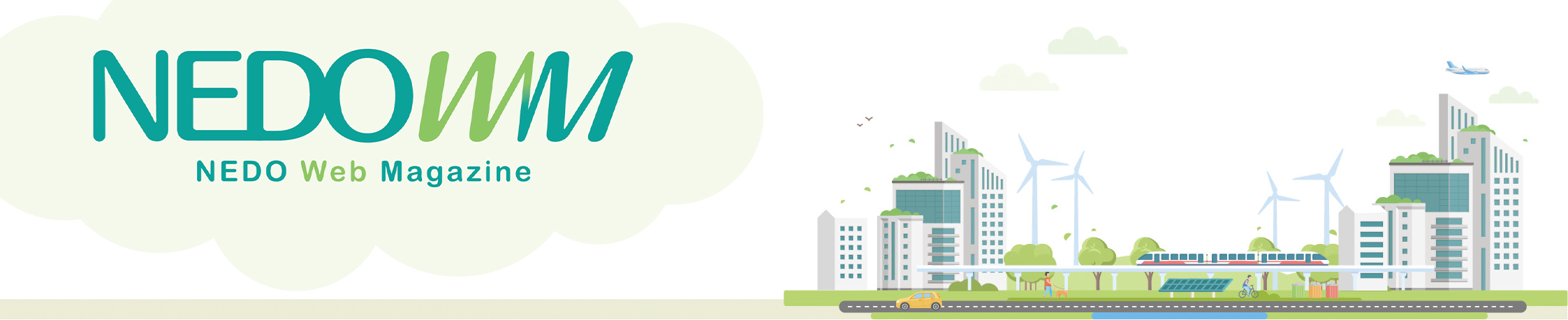
CONTENTS
INTRODUCTION
集積回路の消費電力1/2処理性能100%アップ
BEGINNING
従来の半導体製造装置が抱える問題BREAKTHROUGH
衛星放送受信用のアンテナを、半導体製造プラズマ励起に応用
FOR THE FUTURE
チャンバ内の表面加工と排気ポンプFACE
半導体立国再興の扉を開けるINTRODUCTION 概要
集積回路の消費電力1/2
処理性能100%アップ
パソコンや携帯電話などの情報通信機器はもちろん、家電製品から自動車に至るまで、ほとんどのものに搭載されている「半導体」。今ではシステムLSIなど「集積回路」のことを指すのが一般的です。集積回路はムーアの法則(集積密度は数年で倍増する。)やそれを超えるレベルでの回路の微細化が進むと言われていますが、従来の半導体製造装置の限界も浮き彫りになってきています。そうした中、NEDOプロジェクトの下、東北大学未来科学技術共同研究センターの大見忠弘教授と東京エレクトロン株式会社では、次世代を担う、画期的な半導体製造装置の開発に成功しました。
BIGINNING 開発への道
従来の半導体製造装置が抱える問題
集積回路はシリコンウエハと呼ばれる円盤状の薄い単結晶シリコンの上に、原料となるガスを、薄い膜として堆積させ、それにエッチングなどの微細加工を施すことによって作られます。その処理性能は、微細加工技術の発展に伴い、向上してきました。今や1個の集積回路に収められているトランジスタや抵抗、コンデンサなどの半導体素子の数は100億個を超えています。
しかし、微細化が進むうちに、従来の半導体製造装置には、限界が見え始めてきました。まず、従来の半導体製造装置は、集積回路のベースとなるMOSトランジスタの製造が1,000℃~1,200℃という高温環境下で行われるため、シリコンウエハ表面に損傷が避けられません。損傷は集積回路の性能低下を招きます。しかも、微細であればあるほどその損傷が与える影響は大きくなります。
次に、集積回路の製造工程は、薄膜の生成やエッチングなどの繰り返しで、その工程は約500回以上にも及びます。そして、各工程によって原料となるガスの種類や圧力が異なるため、従来の半導体製造装置では、製造工程毎に、専用の装置を使う必要がありました。各製造装置には生産能力に差があるため、生産能力の低い装置が、半導体製造工程全体の生産性の足を引っ張ることとなり、各装置の生産能力を最大限に発揮させることは、困難な状態でした。
また、生産性をあげるために、これまでにも、一度に製造できるシリコンチップの数を増やそうとして、幾度となくシリコンウエハの大口径化と、シリコンチップの小型化も試みられてきました。しかし、従来の半導体製造装置では、シリコンウエハの加工寸法が変わるたびに、装置の調整や買い替えが必要で、巨額の初期投資が避けられませんでした。
さらに、薄膜の生成やエッチングを行う、チャンバと呼ばれる反応容器内の温度が1,000℃以上と、非常に高温のため、チャンバ内壁や排気口に、原料ガスの反応生成物(かす)が大量に堆積してしまうという問題も抱えています。これは、装置の生産能力を低下させるだけでなく、異なる製造工程を、1台の装置で連続的に行えない要因にもなっています。反応容器内を頻繁にクリーニングする必要もあり、半導体製造工場にとって大きな負担となっています。
画期的な半導体製造装置を開発し、世界の大手半導体メーカーに納入
こうした従来の半導体製造装置が抱える問題の多くを一気に解決するような、画期的な半導体製造装置がNEDOの支援で開発され、世界の大手半導体メーカーで次々と採用されはじめています。研究開発に挑んだのは、東北大学未来科学技術共同研究センターの大見忠弘教授と、半導体やフラットパネルディスプレイなどの製造装置メーカーである東京エレクトロン株式会社です。
両者は、NEDOプロジェクト「高効率半導体製造プロセス基盤技術の開発」(1998~1999年度)、その成果をベースに製品化を目指す「マイクロ波励起高密度プラズマ技術を用いた省エネ型半導体製造装置の技術開発」(2002~2005年度)を通して、従来にない成膜方式の「マイクロ波励起高密度プラズマ技術を用いた半導体製造装置」を開発、その功績が認められ、2003年度「第2回産学官連携推進会議 産学官連携功労表彰内閣総理大臣賞」を受賞。わが国の半導体産業の国際競争力強化に向けて、大きな期待が寄せられています。
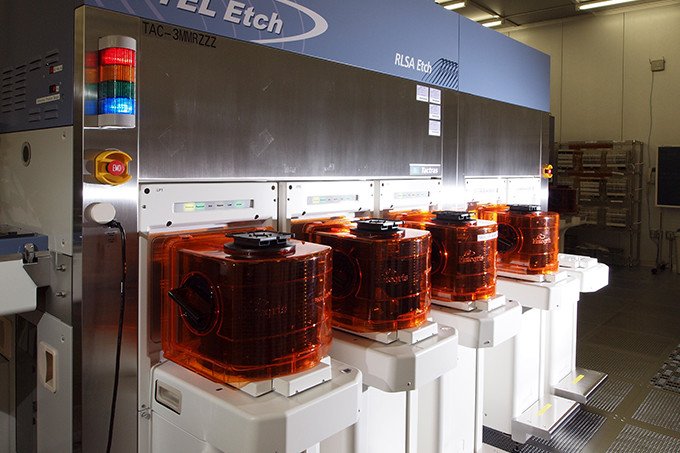
東京エレクトロンが開発・販売する、「マイクロ波励起高密度プラズマ技術を用いた半導体製造(エッチング)装置」
2.45GHzのマイクロ波を使ってプラズマ励起
マイクロ波励起高密度プラズマ技術とは、集積回路の原材料となるガスを、自由空間における電波の波長が12cmと短い2.45GHzという高い周波数を持つマイクロ波を使って、チャンバ内で均一かつ高密度にプラズマ励起し、反応を起こりやすくするという技術です。
プラズマとは、原子核の周りを回っていた電子が原子から離れ、正電荷の原子核と負電荷の電子に分かれた電離状態のことです。原子や分子1個1個が、電気的に不安定で、極めて反応性が強い状態にあります。そのため、従来の半導体製造装置のように、高温環境下で反応を促進させることなく、200~400℃といった、低温環境下でも反応を促進させることができます。
そのため、シリコンウエハの温度を無理に上げる必要がなく、シリコンウエハへの損傷が減り、従来の高温型の製造装置に比べて、何倍もの高性能集積回路を製造できます。
東京エレクトロンが開発した、「マイクロ波励起高密度プラズマ技術を用いた半導体製造装置」以前にも、プラズマを用いた半導体製造装置は、様々な製造工程で使用されてきました。化学気相成長(CVD=Chemical Vapor Deposition)と呼ばれる方法を使った、薄膜生成装置「プラズマCVD装置」です。
しかし、従来の「プラズマCVD装置」の場合、0.013GHz(13MHz)という周波数の電波で、原料ガスをプラズマ励起するため、「熱酸化CVD装置」に比べれば、低温環境下で反応を促進できるものの、電子自身が持つ温度(エネルギー)が高いため、イオン衝撃ダメージが大きくかつシリコンウエハがプラズマ励起領域に設置されるためチャージアップダメージも大きく、シリコンウエハの損傷問題は、あまり解消されませんでした(図1)。
そのため、プラズマ技術そのものが、汚染やダメージを嫌うトランジスタ製造工程には適用できず、配線工程の製造にだけ使えると、考えられてきたのです。さらに、従来の「プラズマCVD装置」の場合、原料ガスがチャンバ内で乱流となって引っかき回されて流れているため、プラズマ励起空間で過剰に解離されて、反応生成物(かす)がチャンバ内表面に大量に堆積するという問題も残されたままでした。
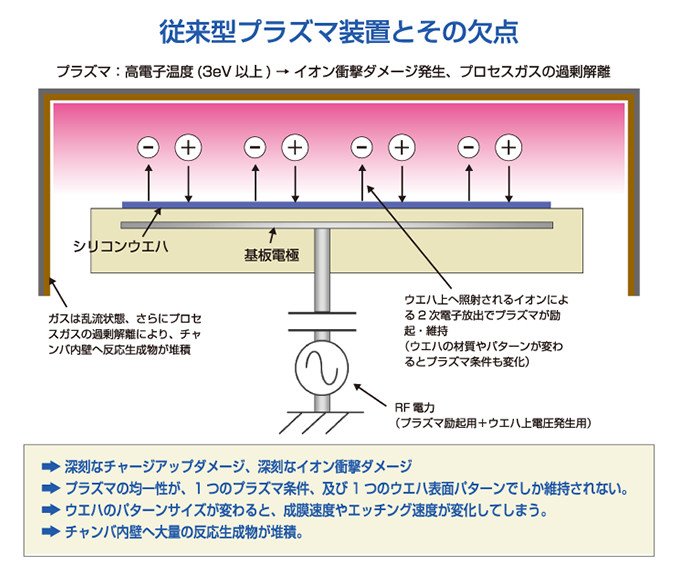
図1 従来型プラズマ装置とその欠点
異なる薄膜の連続成膜と連続エッチングが可能に
それに対し、マイクロ波でプラズマ励起する半導体製造装置では、シリコンウエハが、プラズマ励起領域から離れた拡散プラズマ領域にあり、シリコンウエハの周辺には低電子温度の電子やイオンしか存在しないような構造になっています。そのため、シリコンウエハへの損傷が極めて少ないのです。
東北大学未来科学技術共同研究センターの大見忠弘教授は、「私たちが開発した半導体製造装置であれば、ウエハへの損傷がきわめて少なく、これまでプラズマ技術は使えないとされてきたトランジスタ製造の要ともいうべきゲート絶縁膜形成など、汚染や損傷の存在がいっさい許されない高品質性が強く要求される製造工程への対応も可能です」と胸を張ります。
また、大見教授らは、チャンバの構造を根本から見直し、ガスの流れを均一かつ層流状に工夫したことで、ガスがチャンバ内で乱流化することがなく、反応生成物が堆積するという問題も解消されています。さらに、周辺機器や部品を新たに開発することで、原料となるガスの種類や圧力、ウエハの種類などに関係なく、常に均一で、高密度のプラズマを発生させることができるようにしました(図2)。下の断面図で肌色の部分がRLSAで、その下にプラズマ励起用のガス及びラジカル生成用のガスをチャンバ内に均一かつ層流状に流すセラミック製のシャワープレートが設置されています。紫色の部分が、ガスの送り込まれるチャンバで、青色の基板がウエハに当たります。
その結果、原料ガスの種類や圧力が異なる複数の製造工程を、1つのチャンバ内で、連続して行うことができるようになりました。異なる薄膜の連続成膜と連続エッチングが可能となったことで、生産性が劇的に向上するだけでなく、これまでまったく不可能だった超多品種・少量生産への対応もできるようになったのです。
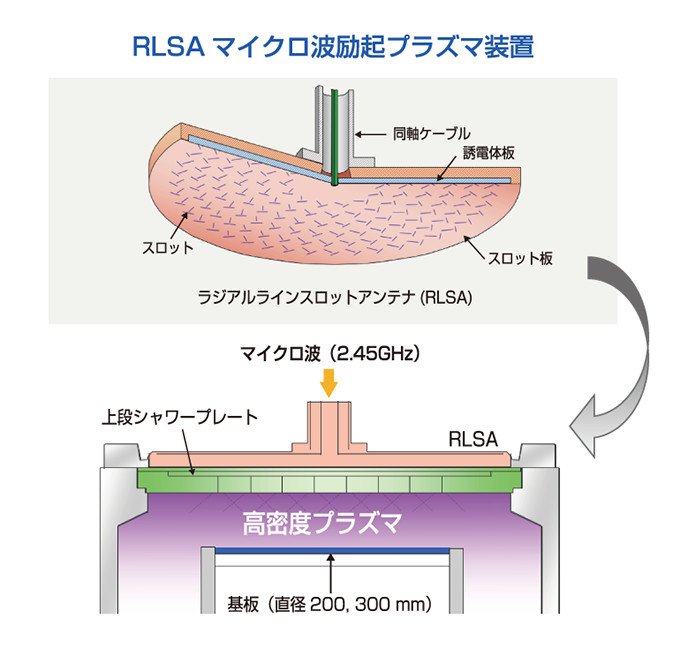
図2 大見教授らが開発したガスを均一化するチャンバの構造模式図。「RLSA」は「ラジアルラインスロットアンテナ」の略、この装置の要となる技術(次ページ以降参照)
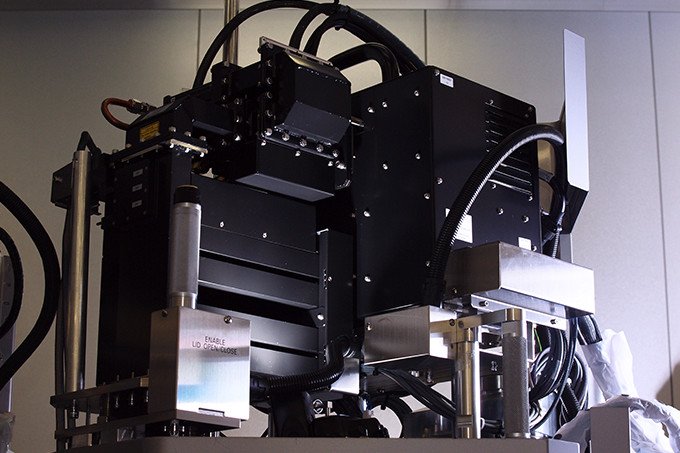
マイクロ波プラズマ発生装置
また、1台の装置で、複数の製造工程やプロセスをこなすことができるため、従来に比べ、非常に少ない台数で、小規模な生産ラインを組むことも可能になりました。シリコンウエハの加工寸法が変わっても、成膜速度やエッチング速度が変わらないため、微細化世代が進行するたびに、大規模な投資をする必要もなくなりました。大幅な低価格生産、超短時間生産が可能になったのです。大量生産が求められる半導体メモリの一種であるDRAMの生産にもきわめて有効です。
さらに、従来の半導体製造装置では、シリコンウエハの特定の結晶面{(100)表面}にしか集積回路を作ることができませんでしたが、マイクロ波励起高密度プラズマ技術を用いた半導体製造装置では、すべての面方位に半導体素子を形成することも可能です。大見教授は語ります。「この装置を使えば、3次元立体構造集積回路の実現も夢ではありません。現在30億回/秒が処理速度の限界となっているシリコン半導体の常識を塗り替えて行くことになります。」
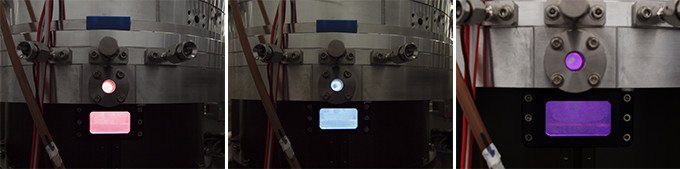
東北大学未来科学技術共同研究センターでの、マイクロ波励起プラズマ装置チャンバへ次々と異種ガスを送り込む反応実験
プラズマの発光の色が瞬時に変化している
BREAKTHROUGH プロジェクトの突破口
衛星放送受信用のアンテナを、半導体製造プラズマ励起に応用
大見教授と東京エレクトロンによる共同プロジェクト開始のきっかけは1993年に遡ります。東京工業大学の後藤尚久教授(現・東京工業大学名誉教授・拓殖大学名誉教授)が、1980年に発明した衛星放送受信用「ラジアルラインスロットアンテナ(以下、RLSA)」を、原子や分子のプラズマ化に応用できないかと、大見教授に持ちかけました。
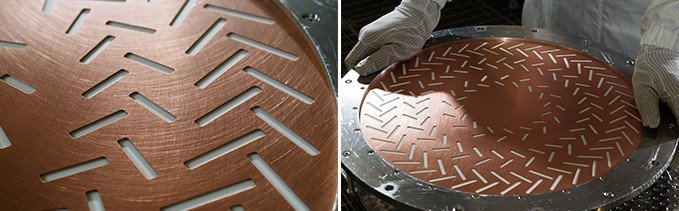
刻み込まれたスロットが特徴的な、ラジアルラインスロットアンテナ
このアンテナの応用が、高温環境下で用いる熱酸化半導体製造装置やプラズマCVD装置の抱えていた様々な問題を解決するブレークスルーの端緒となりました。
従来のアンテナは、波長の20倍以上アンテナから離れないと電磁界分布を正確に制御することができません。一方、RLSAは、アンテナの近傍の電磁界を完全に制御できる点が最大の特徴です。そのため、大見教授は、RLSAが半導体製造装置のプラズマ励起に最適であると直感し、適用を決断。すぐさま、実験を開始しました。
そして、1995年、RLSAを使って初めてマイクロ波で大面積かつ安定的にプラズマを生成することに成功しました。さらに1997年には、MOSトランジスタの製造に応用できることを確認しました。
「このRLSAを使えば、従来の半導体製造装置が抱える問題を一気に解決できる」と大見教授は確信し、東京エレクトロンと共にNEDOプロジェクトへ応募しました。
かくして、1999年、「高効率半導体製造プロセス基盤技術の開発」プロジェクトがスタート。目指すは、RLSAを使ってマイクロ波を当てプラズマを励起し集積回路を製造する半導体製造装置の開発です。
大見教授と東京エレクトロンは、まず、RLSAを使ったマイクロ波励起プラズマ装置の開発に取り掛かりました。実際に大見教授らが設計した装置は、図3のような構造(模式図)になっています。
チャンバ上部から、RLSAを通して、2.45GHzのマイクロ波を当てます。RLSAの真下には、無数の極小の穴が開いたセラミック製の上段シャワープレートが設置されており、そこから、チャンバ内に向かって、プラズマ励起用ガスとラジカル生成用ガスを均一かつ層流状に供給します。
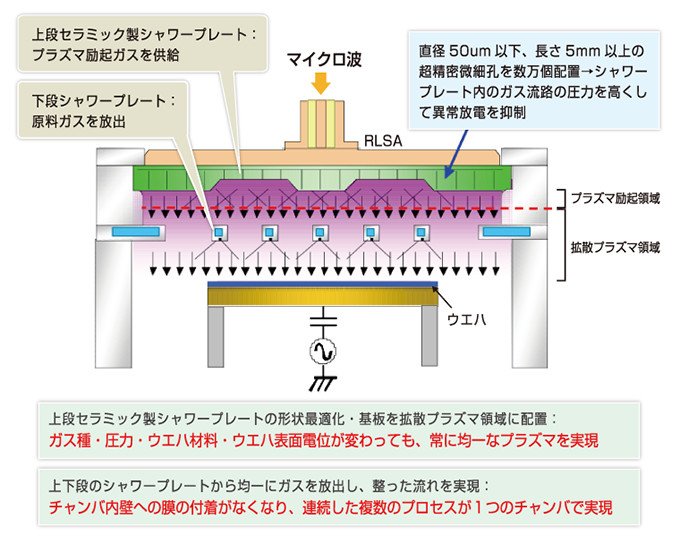
図3 凹凸形状を設けた上段セラミックスシャワープレートで、ガス条件や圧力を変えてもプラズマ均一性を維持可能に
シャワープレートの形状を工夫して、均一なプラズマ状態を実現
また、シリコンウエハとセラミックのシャワープレートの中間に、もう1枚、下段シャワープレートを設置します。そこからは、必要に応じて原料ガスを供給します。ガスのプラズマ励起は、RLSA近傍のごく限られた空間領域でのみ起こります。つまり、プラズマ励起する空間領域は、上段のセラミックシャワープレートと下段のシャワープレートの間に限られ、シリコンウエハ周辺は、プラズマ励起したガスが拡散した、低電子温度の"マイルド"な空間になっています。
東京エレクトロン技術研究所常務執行役員でRLSAプラズマ技術担当の野沢俊久さんは、「さらに、上段シャワープレートの形状を工夫することで、原料ガスの種類や圧力、ウエハの材料に関係なく、ウエハ上面のプラズマを、常に均一で、高密度なプラズマ励起状態にすることに成功しました」と説明します。
また、シャワープレートを上段と下段の2段に分けて設置したのは、原料ガスがRLSA近傍のプラズマ励起領域に逆流し、不必要な反応生成物が発生して、チャンバの内壁や排気口に大量に堆積しないようにするためです。ガスの流れを制御することで、堆積物はほとんどなくなりました(図5)。
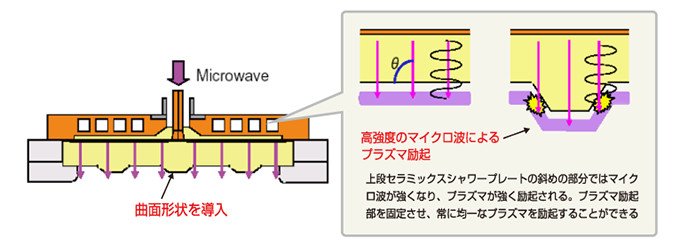
図4 凹凸形状を設けた上段セラミックシャワープレートで、ガス条件や圧力を変えてもプラズマ均一性を維持可能に
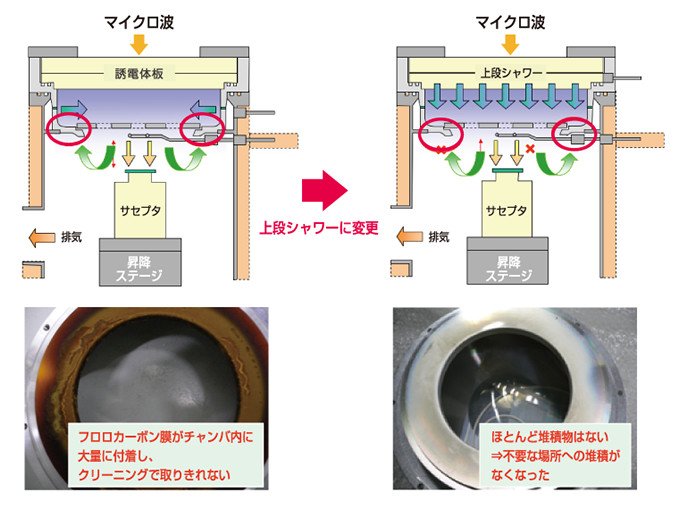
図5 CVD装置チャンバ内生成物の違い。
ガスを均一かつ層流状にチャンバ内に流すことにより、下段シャワープレートから供給される原料ガスがプラズマ励起領域に戻ることが無くなり、反応生成物がチャンバ内表面に堆積しなくなった。クリーニング時間が圧倒的に短縮し、生産性が劇的に向上できる
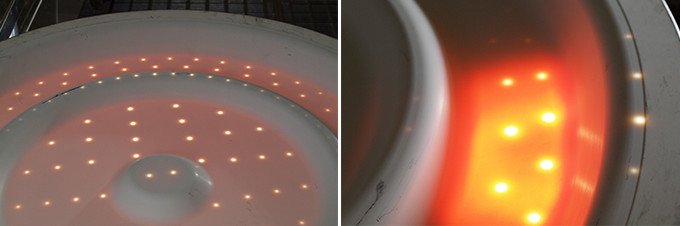
大見研究室で研究中の凹凸形状を取り入れたセラミック製シャワープレートサンプル
FOR THE FUTURE 開発のいま、そして未来
チャンバ内の表面加工と排気ポンプ
半導体製造装置の研究開発において、大見教授はチャンバ内壁の表面加工でも苦労と工夫を重ねました。この半導体製造装置では、1台のチャンバであらゆる原料ガスを処理できるようにすることを目指していたため、反応性や腐食性に富んだ塩素や臭素、フッ素といったハロゲン系など、どんな原料ガスでも反応して腐食しないようにする必要がありました。大見教授は、新しいアルミニウム合金製のチャンバ表面に新しい非水溶液を用いた陽極酸化により酸化アルミニウム(Al2O3)の保護膜を生成することで、これを克服しました。大見教授は、この保護膜を生成するのに、実に25年の歳月をかけたと話します。
また、大見教授らはNEDOプロジェクトで原料やエッチング用のガスをチャンバに注入し、不要となったガスを速やかに排気するポンプも開発しています。ポンプもチャンバ内壁同様、どのようなガスでも腐食せず、どのような圧力範囲でも常に同じ速度でガスの排気ができなければなりません。
水素のような軽いガスから重いガスまですべてのガス種に対して一定の速度で排気できるポンプの開発に挑み、1996年に世界で初めて開発に成功しました。それは、不等ピッチ、不等傾斜角の従来にないスクリューを搭載したポンプでした。「こちらも15年間かけて、ようやく今年、製品化の目処が立ちました」と大見教授は語ります。排気ポンプの実用化で、大見教授の目指す半導体製造装置に必要な、要素技術のほとんどが整うこととなりました。
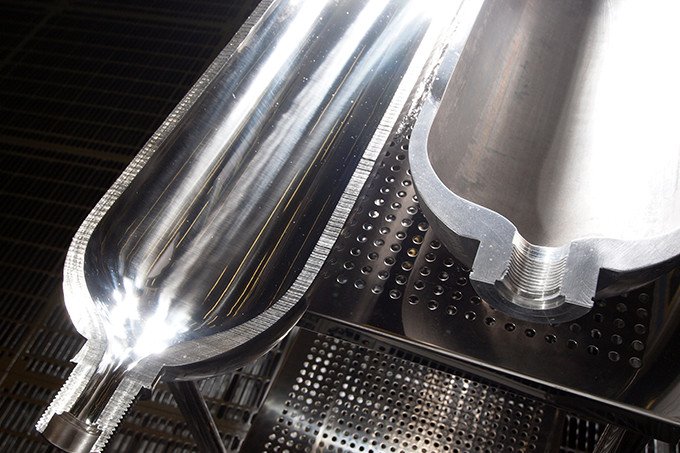
内表面が電解複合研磨によって磨かれたウルトラクリーンボンベ(大見研究室)
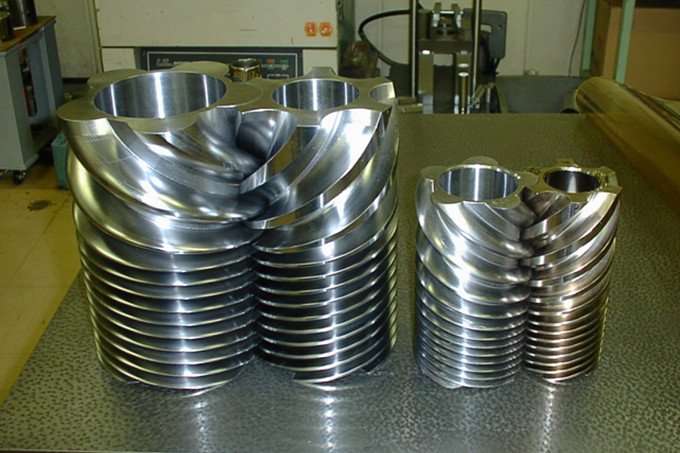
複雑な形状をした排気ポンプのスクリュー。加工時間の大幅な短縮で、東京エレクトロンの半導体製造装置への実装にも目処が立ったと、大見教授は言う
高性能、高品質、低消費電力で世界市場に
こうして、目指す半導体製造装置に必要な要素技術を、徐々に整えていきました。ポンプなど周辺機器の開発に先駆け、2001年12月には、東京エレクトロンが、マイクロ波励起プラズマによるシリコンの酸化膜と窒化膜の製造装置「Trias SPA」の販売を開始しました。
これは、汚染や損傷の極めて少ない高品質のゲート絶縁膜を製造できるプラズマ装置として高い評価を獲得し、2003年以降、多くの世界の大手半導体メーカーに納入されました。現在も、「Trias SPA」シリーズは順調に売り上げを伸ばしています。野沢さんは、「従来の装置に比べて、低周波雑音を100分の1以下に、電力消費に直接影響するゲート絶縁膜のリーク電流(スタンバイ電力)を1000分の1以下に減らすことができます」と省エネルギー性能も装置の特色と語ります。
2002年度~2005年度の4年間で実施されたNEDOプロジェクト「マイクロ波励起高密度プラズマ技術を用いた省エネ型半導体製造装置の技術開発」では、ゲート絶縁膜形成装置に加え、金属配線間を絶縁するための酸化膜である層間絶縁膜の形成装置やエッチング装置の開発など、4テーマが設定されていました。2008年末にはエッチング装置の量産化も実現し、徐々に売り上げを伸ばし始めています。
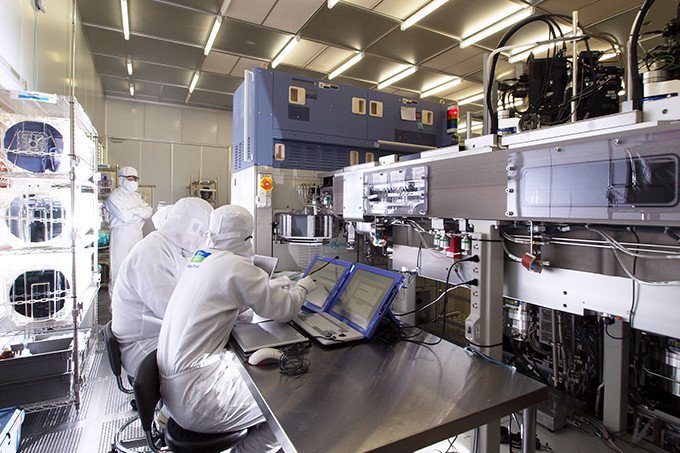
東京エレクトロンの仙台事業所内の研究開発用クリーンルーム
大型有機ELディスプレイやLED、大面積太陽電池への応用も
大見教授は力強く語ります。「NEDOプロジェクトがなければ、このような画期的な半導体製造装置を開発することなどできなかったでしょう」
野沢さんも言います。「新たな半導体製造装置の実現には、セラミックシャワープレートやマイクロ波電力供給システム、ポンプなどさまざまな素材や部品の開発が不可欠でした。しかし、大見教授の強いリーダーシップの下、我々東京エレクトロンを含め、企業が大学とうまく連携し、プロジェクトを推進することができました。これも、ホームグラウンドを用意し、強く支援して下さったNEDOのお陰だと思っています」
同プロジェクトを通して培われた理論や技術は、半導体のみならず、LEDや超低消費電力・低価格の大型有機ELディスプレイ、大面積太陽電池などさまざまな分野への応用が可能なため、環境問題の解決にも寄与するとして、大きな期待が寄せられています。(2010年12月〜2011年1月取材)
開発者の横顔
半導体立国再興の扉を開ける
日本の半導体産業復活の兆しは見えています
半導体研究の第一人者である東北大学未来科学技術共同研究センター大見忠弘教授の半導体との出合いは、1966年に遡ります。東京工業大学の助手時代、電子管や真空管を専門にする研究室で、半導体デバイスの研究開発に着手したのがきっかけです。その後、1972年に転任した東北大学では、理想とする半導体デバイスを製造するため、半導体製造装置の開発に着手。1984年には東北大学の電気通信研究所内にクリーンルームを、1986年3月にはスーパークリーンルームを建設しました。
その頃、日本では、1986年から1991年にかけて、半導体出荷額が世界トップとなりました。しかし、90年代以降は、米国の復活や新興国の台頭で、日本のシェアは低下しつつありました。こうした状況の中、日本の半導体産業の起死回生を果たすべく、数々の国家プロジェクトが立ち上げられました。
その中でもキーパーソンとして活躍し、1998年4月には東北大学に未来科学技術共同研究センターを開設。現在も、最先端の半導体製造装置の研究開発に明け暮れる日々を送っています。NEDOプロジェクトへの参加の際には、申請からプロジェクトリーダーまで担当しています。
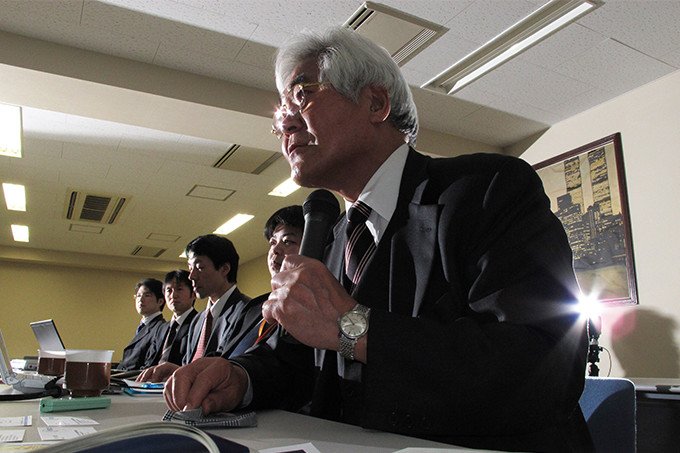
東京エレクトロン株式会社/東北大学未来科学技術共同研究センター
大見教授
大見教授のリーダーシップ、プロジェクトを通して技術者として成長
東京エレクトロン技術研究所株式会社 常務執行役員 RLSAプラズマ技術担当 野沢俊久さんは、大学院修士課程修了後1985年に東京エレクトロンに就職。技術開発部門を経て、米国シリコンバレーに赴任、88年までソフトウエア開発を勉強。帰国後は半導体用エッチング装置開発に従事しました。米国での経験を活かし、装置設計に重要なシリコンウエハの温度制御に関するシミュレーションを担当しました。
そして、2001年、「マイクロ波励起高密度プラズマ技術を用いた省エネ型半導体製造装置の技術開発」プロジェクトで、企業側リーダーを務めることとなります。「最初は、同じプラズマエッチングなので、0.013GHzも、2.45GHzも大差ないだろうと思っていました。しかし、比べてみると品質がまったく異なることに驚き、理論に基づく装置開発の重要性を、大見教授から改めて教えていただきました。開発中、不明点が発生すると、大見先生がすぐさま関連企業を集めて、ミーティングを開催していただき、大見先生を中心に様々な企業と議論を重ねることで、新たな発見や多くの気付きがありました」
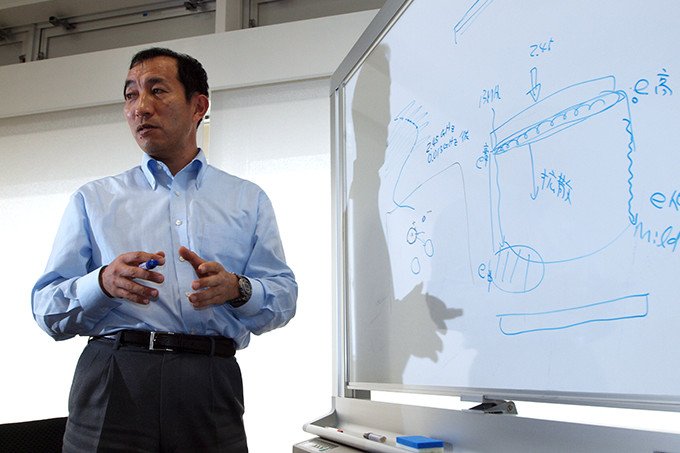
東京エレクトロン株式会社/東北大学未来科学技術共同研究センター
野沢さん
なるほど基礎知識
集積回路(半導体)は、どうやって作る?
集積回路を作るには、まずシリコンウエハの表面に微細加工を施します。絶縁膜や配線金属膜を形成する工程を何度も繰り返して、トランジスタや抵抗、コンデンサ、ダイオードなどミクロン単位の電子部品である半導体素子を作りこんでいくのです。そうしてできたシリコンチップを1個1個切り出し、パッケージに封入したものが集積回路です。
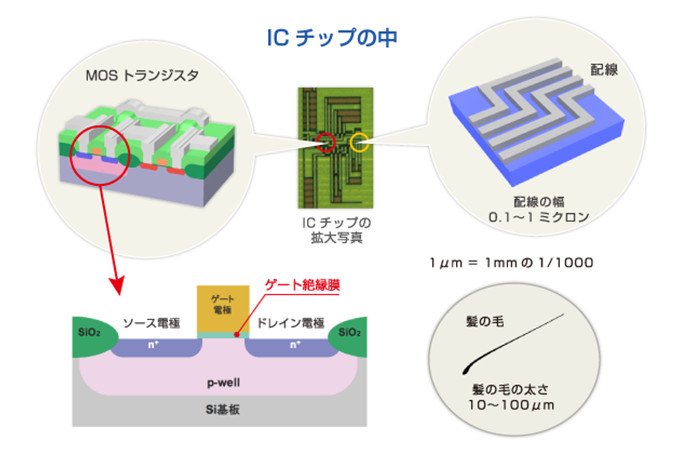
集積回路には、コンピュータの演算処理機能の中枢を担う「マイクロプロセッサ」や、プログラムやデータ情報を記憶する「メモリ」など数種類があります。
半導体素子は集積回路上では、金属配線によって接続され、最小機能単位のゲートを構成します。トランジスタはP型半導体とN型半導体がサンドイッチ状に接合された構成になっています。現在、主流となるのが、「MOSトランジスタ」で、ドレインとソースと呼ばれる2つの電極の間に電流を流します。MOSトランジスタは、半導体基板にソースとドレインを作成し、ゲートから絶縁膜を通して電圧をかける構造になっています。
半導体製造装置で、シリコンウエハ上に電子回路を作る工程には、リソグラフィ技術が使われます。電子回路は20~30枚のフォトマスクに描かれた原画を露光やエッチングを繰り返してウエハに転写、パターン形成し、絶縁膜や金属配線などを形成していきます。
絶縁膜や金属配線を形成するには、素材となる酸化シリコンなどの薄膜層を作る必要があります。成膜の方法は、主に「スパッタ」、「CVD」、「熱酸化」です。CVDとは化学気相成長法のことで、チャンバ内で、原料ガスを化学反応させ、薄膜をウエハ表面に堆積していきます。化学反応を促進する方法として、熱エネルギーを利用する熱CVD、プラズマエネルギーを利用するプラズマCVDなどがあります。
薄膜を微細加工する工程がリソグラフィです。リソグラフィでは、露光、現像、エッチング技術が使われます。プラズマエッチングでは、チャンバ内にウエハを設置し、プラズマ励起したガスを使ってエッチングしていきます。
その後、半導体素子を構成するのに必要なP型やN型の半導体領域を形成するため、ボロンやリンなどの不純物原子をイオン化して、ウエハの全面や表面の一部に添加させ、熱処理などを行い、シリコン内部に不純物を広く分布させていきます。
LSIの製造では、ゲート絶縁膜や金属配線、多層構造間の層間絶縁膜などさまざまな膜が作られ、使われています。最後に、完成した半導体素子をゴミや湿気から保護するため、酸化膜や窒化膜による保護膜で覆えば、完成です。
マイクロ波によるプラズマ励起はなぜいい?
従来の0.013GHz(13MHz)という周波数の電波を用いたプラズマ励起と2.45GHzという周波数のマイクロ波を用いたプラズマ励起との違いはどこにあるのでしょうか。
周波数とは、1秒間に繰り返される電気振動の回数のことですから、2.45 GHzのマイクロ波は、0.013 GHzの電波の約190倍の振動回数になります。言い換えれば、マイクロ波は非常に速く電界の方向が反転するのです。そのため電子が連続して加速されることがなくなり、電子温度が低く電子のエネルギーが小さくなるのです。
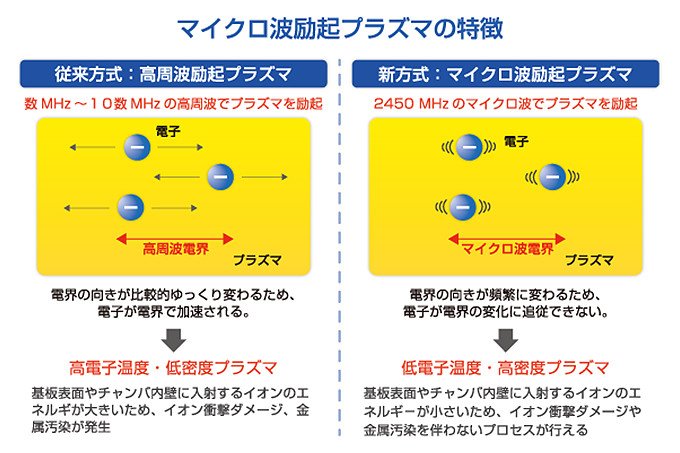
逆に、0.013 GHzの電波は、マイクロ波に比べて電波の波長が長いために、プラズマ励起空間が広くなり、シリコンウエハがプラズマ励起空間に含まれてしまうことが多くなります。また、0.013GHzの電波の電界は、マイクロ波に比べてゆっくり電界の方向が反転しますから、電子が長時間に亘って加速され続けるため、電子温度が高く、電子のエネルギーが大きくなり、シリコンウエハへの損傷が大きくなるのです。
真空容器中の電子は電波やマイクロ波の電界によって加速されますが、前述したように周波数が2.45GHzのマイクロ波は、周波数が0.013GHzの電波に比べて電界の方向が非常に早く反転するため電子のエネルギーが大きくなりません。このため、同じ電力(電気エネルギー)を真空容器に入れた場合、そのエネルギーによって次々に分子の解離、電離が起こり、密度の濃いプラズマを励起することができます。一方、0.013GHzの場合は、エネルギーは主に電子の加速に使われてしまうため、密度の濃いプラズマを作ることができません。
マイクロ波は密度の濃いプラズマの中には侵入できない性質があるため、プラズマはマイクロ波がセラミック誘電体を通って真空容器内に侵入したその場所で発生し、そこでほとんどのエネルギーが吸収されるために、真空容器内へは入っていきません。ウエハ上にはマイクロ波が存在しないため、ウェハ上のプラズマは電子エネルギーが低く、シリコンウエハが損傷することはありません。
ウエハ上にはセラミック誘電体直下で発生したプラズマが拡散によって輸送されます。拡散による輸送は、温度の異なる液体を混ぜるとだんだん一定の温度になるように、電子やイオン、ラジカルも輸送によって均一になるような効果もあるため、ウエハ上での均一な処理に向いています。
一方、0.013GHzの電波によるプラズマ励起の場合は、プラズマの密度が十分高くないために、電波は真空容器内に入り込み、ウエハ上でもプラズマが励起されます。このためウエハ上のプラズマの電子エネルギーも高くなってしまいます。
この現象が、0.013GHzの電波で励起したプラズマではシリコンウエハ表面で損傷が発生してしまい、一方マイクロ波励起プラズマではシリコンウエハ表面への損傷が少なくなるというメカニズムです。
お読みいただきありがとうございました。
ぜひともアンケートにお答えいただき、
お読みいただいた感想をお聞かせください。
いただいた感想は、
今後の連載の参考とさせていただきます。