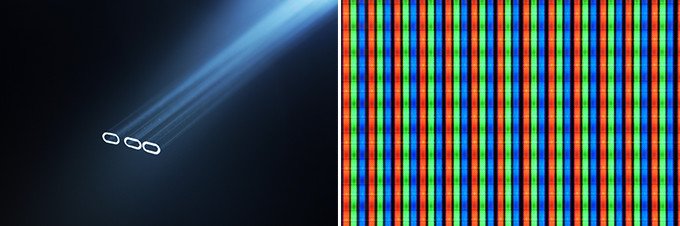
PTAで実際に使用されている直径1mmのガラスチューブ(左)
3色の蛍光体が塗られたガラスチューブの発光状態。左右に走る帯がチューブを発光させる表示電極(右)
自由度が高く、作りやすいPTAディスプレイ
PTA方式で作るディスプレイ装置はガラスチューブの長さに合わせて1m角の大きさでモジュール化されていて、モジュール数を増減することで、任意の大ききの超大型ディスプレイ装置を、設置現場で簡単に組み上げることができます。モジュールは、既存方式の同サイズのディスプレイ装置に比べて、極めて薄く、軽量なため、運搬や設置工事が容易なことも、他のディスプレイ装置にない特色です。また、チューブの並べ方次第でフレキシブルに曲げることが出来、円柱状はもちろん、S字状のような複雑な曲面のディスプレイ装置も製造することもできます。
ガラス管を並べて貼り付ける方式のPTAディスプレイは、製造時にも液晶やプラズマディスプレイ装置にはない大きな特色があります。従来のディスプレイ装置では、大画面を作るためにはそのサイズに合わせた大きなガラス基板が必要で、製造設備も大型化する必要がありました。それに対してPTAディスプレイには大きなサイズの部品がなく、モジュールも1m角のため、大型の製造設備を必要としません。
さらにガラスチューブと電極フィルム貼り合わせるとき以外は、ホコリの影響を受けることも少ないため、電力を大量に使うクリーンルームも不要です。工程数も従来のプラズマディスプレイの半分程度で、熱を加える工程も少ないため、製造エネルギーの大幅低減が可能です。
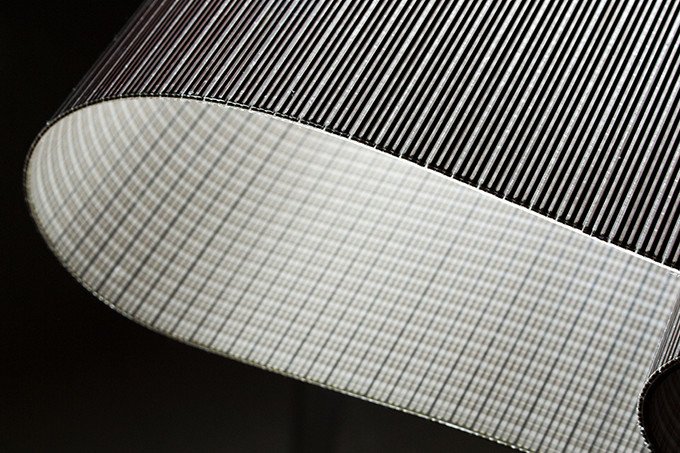
太さ1mmのガラスチューブを電極フィルムで貼り合わせた表示画面シートは、薄く、軽く、その自由度は高い
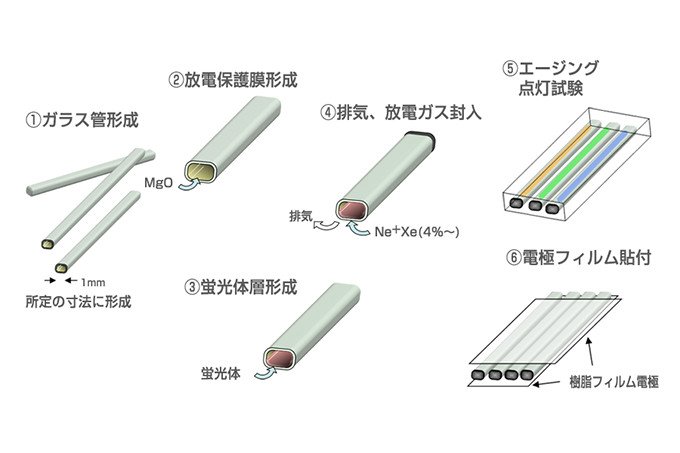
図3 プラズマチューブアレイの製作工程
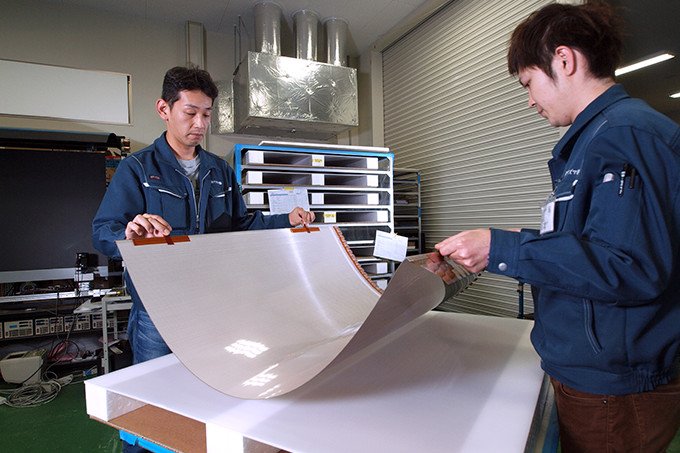
篠田プラズマの工場内。
ガラスチューブと電極フィルムの貼り合わせが終わった表示部のシート。大きさや重さがある部品がないこと、クリーンルームでの作業が必要ないことなどから、超大型ディスプレイでも、製造時のエネルギー削減が可能になる
BREAKTHROUGH プロジェクトの突破口
篠田プラズマの開発メンバーはPTAディスプレイの開発について、富士通時代から多くのノウハウを蓄積していましたが、開発目標の省エネルギー化実現には、新たに取り組むべき課題も多くありました。その代表例がエネルギー損失の低い電極フィルムと駆動方式の開発でした。
明るい映像と省エネルギーを両立する電極フィルム
プラズマチューブに貼り付ける電極フィルムには、映像を映し出すために信号を送る金属パターンを形成する必要があります。2007年12月に、まず格子状に金属を引いた金属メッシュ電極を試作しましたが、コーナーや線幅が太く、光が遮られて表示される映像が暗くなってしまいました。また、電気抵抗が大きいために多くの電力がこの電極で失われていることが確認されました。
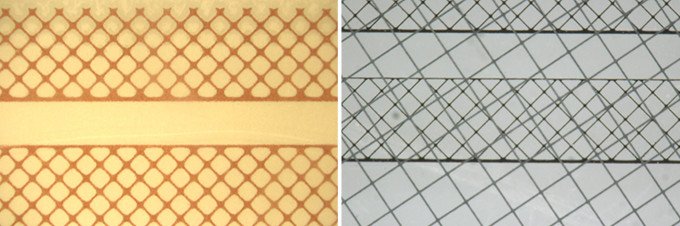
2007年12月に試作された金属メッシュ電極(左)と、75%の開口率と25Ω/mの線抵抗率を実現した金属メッシュ電極(右)
輝度を上げ、抵抗を小さく、明るい映像と省エネルギーを両立するためには、金属メッシュを細くする必要がありました。試作フィルムでは金属薄膜をフィルムに貼り合わせ、型を抜く方式で、金属メッシュ電極を作っていましたが、この方法では線を細くすることに限界がありました。
そこで抜き方を工夫し、細線化に成功。また、透過率を上げるために金属を薄くすることも検討しましたが、敢えて厚みをある程度持たせることで線抵抗率の値を下げることができました。最終的には75%の開口率と、25Ω/mという初期の試作フィルムの1/5程度の線抵抗率を実現することができました。
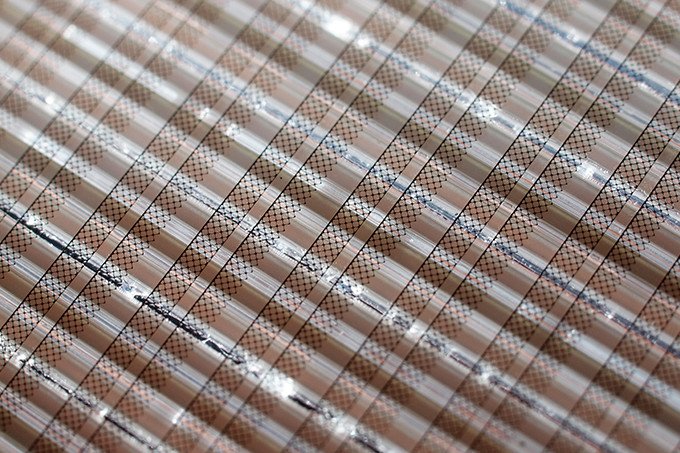
プラズマチューブと貼り合わされた金属メッシュ入り電極フィルム
駆動方式に現れた大きな電力ロス
ディスプレイが映像を映し出すには、その信号を制御する駆動方式も必要です。この駆動方式を損失の少ないものにすることも、省エネルギー化の大きな課題でした。実用化に向けて大画面ディスプレイを試作して動作させてみると、計算上の2倍もの電力が消費されていました。
粟本さんは、「実用化に向けて装置を大型化すれば、課題が出ることは予想できましたが、何が問題になるかは実際に作ってみなければわかりませんでした。大型化で駆動方式に隠れていた電力ロスがはっきりと見えるようになりました」と語ります。
電力損失の原因を探るため、まず回路上に問題はないかを確認しましたが、特に問題は見当たりませんでした。「そこで、装置の分解と組み立てを繰り返しながら実験し、他の原因を探りました」(粟本さん)
その結果、電極フィルムとガラスチューブを接着する接着材に問題があることがわかりました。電圧の上げ下げを繰り返す交流パルスを流すと、接着部分の絶縁体に電気が分極して溜まり、その後、その電気が全て失われてしまっていたのです。
接着剤は厚みに合わせて電気を溜めてしまうため、強度を確保しながらも、薄く接着できるもの、さらに誘電率が低いものへと変更しました。また、共振条件を満たすコンデンサーとコイルから成る電力回収回路を駆動方式に取り入れることで、接着部分に溜まっている電気をそのコンデンサーで回収できるようにして、電気を再利用できる仕組みを作り出しました。この原理は従来のプラズマテレビでも利用していますが、電気特性やサイズが全く違うPTAにそのまま適用しても共振条件を満たさず、動作しないため、PTAそのものの電気特性と回路設計を合わせて見直し、最適化しました。
このような駆動方式の改良で、150型ディスプレイでの電力回収効率を50%程度から90%まで向上することができました。1㎡当たり200W(従来のプラズマディスプレイならば500w)まで消費電力を抑えることができるようになり、開発目標通り、エネルギー効率の高い超大型ディスプレイを実用化することができました。
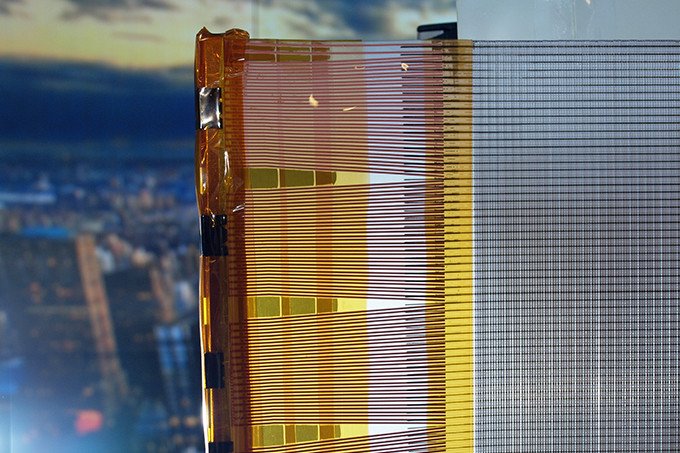
表示部の端には、ガラスチューブに信号を送る大量の電線がつながっている
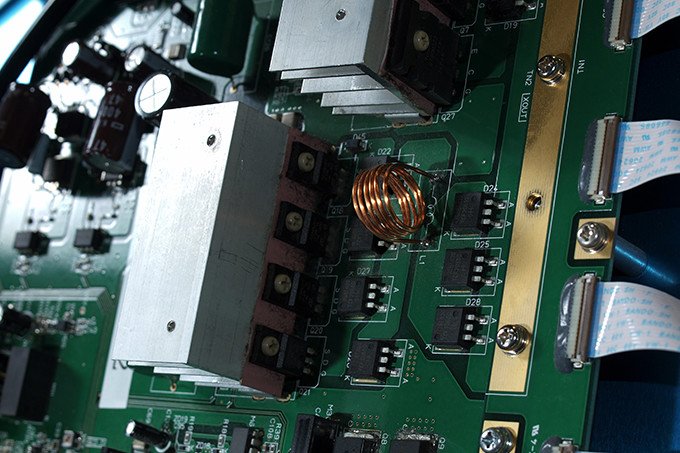
駆動方式に共振条件を満たすコイルとコンデンサーを組み込んだ基板。失われていた電気はここに蓄積し、省エネルギー化を実現した
FOR THE FUTURE 開発のいま、そして未来
目標を高く設定したことが、世界トップレベルの製品を実現
粟本さんは、ベンチャー設立から実用化までの道のりを振り返り、NEDOプロジェクトに応募した際に掲げた高い目標が研究開発に弾みを付けたと話します。
「高い目標を設定するとリスクが高くなり、先に進まないかと言えばそうではなく、必死に人は考えるものです。ほどよい目標を上げてしまうと、かえって研究開発はうまく行かないのが現実です。プロジェクトの申請書を書く中で考えて、考え抜いたことで、実用化に必要な研究アプローチをいくつも思いつくことができました。その結果、世界トップレベルの製品を誕生させることができたと思っています」
実際の研究開発ではつくっては壊しの連続でしたが、実用化を掲げたプロジェクトだからこそ、製品化につながる試行錯誤を思う存分に行うことができたと、粟本さんは言います。「プロジェクトの成果を、今後の量産化や低価格化にも大いに活かせると考えています。なにしろ、もうたくさんだと言いたいほど、プロジェクトでは試行錯誤を繰り返しましたから、後は実践するだけです」
市場創出と量産体制での省エネルギー生産設備実現
篠田プラズマのPTAディスプレイは2009年に製造ラインを始動し、設置場所や利用先も徐々に広がってきていますが、まだ受注生産が主で、本格的な量産のための新規用途開拓にも積極的に取り組んでいるところです。
NEDOプロジェクトの評価委員会で、マーケティングの専門家から"従来とは違う市場で"と指摘されたことで、PTAディスプレイには研究開発だけでなく市場創出の努力が必要なことを強く意識させられたと粟本さんは言います。
PTAディスプレイは大きさも形状も自由度が高く、視野を覆うような曲面表示や超ワイド表示、柱への巻き付け、天井や床への埋め込みなど、これまでのディスプレイ装置では考えられなかったような設置・利用方法も可能です。従来通りの映像表示装置としての使用法ばかりでなく、急速な成長が予測されているデジタルサイネージ(電子看板)などでの利用拡大にも期待がかかります。
また、年間数千〜数万m²の生産規模での生産が必要になれば、さらなる低エネルギーでの量産技術も、今後の課題となってきます。
PTAディスプレイでは、前述した「超軽量チューブ、小さな製造単位、クリーンルーム不要」に加えて、プロセス処理密度の向上や装置熱容量を低減して熱効率を改善して、製造時の省エネルギー化が図られています。
その結果、現状の生産規模では、従来のプラズマディスプレイの1/10である50kWh/m²の生産体制が実現しています。大量生産体制でも現在の数値を維持することができれば、「作る時も、使う時も、省エネルギー」という開発コンセプトが文字通り達成されたことになります。
PTAディスプレイの巨大画面が映し出すリアリティ溢れ、没入感のある映像は、見る人に新鮮な驚きを与えます。これから様々な場所や場面で利用されるようになり、多くの人が体験したことのない、新しい映像表現や感動を提供していくことになるでしょう。(2011年12月取材)
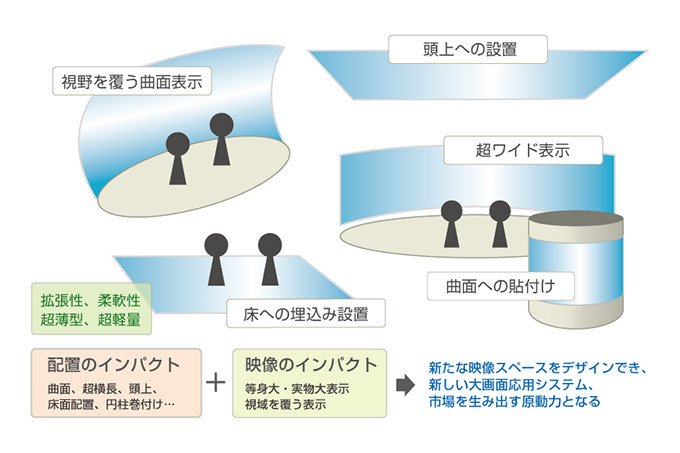
図4 PTAが創り出すディスプレイ装置の新市場

「ENEX 2012」でNEDO成果として展示された円筒形のPTAディスプレイ
開発者の横顔
プラズマチューブアレイに惚れ込んで
粟本さんがディスプレイ装置の研究開発に関わるようになったのは、富士通在籍当時の1996年から。それまでは、気象衛星の赤外線カメラや暗視装置の開発に従事していましたが、「自分の関わった製品が一般社会に広く浸透して、人々が喜んでいる姿を自分の目で見てみたい」と、42型プラズマディスプレイの開発メンバー募集に手を上げました。
その後、プラズマチューブアレイ(PTA)の技術開発にも加わり、その将来性に惚れ込んでいた粟本さんは、会社が事業撤退を決めると、「このままで止めたくはない。この技術は絶対に成功させてみせる」と退職を決意。上司だった篠田傳社長が設立した篠田プラズマに転籍して、PTAディスプレイの研究開発を続けました。
「将来性がある新技術ができたという感触は、研究開発を続けていてもめったに感じられないこと。今、夢見ているのは、SHIPLAを自宅の専用部屋に置いて、好きな映像を流しながら、美味しいお酒を飲むこと。そのためにも、引き続き、量産化、低価格化にも挑んでいくつもりです」
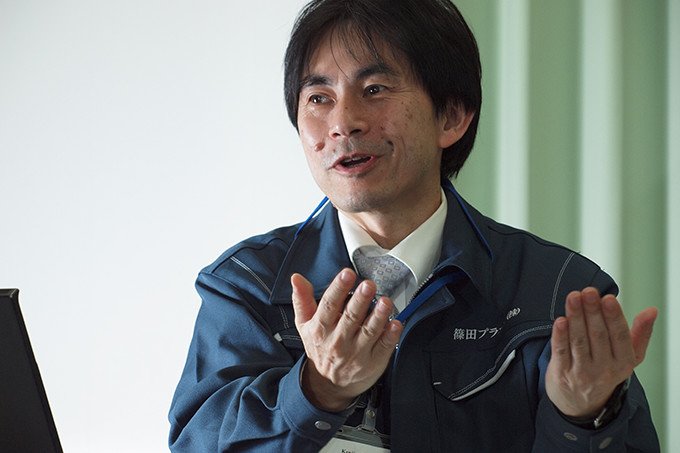
篠田プラズマ株式会社
粟本さん
なるほど基礎知識
液晶、プラズマ、有機EL、ディスプレイの違いとは
薄型ディスプレイには、液晶、プラズマ、有機ELなど色々な方式がありますが、それぞれ何が違うのでしょうか。
ディスプレイ装置に映像を映し出すためには、表示装置から送られてくる映像の電気信号を光に変換する物質が必要です。この物質を何にすれば、安定した美しい映像を映し出せるか、装置を薄くできるか、また曲げることはできるかといったことが、研究開発されてきました。
この変換物質の違いが、ディスプレイの違いになっています。液晶ディスプレイは液体と固体の間の状態の物質で、プラズマディスプレイは気体と蛍光体で、有機ELは固体の変換物質を媒体にしています。
ディスプレイの特性は、変換媒体の種類とその動作、電極マトリクスの構成・動作により決まります。例えば、プラズマディスプレイでは、 パッシブ・マトリックス電極+気体(放電・発光)+蛍光体(カラー変換)で映像を表示しています。プラズマディスプレイは、自発光型のディスプレイで視野角が広い、応答速度が速いなどの特色があります。
篠田プラズマが開発したプラズマチューブアレイ(PTA)は、プラズマディスプレイと発光の仕組みは同じですが、プラズマディスプレイがガラス板の間に気体と蛍光体を封入・形成するのに対して、PTAではガラスチューブに気体と蛍光体を封入・形成させる点が大きく異なります。
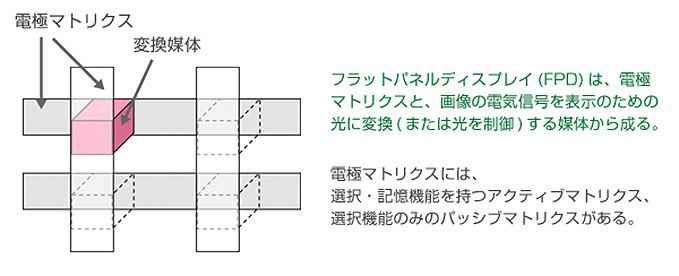
図5 フラットパネルディスプレイの構造概念
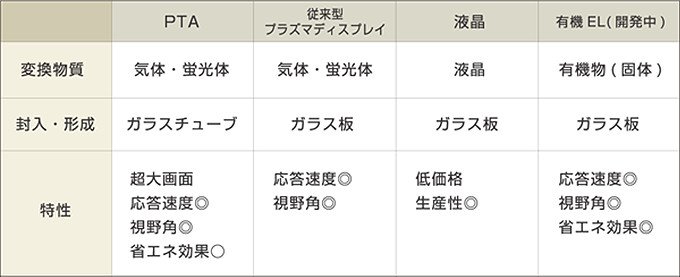
表 フラットパネルディスプレイの構造と特性の比較
NEDOの役割
「省エネルギー超薄型大画面フィルム型自発光表示装置の研究開発」プロジェクト
このプロジェクトがはじまったのは?
画面の大型化や輝度の向上により、薄型ディスプレイ装置は、従来のテレビ やパソコンモニターといった使い方だけでなく、デジタルサイネージ(電子看板)や、ディスプレイの向こうに別空間が広がるような環境型ディスプレイとしての用途拡大が期待されています。それには、人が等身大で表示できるような巨大画面が必要となってくると考えられます。しかし、既存のディスプレイ方式による大画面化では、サイズ拡大に伴う重量やエネルギー消費の増大が避けられません。そこで、薄さだけではなく、これまでにない超大画面でもリアルな映像を表示し、なおかつ軽くて曲げることもできるような、新しいディスプレイ装置の実用化を目標に、本プロジェクトは開始されました。
プロジェクトのねらいは?
従来方式の薄型ディスプレイでは、画面を大型化すると、使用時の消費電力や製造時のエネルギーも大きくなります。150型の場合、使用時消費電力で3,000w、製造時エネルギーで8,000kwhにもなってしまいます。そこで、本プロジェクトでは、わが国発の新技術である「プラズマチューブアレイ(PTA)」方式を用いて、超大画面でも大幅に省エネルギーが可能な新技術の開発を目指しました。150型で、使用時消費電力を従来方式の1/3以下、製造時エネルギーを同じく1/10以下にすることが開発目標でした。
NEDOの役割は?
PTA方式は将来性のある技術である一方、巨大ディスプレイ装置の市場は、まだ小さく、充分に成長していないため、研究開発のリスクがある中で開発資金の調達を行うことは困難な状況にあります。NEDOでは、本プロジェクトにより、超大型ディスプレイの低消費電力化、製造時の省エネルギー化を支援することで、従来の薄型ディスプレイとは異なる、競争力の高い国内新規産業の育成を目指しました。
関連プロジェクト
- エネルギー使用合理化技術戦略的開発/エネルギー使用合理化技術実用化開発/省エネルギー超薄型大画面フィルム型自発光表示装置の研究開発(2007〜2009年度)
- 省エネルギー革新技術開発事業 先導研究 省エネルギー・フイルム型超大画面プラズマチューブアレイの超高精細化技術の研究開発(2010-2011年)
お読みいただきありがとうございました。
ぜひともアンケートにお答えいただき、
お読みいただいた感想をお聞かせください。
いただいた感想は、
今後の連載の参考とさせていただきます。