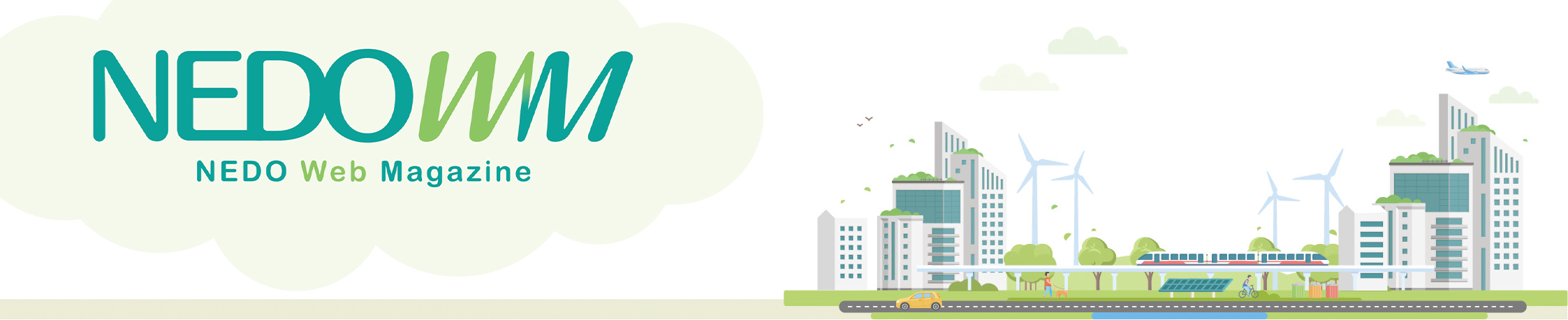
CONTENTS
INTRODUCTION
絶縁保護膜用樹脂のハロゲン(塩素)含有量3,000ppm → 数ppm以下
BEGINNING
相反する柔軟性と絶縁性とを両立させた絶縁保護膜が求められていた
BREAKTHROUGH
常識を超えた短期間でのスケールアップ
FOR THE FUTURE
グリーン効果の連鎖FACE
足掛け30年の構想を実現INTRODUCTION 概要
絶縁保護膜用樹脂のハロゲン(塩素)含有量
3,000ppm → 数ppm以下
エレクトロニクス製品の小型軽量化、高信頼性(長寿命化)などのためには、電子部品や配線の絶縁保護膜の高性能化がますます重要になっています。この保護膜用樹脂として「エポキシ樹脂」が広く一般的に使われていますが、従来の製法には二つの問題がありました。一つは環境面で懸念のあるフェノール類を原料としていること。もう一つはハロゲン化合物を原料として用いるため、どうしても最終製品である絶縁保護膜に有機塩素化合物が不純物として残留し、絶縁保護膜の品質劣化を引き起こす原因となることでした。
この「環境」と「品質」の二つの問題を一度に解決したのが昭和電工の「熱硬化型ソルダーレジスト」です。昭和電工は、NEDOプロジェクト「有害化学物質リスク削減基盤技術研究開発」において、これらフェノール類とハロゲン化合物とを使うことなく、オレフィン化合物を過酸化水素による直接酸化によってエポキシ化合物へと導く技術の開発に成功しました。この技術を応用した製品は2007年の上市以来、多くの液晶パネル製造工程に採用されています。
BIGINNING 開発への道
相反する柔軟性と絶縁性とを両立させた絶縁保護膜が求められていた
最近の薄型液晶テレビは、本体の縁ぎりぎりまで画面が広がっています。この大きな画面を実現するためには、液晶画面に信号を送るICチップを載せるプリント配線基板を小さく折り曲げて使用することが必要になりました(図1)。
絶縁保護膜に求められる性能として、絶縁性能の他に基板上に描かれている銅配線との密着性が高く、それでいて基板を折り曲げたときに絶縁保護膜自体がダメージを受けない、歪みを吸収できる柔軟性とを持ち合わせていなければなりません。しかし、一般に相反する柔軟性と絶縁性とを両立させることは非常に難しい課題でした。
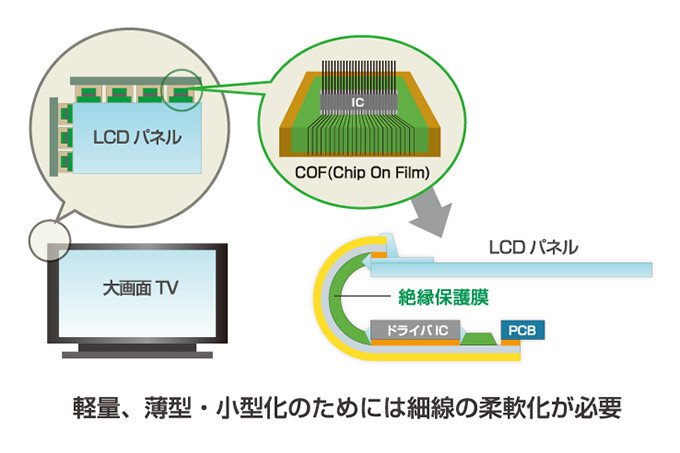
図1 液晶画面を広げるために、柔軟性と絶縁性とを両立させた絶縁保護膜が求められていた
また、絶縁保護膜の寿命にも改良の余地がありました。絶縁保護膜はエポキシ樹脂と硬化剤との組み合わせで成り立っています。従来エポキシ樹脂には、製造工程でどうしても塩素原子を含む不純物が混入してしまいました。この不純物は、長時間使用するうちに細い配線のショートの原因となる塩化水素ガスを発生してしまいます。そのため、そのような不純物を製品中に残さないエポキシ樹脂の開発も望まれていました。
環境に負荷をかけない事業者責任の拡大
プロジェクトを中心となって推し進めた昭和電工研究開発本部の内田博さんは、「環境に負荷をかけないということと、製品の品質とが両立していなければ、事業として成り立たない」と言います。というのも環境への有害物質の排出を防ぐために新たな制度導入や法改正が次々と進められ、事業主は有害物質を廃棄する際、その無害化のために莫大な費用を負担しなければならなくなったのです。
従来使用されていたエポキシ樹脂は、環境ホルモンとして当時注目されていたビスフェノールA構造を含むなど環境への影響面で懸念がありました。また、エポキシ樹脂の製造過程では大量のハロゲンを含んだ廃棄物が排出されてしまい、その処理は製造コストのみならず、地球環境への大きな負担となっていました。このような環境負荷低減の観点からも、これらの原料を使わずにエポキシ樹脂を製造する方法が望まれていたのです。
※ 欧米でもRoHS指令、REACH規制といった化学品に対する厳しい管理が求められるようになり、それに対応して2001年から日本国内でも「特定化学物質の環境への排出量の把握等及び管理の改善の促進に関する法律」に基づくPRTR制度(化学物質排出移動量届出制度)の導入、2003年には「化学物質の審査及び製造等の規制に関する法律」の改正が行われ、それまで企業の自主努力によっていた化学物質の使用・排出管理などが、全事業主に義務付けられるようになりました。また、中国、韓国などでも同じような動きが出てきています。
産学連携が生み出した成果
1996年、タングステン酸を触媒として用いてエポキシ化合物を合成する基本反応が、後にノーベル化学賞を受賞する名古屋大学(当時)の野依良治教授らによって開発されました。それは、過酸化水素を使ってオレフィン化合物を酸化し、エポキシ化合物を得る方法です(図2)。この反応では目的とするエポキシ化合物以外には水のみが副生成物として得られます。そのため廃棄物処理の負担を大幅に減らせ、環境負荷が極めて小さい方法です。その上、これまで溶媒として反応に大量に必要だった有機溶媒も使わずに済むものでした。
昭和電工は、産業技術総合研究所佐藤一彦グループ長(当時)とともにNEDOプロジェクト「有害化学物質リスク削減基盤技術研究開発」に参加し、この過酸化水素による酸化方法を基としたエポキシ化合物製造の研究開発をスタートさせました。また昭和電工では、もうひとつのターゲットである、紫外線による硬化から熱による硬化が可能となる新規の硬化剤開発にも、本プロジェクトの一環として並行して取り組み始めました。

図2 過酸化水素によるオレフィンのエポキシ化反応
プロジェクトでは新たな製法で合成することによって、ハロゲン含有量を従来の約3,000ppmから数ppm以下に低減したエポキシ樹脂と、同じく開発した新規の硬化剤とを組み合わせて絶縁保護膜を実際に試作し、その評価試験を繰り返し行いました。
その試験は、幅50ミクロンと極めて細い配線から形成される特殊な電気回路を試作した絶縁保護膜で覆い、例えば槽内温度85℃、槽内相対湿度85%RHの高温高湿という過酷な環境で数百~数千時間をかけて絶縁保護膜の性能を確認するものです。
従来のエポキシ樹脂による絶縁保護膜を使った評価試験では、試験開始後まもなく絶縁性が急激に落ちてしまいました。回路を観察すると保護膜は黒く変色し、部分的に膨れてしまっていました。一方、試作された絶縁保護膜で覆われた回路には、そのような変化は認められませんでした。
こうして試作と評価試験とを産学連携で重ね、新たに開発された絶縁保護膜は従来品と比較して100倍以上(10万時間の連続運転に相当)の長期絶縁性能を示すようになりました。
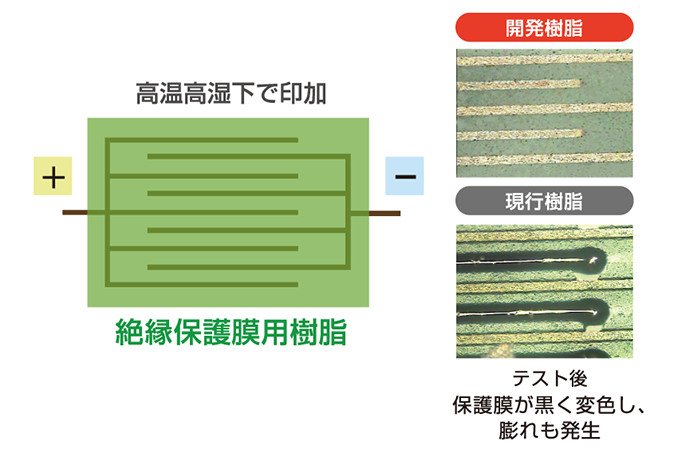
図3 評価試験用回路の模式図(左)と評価試験終了後の回路の拡大写真(右)。
従来のエポキシ樹脂を絶縁保護膜として使った回路では絶縁保護膜が黒く変色し、部分的に膨れあがっていた(右下)
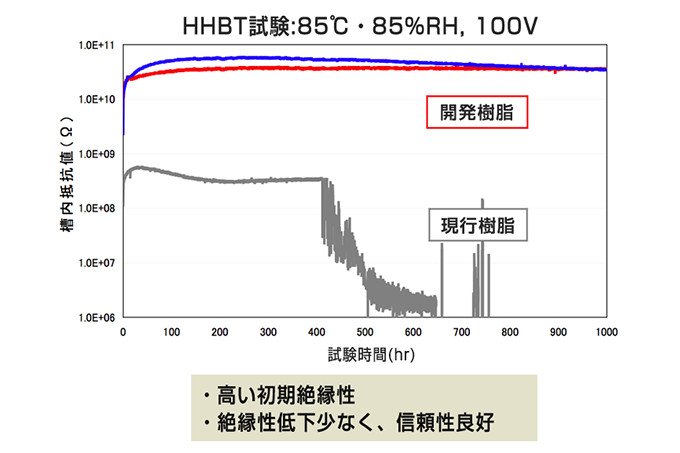
図4 高い初期絶縁性、長期絶縁性を示した新開発樹脂(赤・青線)
BREAKTHROUGH プロジェクトの突破口
常識を超えた短期間でのスケールアップ
実験室の小さなフラスコで数グラムを合成できたエポキシ化合物も、製品として日の目をみるためには、工場でより大きなスケールで製造できるようにならなくてはなりません。
本プロジェクトでも製造を想定したスケールアップにもチャレンジしました。しかし、第一段階から大きな壁にぶつかりました。数グラムのレベルから100倍の100gスケールでの合成で、反応収率が大幅に下がってしまったのです。
エポキシ化の反応は発熱を伴う反応です。そのため反応容積を増やすと、容積あたりの伝熱面積が少なくなったために除熱が追いつかなくなります。反応溶液の温度の急激な上昇により、せっかく生成したエポキシ化合物や酸化剤の過酸化水素が分解する反応が起きていたことがわかりました。
また、プロジェクトで検討されていたプロセスは、水相と有機相との界面で起こる反応です。伝熱面積と同じように、界面もスケールアップに伴い減ってしまいます。原料が分解する上に、反応が起こる場も減ってしまうのでは、収率が下がるのも当然です。研究は振り出しに戻ってしまいました。
これらの苦境に差し掛かり、研究開発チームは共同研究を行っていた産業技術総合研究所の研究員らとともに、再び、より反応速度の速い触媒の探索や改良を日夜行うことになりました。
とくに、昭和電工では、スケールアップと反応速度とを向上させるためのプロセス面での検討に取り組みました。普段はマネージャーに徹していた内田さん自らも絶縁性能の評価を行うなど、プロジェクトに携わるメンバーが総力を挙げて取り組むこととなりました。その結果、数ヶ月間に渡る触媒とプロセスの改良が功を奏し、スケールアップ実験での収率も実験室レベルまで改善される目処を立てることが可能となったのです。
ところが、次にコストの壁が立ちはだかりました。ユーザーに製品を採用してもらうにはキログラムオーダーの生産で、さらに触媒コストを1/10、原材料コストを1/10にしなければなりませんでした。
この問題を解決するために、リーダーの内田さんとNEDO担当者との間で、触媒については10回の繰り返し利用でも同じ性能を出せること、原料については新たなルートによる製法を開発してコストを1/10に抑えること、を目標に更なる検討が続けられました。
また、実験室でキログラムオーダーの大量生産をするとなると、発熱に伴う爆発の危険が伴います。実用化を実現するためのNEDO担当者の厳しい要望に対して、産業技術総合研究所の島田広道プロジェクトリーダーは、出張先のドイツからも国際電話を入れてNEDO担当者と実用化につながるスケールアップの相談をするなど、強い熱意で研究開発に取り組み続けました。
その結果、通常のスケールアップには少なくとも1~2年という時間がかかりますが、本プロジェクトではわずか3ヶ月という短時間で達成することができました。これも、「産業技術総合研究所との連携や事業部のサポート、NEDOプロジェクトの技術検討委員会などのサポートがあったため」と内田さんは振り返ります。
そのころ、開発段階の絶縁保護膜を評価し、従来品に比べ桁違いに優れた絶縁性能と信頼性とを有していると確信したユーザーから、100kgのサンプル提供依頼が舞い込んできました。
開発品をユーザーに採用してもらうためには、新しく創成された化学物質をいくつか法的にも満足させる必要があります。それをクリアするためには莫大な費用、時間を費やす試験が必要でした。本プロジェクトの進捗を評価したNEDOにより、加速財源という手が差しのべられ、ユーザーサイドでの採用決定プロセスの時間軸内で課題をクリアすることができました。
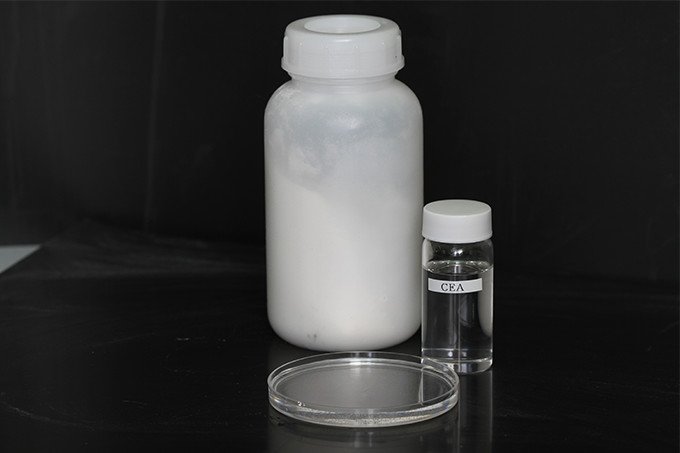
昭和電工が開発したノンハロゲンエポキシ樹脂
FOR THE FUTURE 開発のいま、そして未来
グリーン効果の連鎖
過酸化水素によってエポキシ樹脂を製造する製法確立の段階で、環境への負荷軽減を達成していた本プロジェクトですが、そこから生み出されるグリーン効果はその先にも続いていました。
本プロジェクトと並行して、もうひとつのターゲットである熱硬化が可能な新規の硬化剤の開発が成功していました。この新規の硬化剤を用いて絶縁保護膜を回路上に形成させる際に「スクリーン印刷法」と呼ばれる方法が採用できるようになりました(図5)。従来の「フォトリソグラフィ法」と違い、「スクリーン印刷法」を採用したプロセスでは、露光→現像の工程が必要ないため、大量のアルカリ性現像廃液を排出せずに絶縁保護膜を回路上に形成させることができます。つまり、絶縁保護膜を製造する工程のみならず、使用する場面においても環境負荷を低減させることが可能となりました。
さらに開発された絶縁保護膜を利用したプリント配線基板を採用することで、新たなグリーン効果が加わることがわかりました。
エレクトロニクス製品の寿命は、回路を保護する絶縁保護膜の性能に大きく依存しています。この絶縁保護膜の性能が向上したことでエレクトロニクス製品の信頼性(寿命)を大幅に延ばすことが可能になりました。これは結果的にテレビなどの製品寿命が延びることであり、最終的に廃棄物の排出削減につながるものでした。
また、エレクトロニクス製品の小型化は輸送にかかるエネルギー消費の削減、駆動電力も少なくて済むなど大幅な省エネ効果が実現しました。樹脂の製造方法を改良することで"いくつものグリーンイノベーション"が同時に起こったのです。
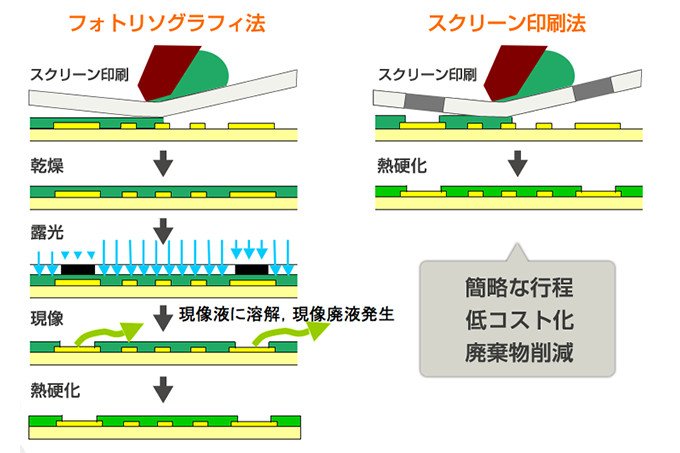
図5 フォトリソグラフィ法からスクリーン印刷法へ。緑の部分が絶縁保護膜
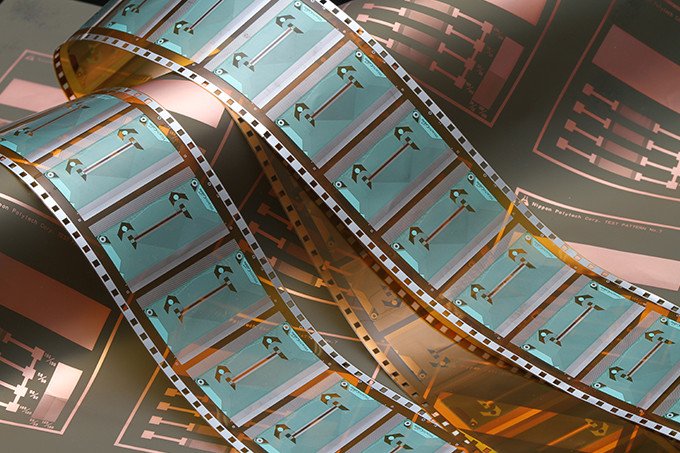
この技術を利用したソルダーレジスト(緑色部分)。柔軟性と絶縁性能を両立した
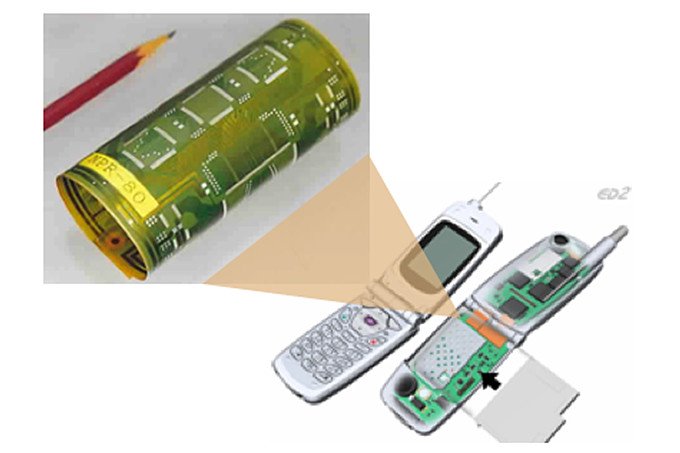
図6 熱硬化型絶縁材料が組み込まれた製品例(携帯電話)
有識者のアドバイスが更なるプロジェクトの発展につながった
野依教授らによる基礎研究を実用化研究につなげるときに、本プロジェクトでは大きな選択を迫られました。プロジェクトの技術検討委員会では、明確なビジネスモデルを常に求められたことです。具体的には、「接着剤のような汎用製品として要求性能が低く安価だが大量に需要が見込まれる開発に重きをおくか、あるいはICチップ用樹脂のように非常に高い要求性能を満たす高価で限られた量の需要しか見込まれない開発をするか」という究極の選択です。
内田さんは、「NEDOプロジェクトの推進委員からの戦略アドバイスは、事業化まで見通したとても有益なアドバイスだった」と当時を振り返ります。非常に高い要求性能を満たす樹脂開発を選択した影には、自社開発だけでは得られなかった各方面の専門家からのアドバイスがあったのです。
今回開発された技術は、世界最大級の国際産業見本市ハノーバー・メッセ(2008年)でも注目され、また化学・バイオつくば賞(2008年)や、産学官連携功労者表彰日本経済団体連合会会長賞(2010年)などの外部の高い評価を受けることとなりました。
プロジェクト終了後も継続研究としてこの成果を基にした改良が続けられており、2008年度より開始された後継プロジェクト「グリーン・サスティナブルケミカルプロセス基盤技術開発」につながり、更なる発展を続けています。(2010年12月取材)
開発者の横顔
足掛け30年の構想を実現
1980年代からエポキシ樹脂の研究開発を手がけていた内田博さんは、「塩素を使わずにエポキシ樹脂を合成したいという問題意識は30年以上前から持っていました」と言います。というのも、昭和電工はエポキシ樹脂の原料のエピクロロヒドリンを大分工場と川崎工場の二箇所にまたがる工程で製造していたのです。
「エピクロロヒドリンを使わなければ、大分工場だけで製造を完結できるのに」というのが当時の問題意識でした。1996年に野依教授の論文を読んだときは、「これは是非ともうちで事業化したい」と思ったそうです。
環境問題や絶縁体としての高い性能要求という追い風に乗って、内田さんの夢は現実のものとなりました。「事業としてだけでなく、環境対策として社会全体に貢献できたというのはうれしいことです」といいながらも、内田さんは「ウカウカしていられない」と考えています。製品化した高機能絶縁性樹脂が使われているのは変化の激しい分野。他用途にむけた製品化を実現し、もっと大きな事業にしておかなければ安心はできないと考えているそうです。
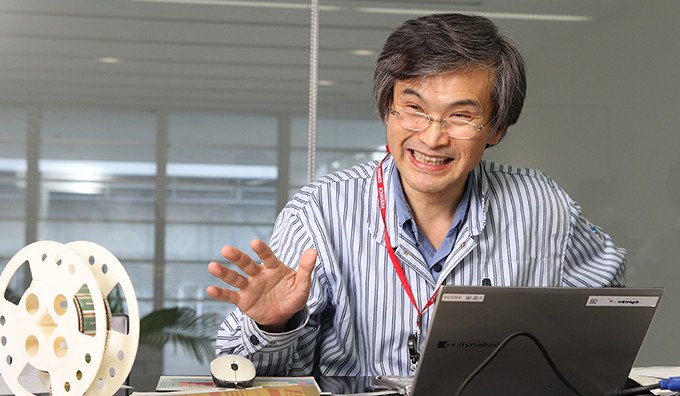
昭和電工株式会社
内田さん
なるほど基礎知識
絶縁保護膜とは
エレクトロニクス製品で使われている電気回路はポリイミドフィルム基板やガラスエポキシ基板表面に主に銅で描かれています。その電気回路がむき出しのままだとゴミや水、他の電気回路が接触したときに不必要な部分に電気が流れたり、電気回路同士のショートなどが起こったりして故障してしまいます。そのため、その電気回路を保護するために絶縁保護膜で覆うのです。
絶縁保護膜には電気抵抗の大きい樹脂が使われます。例えば、液晶画面の走査線一本一本に電気信号を送る駆動IC部分は基板フィルムの上に髪の毛よりも細い数十ミクロン程度の(1ミクロンは1mmの1000分の1)幅で銅線が配線され、それを保護するための絶縁保護膜で覆われています(図A)。
また、絶縁保護膜用の樹脂は、プリント配線基板用途(パッケージ基板、ビルドアップ基板、フレキシブル基板)だけでなく、固体半導体封止材、アンダーフィル材、ダイボンディング材としても使用されています(図B)。
エレクトロニクス製品に用いられる絶縁保護膜には、長時間使用しても絶縁性が落ちないなど、最高レベルの信頼性が必要とされています。
一方、エレクトロニクス製品内部は、絶縁保護膜にとっては過酷な環境です。電気回路が置かれている製品内部は思った以上に高温になります(例えば居間に置いた液晶テレビが意外と熱いことに驚かれたことがある方も多いはずです)。
また、部屋の湿度の変化にもさらされます。高温高湿は樹脂の劣化を促進する条件です。樹脂の絶縁性と耐久性、さらには環境への配慮など、絶縁保護膜に求められる要求は日々高くなっているのです。
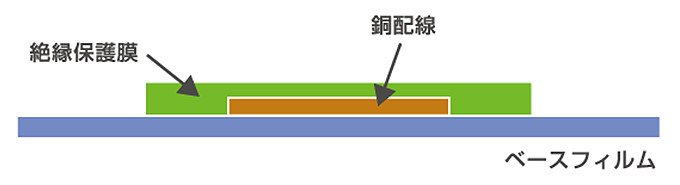
図A プリント配線基板断面模式図
ベースフィルム(紫)の上に銅配線(茶)が形成され、絶縁保護膜(緑)で覆っている
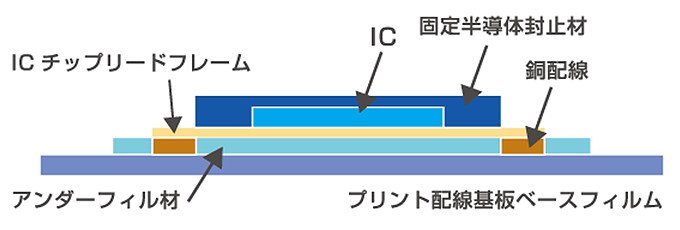
図B 絶縁用樹脂の用途
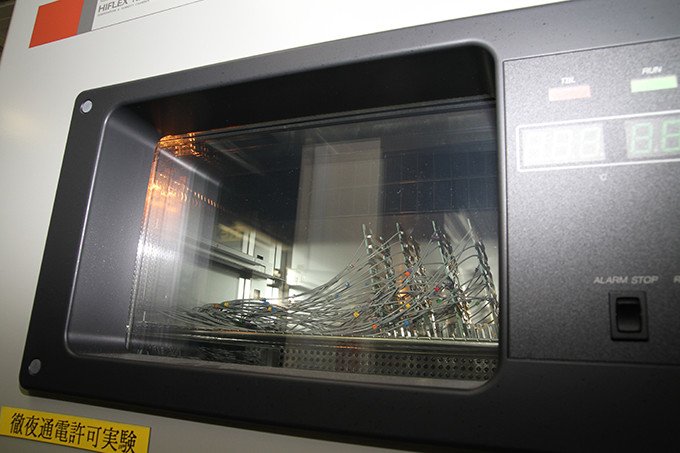
温度85℃ 相対湿度85%RHの環境下で試験用回路に印加し抵抗値の経時変化を測定
お読みいただきありがとうございました。
ぜひともアンケートにお答えいただき、
お読みいただいた感想をお聞かせください。
いただいた感想は、
今後の連載の参考とさせていただきます。